Considering a CNC Metal Spinning Lathe Purchase? Ensure You Make the Right Choice
Explore the world of CNC metal spinning lathes with our comprehensive blog covering maintenance tips, safety measures, future trends, and success stories. Learn about ALTRON AUTO’s innovative solutions and how they can enhance efficiency and productivity in metal fabrication. Discover the latest advancements in technology and gain insights into optimizing your manufacturing processes for success.
Introduction to CNC Metal Spinning Lathe
CNC metal spinning lathes revolutionize metalworking processes by combining computer numerical control (CNC) technology with the traditional art of metal spinning. These lathes utilize automated controls to precisely shape metal blanks into various forms, ranging from simple cylindrical shapes to intricate designs.
1.1 What is CNC Metal Spinning Lathe?
CNC metal spinning lathes are advanced machines that use computer-controlled movements to rotate a metal blank while shaping it against a mandrel or mold. The spinning process involves gradually forming the metal into the desired shape through a combination of spinning and pressure. This method offers exceptional precision and repeatability, making it ideal for manufacturing components with complex geometries.
1.2 Benefits of CNC Metal Spinning Lathe
Compared to traditional metal spinning techniques, CNC metal spinning lathes offer several advantages. Firstly, they significantly reduce production time and labor costs by automating the spinning process. Additionally, CNC technology enables precise control over parameters such as speed, pressure, and tool movements, resulting in consistent quality and accuracy across multiple parts.
1.3 Industries and Applications
CNC metal spinning lathes find applications across various industries, including aerospace, automotive, lighting, and household appliances. They are commonly used to produce components such as engine housings, lampshades, cookware, and decorative pieces. The versatility of these machines allows manufacturers to fulfill diverse design requirements efficiently.
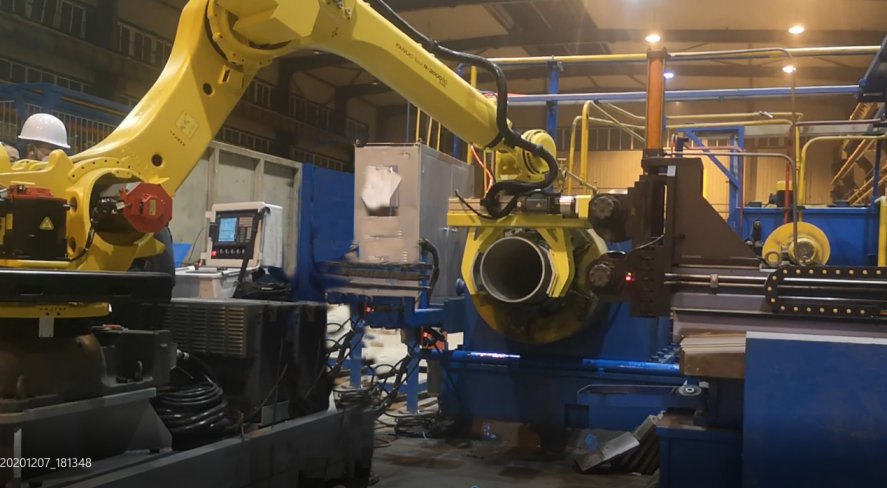
Key Features and Components of CNC Metal Spinning Lathes
CNC metal spinning lathes consist of several crucial components that work together to facilitate the spinning process and achieve the desired results.
2.1 Components Breakdown
- Spindle:The spindle holds and rotates the metal blank during the spinning process. It’s essential for maintaining precise rotational speed and stability.
- Tool Rest: This component supports the spinning tool and controls its movement as it shapes the metal blank.
- Control System:The CNC control system interprets programming instructions and coordinates the movements of the spindle and tool rest.
- Chuck and Mandrel: The chuck secures the metal blank in place, while the mandrel provides support and defines the internal shape of the spun part.
- Drive Mechanism: Various mechanisms, such as servo motors or hydraulic systems, drive the rotation and movement of the spindle and tool rest.
