2024 Efficient Solutions: Maximizing Output with Axial Blower Rolling & Welding
Axial blower rolling & welding represent the pinnacle of precision manufacturing, where form meets function to create ventilation solutions of unparalleled quality and performance. Through the integration of advanced technologies and automated production processes, manufacturers like ALTRON continue to push the boundaries of innovation, delivering products that exceed expectations and stand the test of time.
Unveiling the Mechanics Behind Axial Flow Fans
1.1 Understanding Axial Flow Fans
Axial flow fans, renowned for their efficient air movement capabilities, are indispensable components across various industries. Unlike centrifugal fans that produce airflow perpendicular to the fan blade axis, axial flow fans generate airflow parallel to the axis of the fan. This mechanism allows for a more streamlined and direct airflow, making axial flow fans ideal for applications where high airflow rates are required.
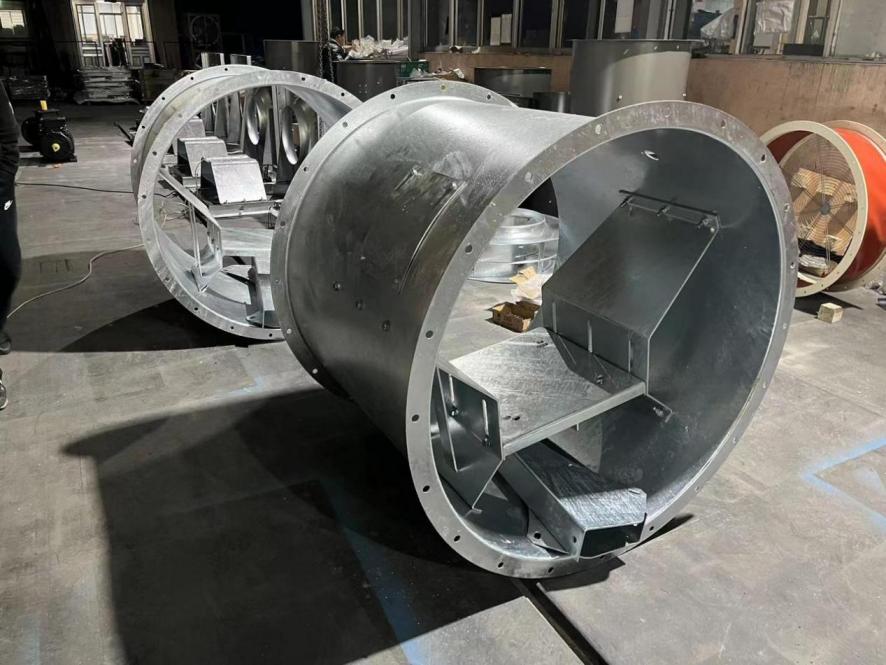
1.2 Features of Axial Flow Fans
High Airflow Efficiency: Axial flow fans are designed to move large volumes of air with minimal resistance, making them highly efficient for ventilation and cooling purposes.
- Low Noise Emission: With their streamlined design and efficient blade configuration, axial flow fans produce lower noise levels compared to other types of fans, making them suitable for applications where noise reduction is crucial.
- Compact Design: Axial flow fans are typically more compact than centrifugal fans, making them easier to install in confined spaces without compromising on performance.
- Variable Speed Control: Many axial flow fans come equipped with variable speed control options, allowing users to adjust the airflow rate according to specific requirements, enhancing energy efficiency.
The Importance of Axial Flow Fan Flanging and Punching
2.1 Meeting Industry Needs
Axial flow fan flanging and punching processes play a crucial role in enhancing the performance and efficiency of axial flow fans. Flanging involves the shaping of the fan casing to ensure a secure fit for the fan blades while punching creates openings in the casing for airflow. These processes are essential for maintaining optimal airflow dynamics and preventing air leakage, which can significantly impact the overall efficiency of the fan system.
