Can CNC Metal Spinning Lathe Enhances Efficiency and Cost-Effectiveness in Production?
Uncover the groundbreaking capabilities of CNC metal spinning technology, delving into its impact on quality control, contrasts with alternative metal forming methods, recent technological strides, and practical industry applications. Explore the innovative contributions of manufacturers such as ALTRON AUTO in shaping the evolution of metal fabrication.
Introduction to CNC Metal Spinning Lathes
1.1 Definition and Brief History of Metal Spinning
Metal spinning, also known as spin forming or spinning, is a metalworking process where a disc or tube of metal is rotated at high speeds and formed into a symmetrical shape over a mandrel or form. This technique has been used for centuries, with evidence of its use dating back to ancient civilizations. Initially performed manually, metal spinning has evolved significantly with technological advancements.
1.2 Explanation of CNC Technology in Metal Spinning
CNC (Computer Numerical Control) technology has revolutionized metal spinning by automating the process and enhancing precision and efficiency. CNC metal spinning lathes are equipped with computer-controlled systems that precisely manipulate the spinning tool and workpiece. This automation allows for complex shapes to be formed with consistency and accuracy, significantly reducing production time and labor costs.
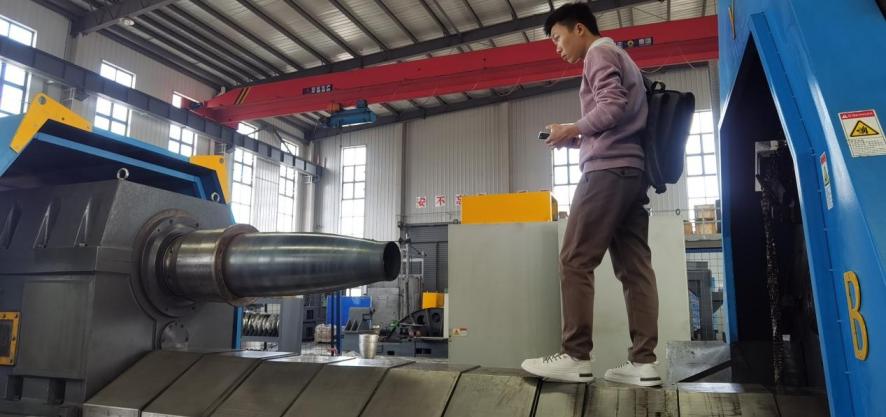
1.3 Advantages of CNC Metal Spinning Lathes over Traditional Methods
- Precision and Consistency: CNC metal spinning lathes offer unmatched precision and consistency compared to manual methods, ensuring uniformity in finished products.
- Efficiency: Automation reduces setup times and increases production rates, making CNC metal spinning lathes highly efficient.
- Complexity:CNC technology enables the production of intricate shapes and designs that may be challenging or impossible with manual spinning.
- Cost-Effectiveness: While initial investment costs may be higher, the long-term cost savings from reduced labor and increased productivity make CNC metal spinning lathes economically advantageous.
1.4 Overview of Industries and Applications
CNC metal spinning lathes find applications across various industries, including aerospace, automotive, lighting, and home appliance manufacturing. They are used to produce a wide range of components such as lampshades, cookware, engine parts, and reflectors. The versatility of CNC metal spinning lathes makes them indispensable in industries that require high-quality, customized metal components.
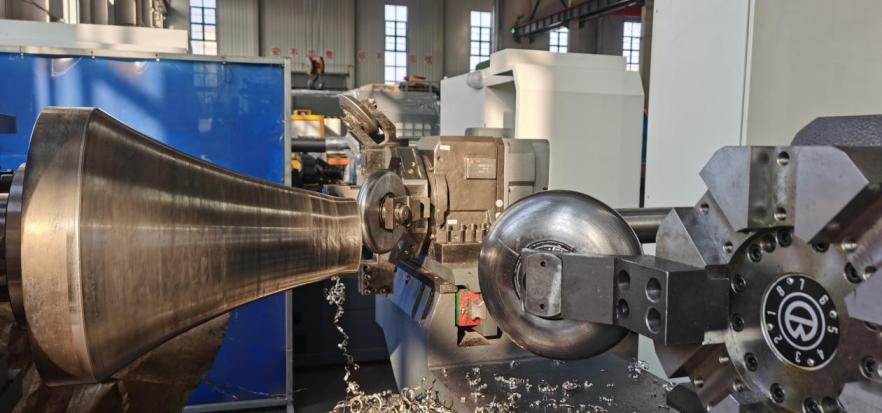
Key Components of a CNC Metal Spinning Lathe
2.1 Main Components
- Spindle: The spindle holds and rotates the workpiece during the spinning process. b. Tooling: Tooling includes the forming tools and mandrels used to shape the metal.
