Quality Unleashed: CNC Metal Flanging Solutions For Axial Fans
Axial fans are ubiquitous in modern industries, serving crucial roles in ventilation, cooling, and air circulation systems across various sectors. These fans play a pivotal role in ensuring optimal working conditions, energy efficiency, and equipment performance. Central to the effectiveness of axial fans are the precision-engineered components that comprise them.
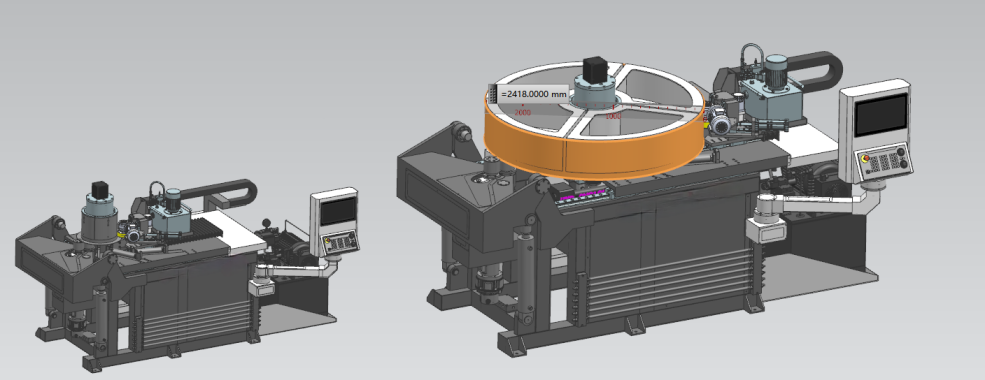
Enter CNC metal flanging, a revolutionary manufacturing process that has redefined the production landscape for axial fan components. In this blog, we delve into the significance of CNC metal flanging, its role in ensuring precision, and the advantages it brings to axial fan manufacturing, with a spotlight on ALTRON’s innovative solutions.
The Importance of Precision in Axial Fan Components
Precision is paramount in the design and production of axial fan components. Even the slightest deviation in dimensions or irregularity in shape can significantly impact the performance and efficiency of the fan. Precision ensures that components fit seamlessly together, minimizing air leakage and maximizing airflow. CNC metal flanging plays a crucial role in achieving this level of precision. Through computer-controlled processes, ALTRON can fabricate fan parts with unparalleled accuracy, meeting exacting specifications and tolerances.
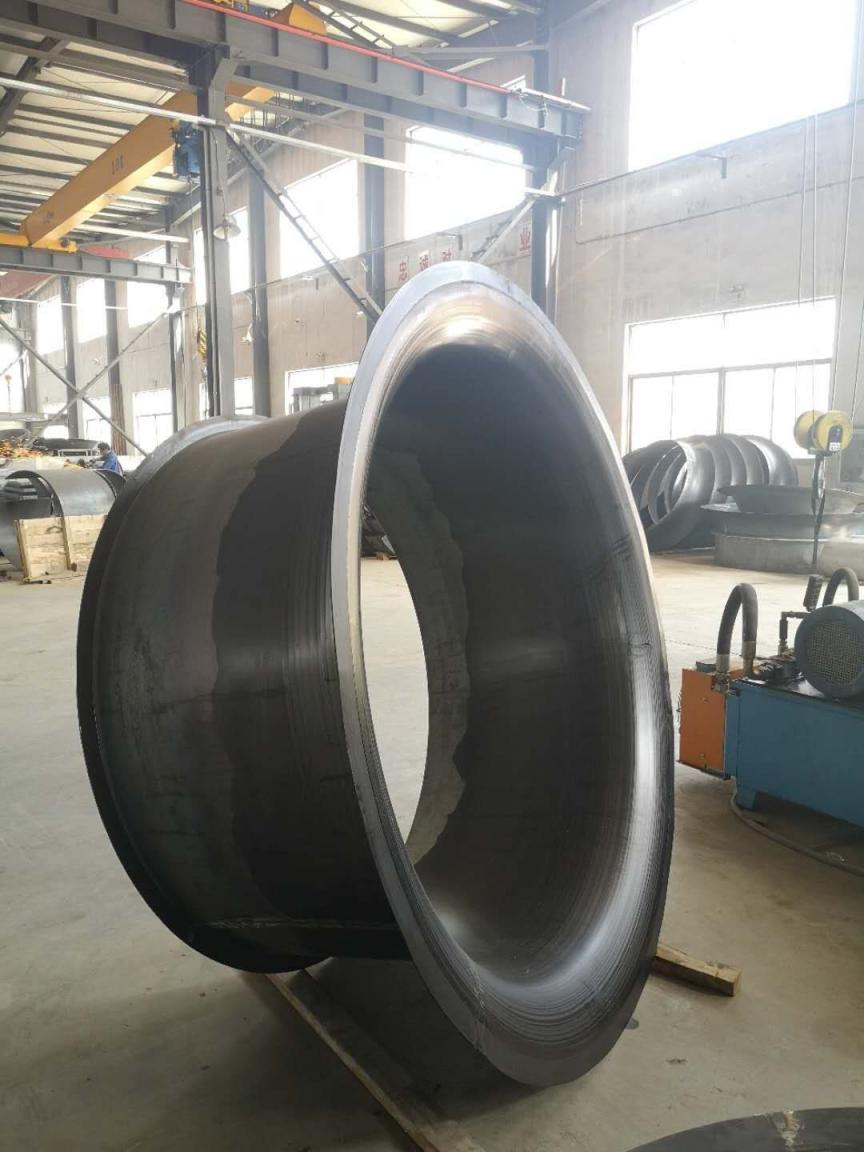
1.1 Ensuring Optimal Performance