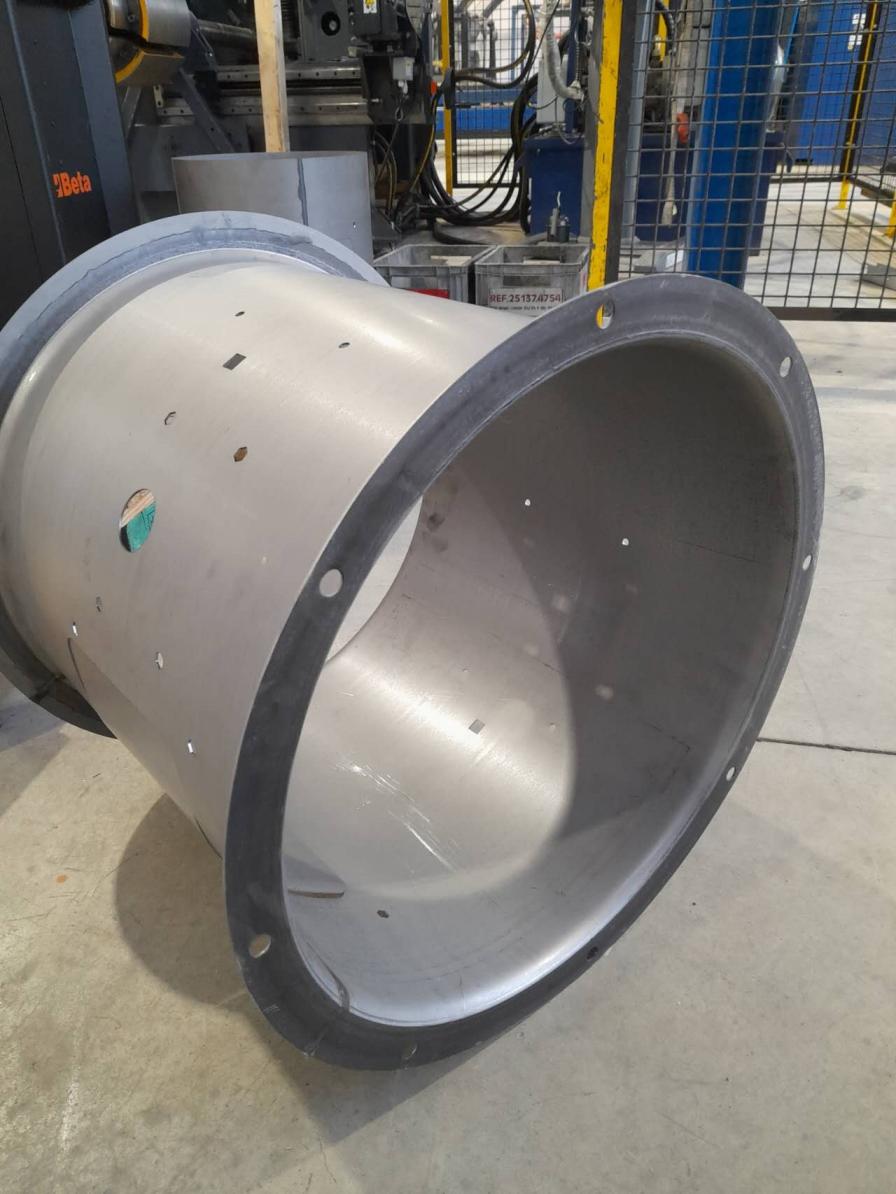
2.2 Solutions for Enhanced Performance
- Precision Engineering: Utilizing advanced flanging and punching techniques ensures precise alignment and fitment of fan components, minimizing air resistance and maximizing airflow efficiency.
- Seamless Integration: By seamlessly integrating flanging and punching processes into the manufacturing workflow, manufacturers can streamline production and reduce lead times, meeting the demands of fast-paced industries.
- Quality Assurance:Implementing stringent quality control measures throughout the flanging and punching processes ensures that each axial flow fan meets the highest standards of performance and reliability, instilling confidence in end-users.
The Role of Axial Flow Fan Flanging Machine
3.1 Advantages of Axial Flow Fan Flanging Machine
Axial flow fan flanging machines are specialized equipment designed to automate the flanging process, offering numerous advantages over traditional manual methods. These machines utilize precision-engineered tooling and advanced control systems to ensure consistent and accurate flange formation, resulting in superior airflow performance and product quality.
