Mastering Precision: 2024 Forming and Welding Solutions for Industrial Fan
ALTRON’s advanced forming and welding solutions are revolutionizing the industrial fan manufacturing industry, offering unparalleled precision, efficiency, and quality. Through continuous innovation and a steadfast commitment to quality and compliance, ALTRON empowers manufacturers to achieve excellence in forming and welding processes, driving the next generation of industrial fan production.
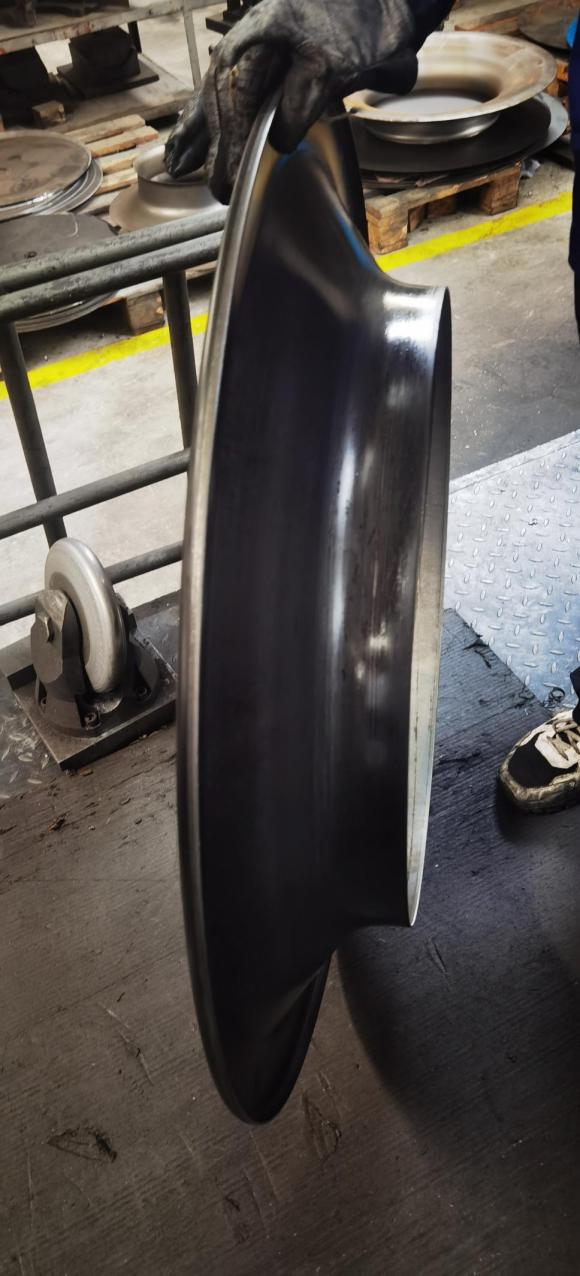
Introduction
1.1 Introduction to Industrial Fans
Industrial fans are indispensable components across various industries, serving critical roles in numerous applications. These powerful machines are integral for maintaining proper ventilation, controlling temperatures, and ensuring efficient operations in diverse settings.
1.2 Importance of Industrial Fans in Various Applications
Industrial fans are essential in a multitude of sectors, including manufacturing, agriculture, construction, and commercial buildings. They play crucial roles in air circulation, dust and fume control, process cooling, and maintaining comfortable indoor environments.
1.3 Different Types of Industrial Fans and Their Functionalities
- Centrifugal Fans:These fans utilize centrifugal force to move air perpendicular to the fan blades’ rotation axis. They’re commonly used in ventilation systems and air conditioning units due to their ability to handle high-pressure environments effectively.
