2024 Customization at Scale: CNC Metal Spinning Solutions For Centrifugal Fans
CNC metal spinning technology is revolutionizing centrifugal fan manufacturing, offering unprecedented levels of efficiency, customization, and sustainability. Companies like ALTRON are at the forefront of this transformation, leveraging cutting-edge technology to meet the evolving needs of customers and markets. As the industry continues to evolve, manufacturers must embrace innovation, address environmental considerations, and adapt to changing regulations to stay ahead of the curve.
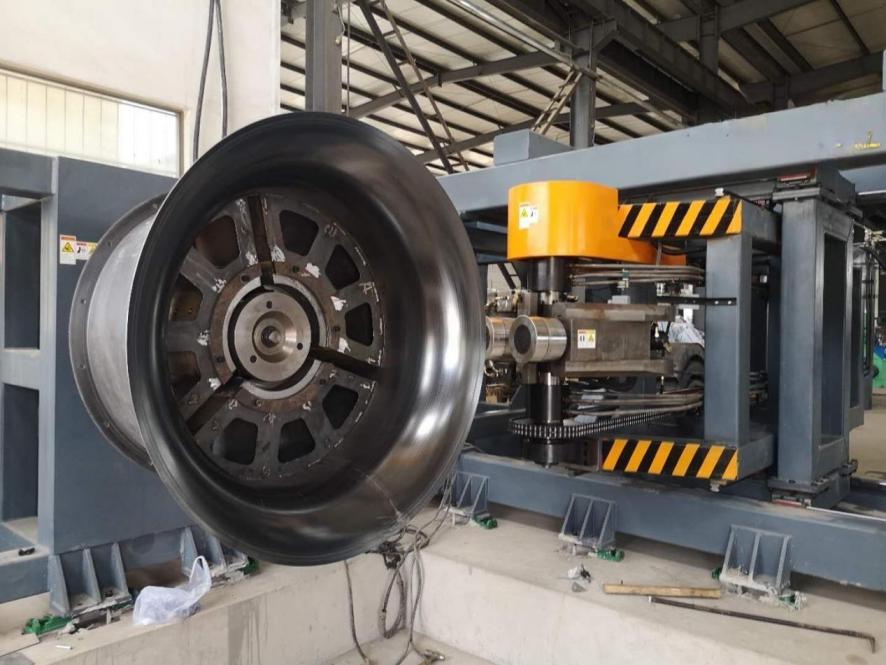
Understanding CNC Metal Spinning Technology for Centrifugal Fans
1.1 Introduction to CNC Metal Spinning
CNC metal spinning stands as a cutting-edge technology transforming the landscape of manufacturing, especially in the realm of centrifugal fan production. This advanced technique involves the use of computer numerical control (CNC) machines to shape metal blanks into precise, intricate shapes through high-speed rotation. The application of CNC metal spinning in centrifugal fan manufacturing has opened up new possibilities for efficiency, precision, and customization.
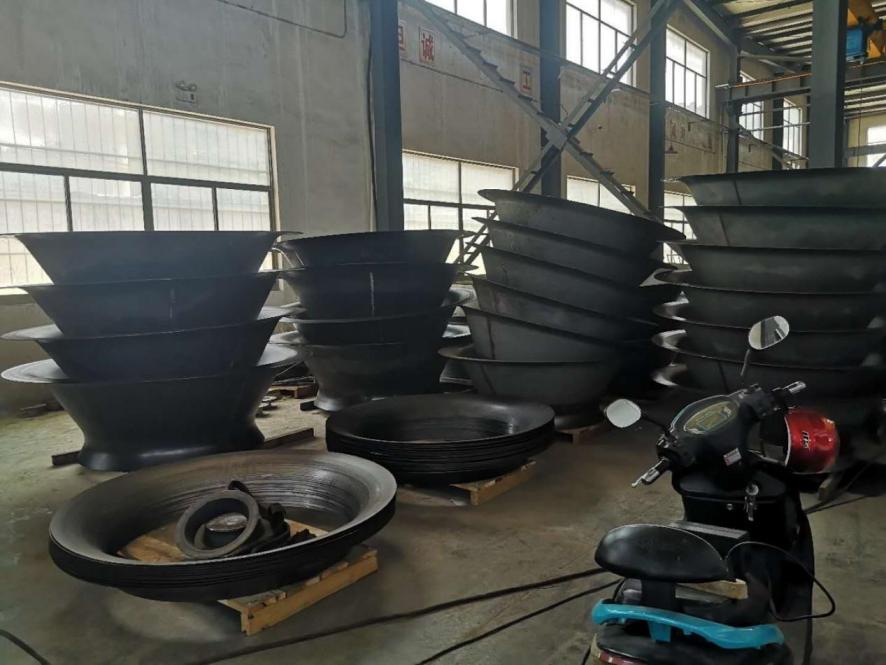
1.2 Technology Involved in CNC Metal Spinning
The process of CNC metal spinning begins with a metal blank being clamped onto a spinning mandrel. As the mandrel rotates, a CNC-controlled tool moves along the surface of the blank, gradually shaping it into the desired form. This process allows for the creation of complex shapes with minimal material waste and exceptional accuracy. The flexibility of CNC programming enables manufacturers to produce a wide range of centrifugal fan designs with ease.
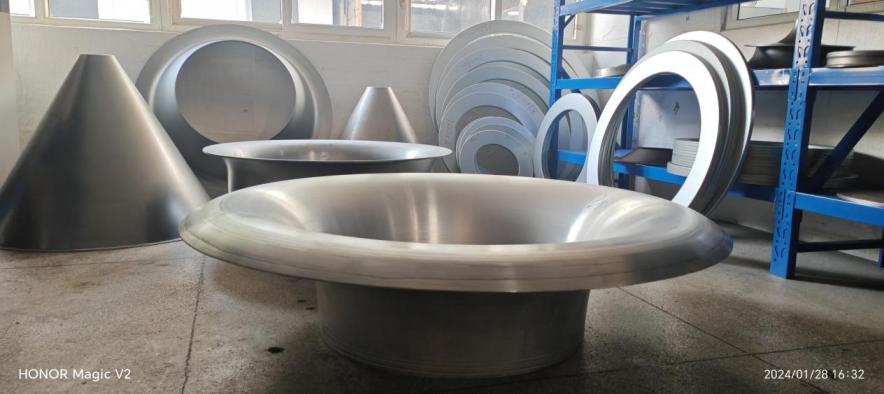
1.3 Advantages of CNC Metal Spinning
- Precision and Consistency:CNC metal spinning ensures precise replication of designs, resulting in consistent product quality and performance across production batches.