2.2 Key Features
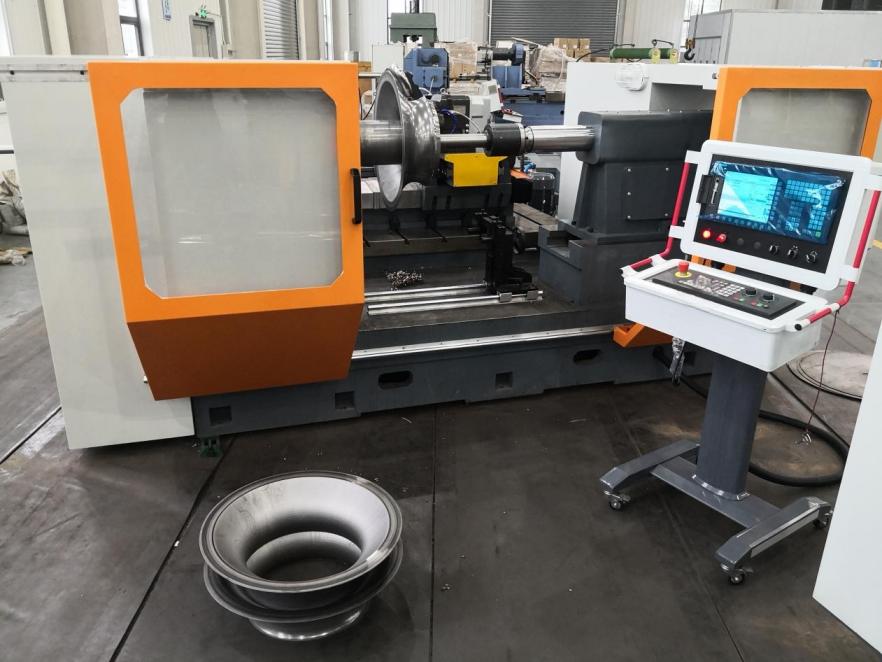
- Precision Machining:CNC metal spinning lathes offer high precision and repeatability, ensuring consistent quality in produced parts.
- Flexibility:These machines can accommodate a wide range of metal materials and part geometries, making them versatile for different applications.
- Automation:Automated controls streamline the spinning process, reducing manual intervention and minimizing errors.
- Integrated Software:Advanced software enables programming of complex shapes and facilitates seamless integration with CAD/CAM systems for design optimization.
2.3 Comparison of Models
When choosing a CNC metal spinning lathe, considerations such as maximum part diameter, spindle speed range, tooling options, and control system capabilities are essential. Manufacturers like ALTRON AUTO offer a range of models with varying specifications to suit different production requirements and budgets.
Advantages of Investing in a CNC Metal Spinning Lathe
Investing in a CNC metal spinning lathe can yield numerous benefits for businesses involved in metal fabrication.
3.1 Cost-effectiveness and Efficiency
CNC metal spinning lathes improve production efficiency by reducing setup time, minimizing material waste, and optimizing machining processes. This results in lower per-part costs and increased profitability over time.
3.2 Quality Control and Precision
The precision afforded by CNC technology ensures that each spun part meets strict quality standards. Consistent dimensional accuracy and surface finish contribute to the overall quality of the manufactured components.
3.3 Versatility and Flexibility
CNC metal spinning lathes offer versatility in terms of material compatibility, part complexity, and design customization. This flexibility enables manufacturers to adapt to changing market demands and explore new opportunities.
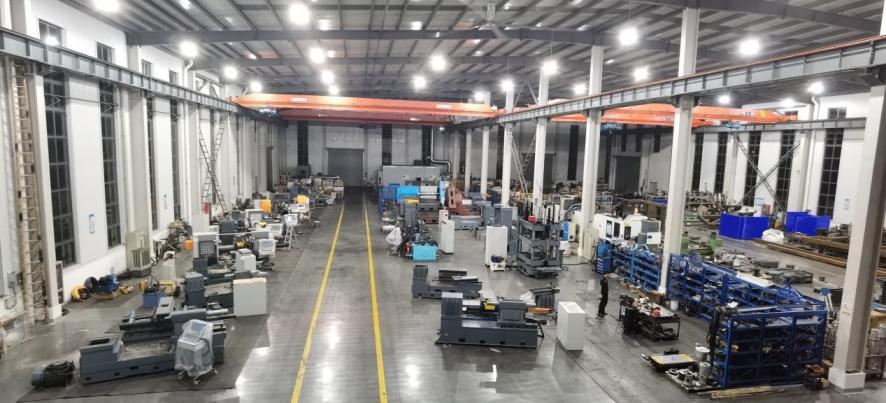
Choosing the Right CNC Metal Spinning Lathe for Your Business
Selecting the appropriate CNC metal spinning lathe requires careful consideration of various factors to ensure optimal performance and return on investment.
