How to Make a Centrifugal Fan Impeller?
Overview of Industrial Centrifugal Fans
Industrial centrifugal fans are essential components in various industrial processes, providing crucial ventilation, aeration, and exhaust functions. These fans operate by converting rotational kinetic energy into fluid motion, using centrifugal force to move air or gases radially outwards from the center of the fan. Their robust design and efficient performance make them ideal for demanding environments, including manufacturing plants, chemical processing facilities, and HVAC systems.
Centrifugal fans are preferred in industrial settings due to their ability to handle high-pressure applications, maintain airflow at varying speeds, and operate efficiently under harsh conditions. The impeller, a core component of these fans, plays a significant role in determining their overall performance and energy efficiency.
Design of Industrial Centrifugal Fan Impeller
The design of the industrial centrifugal fan impeller is critical to the fan’s effectiveness and efficiency. Impellers are responsible for drawing air into the fan and accelerating it outwards through the fan housing. The design considerations include the shape, size, and material of the impeller, which must be tailored to meet specific application requirements.
Differences in Materials of Industrial Centrifugal Fan Impellers
Impellers can be constructed from a variety of materials, each offering unique advantages. Common materials include stainless steel, aluminum, and composites.
Stainless Steel: Known for its durability and resistance to corrosion, stainless steel is ideal for environments with high humidity or exposure to corrosive substances. It is often used in chemical plants and food processing industries.
Aluminum: Lightweight and resistant to corrosion, aluminum impellers are suitable for applications requiring high-speed operations and where weight reduction is crucial. They are frequently used in HVAC systems and light-duty industrial applications.
Composites: Composite materials offer excellent strength-to-weight ratios and resistance to various environmental factors. These impellers are used in specialized applications where weight and corrosion resistance are critical, such as in aerospace and marine industries.
Application Scenarios of Different Industrial Centrifugal Fan Impellers
The selection of impeller material depends on the specific application and operational environment.
High-Temperature Environments: Stainless steel impellers are preferred due to their ability to withstand high temperatures without deforming or losing strength.
Corrosive Environments: Both stainless steel and composite impellers are suitable, with the choice depending on the severity of the corrosion and specific chemical exposure.
Light-Duty Applications: Aluminum impellers are ideal for applications where high-speed operation and low weight are essential, such as in ventilation systems for office buildings.
Manufacturing Process of Industrial Centrifugal Fan Impeller
The manufacturing process of centrifugal fan impellers involves several stages, including welding, forming, and casting. Each stage must be executed with precision to ensure the impeller’s performance and durability.
Welding for Impeller
Welding Robot Machine for Centrifugal Fan Impeller
Altron’s centrifugal blower impeller welding robot simplifies the welding process, enhancing the quality and consistency of impellers. Traditional welding methods often fall short in achieving precise and consistent welds, relying heavily on manual labor. This can lead to inconsistencies in the assembly of impeller blades, affecting the overall performance of the fan.
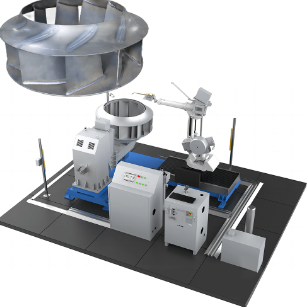
The laser vision-guided welding robot introduced by Altron addresses these issues by automating the welding process. This robot can track the weld in real time and correct the welding trajectory, ensuring true automatic welding. The result is a consistent weld strength, improved appearance, and the elimination of the need for manual grinding.
Forming for Impeller
Multi-Wing Centrifugal Fan Impeller Forming and Punching Machine
Altron’s high-tech equipment solutions are designed to meet the diverse needs of industrial fan manufacturers. The multi-blade impeller forming and punching machines offer customized solutions for forming impellers, ensuring precise and consistent production.