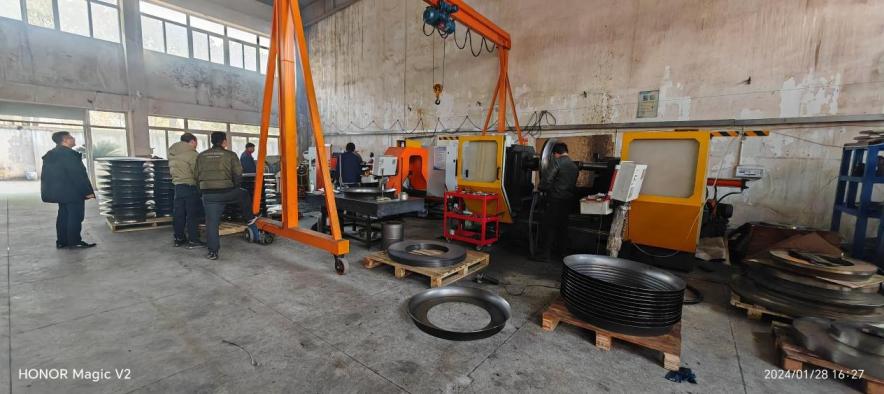
- Cost-Efficiency:By minimizing material waste and reducing setup times, CNC metal spinning offers cost savings compared to traditional manufacturing methods.
- Design Flexibility:Manufacturers can easily modify designs and produce custom components to meet specific customer requirements, enhancing product versatility and market competitiveness.
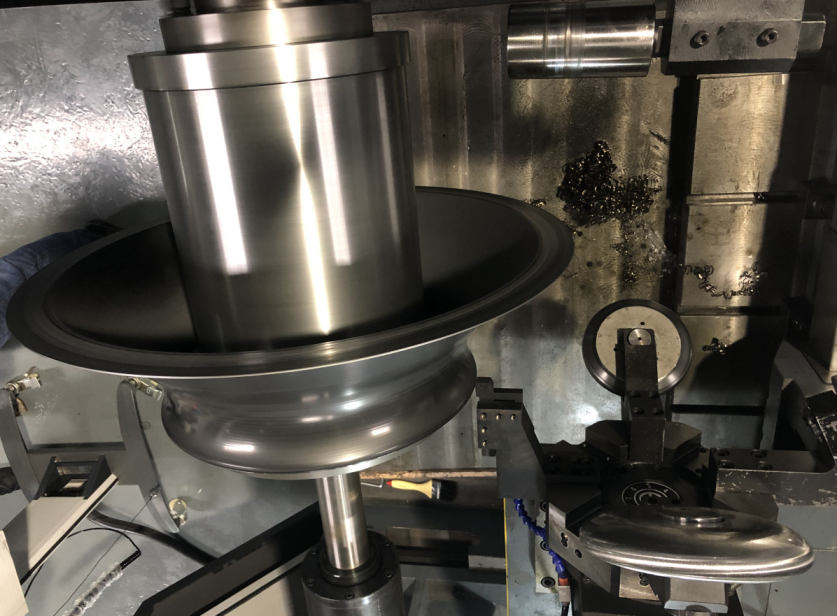
Market Analysis: Current Status and Growth Opportunities
2.1 Current Market Landscape
The market for CNC metal spinning in centrifugal fan manufacturing is experiencing steady growth, driven by increasing demand for high-performance ventilation systems across various industries. Established players like ALTRON are capitalizing on this trend by integrating CNC metal spinning into their production processes to meet market demand effectively.
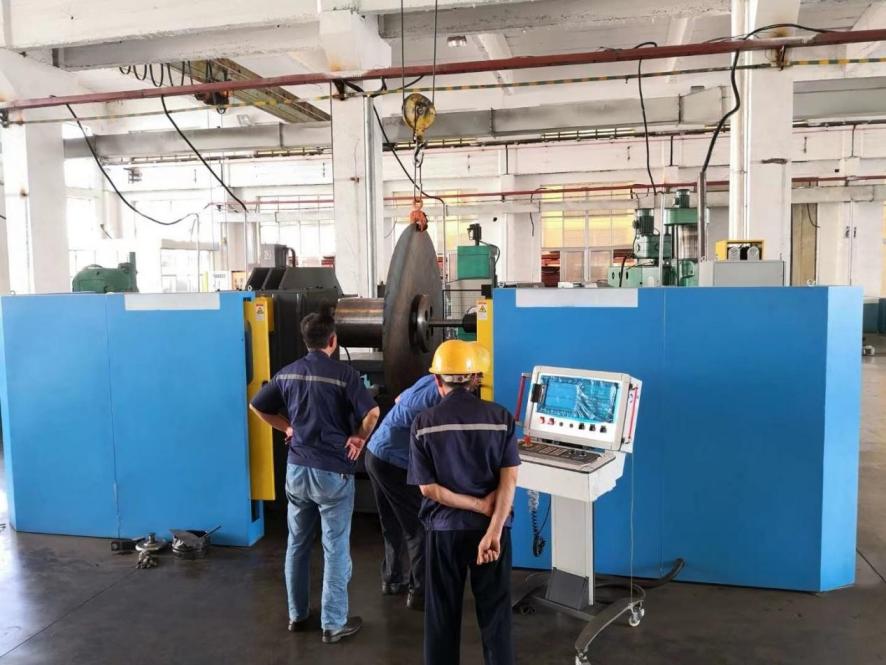
2.2 Trends and Growth Prospects
- Rising Adoption of Automation: Automation and robotics are becoming increasingly prevalent in CNC metal spinning facilities, enhancing productivity and reducing labor costs.