4.1 Factors to Consider
- Size and Capacity: Determine the maximum part size and weight your business needs to produce to choose a lathe with adequate capacity.
- Budget:Consider upfront costs, ongoing maintenance expenses, and potential ROI when evaluating different models.
- Performance Specifications: Pay attention to spindle speed, tooling options, control system features, and additional capabilities that align with your production requirements.
- Support and Training: Evaluate the manufacturer’s customer support services, training programs, and warranty coverage to ensure ongoing operational efficiency and reliability.
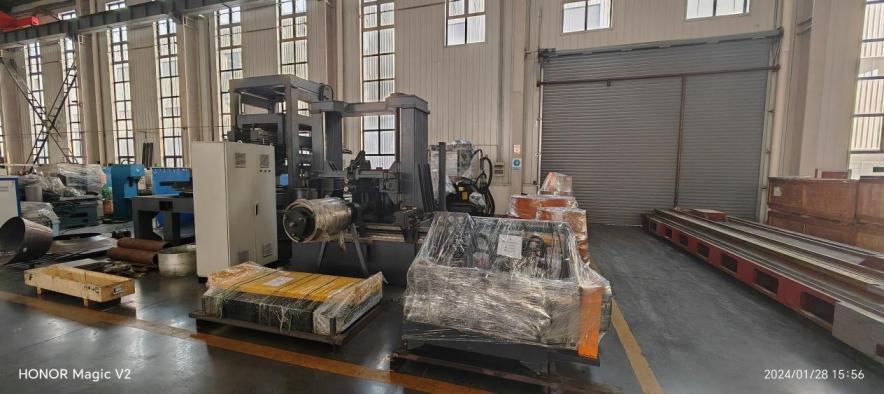
Maintenance and Care Tips for CNC Metal Spinning Lathes
Regular maintenance is crucial for ensuring optimal performance and extending the lifespan of CNC metal spinning lathes. Neglecting maintenance tasks can lead to increased downtime, reduced efficiency, and potential damage to the machine.
5.1 Importance of Regular Maintenance
Maintaining a CNC metal spinning lathe is essential to keep it operating at peak performance. Regular maintenance helps prevent wear and tear on components, reduces the risk of breakdowns, and ensures consistent quality in produced parts. By following a maintenance schedule, businesses can minimize unexpected downtime and maximize productivity.
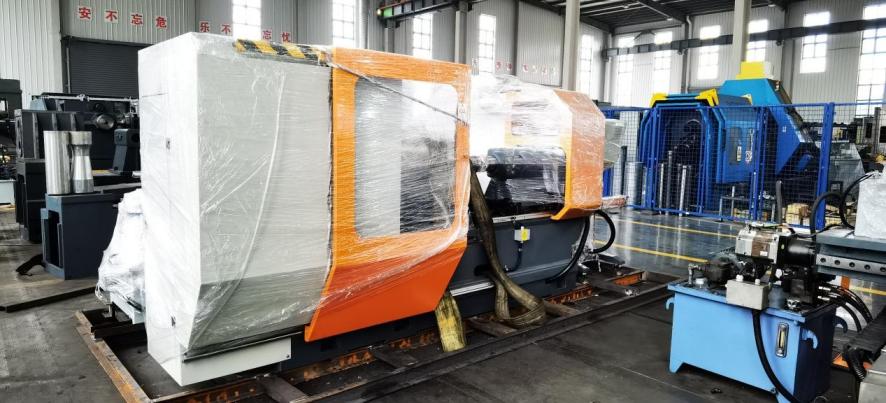
5.2 Basic Maintenance Tasks
- Lubrication:Proper lubrication of moving parts is critical for preventing friction and minimizing wear. Follow manufacturer recommendations for the type and frequency of lubrication. Regularly inspect and replenish lubricants as needed to keep the machine running smoothly.
- Calibration:Regular calibration ensures that the CNC metal spinning lathe maintains accuracy and precision in its operations. Calibrate components such as the spindle, tool rest, and control system according to manufacturer specifications. Use precision instruments to verify and adjust settings as necessary.
- Cleaning:Keep the machine clean and free of debris to prevent contamination and damage to sensitive components. Regularly remove chips, dust, and coolant residue from the work area and machine surfaces. Use compressed air or specialized cleaning tools to reach tight spaces and remove buildup.