- Control System: The control system consists of the computer and software that govern the movement of the spinning tool.
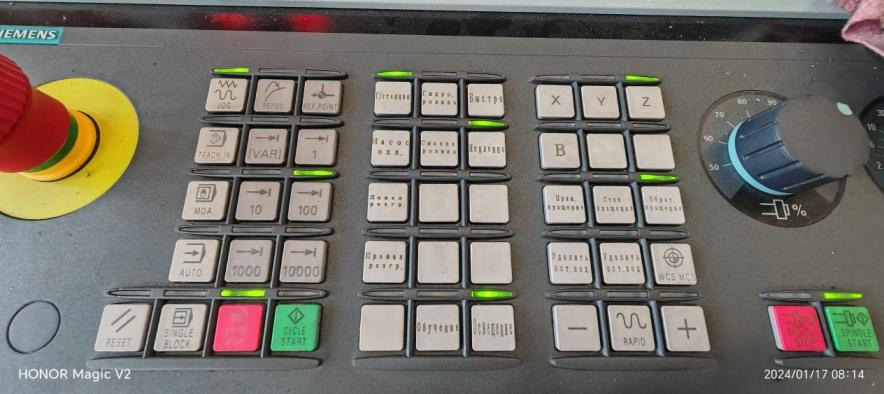
2.2 Detailed Explanation of Each Component’s Function
- Spindle: The spindle provides rotational motion to the workpiece, allowing it to be formed into the desired shape.
- Tooling: Forming tools and mandrels exert pressure on the metal, causing it to deform and take the shape of the tool.
- Control System: The control system interprets CNC programs and commands the movement of the spinning tool with precision.
2.3 Importance of Precision and Durability
Precision and durability are crucial in CNC metal spinning lathe components to ensure consistent performance and longevity. High-quality materials and precise manufacturing processes are essential to withstand the rigors of metal spinning operations and maintain tight tolerances.
2.4 Discussion on Modern Advancements
Modern advancements in CNC metal spinning lathe technology focus on improving automation, enhancing software capabilities, and integrating advanced materials. These advancements aim to further increase productivity, reduce cycle times, and expand the range of possible shapes and designs.
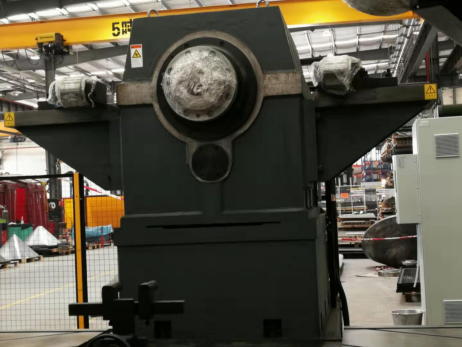
Setting Up and Operating a CNC Metal Spinning Lathe
3.1 Setting Up Guide
- Prepare Workpiece: Ensure the workpiece is securely mounted on the spindle.
- Select Tooling:Choose appropriate forming tools and mandrels based on the desired shape and material.
- Program CNC: Input the CNC program specifying the spinning operation parameters.
- Calibration: Calibrate the machine to ensure accuracy and repeatability.
3.2 Safety Protocols
- Wear Personal Protective Equipment: Operators should wear safety goggles, gloves, and other protective gear.
- Machine Guards: Ensure machine guards are in place to prevent accidents.
- Emergency Stop:Familiarize yourself with the location of the emergency stop button and its proper use.