- Growing Demand for Lightweight Materials:The shift towards lightweight materials such as aluminum and stainless steel in centrifugal fan construction is fueling the demand for CNC metal spinning technology.
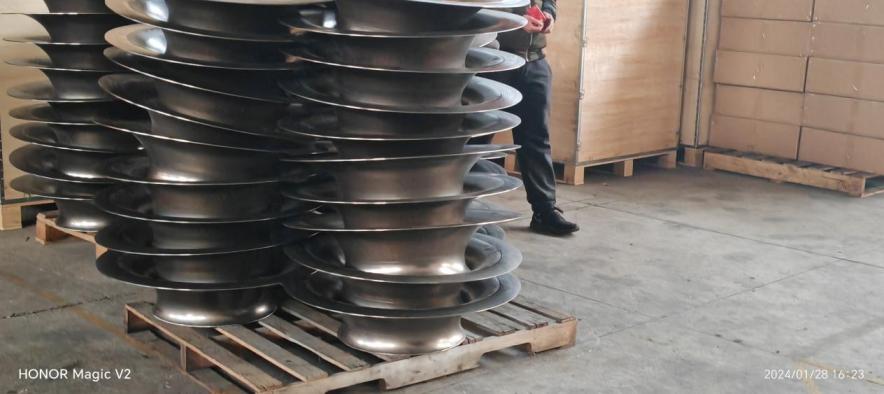
- Expansion into Emerging Markets:Manufacturers are exploring opportunities in emerging markets, leveraging CNC metal spinning to cater to the growing demand for centrifugal fans in sectors like automotive, aerospace, and HVAC.
2.3 Key Players and Regional Dynamics
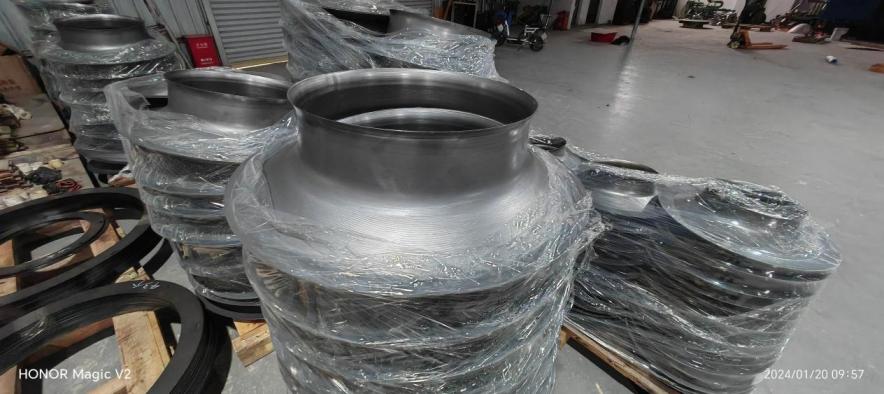
ALTRON stands out as a leading player in the CNC metal spinning market, offering a comprehensive range of solutions for centrifugal fan manufacturers worldwide. Regional dynamics play a crucial role in shaping market trends, with Asia-Pacific emerging as a key hub for CNC metal spinning due to its thriving manufacturing sector and technological advancements.
Identifying Needs and Challenges in CNC Metal Spinning
3.1 Specific Requirements of Manufacturers
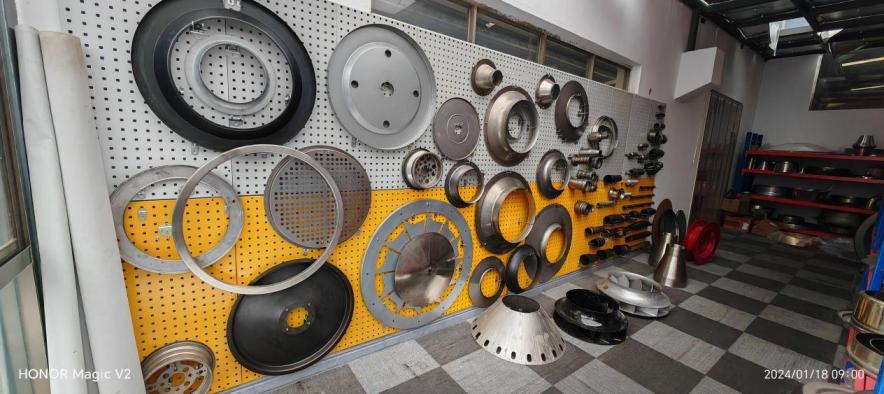
Centrifugal fan manufacturers require solutions that offer high precision, efficiency, and scalability to meet diverse customer demands. They seek advanced CNC metal spinning technology capable of handling a variety of materials and designs while ensuring cost-effective production.
3.2 Challenges in Adoption
- Material Selection: Choosing the right material for CNC metal spinning presents a challenge, as manufacturers must balance factors such as strength, durability, and cost to optimize product performance.
- Design Complexity: Complex geometries and intricate designs can pose challenges during CNC metal spinning, requiring innovative solutions and specialized tooling to achieve desired outcomes.
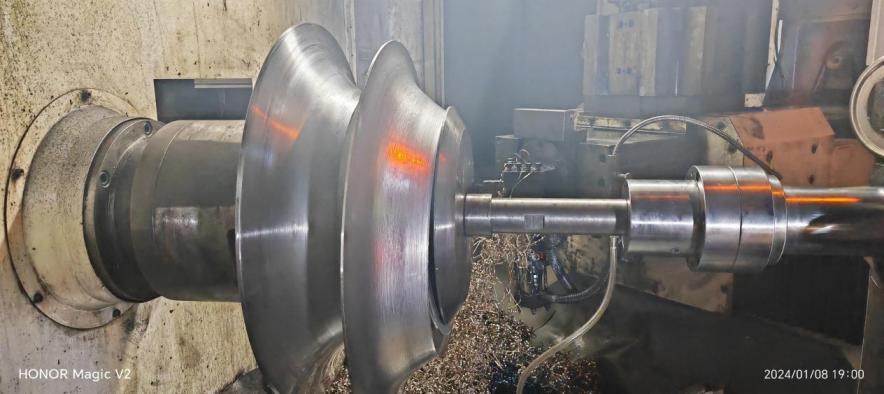
- Production Scalability:Maintaining consistent quality and throughput while scaling production volumes remains a significant challenge for manufacturers, necessitating efficient workflow management and resource allocation.