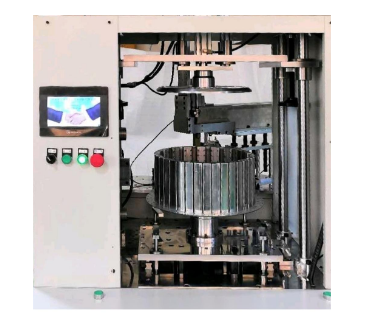
Altron’s mechanical equipment includes automated mechanical equipment, visual inspection systems, industrial robots, and various specialized machines for blower blade insertion, wind power end ring punching, and more. These automated solutions enhance efficiency, safety, and sustainability in the manufacturing process, reducing labor costs and improving production quality.
Casting for Impeller
Casting is another critical process in the manufacturing of impellers, particularly for applications requiring high strength and durability. The casting process involves pouring molten metal into a mold to create the desired impeller shape. This method allows for complex geometries and ensures uniform material properties throughout the impeller.
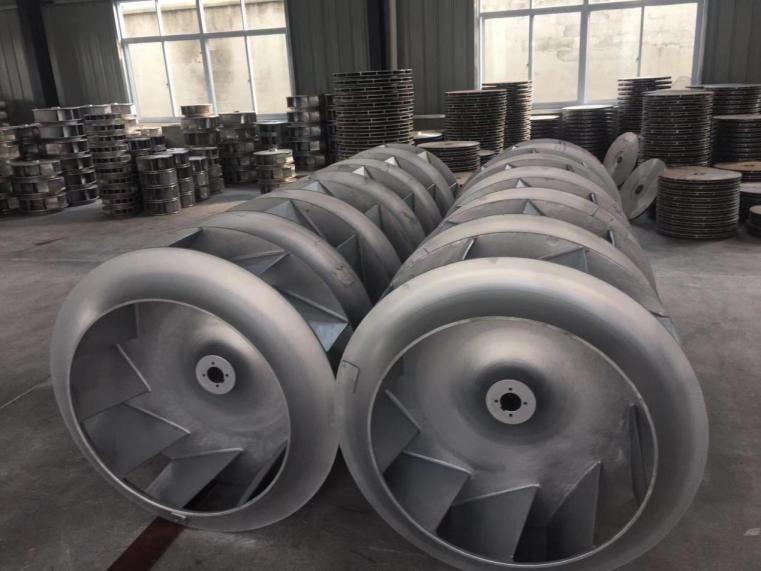
Advantages and Trends of Automated Impeller Production
Automated impeller production offers several advantages over traditional manufacturing methods. Automation improves precision, reduces labor costs, and enhances production speed. It also ensures consistent quality, which is crucial for the performance and energy efficiency of industrial fans.
Recent trends in impeller production focus on integrating advanced technologies such as laser vision systems, robotics, and AI-driven quality control. These innovations enable real-time monitoring and adjustments, further improving the efficiency and reliability of the manufacturing process.
CNC Metal Spinning & Flanging for Impeller Shroud & Air Inlet Cone
CNC Metal Spinning Machine – Single Roller AC2000
The Single Roller CNC Metal Spinning Machine AC2000 is designed for processing large round materials, making it suitable for industrial blowers and centrifugal fans. It can handle diameters up to 2050mm, making it ideal for producing air inlet funnels and impeller shrouds.
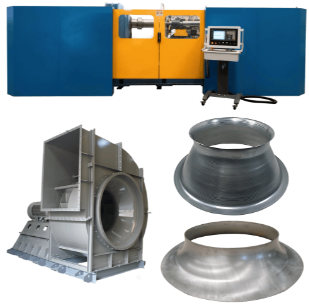
The AC2000 offers precise control over the spinning process, ensuring uniform thickness and high-quality finishes. This machine enhances the efficiency of producing large components, reducing material waste and improving overall production speed.