Precision in axial fan components directly translates to optimal performance. Each component must function seamlessly within the fan assembly to maintain airflow, minimize turbulence, and achieve the desired cooling or ventilation effect. Whether it’s the curvature of fan blades or the dimensions of housing components, precision ensures that every element contributes to the fan’s efficiency and effectiveness.
1.2 Enhancing Energy Efficiency
Precision-engineered components reduce energy wastage by optimizing airflow and minimizing resistance. When components fit together seamlessly, the fan operates more efficiently, consuming less energy to achieve the desired output. This not only reduces operational costs but also contributes to sustainability efforts by conserving energy resources.
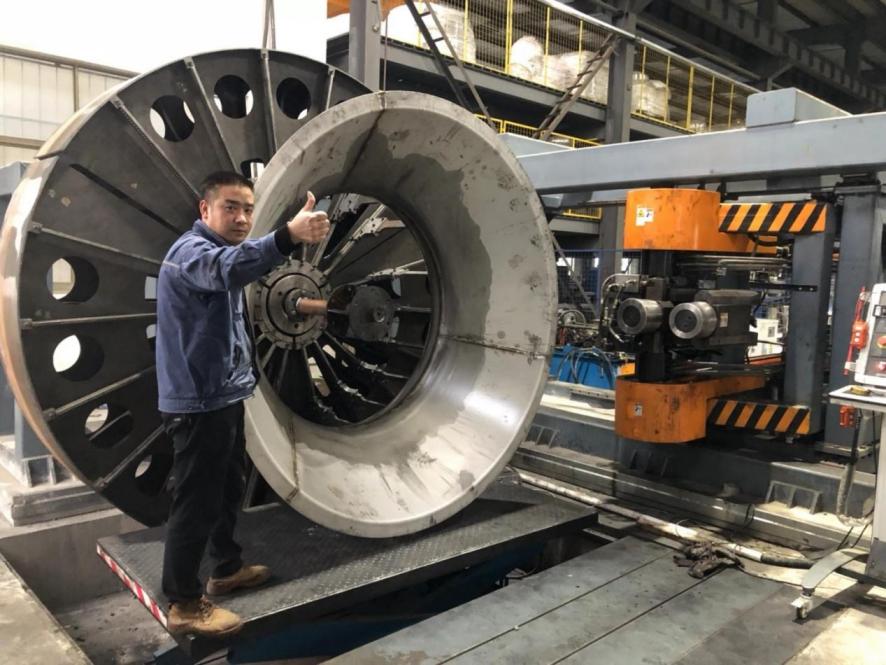
1.3 Prolonging Equipment Lifespan
Precision components are less prone to wear and tear, resulting in longer equipment lifespan. By minimizing friction, vibration, and stress on components, precision engineering reduces the risk of premature failure and extends the operational life of axial fans. This not only improves reliability but also reduces maintenance costs and downtime.
Understanding CNC Metal Flanging Techniques
CNC metal flanging encompasses a range of techniques tailored to meet the specific requirements of axial fan manufacturing. ALTRON leverages various methods, each offering unique advantages and applications in fan production.
2.1 Spinning
Spinning involves rotating a metal disc against a mandrel to form seamless, symmetrical shapes. This technique is ideal for producing cylindrical components such as fan housings and impellers. By controlling the speed and pressure of the spinning process, ALTRON can achieve precise dimensions and smooth surface finishes.