5.3 Troubleshooting Common Issues
Despite regular maintenance, CNC metal spinning lathes may encounter issues that require troubleshooting. Common problems include tool wear, programming errors, and mechanical malfunctions. Operators should be trained to identify and address these issues promptly to minimize downtime and prevent further damage. If unable to resolve the problem, seek assistance from qualified technicians or the manufacturer’s support team.
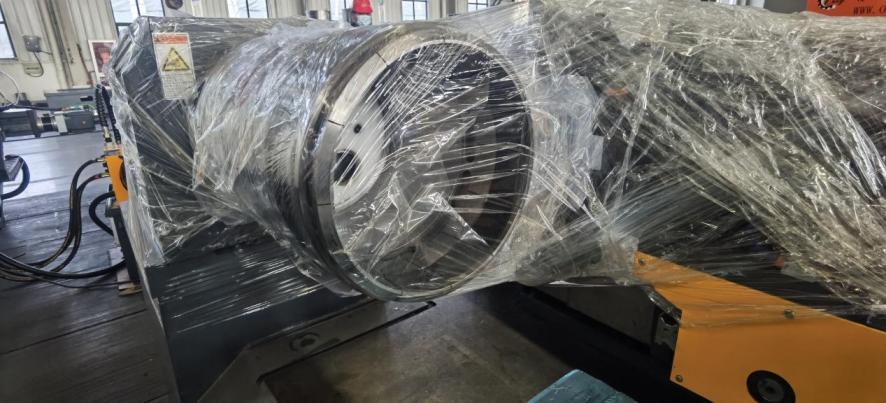
Safety Measures When Operating CNC Metal Spinning Lathes
Operating CNC metal spinning lathes involves inherent risks that require strict adherence to safety protocols and guidelines.
6.1 Potential Hazards
- Mechanical Hazards: Moving parts such as the spindle and tool rest pose crush and entanglement hazards if not properly guarded.
- Chemical Hazards:Coolants and lubricants used in machining processes can be hazardous if mishandled or exposed to skin or eyes.
- Electrical Hazards:High-voltage components and electrical systems pose risks of electric shock if not properly maintained or operated.
6.2 Safety Protocols
- Machine Guarding:Ensure all moving parts are adequately guarded to prevent accidental contact. Install safety interlocks and emergency stop buttons to immediately halt machine operations in case of emergencies.
- Personal Protective Equipment (PPE): Provide operators with appropriate PPE such as safety glasses, gloves, and hearing protection to minimize risks of injury.
- Training and Education: Properly train operators on safe operating procedures, hazard recognition, and emergency response protocols. Regularly conduct refresher training to reinforce safety practices and address any new hazards or concerns.
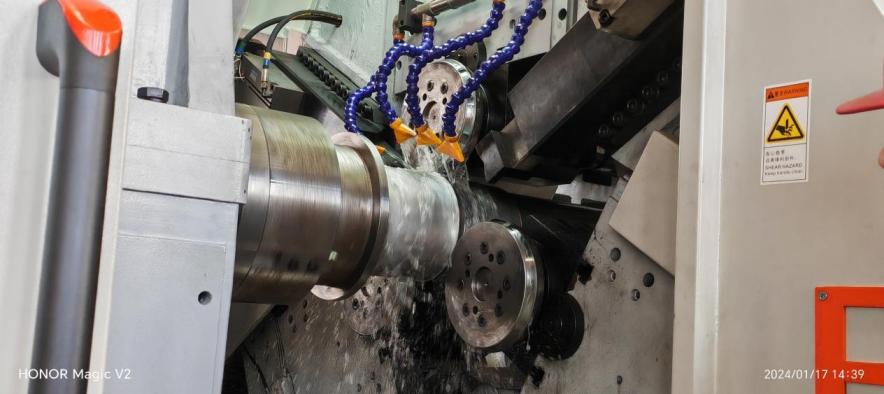
Future Trends in CNC Metal Spinning Technology
The future of CNC metal spinning technology is marked by advancements in automation, software integration, and material compatibility.
7.1 Emerging Technologies
- Automation: Increasing automation in CNC metal spinning lathes streamlines production processes, reduces reliance on manual labor, and improves efficiency.