Function of the Impeller of an Industrial Centrifugal Fan
The impeller of an industrial centrifugal fan is a crucial component that determines the overall efficiency and performance of the fan. It functions by converting mechanical energy from the motor into kinetic energy, thereby moving air or gases. The impeller consists of a series of blades that rotate to create a centrifugal force, pushing the air outward from the center towards the fan housing and into the desired direction.
Airflow Generation
The primary function of the impeller is to generate airflow by accelerating the air through its blades. As the impeller rotates, it draws air into the fan’s central hub and expels it radially outward, creating a continuous flow. This mechanism is essential for applications requiring ventilation, exhaust, and cooling in industrial settings.
Pressure Increase
Another critical function of the impeller is to increase the pressure of the air or gas being moved. The centrifugal force created by the rotating impeller blades compresses the air, thereby increasing its pressure. This pressure rise is vital for applications where high-pressure airflow is necessary, such as in pneumatic conveying systems and high-efficiency ventilation systems.
Energy Conversion
The impeller also plays a key role in energy conversion. It efficiently transforms the mechanical energy provided by the fan motor into the kinetic energy of the airflow. This conversion process is critical for the fan’s overall energy efficiency and operational cost-effectiveness. A well-designed impeller ensures minimal energy loss and maximizes the fan’s performance.
How to Improve the Performance of the Impeller and Improve the Energy Efficiency of Industrial Centrifugal Fans
Enhancing the performance of the impeller is essential for improving the energy efficiency of industrial centrifugal fans. Several strategies can be employed to achieve this goal.
Optimizing Impeller Design
The design of the impeller significantly impacts its performance. Engineers can optimize the blade shape, size, and angle to improve airflow and reduce energy losses. Advanced computational fluid dynamics (CFD) tools can simulate airflow patterns and identify design modifications that enhance efficiency.
Using High-Quality Materials
The choice of materials for the impeller affects its durability and performance. High-quality materials like stainless steel, aluminum, and advanced composites offer superior strength, corrosion resistance, and lightweight properties. Using such materials ensures the impeller operates efficiently under various environmental conditions and extends its lifespan.
Implementing Advanced Manufacturing Techniques
Adopting advanced manufacturing techniques such as CNC machining, precision welding, and dynamic balancing can enhance impeller performance. These techniques ensure high precision in impeller fabrication, reducing mechanical imbalances and improving energy efficiency. For example, CNC metal spinning can produce impellers with uniform thickness and precise dimensions.
Important Components of Industrial Centrifugal Fans
Industrial centrifugal fans comprise several critical components, each contributing to the fan’s overall performance and reliability.
Impeller
As discussed, the impeller is the heart of the centrifugal fan, responsible for generating airflow and increasing pressure. Its design and material choice are crucial for the fan’s efficiency.
Housing
The housing encloses the impeller and directs the airflow. It is designed to minimize air leakage and ensure smooth airflow transitions. The housing also protects the impeller from external contaminants and damage.
Motor
The motor provides the mechanical energy needed to rotate the impeller. It must be powerful enough to drive the impeller at the required speed while maintaining energy efficiency. High-efficiency motors are preferred to reduce energy consumption and operational costs.
How to Choose the Centrifugal Fan Impeller Correctly
Selecting the right centrifugal fan impeller is essential for achieving optimal performance and efficiency in industrial applications.
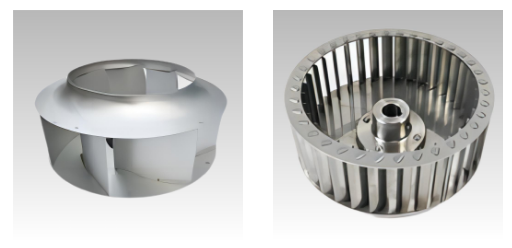
Assessing Application Requirements
The first step in choosing the correct impeller is to assess the specific requirements of the application. Factors such as airflow rate, pressure, temperature, and environmental conditions must be considered. For example, applications requiring high-pressure airflow will benefit from impellers with backward-curved blades.