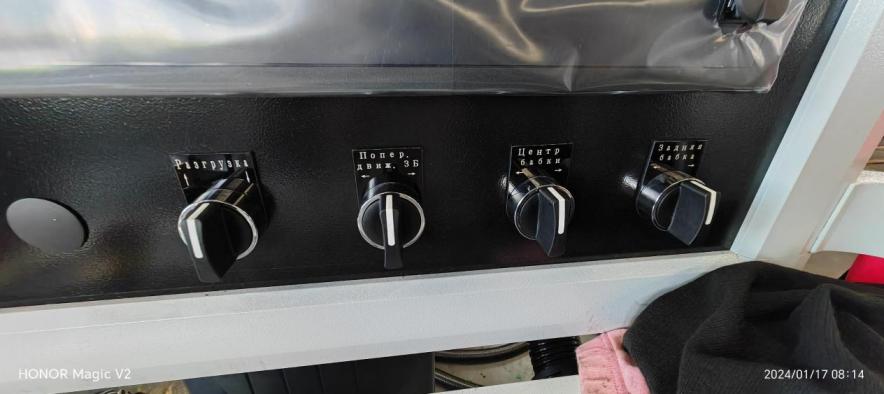
3.3 CNC Programming
- Tool Paths: Define the tool paths required to achieve the desired shape.
- Speed and Feed Rates: Set appropriate speed and feed rates based on material and tooling.
- Testing: Conduct trial runs to verify the program before running full production.
3.4 Tips for Optimization
- Tool Maintenance:Regularly inspect and maintain tooling to ensure optimal performance.
- Material Handling:Use quality materials and handle them with care to prevent defects.
- Process Monitoring: Monitor the spinning process for any deviations and make adjustments as necessary.
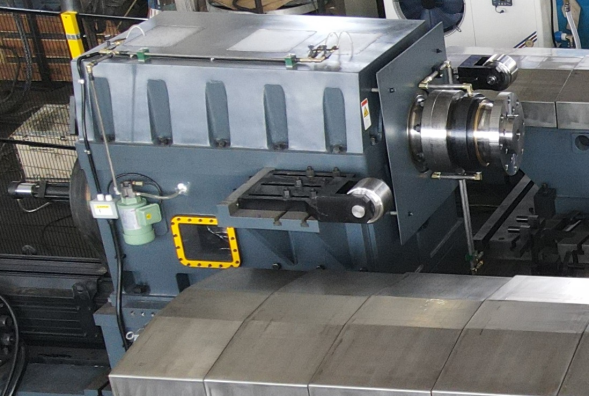
Materials and Designs Suitable for CNC Metal Spinning
4.1 Overview of Materials
- Aluminum:Lightweight and malleable, aluminum is commonly used for aerospace and automotive components.
- Stainless Steel: Known for its corrosion resistance, stainless steel is ideal for applications requiring durability and aesthetics.
- Copper:With excellent conductivity, copper is often used for electrical and decorative purposes.
4.2 Design Possibilities
- Symmetrical Shapes: CNC metal spinning enables the production of symmetrical shapes such as cones, domes, and cylinders with precision.
- Customization: Designs can be customized to meet specific requirements, allowing for unique and innovative solutions.
- Complex Geometries:Advanced CAD/CAM software facilitates the creation of complex geometries that were previously challenging to achieve.
4.3 Case Studies
- Automotive Reflectors:CNC metal spinning is used to produce reflective surfaces for automotive headlights, ensuring optimal light distribution and visibility.
- Decorative Lampshades:Intricate designs and patterns can be effortlessly achieved with CNC metal spinning, enhancing the aesthetics of decorative lampshades.
- Medical Equipment: CNC metal spinning is utilized in the production of medical equipment components such as surgical instruments and imaging devices, where precision is critical.
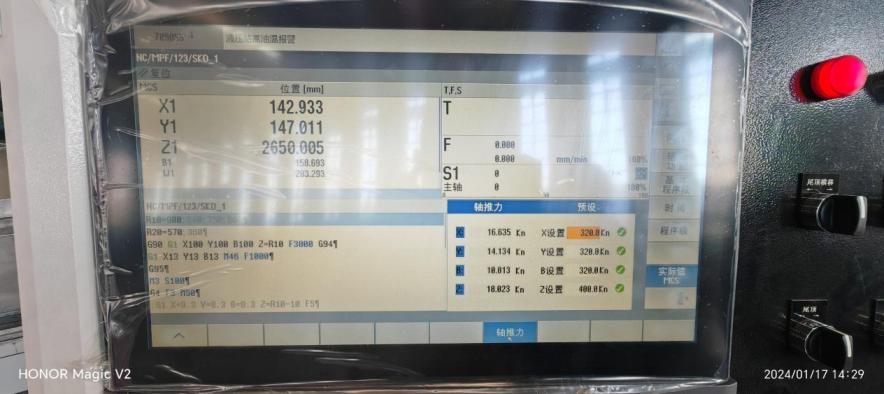
Quality Control and Inspection in CNC Metal Spinning
5.1 Importance of Quality Control
Quality control is paramount in CNC metal spinning processes to ensure the production of high-quality parts that meet specifications and standards. Consistency in dimensions, surface finish, and material integrity is essential for the functionality and aesthetics of spun metal parts.