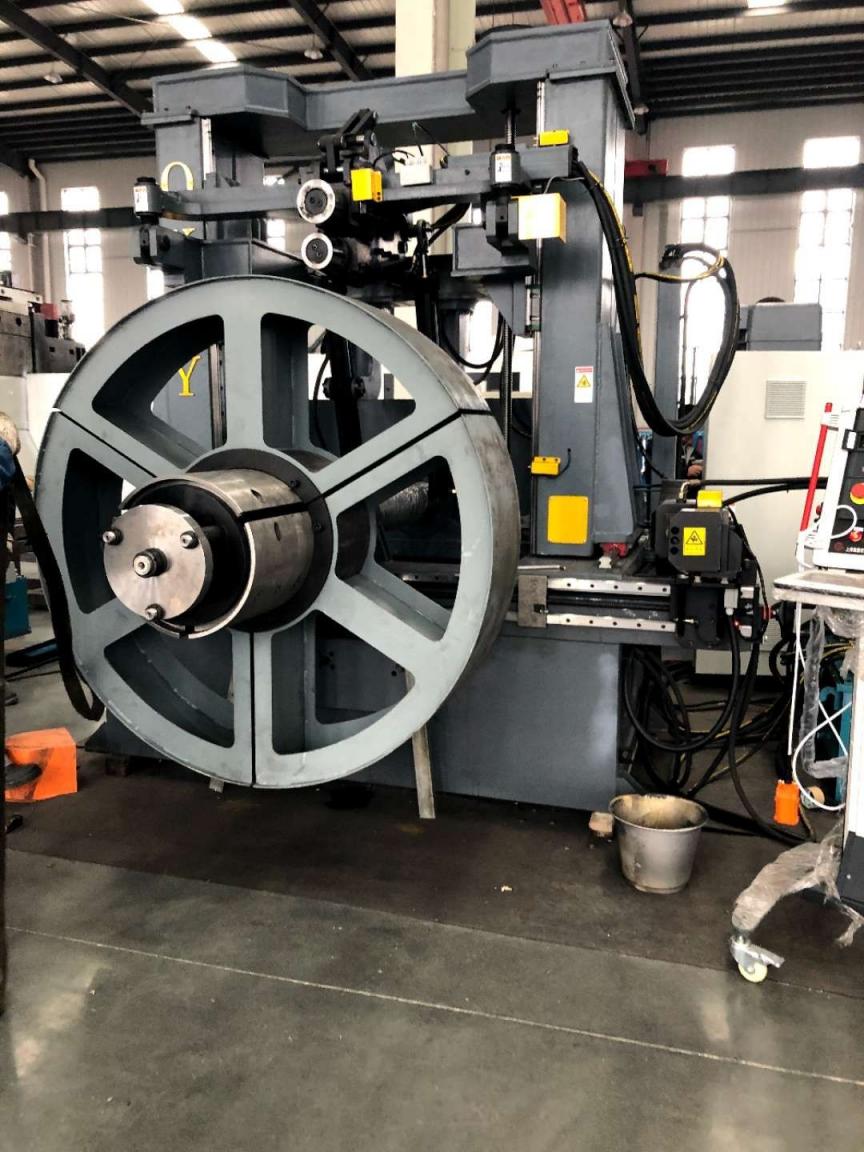
2.2 Pressing
Pressing utilizes hydraulic or mechanical force to shape metal sheets into intricate profiles. This technique is well-suited for producing fan blades, vanes, and other complex geometries. ALTRON’s state-of-the-art presses can exert precise pressure to create components with uniform thickness and accurate contours.
2.3 Forming
Forming involves using dies and punches to deform metal sheets into desired shapes. This versatile technique is suitable for producing a wide range of fan components, from bearing housings to shafts. ALTRON’s advanced forming capabilities allow for the creation of intricate features and tight tolerances, ensuring compatibility and reliability in fan assemblies.
Advantages of CNC Metal Flanging for Axial Fans
ALTRON’s adoption of CNC metal flanging brings forth a multitude of benefits for axial fan production, cementing its position as a leader in the industry.