Solutions for Overcoming Challenges in CNC Metal Spinning
4.1 Addressing Material Selection
ALTRON offers comprehensive material testing and selection services, enabling manufacturers to identify the most suitable materials for their centrifugal fan applications. Advanced metallurgical analysis and simulation tools help optimize material properties for enhanced performance and cost-effectiveness.
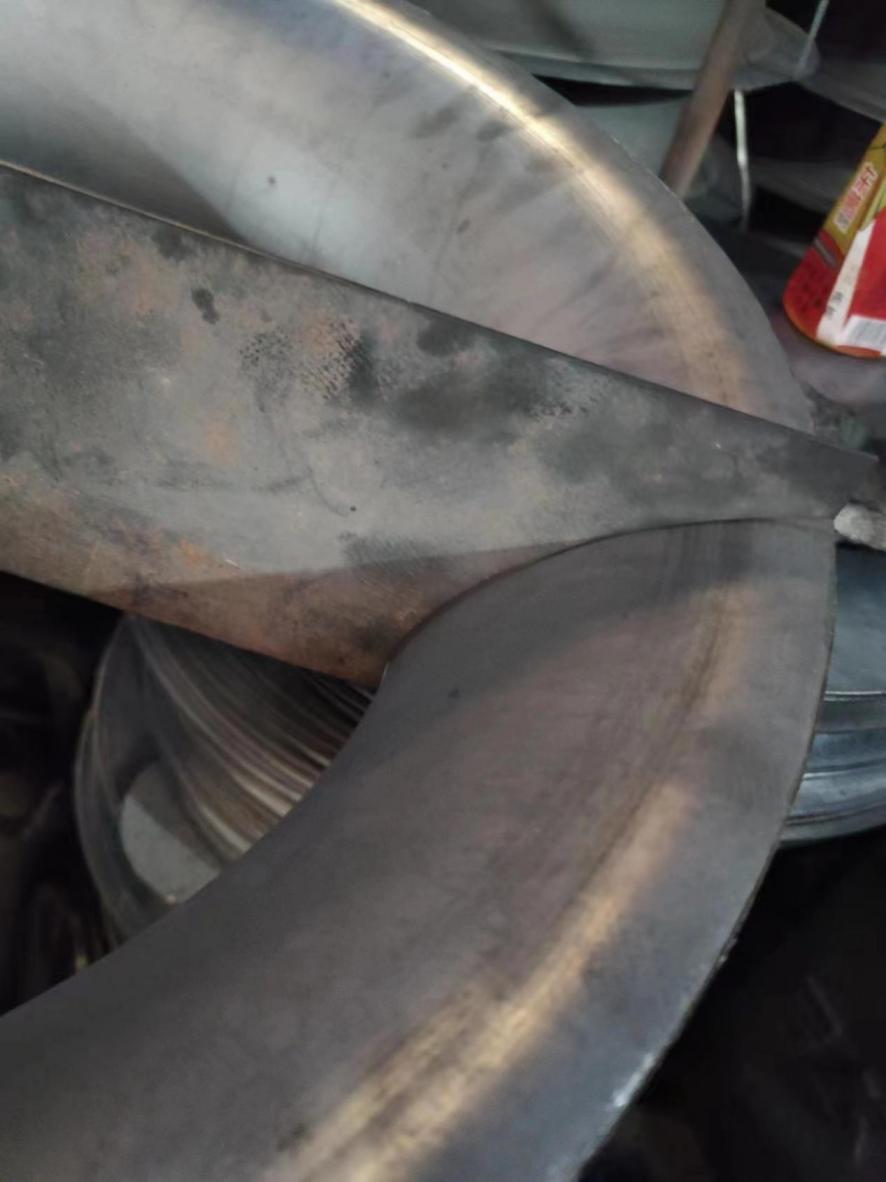
4.2 Managing Design Complexity
Through collaboration with ALTRON’s team of engineers and designers, manufacturers can leverage cutting-edge CAD/CAM software and simulation tools to streamline the design process and optimize part geometries for CNC metal spinning. Prototyping and iterative testing facilitate rapid iteration and validation of designs, ensuring successful outcomes.
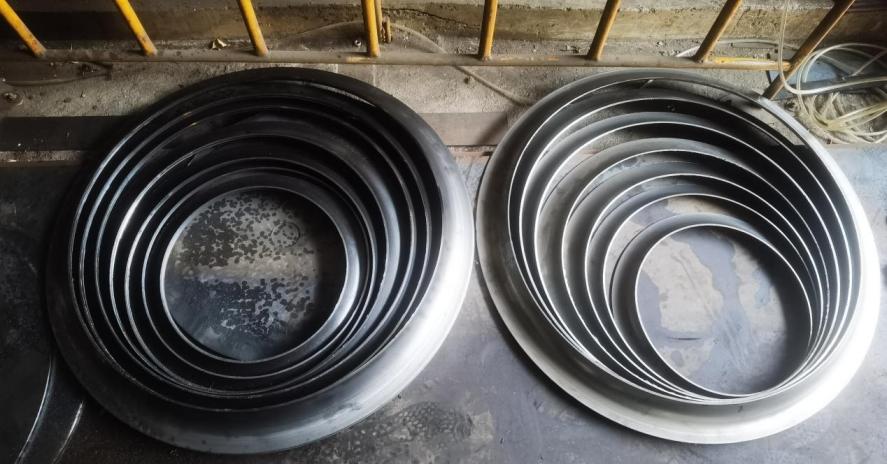
4.3 Enhancing Production Scalability
ALTRON’s integrated manufacturing solutions encompass automated production systems, real-time monitoring, and adaptive process control, enabling manufacturers to achieve high levels of productivity and scalability. Flexible production schedules and agile manufacturing processes allow for quick adaptation to changing market demands, ensuring competitiveness and profitability.