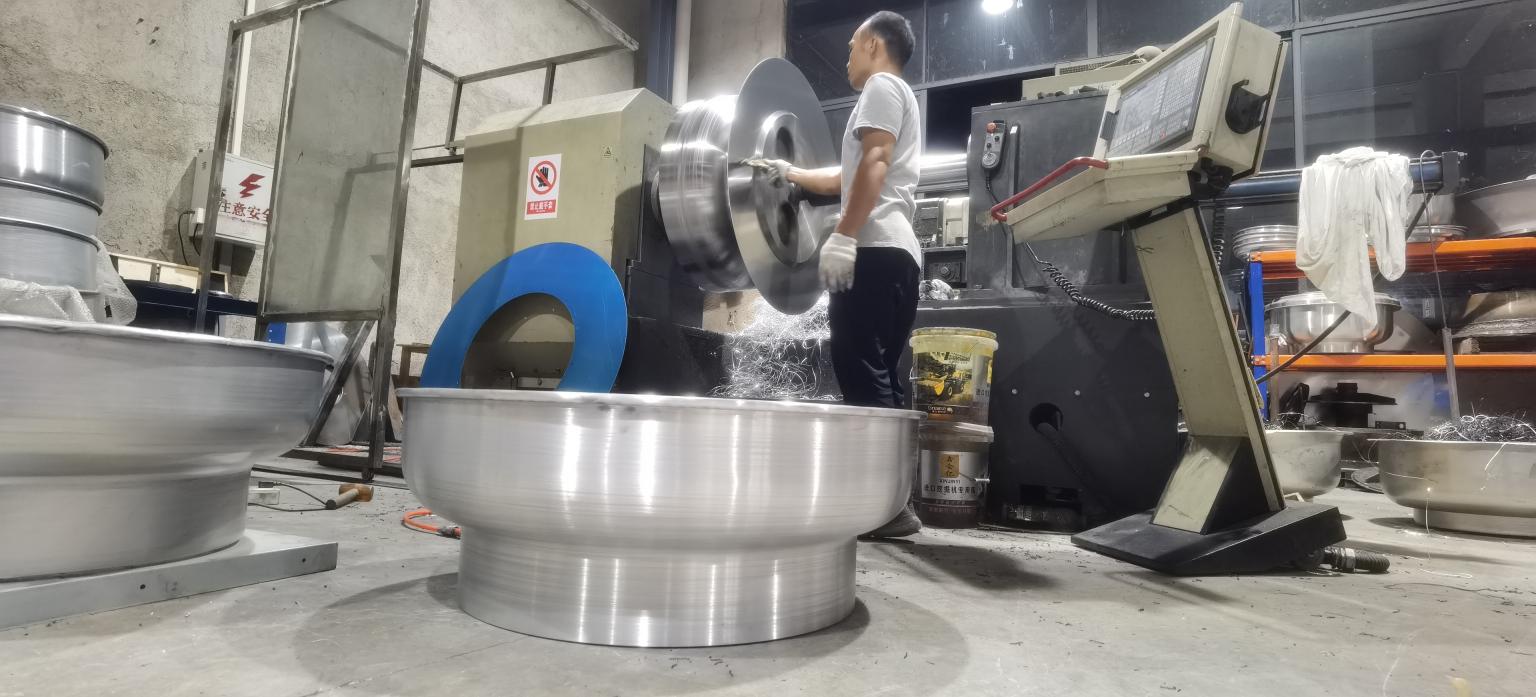
2.Axial Fans:Axial fans move air parallel to the fan blade’s rotation axis. They are ideal for applications requiring high airflow rates at low pressures, such as cooling electronic equipment and drying processes.
3.Flow Fans:Combining features of both centrifugal and axial fans, mixed flow fans offer a balance between airflow and pressure. They are suitable for various applications, including HVAC systems and industrial ventilation.
1.4 Importance of Efficient Design and Manufacturing Processes for Industrial Fans
Efficient design and manufacturing processes are vital for producing high-quality industrial fans that meet performance requirements while minimizing costs and lead times. ALTRON, a leading supplier of forming and welding solutions, recognizes the significance of optimized manufacturing processes in achieving superior fan performance.
Basic Principles of Forming for Industrial Fans
2.1 Explanation of Forming Processes
- Stamping:Stamping involves pressing a metal sheet between two dies to form it into the desired shape. This process is commonly used for manufacturing fan blades and housing components.
- Rolling:Rolling involves passing a metal sheet through a pair of rollers to reduce its thickness or shape it into cylindrical or curved forms. It is particularly useful for forming fan housings and impellers.
