Metal Spinning For Venturi -CNC Metal Forming Machine ACD-800
Metal Spinning For Venturi
Machine Name |
Double Wheel CNC Metal Spinning Machine |
Model |
AC-D800(diameter max Ф800;aluminum-Max 8mm; carbon steel-Max 4.0mm) |
Application Industry |
(Aerospace, Aviation Weapons, Medical, Furniture, Lighting, Building, Fire, Musical Instruments, Crafts, Automotive Parts, Pressure Vessel,Venturi ) |
Technical Service |
Complete the test in the early stage; provide online and offline training in the later stage, and complete the turnkey project. |
Technical Guidance |
Online 24 hours a day/ 7*24 Pre-sales technical service |
Project Progress |
30-120 days |
Relevant Files |
ALTRON_AUTO Catalog-Industrial Blower Machinery Turnkey Project |
- ADAVANTAGES
- PARAMETERS
- CUSTOMER TESTIMONIALS
Altron’s Double Roller CNC Metal Spinning machine is a machine with dual X-axis motors, which can realize multi-axis linkage metal spinning; the X-axis does not need to move the turret position when the synchronous metal spinning process is applicable, and synchronous metal spinning can be achieved by controlling the motor alone;
The machine uses a double 8-station turret, which can be equipped with 16 tools with different functions, or spinning rollers!
The AC-D800 can process a maximum wafer diameter of 1100mm (customized spinning roller tool), which is a very suitable machine for external processing and OEM metal spin forming; at the same time, it is free of charge to deliver special CNC spinning programming software, making production debugging and machine operation more intelligent!
CNC Spinning Machine AC-D800 Structure Introduction:
Spindle unit:
The spindle structure design of CNC metal spinning machine is suitable for the heavy load of metal spinning process. The spindle box frame is an integral casting.
The spindle is a hollow structure, made of 42CrMo, and the spindle installation runout accuracy is no more than 0.03mm. All spindle bearings are Japanese NSK.
The spindle is equipped with a 22KW AC motor; a rotary cylinder can be optionally used to clamp the pipe, which is used for pipe necking, waist shrinking and other spinning processes.
At the same time, the tail of the spindle is designed with a pneumatic unloading device, which can realize pneumatic demoulding for barreled products.
Frame:
The whole frame adopts casting structure, reasonably distributes mechanical properties, and is designed strictly in accordance with machine tool design standards, with reasonable rigidity, strength and seismic resistance.
Tailstock:
The tailstock is divided into two parts, upper and lower, and the base has a travel of 650mm, driven by dual hydraulic cylinders.
The upper part is integrally cast, equipped with a hydraulically controlled ejector rod, and the friction surface of the cylinder is hard chrome plated and then ground. The tailstock power hydraulic cylinder has a travel of 370mm and a Max of 20KN.
The tailstock has a coaxial fine-tuning function, which can adjust the downward droop of the tailstock caused by different top plate weights, especially for spinning products with small bottom end face diameters, which can improve the product surface quality and production stability.
Spinning work slide:
The slide is designed with a horizontally symmetrical layout and an overall casting structure. The materials are all QT50 castings, which are strong in rigidity. All components are cast in ductile iron and have strong vibration resistance.
The ball screw and linear slide rails are heavy-duty products to improve the rigidity and life of the equipment.
When spinning the sheet, the slide is designed with a material center material locator and pneumatic lifting.
Spinning tool turret:
The left and right slides are equipped with 8-station CNC tool holders, which can rotate and change tools on the vertical surface. Up to 16 different tools can be installed to avoid interference and collision between tools.
X, Z axis power motor:
The power adopts Siemens Germany’s original imported 1KF7 series servo motor and 611U drive system, which are stable and reliable. There are 3 sets of servo motors in total. The X-axis direction can run separately or synchronously. The two spinning wheels can be digitally positioned separately, which is convenient and fast. The Z-axis (longitudinal) is connected to the ball screw by the servo motor through a servo-specific reducer.