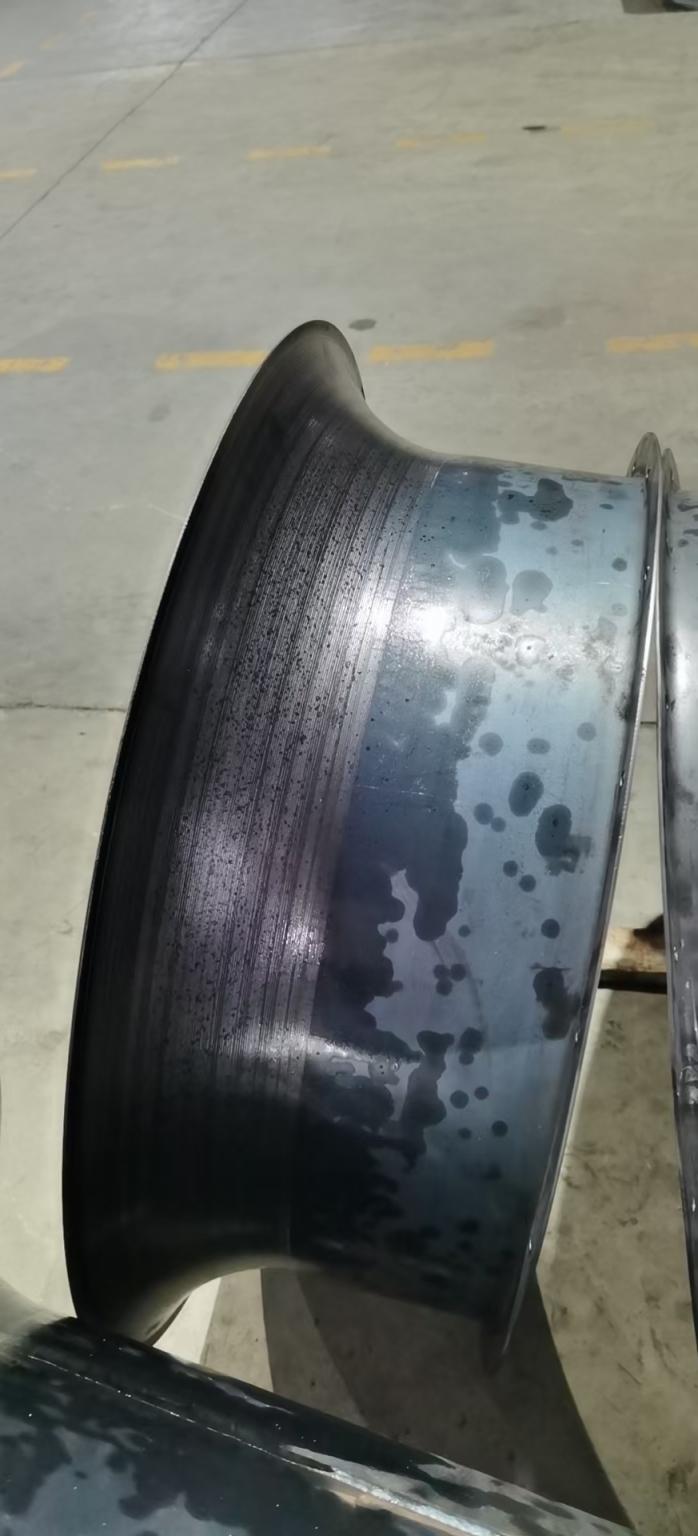
3.1 Increased Efficiency
CNC metal flanging ensures consistent quality and precise dimensions, resulting in axial fans that operate at peak efficiency. By minimizing air leakage and optimizing airflow, ALTRON’s precision-engineered components maximize the performance of fan systems, delivering superior ventilation, cooling, and air circulation.
3.2 Reduced Material Waste
Precision engineering minimizes material waste during the manufacturing process. By precisely shaping metal sheets into desired components, ALTRON minimizes scrap and offcuts, optimizing material utilization and reducing environmental impact. This not only contributes to sustainability efforts but also improves cost-effectiveness in fan production.