- Bending:Bending utilizes pressure to deform metal sheets into specific angles or curves. It is commonly employed in forming fan blades and other components with curved geometries.
2.2 Advantages and Limitations of Each Forming Process
- Stamping:Offers high precision and repeatability but may be limited in forming complex geometries.
- Rolling:Efficient for producing cylindrical or curved components but may require additional machining for complex shapes.
- Bending: Versatile and cost-effective for forming various geometries but may result in material deformation or springback.
2.3 Considerations for Material Selection and Thickness in Forming
The choice of materials and their thicknesses significantly impact the forming process and the performance of industrial fans. Factors to consider include material properties, such as strength and ductility, as well as corrosion resistance and weight requirements.
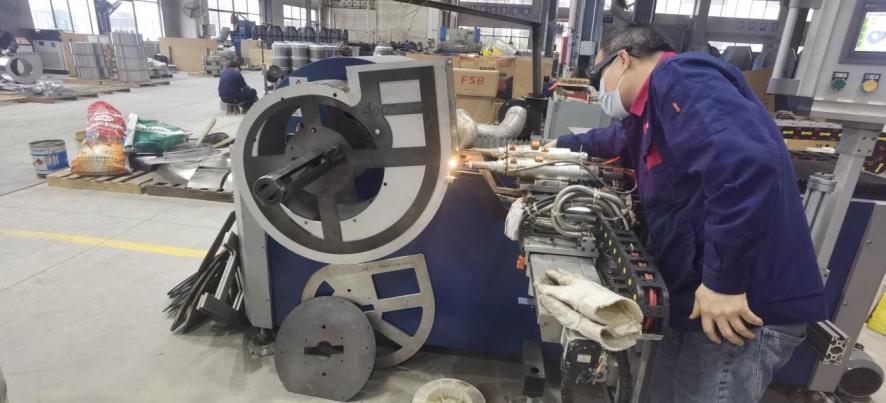
Welding Techniques for Industrial Fan Components
3.1 Introduction to Various Welding Techniques
Welding is crucial for assembling industrial fan components, ensuring structural integrity and longevity. ALTRON provides advanced welding solutions suitable for various fan manufacturing needs.
3.2 Comparison of Welding Techniques
- MIG (Metal Inert Gas) Welding:Offers high welding speeds and productivity, suitable for a wide range of materials and thicknesses.
- TIG (Tungsten Inert Gas) Welding:Provides precise control over the welding process, ideal for welding thin materials with superior quality.
- Resistance Welding:Fast, efficient, and suitable for high-volume production, making it ideal for welding thin materials in industrial fan manufacturing.
Importance of Weld Quality and Inspection
Ensuring the quality of welds is essential for maintaining the structural integrity and reliability of industrial fan components. ALTRON emphasizes the importance of rigorous weld quality control measures, including non-destructive testing (NDT) and visual inspection.
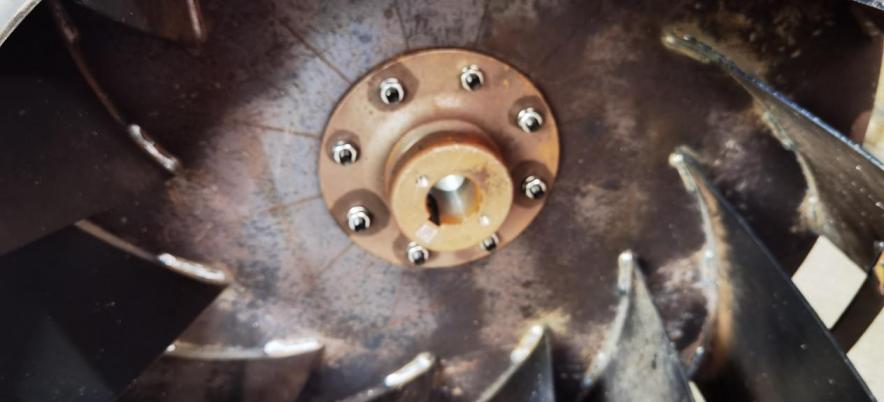
4.1 Optimizing Forming Processes for Industrial Fan Efficiency
ALTRON offers comprehensive solutions for optimizing forming processes to enhance industrial fan performance and efficiency. By leveraging advanced materials, geometric design optimization, and cutting-edge tooling technologies, ALTRON helps manufacturers achieve superior results.