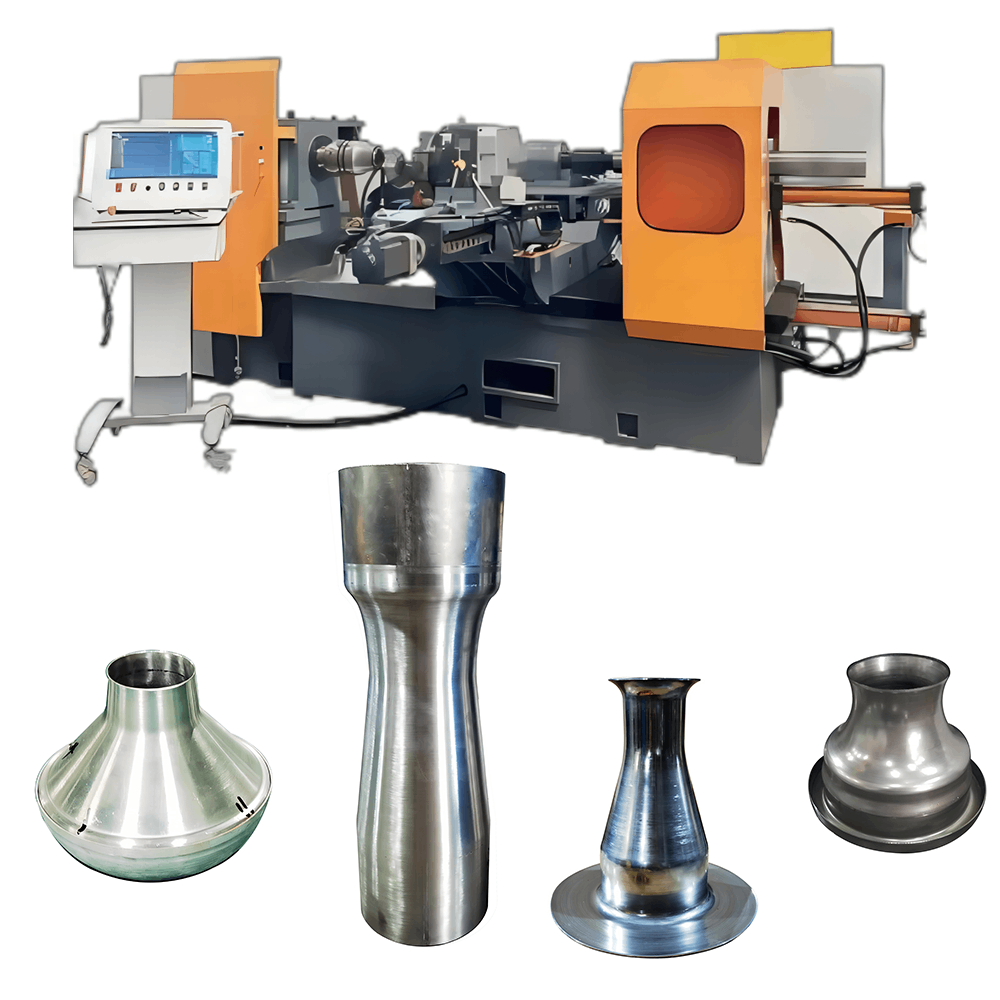
CNC Metal Spinning For Venturi Case
Venturi is a ventilation device used in special environments for special purposes; for example, in laboratories and medical operating rooms, when the internal space gas is isolated from the outside environment, Venturi will maintain and adjust the isolation environment of the space airflow in a rated negative pressure space.
Conventional Venturi: There are different materials: aluminum, iron, stainless steel; the size is more commonly used from 8-16 inches, and the AC-D800CNC metal spinning machine can fully cover this processing range.
Metal Spinning Venturi Mold

The internal contour of the Venturi requires high precision, and the mold surface needs to be inspected after the mold is manufactured. Laser scanning or high-precision turning and milling composite intermediate finishing can be used;
Mold material and processing technology: CR12 heat treatment/#45 steel surface tempering
Clamp design: Reasonable application of hydraulic rotary cylinder, different ways of tightening/clamping;
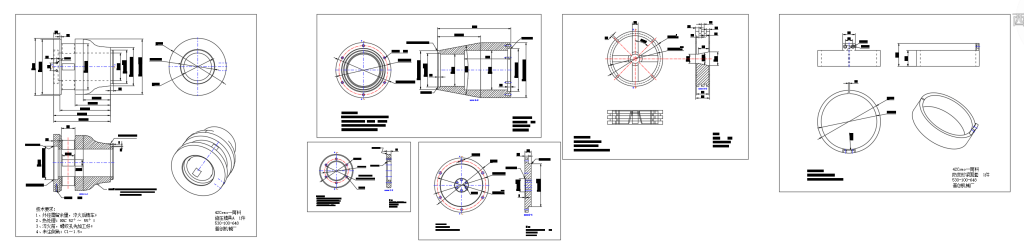
- Stainless steel material has high hardness and can be used for tightening structure, which is not easy to damage the surface of the pipe
- Aluminum material has low hardness and needs to be used for clamping structure. The contact part between aluminum and the clamp must be made of nylon material or soft silicone material to protect the surface from damage
CNC metal Venturi spinning process:

- Adjust the hydraulic pressure of the clamp, and adjust the value during the test to ensure that the tube is not clamped and deformed, so that the tube can be ensured not to loosen.
- The metal spinning roller should first use a tool with a larger R to reduce the thinning of the material, which may cause the tube to break, or the weld to crack! Improve the surface spinning texture quality.