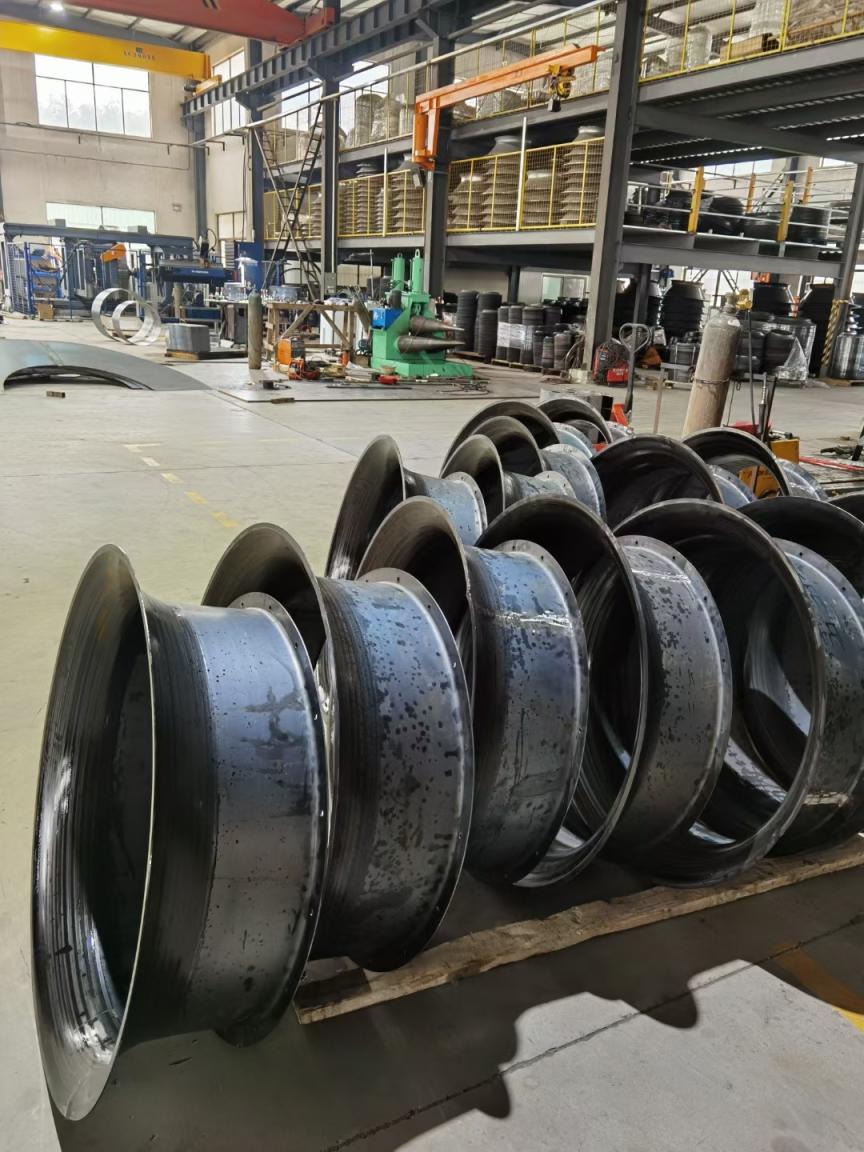
3.3 Enhanced Product Quality
ALTRON’s CNC metal flanging solutions guarantee unmatched quality and reliability in axial fan components. By adhering to strict quality control standards and leveraging advanced manufacturing techniques, ALTRON delivers components that meet or exceed industry standards. This ensures the longevity, durability, and performance of fan systems in diverse applications and operating conditions.
3.4 Cost-Effectiveness and Time-Saving
CNC metal flanging streamlines the manufacturing process, reducing lead times and production costs. ALTRON’s efficient production workflows and optimized processes enable swift turnaround times without compromising quality. This ensures that customers receive high-quality axial fan components on time and within budget, enhancing overall project efficiency and profitability.
Quality Control in CNC Metal Flanging Processes
Quality control measures are essential in CNC metal flanging to ensure dimensional accuracy, surface finish, and overall product quality. ALTRON implements rigorous quality control protocols throughout the manufacturing process to meet stringent industry standards and customer requirements.
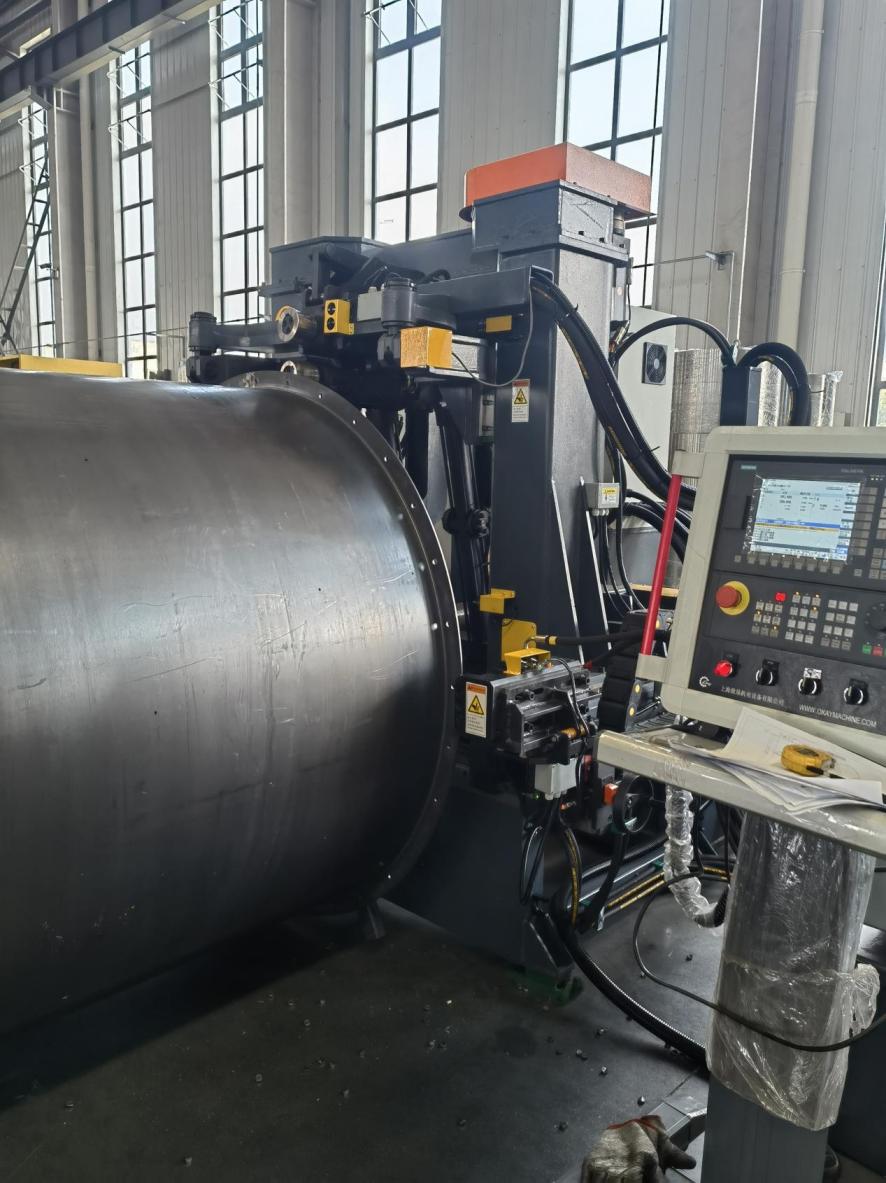
4.1 Importance of Quality Control Measures
Quality control measures are vital to identify and rectify any deviations or defects in the manufacturing process promptly. Dimensional accuracy is crucial in axial fan components to ensure proper fit and alignment within the fan assembly. Surface finish plays a significant role in performance and aesthetics, as smooth surfaces minimize airflow resistance and enhance corrosion resistance. By implementing quality control measures, ALTRON ensures that every component meets or exceeds specified tolerances and surface finish requirements.
