Air Duct Automatic Rolling Production Line
Air Duct Rolling Production Line- Rolling Welding Flanging for Axial Flow Fan
Machine Name | Air Duct Rolling Production Line |
Model | AC-JHF 2000 – Custom |
Application Industry | Industrial Fan Ducts, Ventilation Ducts, Axial Fan Ducts, Fire Protection Ducts, Water Storage Tanks, Cylindrical Barrels, Etc. |
Technical Service | Complete the test in the early stage; provide online and offline training in the later stage, and complete the turnkey project. |
Technical Guidance | Online 24 hours a day/ Conference To Solve Pre-Sales Problems. |
Project Progress | 30-120 days |
Relevant Files | ALTRON_AUTO Catalog-Industrial Blower Machinery Turnkey Project |
Industrial Fans A-Z Project:
1 CNC Rolling machine 2 Seam Welding machine 3 Axial Flow Fans Forming Production Line , 4 CNC Flanging Machines, 5 CNC Spinning Machine,
- ADAVANTAGES
- PARAMETERS
- CUSTOMER TESTIMONIALS
Altron’s Air Duct Rolling Welding Flanging Production Line is designed for the industrial fan and ventilation industries. It is a customized production line that is widely used in metal forming and welding of industrial fan ducts, ventilation ducts, axial fan ducts, fire ducts, water tanks, and products in cylindrical barrels. Different production plans and production line layouts can be selected according to different materials; different welding machine models are selected to match the corresponding metal materials.
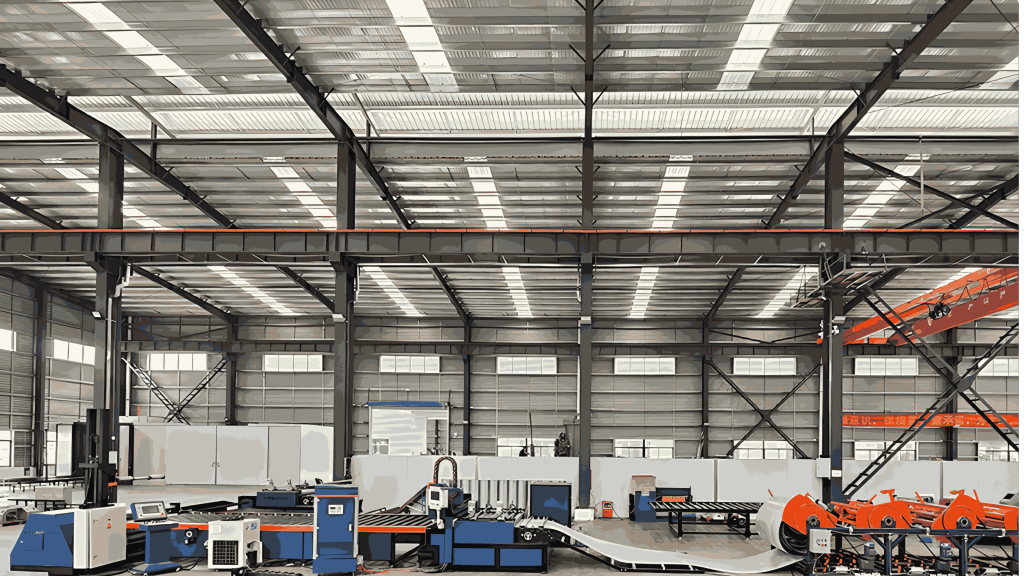
Main Features Of The Rolling Production Line
- Automatic loading, automatic rolling, automatic welding, automatic unloading;
- Improve production efficiency and the quality of cylindrical rolls;
- Reduce labor costs and manufacturing process steps.
Main functional parts of the Air Duct Rolling Welding Flanging Production Line:
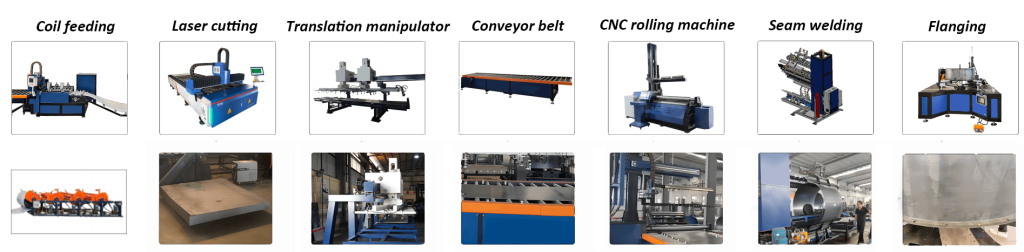
Video Of Air Duct Rolling Welding Flanging Production Line
Application areas of Duct Rolling Welding Flanging Production Line:
- HVAC system: This production line can efficiently produce cylindrical ducts, dampers, fan housings, etc. for heating, ventilation and air conditioning (HVAC) systems.
- Industrial ventilation: The production line is suitable for manufacturing cylindrical ducts for industrial ventilation systems.
- Commercial buildings: This production line can efficiently produce ventilation ducts for commercial buildings such as offices, shopping malls and hotels.
- Special applications: The production line can meet special applications such as operating rooms, clean rooms, laboratories, hospitals and large data centers. These special environments require air circulation and control, filtration, and the ducts play the role of gas transportation and discharge.
Air Duct Rolling Finished Effect
Advantages and Introduction of Air Duct Production Line
Configuration
Customized solutions for rolling and welding production line
Production line planning
Zike Equipment Co., Ltd.: The roll barrel workshop area is 36*32 meters; the production line part occupies 27*8.5 meters, and the customer will match the original roll flat production line!
Air duct Rolling Welding Flanging production line Operation diagram and step description
- The suction cup of the material-retrieving manipulator sucks the plate to the conveying platform;
- The conveying platform, conveys the plate to the rolling machine, and the rolling machine rolls it;
- The rolling machine completes the work, and the roll barrel is pushed to the transport trolley;
- The track conveying trolley automatically transports it to the position of the seam welding machine lifting trolley;
- The track conveying trolley automatically pushes the cylinder into the lifting trolley;
- The manual operation of the lifting trolley moves to the lifting seam welding machine and performs welding;
- The seam welding machine diagram, including pneumatic position positioning: end face and weld;
- The manual operation of the lifting trolley moves the welded round tube to the discharge position, and the discharge trolley moves to the discharge position at the same time;
- The manual pushes the welded cylinder into the track discharge trolley;
- Press the start button to automatically flanging the flanging machine (both sides can be flanging at the same time), and the operation steps on both sides are the same;
- After the flanging is completed, the track discharge trolley moves to the pipe arrangement station and manually unloads the material;
Air duct roll welding and flanging production line production display
![]() | ![]() | ![]() |
![]() | ![]() | ![]() |