5.2 Overview of Inspection Techniques
- Dimensional Inspection: Utilizing tools such as calipers, micrometers, and coordinate measuring machines (CMMs) to verify part dimensions against design specifications.
- Surface Finish Analysis:Assessing surface roughness using profilometers or visual inspection to ensure desired surface quality.
- Material Integrity Testing: Employing non-destructive testing methods like ultrasonic testing or dye penetrant inspection to detect defects without compromising the integrity of the part.
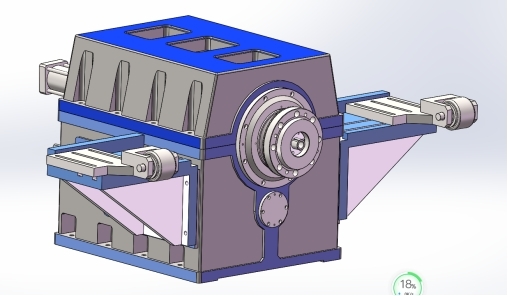
5.3 Discussion on Tolerances and Surface Finishes
CNC metal spinning can achieve tight tolerances and excellent surface finishes, making it suitable for applications requiring precision and aesthetics. Tolerances as low as ±0.005 inches are achievable, while surface finishes ranging from rough to mirror-like can be attained, depending on the material and spinning parameters.
5.4 Strategies for Ensuring Consistency
- Process Optimization: Fine-tuning spinning parameters such as spindle speed, feed rate, and tooling geometry to optimize part quality.
- Regular Maintenance: Periodic maintenance of CNC metal spinning lathes and tooling to prevent wear and ensure consistent performance.
- Continuous Monitoring:Implementing real-time monitoring systems to detect deviations during the spinning process and make immediate adjustments.
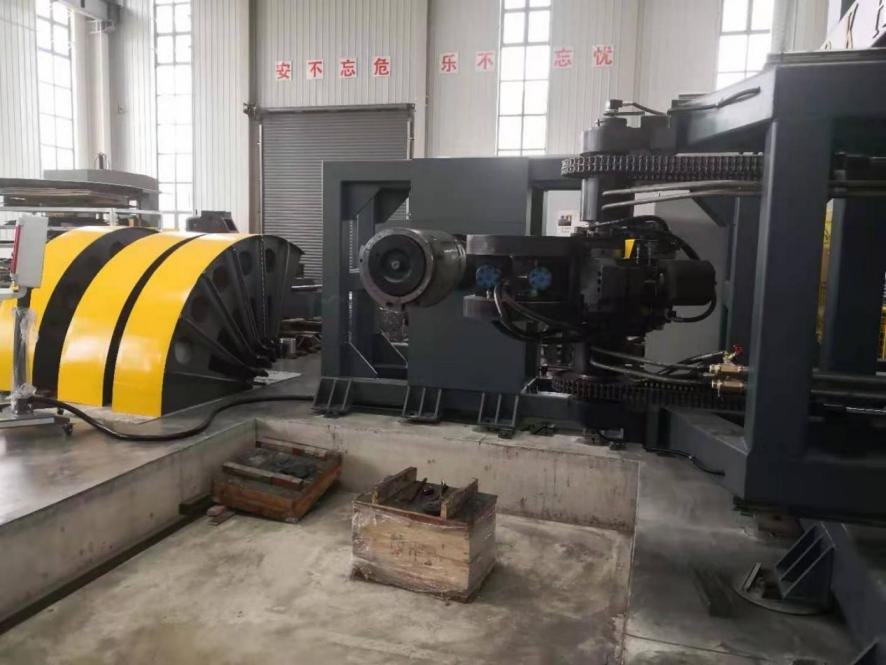
Comparing CNC Metal Spinning with Other Metal Forming Techniques
6.1 Comparison with Traditional Spinning Methods
CNC metal spinning offers several advantages over traditional spinning methods, including higher precision, repeatability, and automation. While traditional spinning relies on manual operation, CNC metal spinning utilizes computer-controlled systems for enhanced accuracy and efficiency.