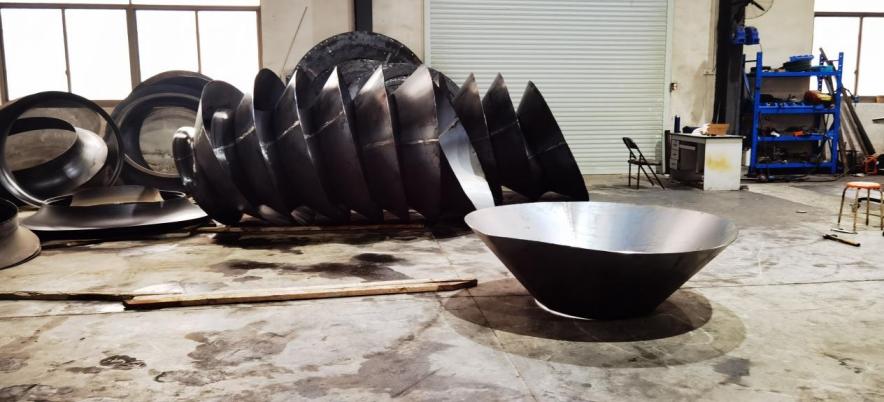
Trends Driving Innovation in CNC Metal Spinning for Centrifugal Fans
5.1 Emerging Trends and Advancements
The landscape of CNC metal spinning technology for centrifugal fan manufacturing is constantly evolving, driven by emerging trends and advancements. One significant trend is the increasing adoption of automation, which streamlines production processes, reduces labor costs, and enhances efficiency. Additionally, digitization plays a crucial role in enabling data-driven decision-making and process optimization. Furthermore, additive manufacturing techniques are gaining traction, allowing for the creation of complex geometries and lightweight components with reduced material waste.
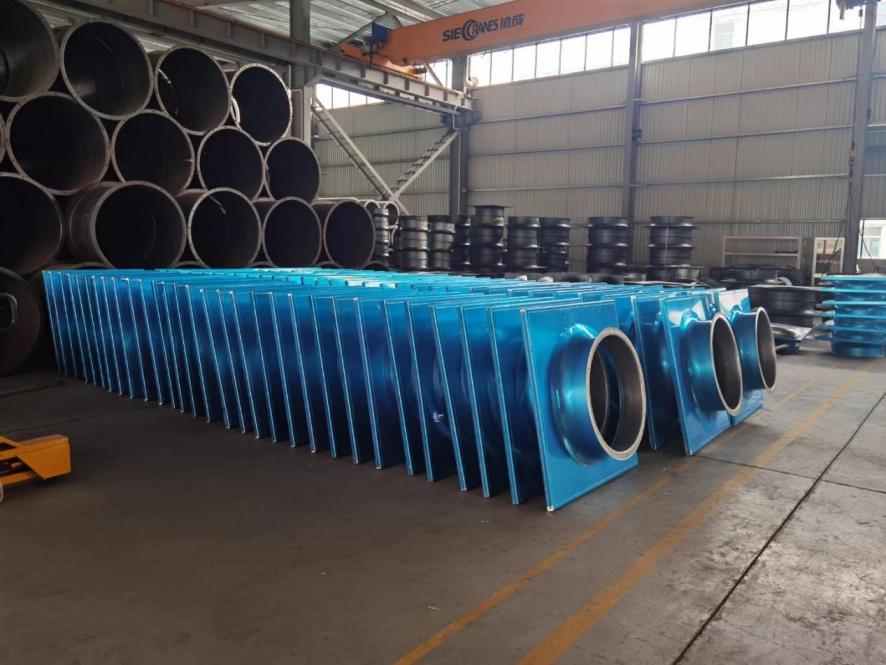
5.2 Impact on Efficiency, Customization, and Sustainability
These technological innovations have a profound impact on the efficiency, customization, and sustainability of centrifugal fan production. Automation minimizes manual intervention, leading to faster turnaround times and improved productivity. Digitization enables real-time monitoring and analysis of manufacturing processes, facilitating continuous improvement and customization based on customer requirements. Additive manufacturing techniques promote sustainability by reducing material consumption and energy usage, while also enabling the production of lightweight and eco-friendly components.
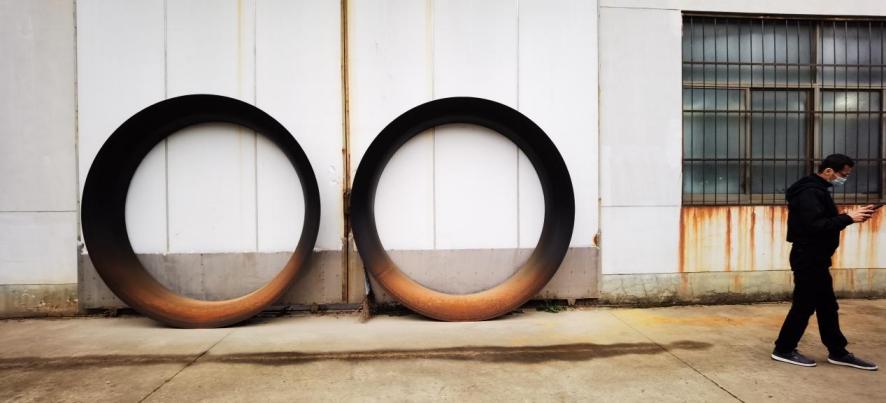
Adoption of CNC Metal Spinning in Centrifugal Fan Manufacturing: Case Studies
6.1 Successful Adoption Stories
Numerous companies have successfully transitioned to CNC metal spinning for centrifugal fan production, realizing significant benefits in terms of quality, efficiency, and cost-effectiveness. One such example is ALTRON, a leading manufacturer in the industry. By integrating CNC technology into their production processes, ALTRON has achieved higher precision, faster lead times, and increased design flexibility.