4.2 Inspection Techniques
ALTRON employs a range of inspection techniques to verify dimensional accuracy and surface finish of CNC metal flanged components. These techniques include coordinate measuring machines (CMMs), optical comparators, surface profilometers, and visual inspection. CMMs use precise probes to measure component dimensions and compare them against CAD models or engineering drawings. Optical comparators magnify and project component images onto a screen for visual inspection and measurement. Surface profilometers measure surface roughness and texture to ensure compliance with specified requirements. Visual inspection is conducted to identify any defects or irregularities that may affect component performance or appearance.
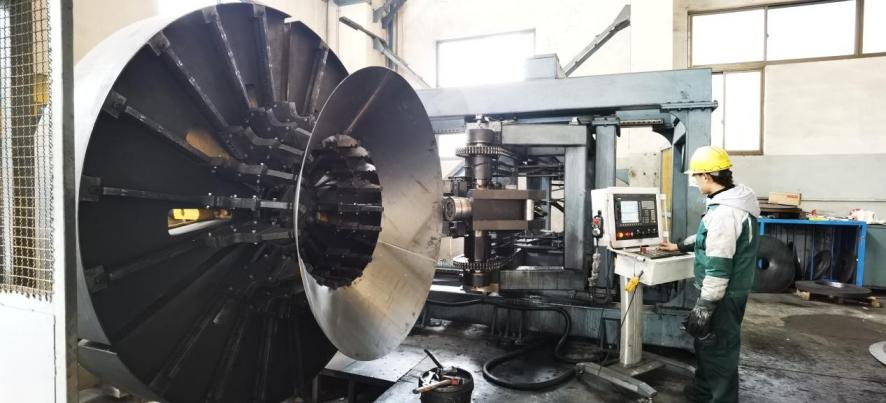
4.3 Implementation of Quality Control Protocols
ALTRON integrates quality control protocols into every stage of the manufacturing process, from material inspection and tool setup to final inspection and packaging. Advanced machining technologies, such as real-time monitoring and feedback systems, help detect and correct deviations during production. Statistical process control (SPC) techniques track process variability and identify trends to prevent defects and ensure consistency. By implementing comprehensive quality control protocols, ALTRON delivers axial fan components of the highest quality and reliability to meet customer expectations and industry standards.