4.2 Strategies for Forming Optimization
- Material Properties: Selecting materials with optimal properties for forming, such as high strength and ductility, can improve forming efficiency and reduce material waste.
- Geometric Design:Designing components with optimized geometries and draft angles facilitates the forming process and minimizes the risk of defects such as wrinkling and tearing.
- Tooling Optimization: Investing in high-quality tooling and die sets improves forming accuracy and repeatability, reducing scrap rates and rework.
4.3 Role of Material Properties, Geometric Design, and Tooling
- Material Properties:The mechanical properties of the material influence its formability and the feasibility of specific forming processes.
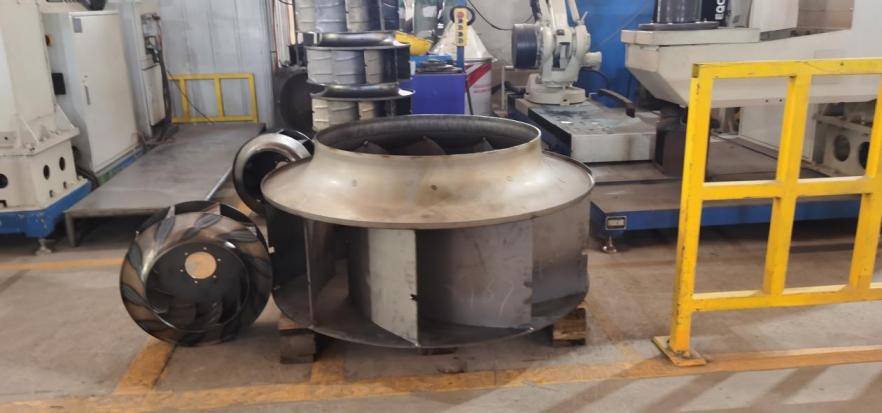
- Geometric Design: Optimized geometries contribute to the efficiency and accuracy of forming processes, ensuring consistent results.
- Tooling:Proper selection and maintenance of forming tools are essential for achieving precise and reliable forming results.
Exploring Advanced Welding Technologies for Industrial Fans
In the realm of industrial fan manufacturing, advanced welding technologies have emerged as game-changers, offering enhanced precision, efficiency, and quality. Among these technologies are laser welding, electron beam welding, and friction stir welding, each presenting unique advantages and challenges.
5.1 Laser Welding
Laser welding employs highly focused laser beams to join metals with exceptional precision and minimal heat input. Its non-contact nature enables the welding of intricate geometries without distortion, making it ideal for delicate components. However, the initial investment in equipment and the need for skilled operators pose challenges for adoption.
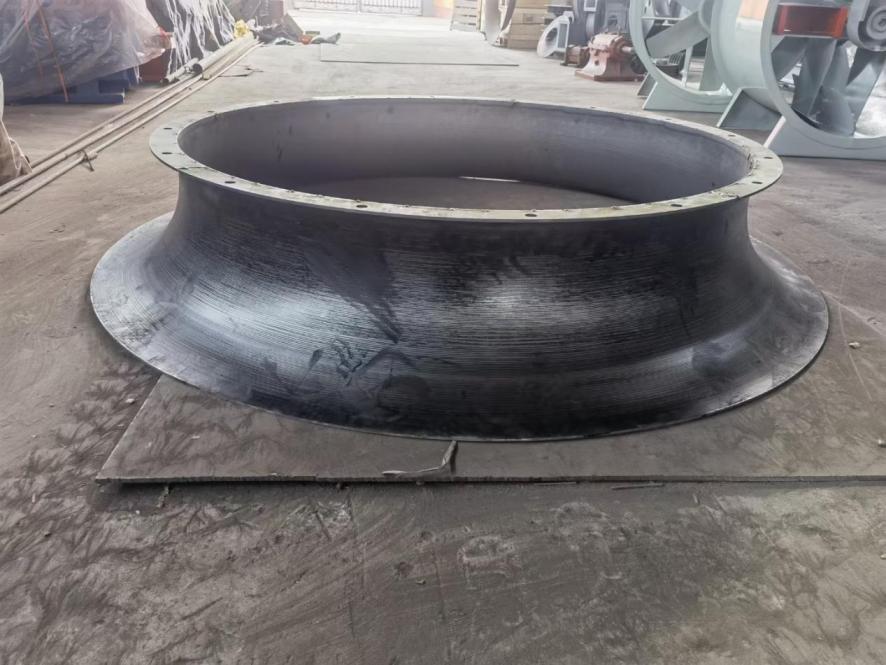
5.2 Electron Beam Welding
Electron beam welding utilizes a focused beam of high-velocity electrons to create welds with deep penetration and minimal heat-affected zones. This technology is particularly advantageous for welding thick materials and dissimilar metals. Yet, its vacuum chamber requirement and sensitivity to environmental factors may present operational challenges.