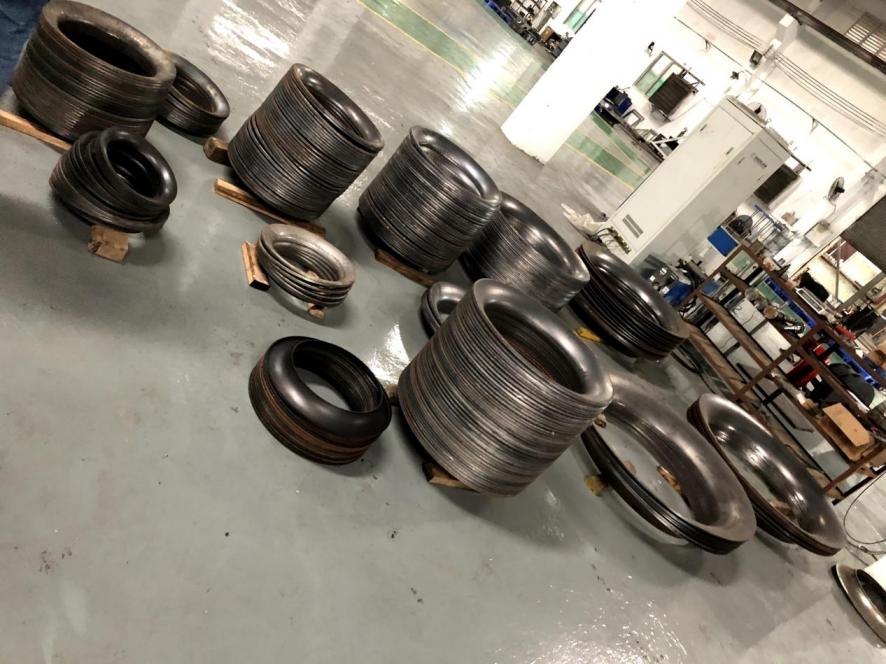
6.2 Challenges and Benefits
The adoption of CNC metal spinning technology is not without its challenges. Companies may encounter initial investment costs, as well as the need for training and retooling. However, the benefits far outweigh these challenges. CNC metal spinning offers greater accuracy and repeatability compared to traditional methods, resulting in improved product quality and consistency. Moreover, the ability to produce custom components enhances market competitiveness and customer satisfaction.
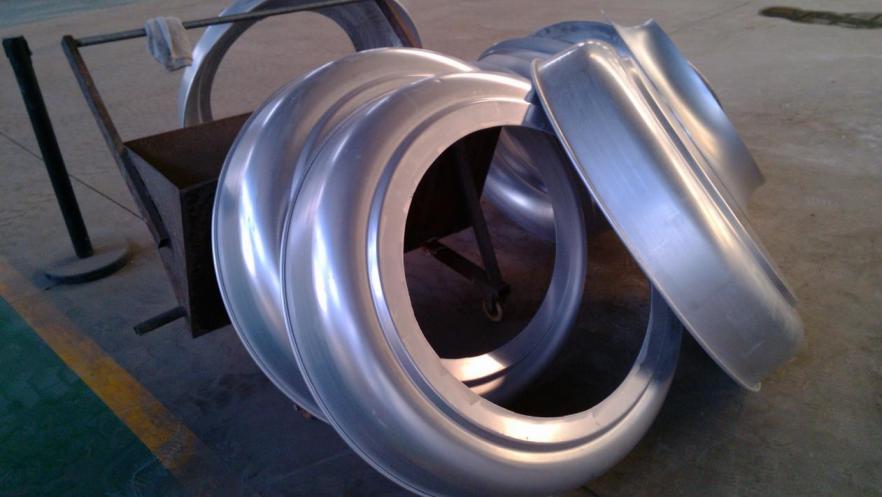
6.3 Factors Driving Adoption
Several factors drive companies to transition to CNC metal spinning technology. These include the demand for higher quality products, increased production efficiency, and the need for greater design flexibility. Additionally, advancements in CNC technology, such as improved programming software and faster machining speeds, make it an attractive option for manufacturers looking to stay ahead of the curve.
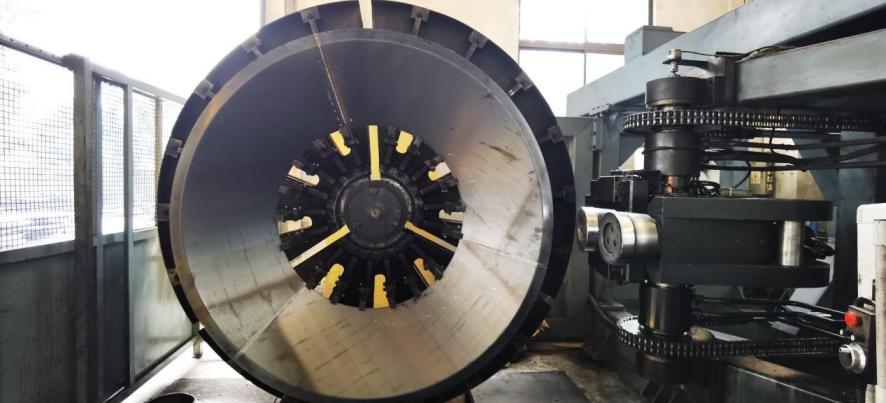
Addressing Environmental and Regulatory Considerations in CNC Metal Spinning
7.1 Environmental Sustainability
Environmental sustainability is a growing concern in centrifugal fan manufacturing. CNC metal spinning offers several eco-friendly practices, such as reducing material waste through precise shaping and optimizing energy usage through automation. Furthermore, the use of lightweight materials and additive manufacturing techniques contributes to overall sustainability by minimizing resource consumption.