Applications of CNC Metal Flanging in Axial Fan Design
CNC metal flanging offers unparalleled customization options and design flexibility, enabling innovative solutions in axial fan design. ALTRON leverages CNC technology to push the boundaries of fan design, catering to diverse applications and customer requirements.
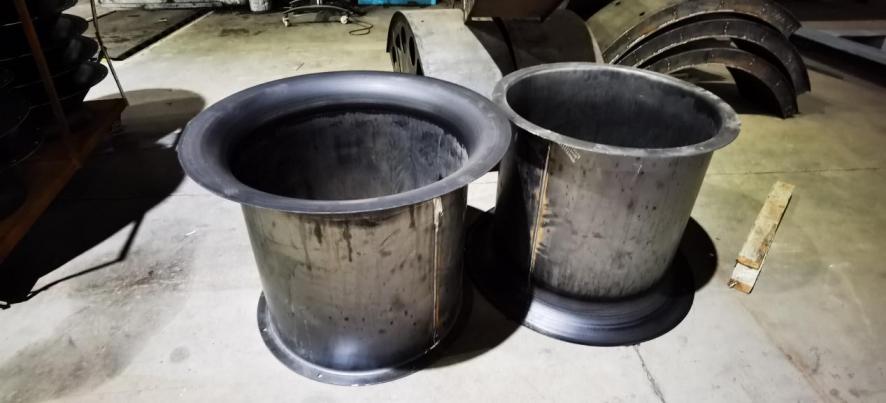
5.1 Influencing Axial Fan Design
CNC metal flanging enables precise fabrication of complex geometries and intricate features, allowing for optimized airflow, noise reduction, and energy efficiency. Customization options such as blade profiles, hub designs, and mounting configurations are easily achievable with CNC technology, ensuring tailored solutions for specific applications. ALTRON collaborates closely with customers to develop innovative fan designs that meet performance objectives while maximizing cost-effectiveness and reliability.
5.2 Design Flexibility
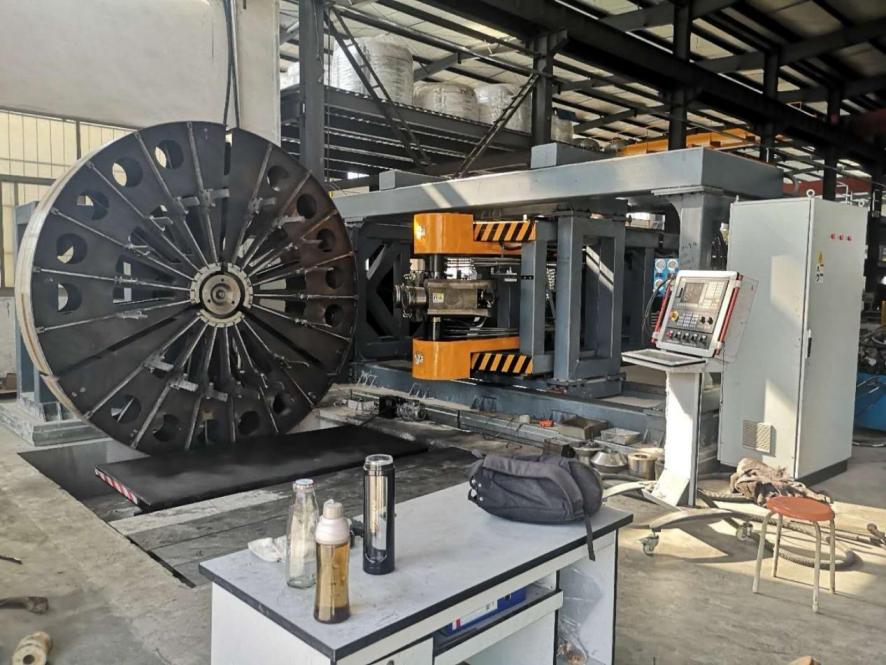
CNC metal flanging offers unmatched design flexibility, allowing for rapid prototyping and iteration of fan designs. ALTRON’s engineering team utilizes CAD/CAM software and simulation tools to optimize component designs for performance, manufacturability, and cost. By leveraging CNC technology, ALTRON can quickly translate design concepts into functional prototypes and production-ready components, reducing time-to-market and facilitating product innovation.
Future Trends in CNC Metal Flanging for Axial Fans
The future of CNC metal flanging for axial fans is characterized by advancements in automation, precision, and material capabilities, driven by emerging technologies and industry trends.