- Software Integration:Integration with advanced CAD/CAM software enhances design capabilities, optimizes tool paths, and improves overall machining efficiency.
- Material Innovation: Advancements in material science enable CNC metal spinning lathes to work with a wider range of materials, including composites and exotic alloys, expanding their applications in various industries.
7.2 Implications for Businesses
Businesses adopting CNC metal spinning technology stand to benefit from increased productivity, improved quality control, and enhanced competitiveness. By embracing emerging trends and investing in state-of-the-art equipment, manufacturers can stay ahead of the curve and meet evolving customer demands.
Case Studies: Success Stories with CNC Metal Spinning Lathes
Real-world examples highlight the transformative impact of CNC metal spinning technology on businesses and industries.
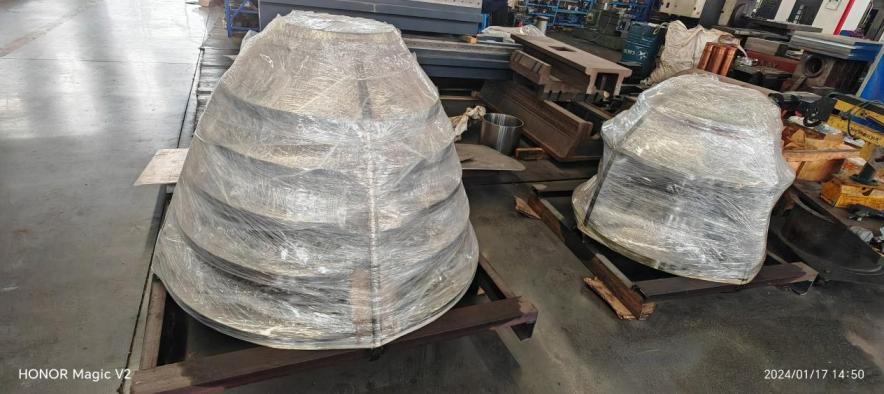
8.1 Testimonials
- ALTRON AUTO Customer:“Since integrating ALTRON AUTO’s CNC metal spinning lathe into our production line, we’ve seen a significant improvement in efficiency and quality. The precision and versatility of the machine have allowed us to expand our product offerings and attract new customers.”
- Industry Leader: “By leveraging CNC metal spinning technology, we’ve been able to reduce lead times, minimize material waste, and deliver superior products to our customers. The investment in advanced machining equipment has paid off in terms of increased profitability and market share.”
8.2 Analysis of ROI
Businesses that invest in CNC metal spinning lathes can expect a positive return on investment through cost savings, productivity gains, and improved competitiveness. The ability to produce high-quality parts efficiently translates into higher customer satisfaction and repeat business, further enhancing profitability in the long run.
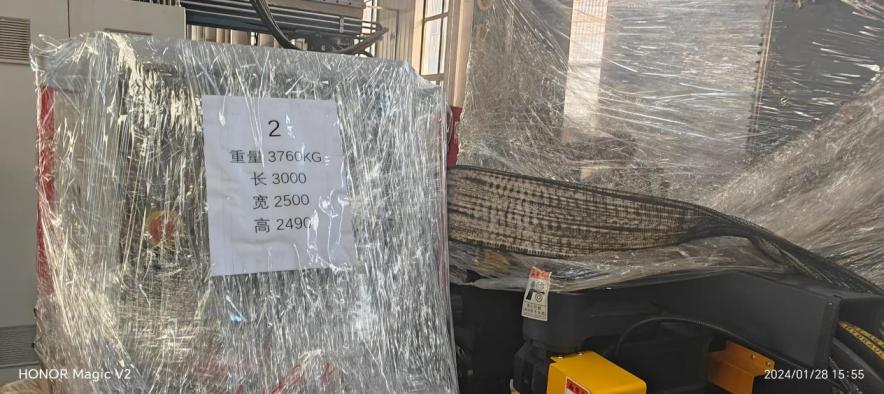
Conclusion
CNC metal spinning lathes represent a significant advancement in metalworking technology, offering efficiency, precision, and versatility for manufacturers across various industries. By understanding their features, benefits, and considerations for selection, businesses can make informed decisions to enhance their production capabilities and remain competitive in today’s market. For those seeking a reliable manufacturer, ALTRON AUTO stands out with its range of high-quality CNC metal spinning lathes designed to meet diverse manufacturing needs.