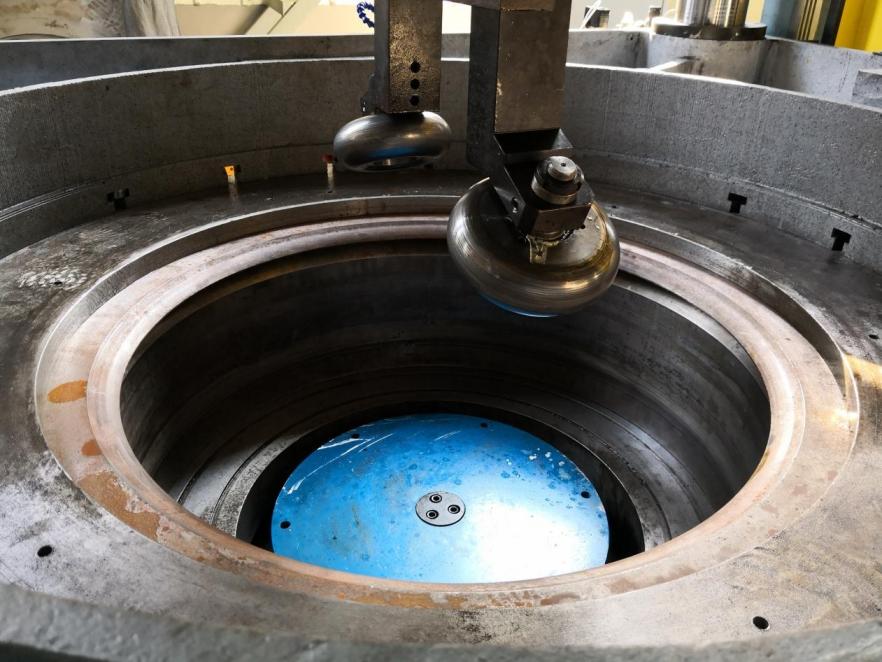
7.2 Regulatory Compliance
Regulatory compliance is another important consideration in CNC metal spinning for centrifugal fan production. Manufacturers must adhere to various standards and regulations governing material usage, emissions, and workplace safety. ALTRON ensures compliance with all relevant regulations, providing customers with peace of mind and confidence in their products.
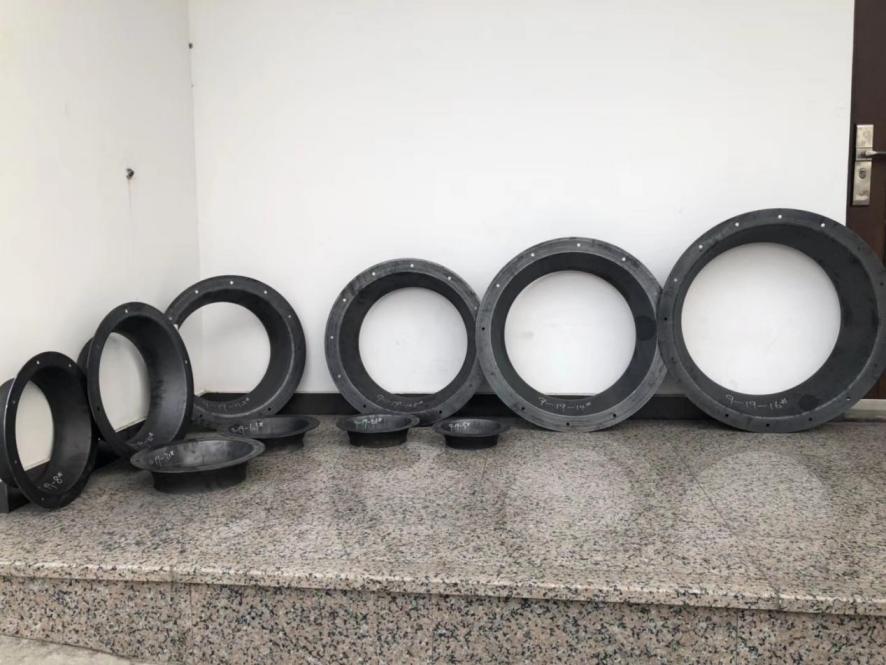
Future Outlook: Opportunities and Challenges in the Evolution of CNC Metal Spinning
8.1 Future Opportunities
The future of CNC metal spinning for centrifugal fan manufacturing holds immense potential for growth and innovation. Market trends indicate increasing demand for customized solutions, driven by advancements in technology and evolving customer preferences. Opportunities also abound in the development of sustainable practices and materials, as well as the integration of advanced analytics and artificial intelligence into manufacturing processes.
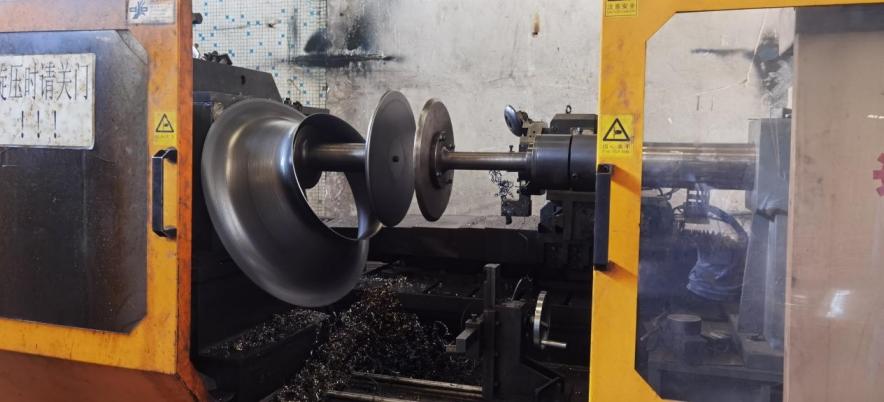
8.2 Challenges Ahead
Despite the promising outlook, manufacturers may face challenges in adapting to rapidly evolving technology and market dynamics. The pace of innovation requires companies to invest in continuous research and development to stay competitive. Additionally, regulatory requirements and environmental concerns pose ongoing challenges that must be addressed through collaboration and proactive measures.