6.1 Emerging Technologies
Advancements in CNC machining technologies, such as multi-axis machining, robotic automation, and additive manufacturing, are poised to revolutionize axial fan manufacturing. Multi-axis machining allows for simultaneous machining of complex geometries, reducing setup time and increasing production efficiency. Robotic automation streamlines production workflows and enhances process flexibility, enabling lights-out manufacturing and unmanned operation. Additive manufacturing technologies, such as 3D printing, offer new possibilities for rapid prototyping and on-demand production of customized fan components.
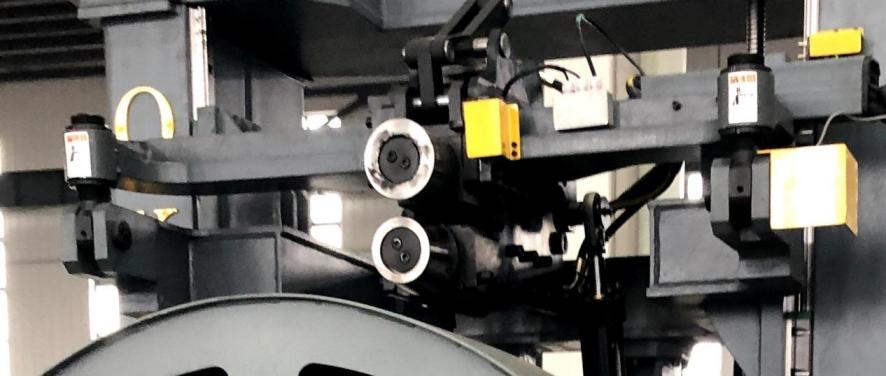
6.2 Precision Engineering
The demand for higher precision and tighter tolerances in axial fan components continues to drive advancements in CNC metal flanging technology. Improved tooling, cutting strategies, and metrology techniques enable finer surface finishes, smoother transitions, and more precise geometries. As industries seek to optimize energy efficiency, reduce noise emissions, and enhance equipment performance, CNC metal flanging solutions will play a critical role in delivering precision-engineered fan components that meet evolving requirements.
6.3 Material Innovations
Advances in material science and processing techniques expand the range of materials available for CNC metal flanging, offering new possibilities for lightweighting, corrosion resistance, and thermal management. Composite materials, hybrid alloys, and nanostructured materials present opportunities for designing fan components with enhanced mechanical properties and performance characteristics. ALTRON continues to invest in research and development to explore novel materials and manufacturing processes that push the boundaries of axial fan design and performance.
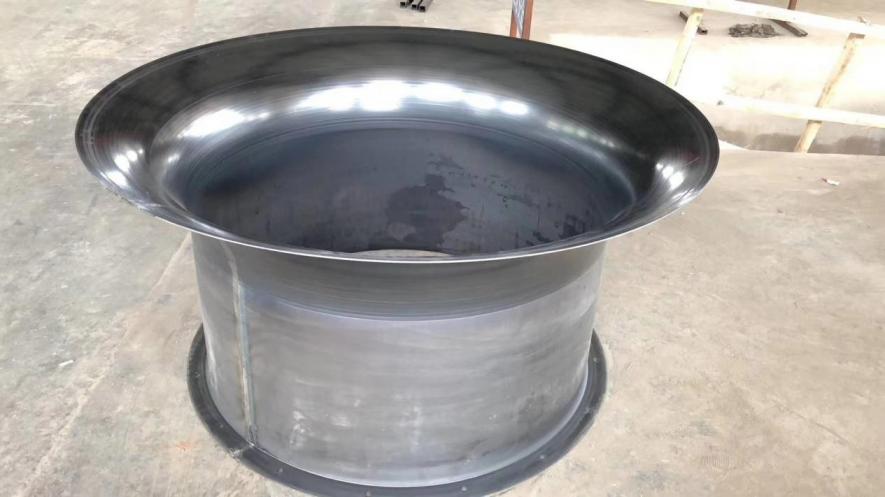
Conclusion
In conclusion, CNC metal flanging solutions offered by ALTRON have transformed the landscape of axial fan manufacturing, setting new standards for precision, quality, and efficiency. Through precision engineering, advanced technology, and a commitment to excellence, ALTRON continues to lead the way in delivering innovative solutions that meet the evolving needs of industries worldwide. As the demand for high-performance axial fans continues to grow, ALTRON remains at the forefront, driving innovation and shaping the future of fan technology. With CNC metal flanging, ALTRON empowers industries to achieve optimal airflow, energy efficiency, and equipment performance, ensuring a sustainable and prosperous future.