CNC Machining Wheels: Precision and Performance
The journey from raw material to finished CNC machine wheels is a remarkable testament to precision engineering and quality control. ALTRON, a prominent manufacturer in this field, takes great pride in producing wheels that are not only aesthetically pleasing but also durable and high-performing. As CNC technology continues to advance, we can only expect even greater precision and efficiency in the production of these essential components that keep our vehicles and machines rolling smoothly.
I. Project Introduction
A. Purpose of Machining Wheels using CNC
Machining wheels using Computer Numerical Control (CNC) technology has become an essential aspect of modern manufacturing. CNC machines, renowned for their precision and versatility, are employed to craft wheels that meet the highest standards of performance, aesthetics, and safety.
B. Types of Wheels to be Machined
Within the realm of wheel manufacturing, a diverse array of wheel types is crafted using CNC machining techniques. These encompass automotive wheels, motorcycle wheels, bicycle wheels, industrial wheels, and specialized wheels used in aerospace and robotics.
C. Key Goals and Objectives of the Machining Process
The primary goals and objectives of machining wheels using CNC include achieving precise dimensions, exceptional surface finishes, and consistent quality. This process aims to produce wheels that are not only visually appealing but also durable and capable of withstanding the rigors of their intended applications.
II. Wheel Design and Specifications
A. Gathering Design Specifications
In the wheel manufacturing process undertaken by ALTRON, detailed design specifications are the foundation. These specifications include load-bearing capacity, bolt pattern, spoke design, and the desired aesthetics. Each wheel is designed with a specific purpose and performance criteria in mind.
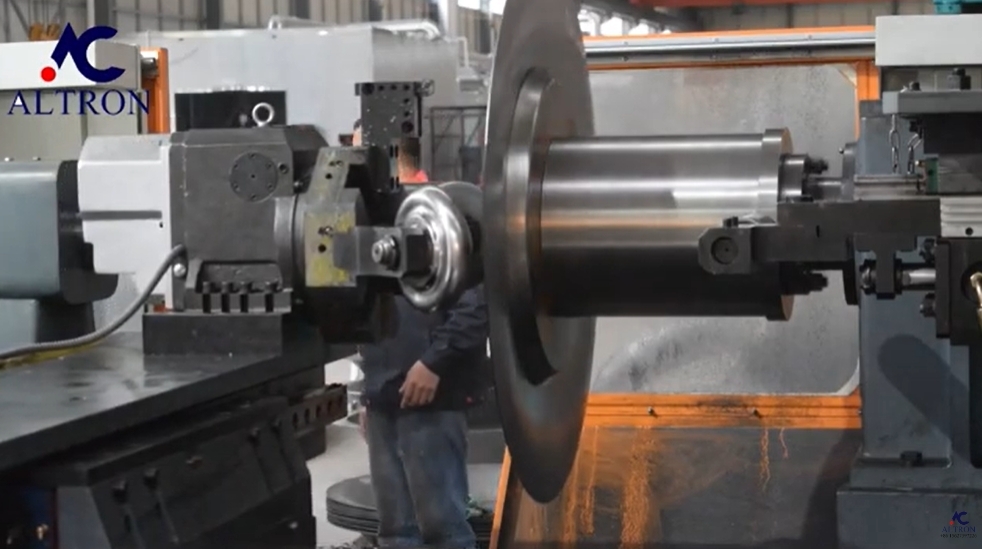
B. Material Selection
The choice of material is critical to the performance and appearance of the wheels. ALTRON works with a variety of materials, such as aluminum, steel, and alloy blends, each chosen to match the desired characteristics of strength, weight, and aesthetics.
C. Wheel Dimensions
Wheel dimensions are meticulously specified, considering factors like diameter, width, and offset. These dimensions play a vital role in determining the fitment and performance of the wheels on various vehicles or machinery.
