PLC Flanging and Hole Punching Machine
PLC Flanging and Punchine Machine for Axial Fans
Machine Name |
PLC Flanging Machine for Axial Fans & Hole Punching |
Model |
AC-FJFB 1600 |
Application Industry |
Axial Fan, Subway Fan, Tunnel Fan, Jet Fan |
Technical Service |
Complete the test in the early stage; provide online and offline training in the later stage, and complete the turnkey project. |
Technical Guidance |
Online 24 hours a day / Conference To Solve Pre-Sales Problems. |
Project Progress |
30-120 days |
Relevant Files |
ALTRON_AUTO Catalog-Industrial Blower Machinery Turnkey Project |
Industrial Fans A-Z Project:
1 CNC Rolling machine 2 Seam Welding machine 3 Axial Flow Fans Forming Production Line, 4 CNC Flanging Machines, 5 CNC Spinning Machine,6 AI Automatic Welding,
- ADAVANTAGES
- PARAMETERS
- CUSTOMER TESTIMONIALS
The PLC Flanging and Punching Machine is a versatile device designed to simplify the flanging and punching process in various industries. The machine combines multiple functions to perform flanging, curling, folding, hemming, and punching of axial fans; the stations can be customized according to the actual needs of the customer, and up to 4 functions can be selected for one machine!
Flanging and Punchine Machine Applications:
- HVAC (Heating, Ventilation, and Air Conditioning): The machine is commonly employed in the HVAC industry for flanging and hole-punching tasks in the manufacturing of ducts, fittings, and other HVAC system components.
- Industrial axial fan air cylinder, air duct, and other pipes that need to be flanging on the cylindrical reel.
- Hardware machinery, such as vibrating screen machinery, the flange cylinder of this machinery also needs to be processed by a flanging machine!
PLC Flanging and Punchine Machine Video
Features of PLC Flanging Machine:
Altron’s Flanging and Punching Machine has a sturdy mechanical design. It uses large-sized and thick plates to make the base of the machine. Reasonable mechanical analysis and calculation make the machine very stable during the forming process!
-
Easy to Use with Parameterized Settings and Touch Screen Input: The machine features a user-friendly interface with parameterized settings that simplify operation. The touch screen input allows for easy navigation and adjustment of settings, making it convenient for operators to control the machine.
-
Fully Automated Flanging and Punching: Once the settings are established, the machine operates in a fully automated manner, eliminating the need for constant personal intervention. This automation streamlines the flanging and punching processes, enhancing efficiency and productivity.At the same time, laser tracking can be configured to automatically find the weld, take the weld as the starting point, and index the hole distance!
PLC flange flanging operation process
- Select the corresponding inner support mold according to the product specifications and install it on the flanging machine.
- Adjust the position and height of the lifting and positioning device and the position of the curling component according to the diameter of the workpiece and the width of the flanging.
- Select the corresponding program formula according to the product specifications.
- Place the workpiece on the mold and lift the main shaft to clamp it.
- Press the start button.
- The main shaft rotates and the flanging component starts flanging.
- After the flanging is completed, the punching component starts punching; (use laser positioning according to needs)
- After the punching is completed, the curling forming component starts curling.
- At this point, the single-piece work is completed, and the workpiece is manually replaced for the next cycle.