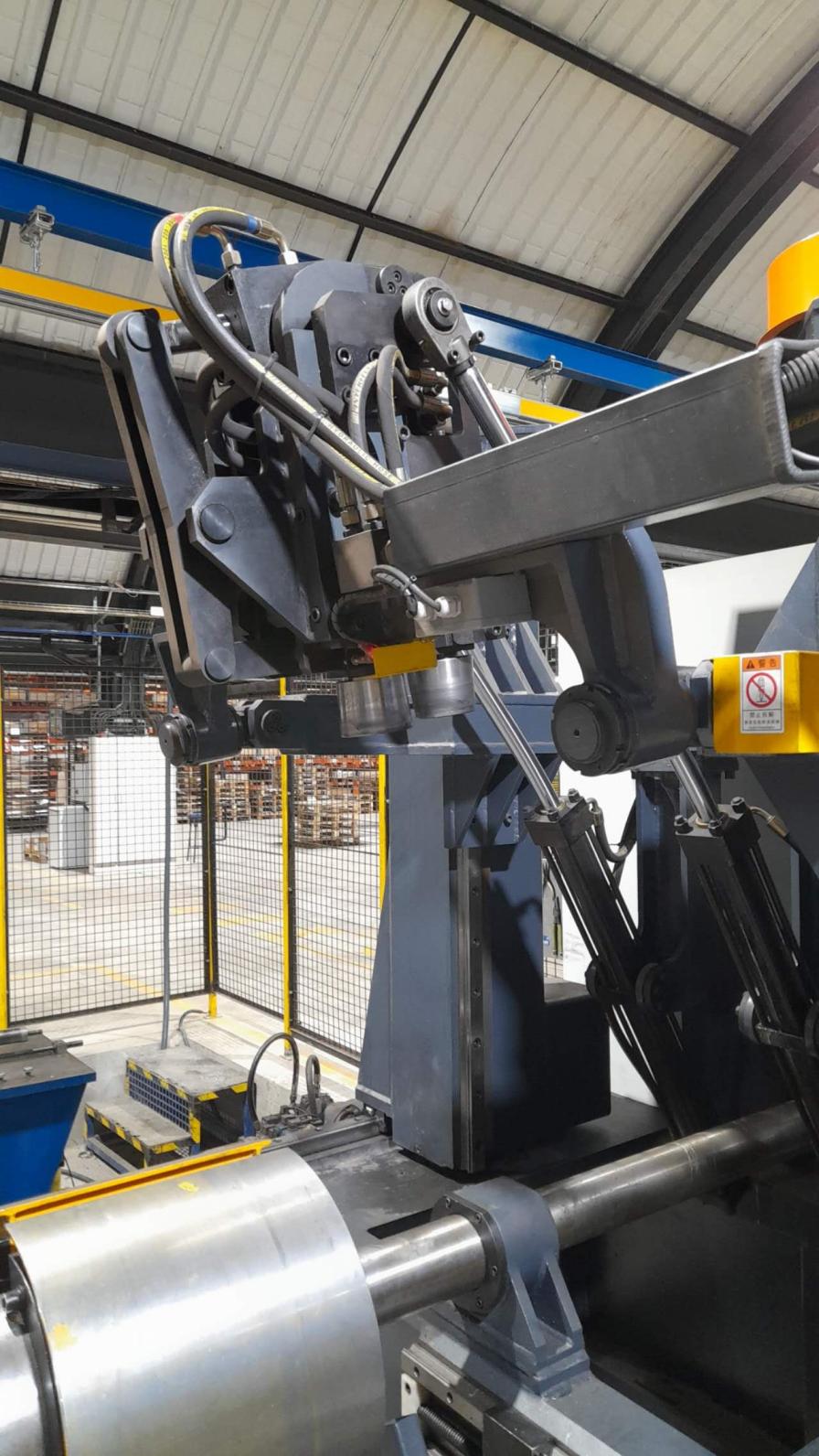
3.2 Applications of Axial Flow Fan Flanging Machine
- Mass Production:Axial flow fan flanging machines are capable of high-speed operation, making them ideal for mass production environments where efficiency and productivity are paramount.
- Customization Flexibility: With programmable control systems, axial flow fan flanging machines can accommodate a wide range of fan sizes and configurations, allowing manufacturers to offer customized solutions to meet specific customer requirements.
- Quality Assurance:By automating the flanging process, these machines minimize the risk of human error, ensuring uniformity and precision in every fan-produced, thereby enhancing overall product quality and reliability.
Rolling & Welding Automatic Production Line: Engineering Excellence in Action
4.1 A Symphony of Automation
The rolling & welding automatic production line epitomizes engineering excellence in action, orchestrating a symphony of automated processes to streamline production and enhance efficiency. From material handling to final inspection, every stage of the manufacturing process is meticulously choreographed to maximize productivity and minimize waste. By harnessing the power of automation, ALTRON and similar manufacturers can meet the growing demand for axial blowers while maintaining exceptional quality standards.