- The path trajectory of the spinning should be regular so that the flow direction of the material can be stable, especially for the stainless steel Venturi tube. The necking amount of each spinning is about 1.5-2mm each time. Too much will cause the material to become thinner, and too fast a spinning speed will cause the surface to wrinkle.
CNC Metal Spinning Mass Production Of Venturi

- Pipe production:
- Order metal sheets (according to the length of the pipe + 25mm * pipe diameter * 3.14) to calculate and reserve the size of the square plate;
Pipe rolling: - Two-roller rolling machines are generally used to produce cylinders, and the overall ovality will be relative to the 4-roller rolling machine;
- Seam welding machine:
Stainless steel uses argon arc welding technology to ensure the penetration depth and tension of welding;
Aluminum can be used with water-cooled welding machines, and the welding temperature cannot be too high! Especially the welding gun part!
Ensure the flatness of the weld.
Small diameter pipes can be used for high-power laser welding, and the efficiency can be effectively improved!
Flush trimming:
The end faces of the pipes are flush to ensure the deviations in rolling and welding! Cause the tightening to send. - Pipe blank inspection:
Pipe blanks need to be inspected in batches. Pipes with defects in the welding process should be manually welded inside and outside; spinning alone cannot be mixed with qualified pipes produced in batches;
Metal Spinning For Venturi Video
If you plan to produce Venturi or encounter unsolvable technical problems when spinning stainless steel, please contact me and Joby engineers will give you a detailed plan.
Altron’s Factory Video
Configuration
Standard Configuration
- SIEMENS CNC 828D
- SIEMENS Servo Motor & Drive
- Asynchronous Servo Spindle Motor
- Two Turrets Tool Setting Simultaneously
- APEX Servo Reducer
- High Strength Ductile Iron Sliding Table
- Blanks Center Assembly
- Back Roller Assembly
- CNC Tool Turret
- Hydraulic Station & Air Cooling System
- Air Unload Assembly
- Self-developed Spinning System
- Control System Remote Maintenance
Select Configuration
- Spindle Spinning Cylinder
- Trimming Tool Assembly
- Air Conditioner for Hydraulic Station
- Hot Spinning Parts Under 700℃
- Teach In & Play Back System
Model No. |
Max. Material Dia. (mm) |
Radial Stroke (mm) |
Axial Stroke (mm) |
Roller Thrust (KN) |
Tailstock Force (KN) |
Spindle Power (KN) |
Spindle Speed (RPM) |
Material Thickness AL./carbon steel/SUS (mm) |
ACD-600 | 600 | 260 | 1100 | 40 | 20 | 18.5 | 50-1000 | 6 / 4 / 3 |
ACD-800 | 1300 | 400 | 1600 | 60 | 50 | 30 | 50-800 | 8 / 5 / 4 |
ACD-1200 | 1650 | 500 | 800 | 80 | 50 | 37 | 30-500 | 10 / 6 / 4.5 |
ACD-1600 | 1800 | 600 | 1000 | 120 | 70 | 45 | 30-450 | 14 / 8 / 5.5 |
ACD-2000 | 2000 | 750 | 1250 | 140 | 100 | 75 | 30-400 | 14 / 10 / 7 |
ACD-2500 | 2500 | 850 | 2050 | 200 | 140 | 132 | 10-300 | 30 / 20 / 15 |
ACD-3500 | 3500 | 950 | 2550 | 300 | 140 / 200 | 200 | 10-300 | 40 / 25 / 20 |
Machine Configuration Parameters
Technical index
HIWIN ball screw
-
Marcley
★★★★★Post a review on Aug 21, 2022 From Bolivia
The Double Wheel CNC Spinning Machine has revolutionized our spinning operations. The accuracy and surface quality it delivers are truly outstanding. We can handle large blanks up to 2500mm in diameter with ease, and the results are always precise.
-
Arthur Zonneveld
★★★★★Post a review on Fec 21, 2022 From Mauritius
The machine’s shock protection system ensures smooth and stable operation, even during demanding tasks. It has greatly enhanced our productivity and allowed us to expand our capabilities. We highly recommend the double wheel spinning machine.
-
Nicolas Vazquez
★★★★★Post a review on jul 21, 2022 From Uruguay
We are extremely satisfied with the performance of the Double Wheel CNC Spinning Machine. It has exceeded our expectations in terms of accuracy and surface finish. The symmetrical distribution of spinning force and pressure to the spindle provides excellent shock protection, ensuring consistent and reliable spinning results.
-
OSCAR URBANEJA
★★★★★Post a review on Oct 10, 2022 From Venezuela
The machine’s versatility allows us to work with long and thin goods as well as cone-shaped products, expanding our product range. The combination of the SIEMENS control system and the user-friendly programming software makes operation seamless. It has been a game-changer for our spinning operations