D. Customizations and Unique Features
Customizations are often necessary to meet specific customer requirements or to add unique features. This may include special coatings for corrosion resistance, intricate spoke patterns for aesthetics, or lightweight designs for improved fuel efficiency.
III. CNC Machine Setup
A. Choosing the Right CNC Machine
ALTRON, a renowned CNC machine manufacturer, understands the importance of selecting the appropriate CNC machine type for wheel machining. Depending on the complexity of the design, they may employ CNC lathes, milling machines, or even multi-axis machining centers to achieve the desired precision and finish.
B. Tooling and Fixtures
To ensure precise and repeatable machining, the setup includes the installation and alignment of the necessary tooling, such as chucks or fixtures. These components securely hold the wheel blanks in place during machining, minimizing errors and maximizing efficiency.
C. CNC Programming
The heart of the CNC machining process lies in the CNC program or G-code. Skilled programmers at ALTRON develop intricate programs that guide the machine through the various machining operations required to transform raw materials into finished wheels. These programs incorporate toolpaths, speeds, feeds, and tool changes to optimize the machining process.
Ⅳ. Material Preparation
A. Procuring the Raw Material
Before the wheels take shape, ALTRON, the renowned CNC machine wheels manufacturer, begins by procuring the raw material. In this case, the raw material often comes in the form of billets or forged wheel blanks. These materials are carefully selected for their durability and suitability for CNC machining.
B. Securing the Raw Material
Once the raw material is in-house, the next step is to securely fix it onto the CNC machine. ALTRON employs precision clamps or chucks to ensure the material remains firmly in place throughout the machining process. A secure fixture is essential for maintaining dimensional accuracy and achieving precise results.
C. Verifying Material Dimensions and Alignment
Before the CNC machine springs into action, a crucial quality control step is to verify the dimensions and alignment of the raw material. Precise measurements and alignments are essential to ensure that the finished wheel meets the design specifications.
Ⅴ. Machining Process
A. Rough Machining: Shaping the Wheel
With the raw material securely fastened, rough machining commences. ALTRON utilizes roughing tools such as end mills and drills to begin shaping the wheel. This initial stage involves removing excess material to approach the wheel’s final shape. Rough machining sets the foundation for the subsequent precision work.
B. Finish Machining: Achieving Exact Design
Once the rough shape is achieved, it’s time for precision. ALTRON employs cutting-edge precision cutting tools, calibrated to perfection, to achieve the exact wheel design specified. Fine-tuning dimensions and surface finish are the primary focus during this phase.
C. Hole Drilling and Other Operations: Completing the Wheel
To complete the wheel, additional operations are often necessary. Hole drilling for wheel attachments, such as bolts or valve stems, is a critical step. ALTRON ensures that these holes are precisely drilled to match the required specifications. Any other machining operations needed to meet design requirements are also carried out with the same precision and care.
Ⅵ. Quality Control and Inspection
A. Implementing Quality Control
Throughout the entire machining process, ALTRON has stringent quality control measures in place. These checks are not just limited to the final product but are integrated into every step of production. Continuous monitoring ensures that any deviations from the design specifications are promptly addressed.
B. Inspecting Wheel Dimensions and Finish
Wheel dimensions and surface finish are closely inspected to guarantee excellence. Any irregularities are meticulously corrected to maintain the high-quality standards ALTRON is known for.
C. Ensuring Compliance
In the end, it all comes down to compliance with design specifications. ALTRON ensures that each CNC machine wheel produced meets or exceeds the specified criteria for strength, durability, and performance.
Conclusion
CNC machining of wheels is a complex and precise operation that demands meticulous planning, design, and execution. ALTRON, a leading CNC machine wheels manufacturer, plays a crucial role in this process by providing state-of-the-art CNC machines that enable manufacturers to craft wheels that meet the highest standards of quality, performance, and aesthetics. Whether it’s for automotive, industrial, or specialized applications, CNC machining ensures that wheels roll out with precision and reliability.