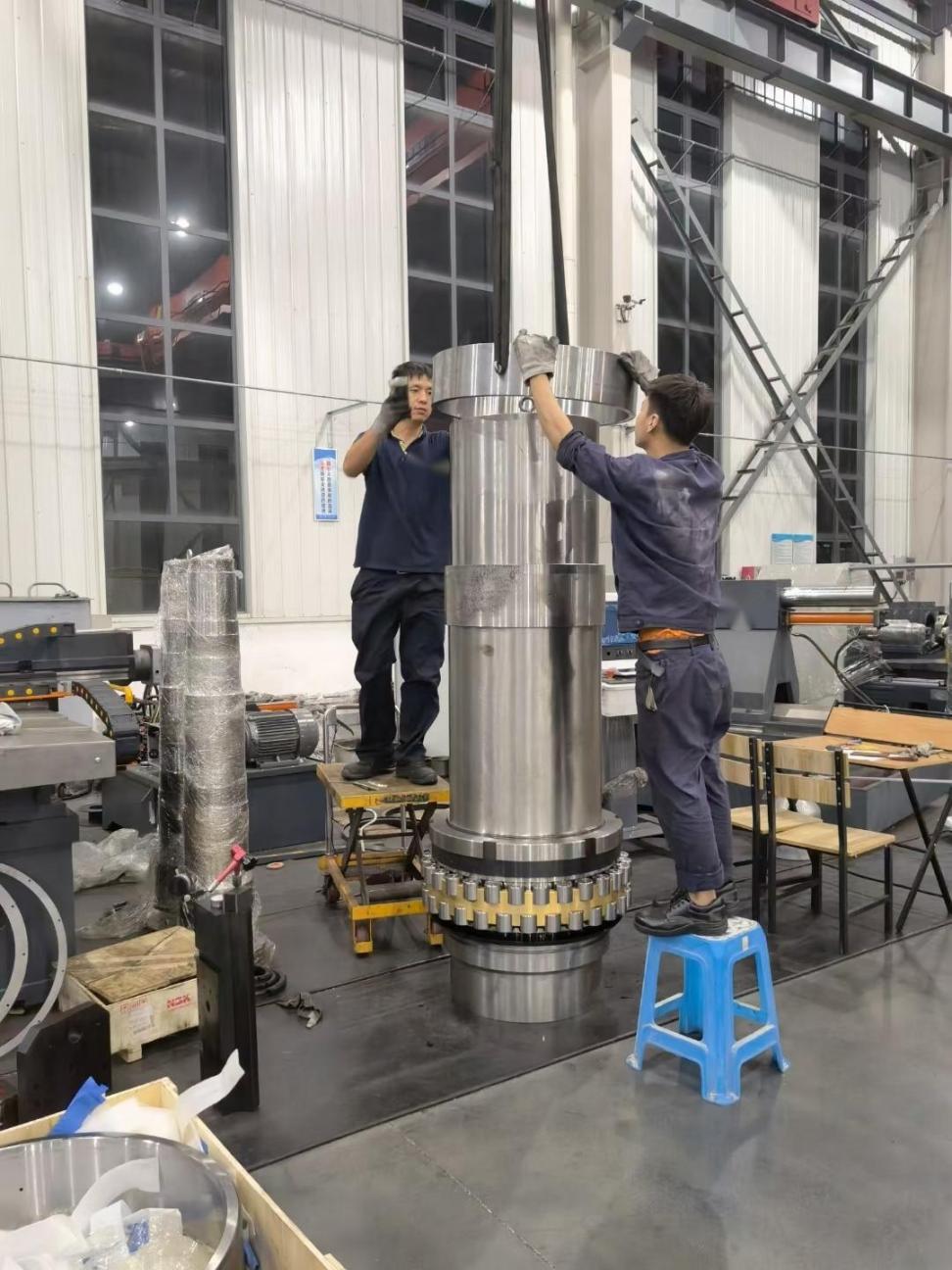
6.2 Contrasting with Other Metal Forming Techniques
- CNC Machining: CNC machining removes material from a solid block to form the desired shape, making it suitable for complex geometries but less efficient for thin-walled parts compared to metal spinning.