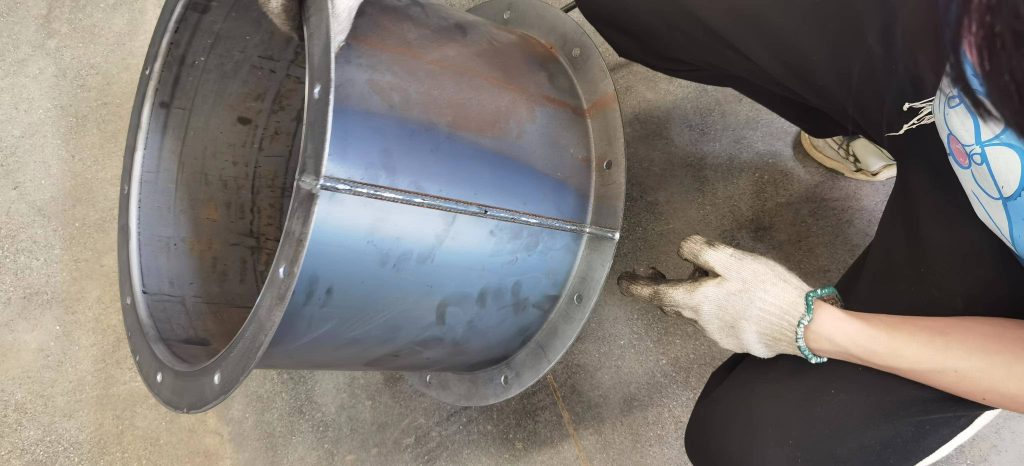
The structure of PLC flanging machine
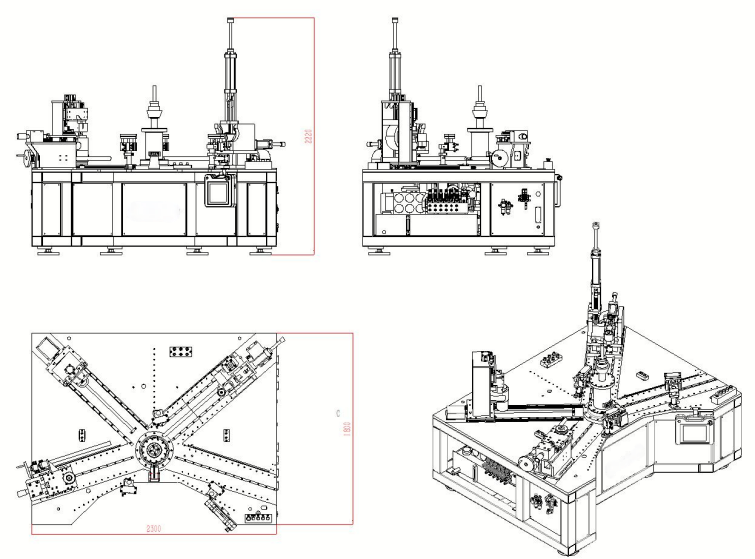
What does the PLC flange flanging machine bring to the factory:
-
CNC Drive for High Efficiency and Energy Savings: With CNC drive technology, the machine offers high efficiency and energy savings. It consumes less power (60% less compared to traditional machines) while delivering excellent flanging results in terms of safety and reliability.
-
Permanent Lubrication Technology: The machine utilizes permanent lubrication technology, eliminating the need for frequent lubrication during the bearing’s lifespan. This feature reduces maintenance requirements and ensures smooth and uninterrupted operation.
-
Adjustable Clamping Pressure: The machine allows for adjustable clamping pressure, preventing slippage during operation. This feature contributes to higher productivity, achieving 50%-80% higher productivity compared to older flanging machines.
Configuration
Mainly used for industrial fan edge flanging and hole punching,Application scenarios of products processed by PLC flanging machine
Material Thickness |
carbon steel 1~5mm stainless steel 3mm |
Workpiece Dia. | Φ400~Φ1600mm |
Outer Flange Edge Width | 30~50mm |
Machine Size | 3675×2450×2400mm (L×W×H) |
Total Power | 14KW |
-
Marcley
★★★★★Post a review on Aug 21, 2022 From Bolivia
I recently received the welding equipment and I must say that I am extremely satisfied with my experience so far. The training video provided was comprehensive and helped me understand the setup and operation of the machine. The after-sales service has been exceptional, with patient and helpful support staff guiding me through any questions or concerns I had.
-
Arthur Zonneveld
★★★★★Post a review on Fec 21, 2022 From Mauritius
I was pleasantly surprised by how simple the equipment was to operate. With the clear instructions and intuitive interface, I was able to get the machine up and running quickly. The user-friendly design made it easy for me to grasp the controls and make adjustments as needed.
-
Nicolas Vazquez
★★★★★Post a review on jul 21, 2022 From Uruguay
The efficiency of the equipment has exceeded my expectations. It has significantly reduced labor costs and improved productivity in our welding processes. The quality of the welds produced by the machine is excellent, and I no longer have to worry about inconsistencies or uncertainties that were common with manual work. This has increased the acceptance of our products among our customers.
-
OSCAR URBANEJA
★★★★★Post a review on Oct 10, 2022 From Venezuela
I am extremely pleased with the performance of the equipment and the support provided by the company. I highly recommend this welding system to others in need of efficient and reliable welding solutions.