Considering Material Compatibility
The material of the impeller must be compatible with the operational environment. Stainless steel impellers are suitable for corrosive environments, while aluminum impellers are ideal for applications where weight reduction is critical. Composites are chosen for their excellent strength-to-weight ratios and resistance to specific environmental factors.
Customization and OEM Services
Customizing the impeller to match the specific parameters of the fan can significantly improve performance. Altron offers industrial fan impeller OEM services, allowing manufacturers to send fan drawings or match fan parameters to the appropriate impeller. This customization ensures that the impeller meets the precise requirements of the application.
Dynamic Balancing Test of Industrial Centrifugal Fan Impeller
Dynamic balancing is crucial for ensuring the smooth operation and longevity of centrifugal fan impellers.
Special Dynamic Balancing Machine for Industrial Fans
Altron’s dynamic balancing machines are designed to provide accurate and efficient balancing for industrial fan impellers. These machines feature solid and reliable brackets that transmit mechanical force with low vibration damping and high rigidity.
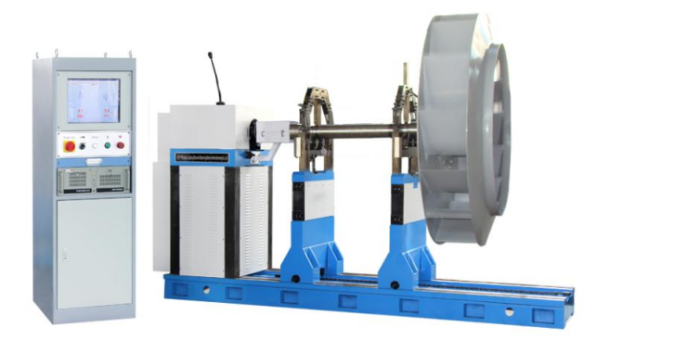
High Sensitivity and Accuracy
The sensors used in these machines possess high sensitivity and good linearity, ensuring precise measurements. Permanent calibration ensures high accuracy, even with large initial unbalanced amounts. This level of precision is critical for maintaining the performance and reliability of the impeller.
Universal Coupling Driven System
The universal coupling-driven system offers stable power transmission, fast startup, and convenient operation. It is particularly suitable for rotors that cannot be driven by belts or require larger transmission devices. The balancing machines are adaptable to various applications, including blowers, large motors, pumps, centrifuges, and more.
Why Choose Altron’s Industrial Centrifugal Fan Impeller Services?
Altron’s expertise in industrial centrifugal fan impeller manufacturing makes it a preferred choice for OEM services.
Custom Manufacturing and Sales
Altron custom manufactures and sells industrial fan impellers, providing comprehensive production line services. They support fan impeller metal forming and welding solutions, ensuring that each impeller meets the specific needs of industrial fan manufacturers.
Advanced Production Processes
Altron employs advanced production processes, including CNC metal spinning, stamping, deep drawing, rolling, auto welding, and riveting. These processes ensure high precision and quality in impeller fabrication. Alignment, dynamic balancing, and rigorous quality inspection further guarantee the performance and reliability of each impeller.
Versatility and Wide Application
With a complete impeller production line, Altron can produce forward impellers, backward impellers, multi-blade impellers, and water pump impellers. These impellers are widely used in various industries, including sweepers, fresh air systems, and dust removal applications. Altron’s ability to customize multi-wing impeller production lines ensures they can meet diverse industrial needs.
Conclusion
The manufacturing of industrial centrifugal fan impellers is a complex process that involves careful design, material selection, and advanced production techniques. Automation plays a crucial role in enhancing the efficiency, quality, and consistency of impeller production. Companies like Altron are at the forefront of this industry, providing innovative solutions that meet the evolving needs of industrial fan manufacturers. By leveraging automated welding, forming, casting, and CNC spinning technologies, manufacturers can achieve superior performance and energy efficiency in their centrifugal fans, supporting a wide range of industrial applications.