- Stamping:Stamping involves pressing a metal sheet into a die to create parts, which may be faster for high-volume production but lacks the design flexibility of metal spinning.
- Casting:Casting pours molten metal into a mold to produce parts, offering cost-effectiveness for large quantities but limited in geometric complexity compared to metal spinning.
6.3 Analysis of Factors Influencing Choice
The choice of metal forming technique depends on factors such as part geometry, material properties, production volume, and desired quality. CNC metal spinning is favored for applications requiring precise, thin-walled components with high aesthetic value, whereas other methods may be less suitable.
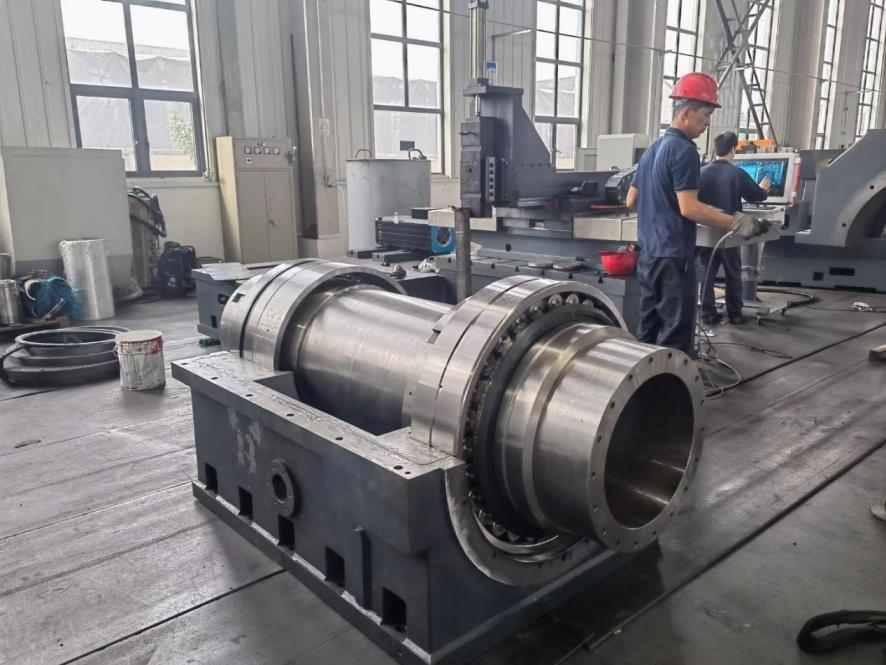
6.4 Advantages and Limitations
Advantages of CNC metal spinning include its ability to produce seamless, symmetrical parts with excellent surface finish and material utilization efficiency. However, limitations may arise in complex geometries and high-volume production, where alternative methods may offer better cost-effectiveness.
Advancements and Trends in CNC Metal Spinning Technology
7.1 Recent Technological Advancements
Recent advancements in CNC metal spinning technology focus on enhancing automation, improving software capabilities, and integrating advanced materials. Robotic arms and AI-powered algorithms are being utilized to further streamline the spinning process and expand the range of possible shapes and designs.
7.2 Emerging Trends
- Additive Manufacturing Integration:The integration of additive manufacturing techniques such as 3D printing with CNC metal spinning holds promise for creating hybrid structures with optimized properties.
- Industry 4.0 Connectivity: Connectivity features enable remote monitoring, predictive maintenance, and data-driven optimization of CNC metal spinning operations, contributing to increased efficiency and reduced downtime.