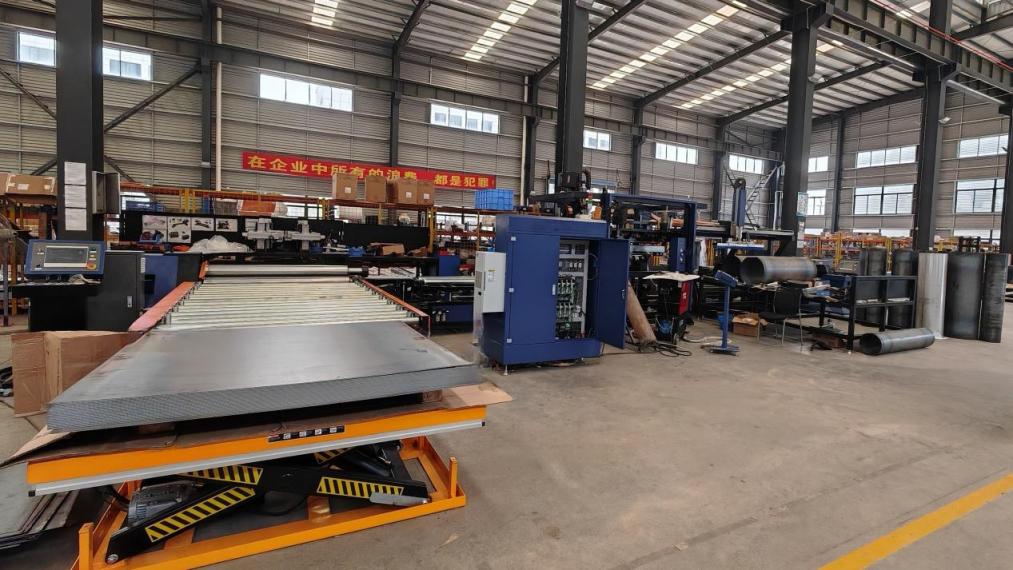
4.2 Integration of Advanced Technologies
At the heart of the Axial blower rolling & welding automatic production line lie state-of-the-art technologies that enable seamless integration and precision control. Robotics, sensors, and advanced control systems work in harmony to ensure consistency and accuracy throughout the manufacturing process. Whether it’s controlling the movement of materials or monitoring welding parameters, these technologies play a pivotal role in delivering axial blowers of unmatched quality and performance.
4.3 Optimizing Efficiency and Throughput
By automating repetitive tasks and eliminating manual intervention, the rolling & welding automatic production line optimizes efficiency and throughput. This results in shorter lead times, reduced production costs, and increased scalability, allowing manufacturers to respond swiftly to market demands. Furthermore, automation minimizes the risk of errors and defects, ensuring that each axial blower meets the exact specifications set forth by industry standards.
Rolling Round Welding Effect: Precision in Motion
5.1 Achieving Seamless Integration
The rolling round welding effect is the hallmark of excellence in axial blower manufacturing. By precisely rolling and welding the cylindrical casing of the blower, manufacturers can create a seamless and airtight enclosure that maximizes airflow efficiency and minimizes energy loss. This meticulous process ensures that each axial blower delivers consistent performance and reliability, meeting the stringent demands of modern industrial applications.