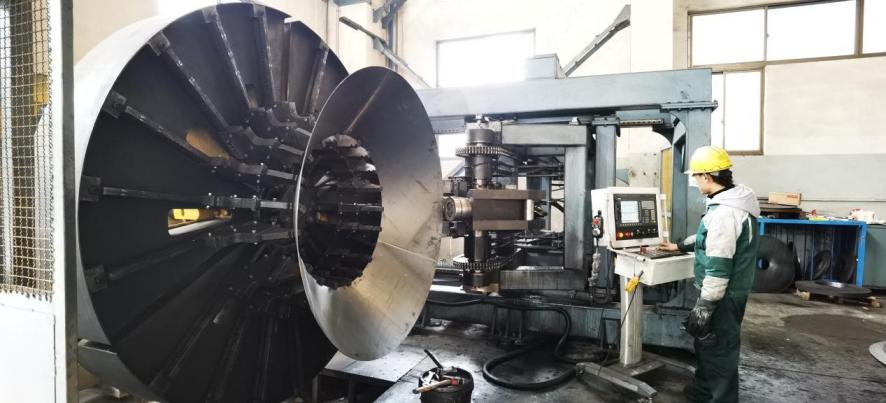
Why Choose ALTRON for CNC Metal Spinning Solutions for Centrifugal Fans
9.1 Unrivaled Expertise and Experience
ALTRON stands as a trusted leader in CNC metal spinning solutions for centrifugal fans, boasting decades of expertise and experience in the field. With a dedicated team of skilled engineers, designers, and technicians, ALTRON is committed to delivering innovative and high-quality solutions tailored to meet the unique needs of its clients. The company’s extensive knowledge base and proven track record make it the go-to choice for manufacturers seeking reliable and efficient CNC metal spinning services.
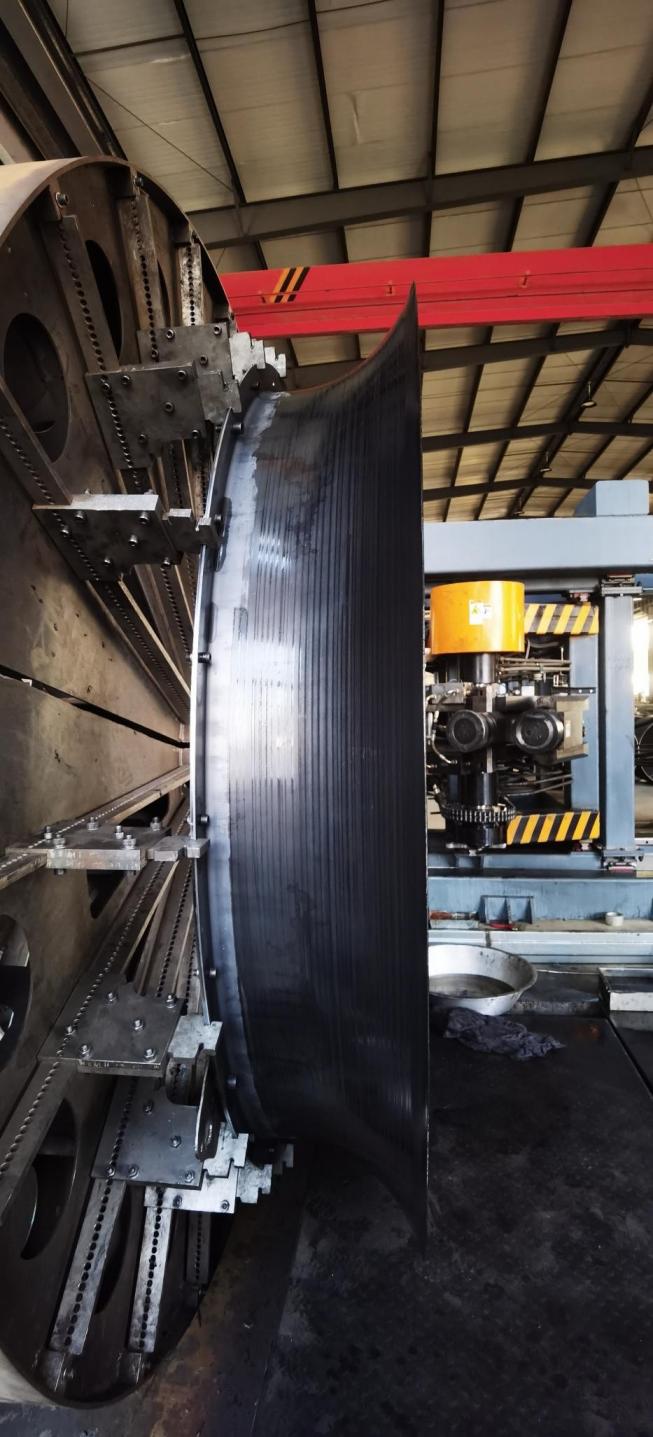
9.2 State-of-the-Art Technology and Facilities
At the heart of ALTRON’s success lies its state-of-the-art technology and world-class manufacturing facilities. Equipped with cutting-edge CNC machines, advanced software tools, and precision instrumentation, ALTRON ensures unparalleled accuracy, consistency, and efficiency in every aspect of the metal spinning process. From prototyping to production, the company leverages the latest technological advancements to deliver superior results that exceed customer expectations.
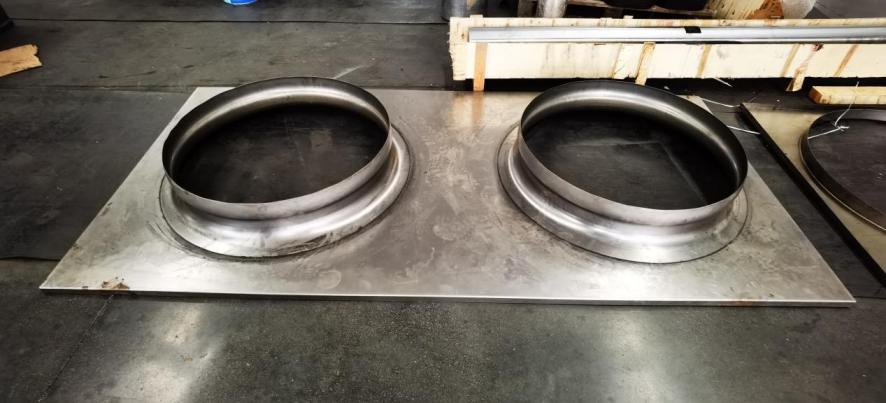
Conclusion
CNC metal spinning technology represents a game-changer in centrifugal fan manufacturing, offering unparalleled precision, efficiency, and flexibility. As the market continues to evolve, manufacturers must embrace innovative solutions and best practices to overcome challenges and seize growth opportunities. With ALTRON’s expertise and cutting-edge solutions, centrifugal fan manufacturers can stay ahead of the curve and deliver superior products to meet the demands of diverse industries.