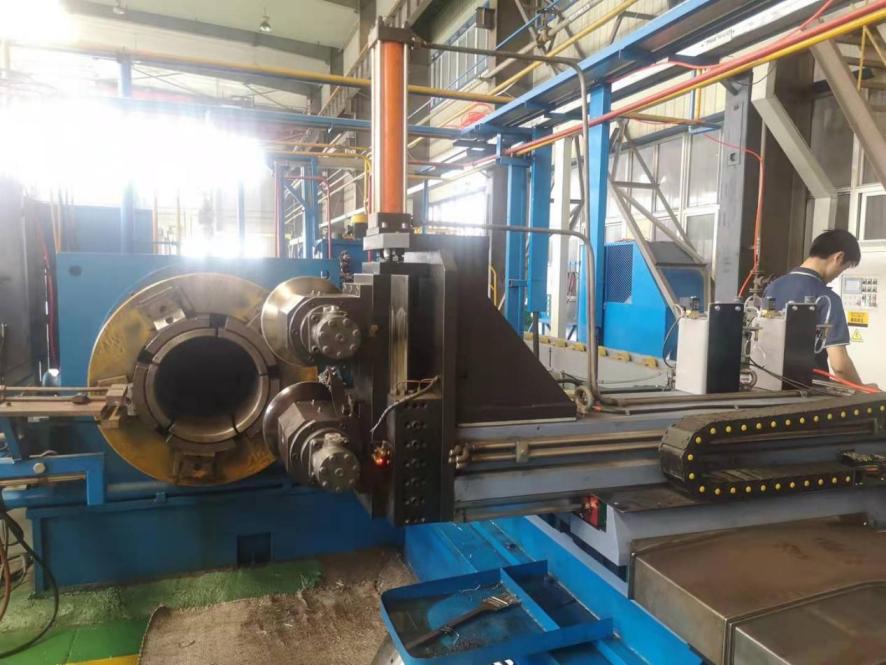
7.3 Innovative Applications
Innovative applications of CNC metal spinning technology include aerospace components, architectural features, and medical devices. The ability to produce lightweight, complex parts with superior mechanical properties and aesthetic appeal makes CNC metal spinning attractive across various industries.
7.4 Predictions for the Future
The future of CNC metal spinning technology is expected to witness further integration with advanced materials, increased automation, and improved sustainability practices. As manufacturers like ALTRON AUTO continue to push the boundaries of innovation, CNC metal spinning is poised to play a pivotal role in shaping the future of metal fabrication.
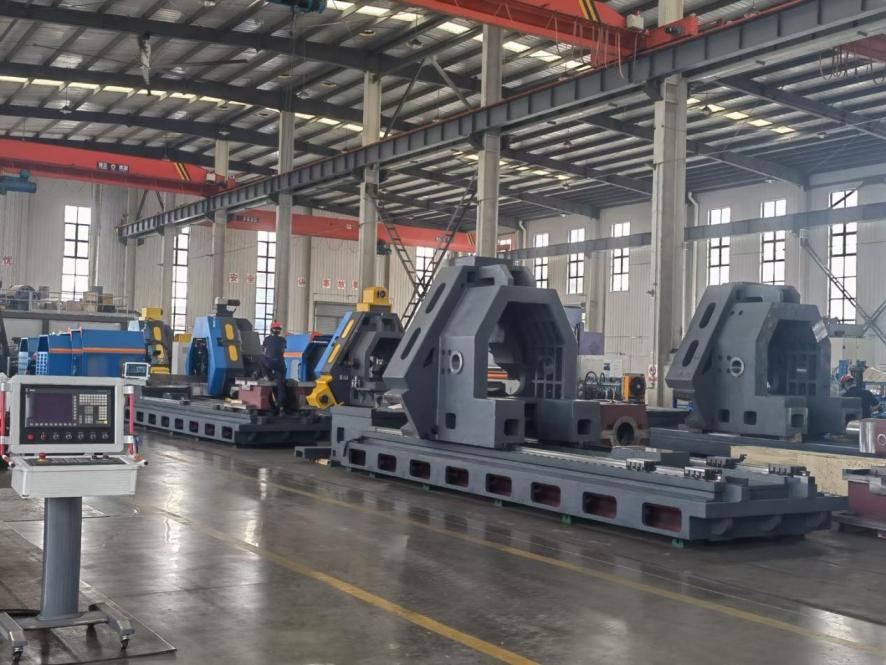
Conclusion
CNC metal spinning lathes have transformed the metalworking industry by offering unparalleled precision, efficiency, and versatility. With advancements in technology and materials, the potential applications of CNC metal spinning continue to expand, driving innovation across various industries. As manufacturers like ALTRON AUTO continue to push the boundaries of what is possible, the future of CNC metal spinning remains bright.