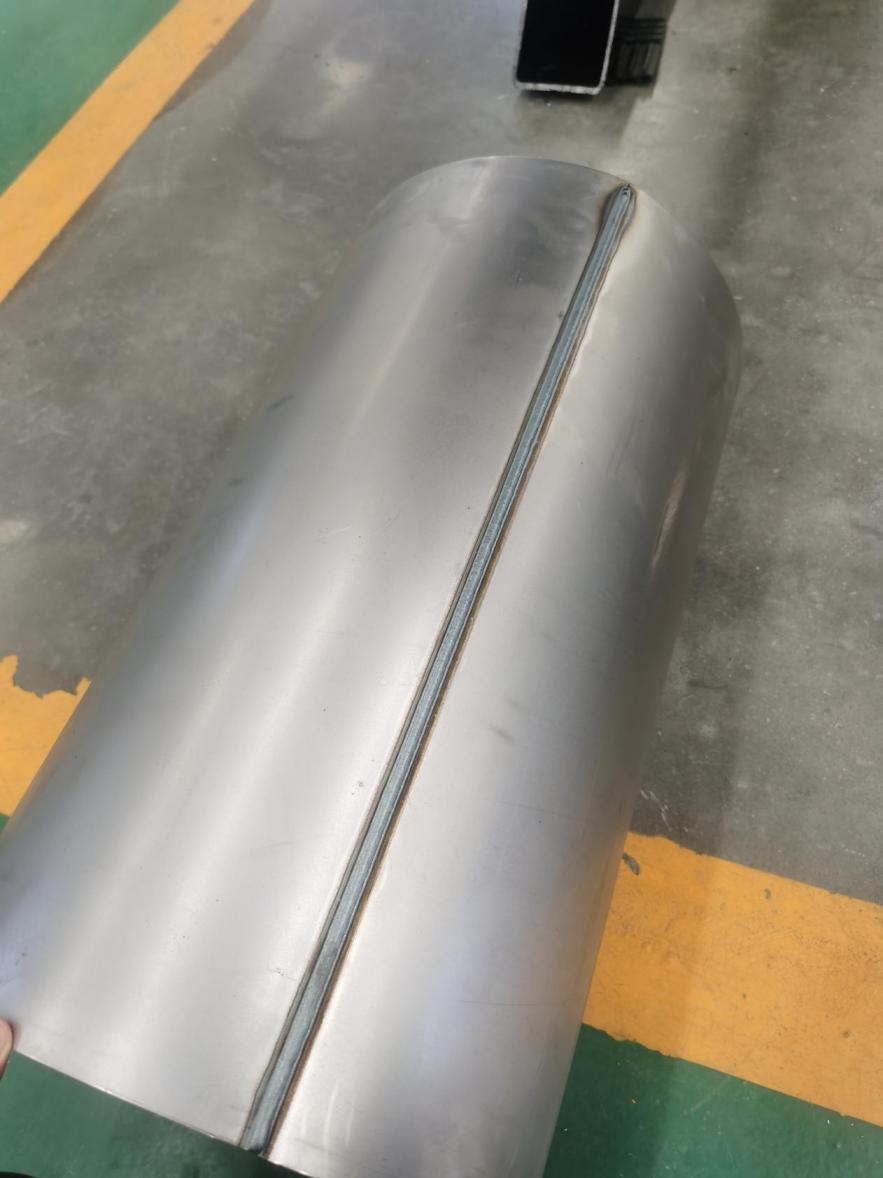
5.2 Enhancing Structural Integrity
Through the rolling round welding effect, axial blowers are endowed with enhanced structural integrity, capable of withstanding high pressures and temperatures without compromising performance. By seamlessly joining the edges of the cylindrical casing through precision welding, manufacturers create a robust enclosure that protects internal components and ensures long-term durability, even in the most demanding operating conditions.
5.3 Optimizing Airflow Dynamics
The rolling round welding effect plays a pivotal role in optimizing airflow dynamics within axial blowers. By eliminating irregularities and imperfections along the casing, manufacturers can achieve smooth and uninterrupted airflow, reducing turbulence and maximizing efficiency. This precision-engineered airflow path ensures that each axial blower delivers optimal performance, whether it’s providing ventilation in industrial facilities or cooling electronic components in electronic enclosures.
Automating Roll Round: Precision at Scale
6.1 Streamlining Production Processes
Automating the roll round process is essential for maximizing efficiency and scalability in axial blower manufacturing. By utilizing advanced robotics and control systems, manufacturers can achieve consistent and precise rolling of the cylindrical casing, minimizing material waste and optimizing production throughput. This automation enables manufacturers to meet the growing demand for axial blowers while maintaining high standards of quality and performance.
6.2 Ensuring Accuracy and Consistency
Automatic roll-round systems are equipped with sensors and feedback mechanisms that monitor and adjust the rolling process in real time, ensuring accuracy and consistency across every blower produced. By eliminating human error and variability, these automated systems guarantee uniformity in casing dimensions and geometry, resulting in axial blowers that meet the most stringent quality standards.
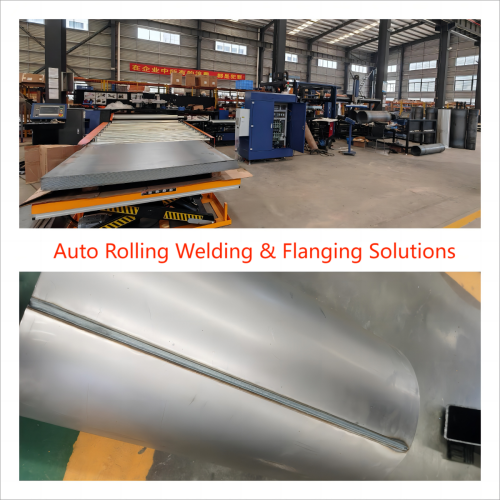
6.3 Improving Worker Safety
Automating the roll round process not only improves efficiency but also enhances worker safety in the manufacturing environment. By minimizing manual handling of heavy materials and reducing exposure to hazardous welding operations, automated roll-round systems create a safer and healthier workplace for manufacturing personnel. This prioritization of worker safety underscores the commitment of manufacturers like ALTRON to employee well-being and operational excellence.
Automated Welding: Fusion of Precision and Speed
7.1 Precision Welding Technology
Automatic welding plays a critical role in ensuring the structural integrity and airtightness of axial blowers. Utilizing advanced welding technologies such as laser welding or robotic arc welding, manufacturers can achieve precise and consistent welds that withstand the rigors of industrial operation. This fusion of precision and speed ensures that each weld joint is robust and reliable, contributing to the overall quality and performance of the axial blower.
7.2 Enhancing Production Efficiency
Automated welding systems offer unparalleled speed and efficiency compared to manual welding methods, significantly reducing production lead times and costs. By leveraging robotic welding arms and intelligent control algorithms, manufacturers can achieve high throughput without compromising weld quality. This increased production efficiency enables manufacturers to meet tight deadlines and fulfill customer orders with ease.
7.3 Ensuring Weld Quality and Integrity
Automatic welding systems are equipped with advanced quality control mechanisms that monitor weld parameters in real time, detecting defects and deviations before they compromise product quality. By maintaining strict adherence to welding standards and specifications, manufacturers can ensure that each weld joint meets the highest industry standards for strength and integrity. This commitment to quality assurance underscores the reliability and durability of axial blowers produced using automated welding technology.
Efficient Workflow of Automatic Round Rolling Production Line
8.1 Servo Feeding of Sheet Metal
The production process begins with servo feeding of sheet metal onto the conveyor belt, where precision control ensures accurate positioning for subsequent operations.
8.2 CNC Hydraulic Four-Roller Rolling
The sheet metal is then fed into CNC hydraulic automatic rounding machines, where it undergoes precision rolling to form the cylindrical casing of the axial blower. This process ensures uniformity in wall thickness and dimensional accuracy, essential for optimal performance.
8.3 Longitudinal Seam Gas Shield Welding
After rounding, the casing moves to the longitudinal seam tunnel welding machine, where gas shield welding is performed to join the edges of the casing. This welding process creates a strong and airtight seal, crucial for maintaining optimal airflow efficiency.
8.4 End Welding and Release of Drum Positioning
Once the longitudinal seam welding is complete, the casing undergoes end welding and is released from the drum positioning. This step ensures that the casing is securely welded and ready for further processing.
8.5 Welding Effect Display
Finally, the completed casing undergoes a welding effect display, where the quality of the welds is visually inspected to ensure they meet the highest standards of excellence.
Advantages of Single-Beat Test Rolling & Welding Automatic Production Line
9.1 Precision and Consistency
The single-beat test rolling & welding automatic production line offers unparalleled precision and consistency in the manufacturing process. By leveraging advanced technologies such as CNC control and servo feeding, ALTRON ensures that each axial blower produced meets exacting standards of quality and performance.
9.2 Efficiency and Productivity
With its streamlined workflow and automated processes, the production line maximizes efficiency and productivity, allowing ALTRON to meet the demands of a fast-paced industry. Shorter lead times and increased throughput enable the company to fulfill customer orders promptly and effectively.
9.3 Quality Assurance
Quality assurance is paramount in the manufacturing of axial blowers, and the single-beat test rolling & welding automatic production line delivers on this front. Through real-time monitoring and inspection, ALTRON ensures that every blower meets stringent quality standards, providing customers with products they can rely on.
Conclusion
In conclusion, axial flow fans and their associated flanging and punching processes are integral components of various industrial applications. By leveraging advanced technologies such as axial flow fan flanging machines, manufacturers can enhance efficiency, productivity, and product quality, meeting the evolving demands of modern industries. ALTRON, as a leading manufacturer in Axial blower rolling & welding, exemplifies excellence in engineering and innovation, driving advancements in airflow technology.