5.3 Friction Stir Welding
Friction stir welding is a solid-state joining process that involves rotating a non-consumable tool along the joint between two workpieces. The frictional heat softens the material, allowing for plastic deformation and subsequent bonding. This technique offers superior mechanical properties and is well-suited for joining lightweight materials. However, its suitability for complex geometries and limited thicknesses may restrict its applicability.
Applications of Advanced Welding in Industrial Fan Manufacturing
In the context of industrial fan manufacturing, advanced welding technologies find diverse applications. From joining fan blades and housings to assembling motor mounts and impellers, these techniques enable the fabrication of robust and reliable fan components with high structural integrity and performance.
6.1 Quality Control in Forming and Welding Processes
Ensuring consistency and reliability in forming and welding processes is paramount in industrial fan manufacturing. ALTRON, a leading supplier of forming and welding solutions, emphasizes the importance of stringent quality control measures to meet industry standards and regulations.
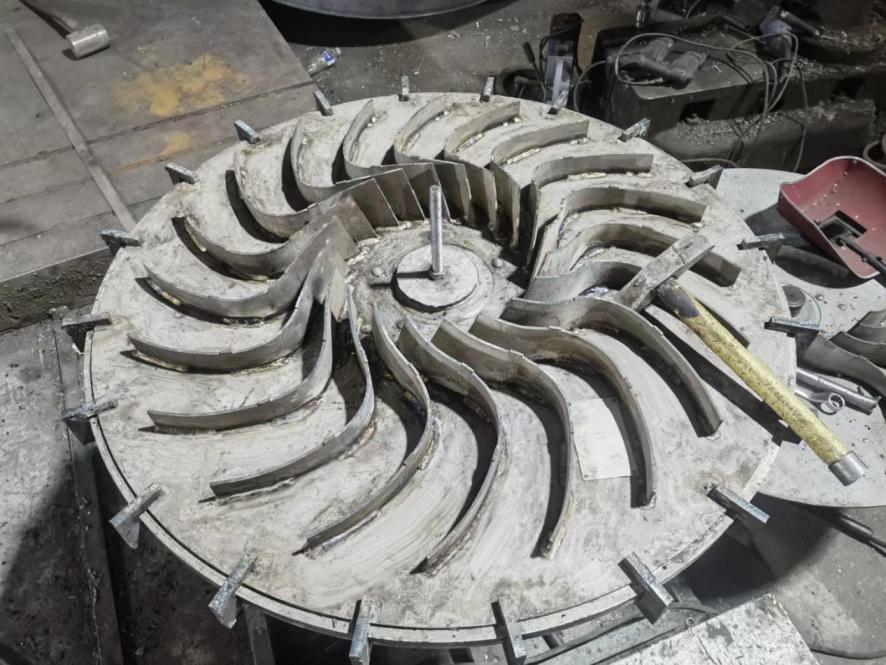
6.2 Quality Control Techniques
ALTRON employs a comprehensive range of quality control techniques to validate the integrity of formed and welded components. These include non-destructive testing (NDT) methods such as ultrasonic testing and radiographic testing, visual inspection for surface defects, and dimensional inspection to verify dimensional accuracy.
6.3 Compliance with Industry Standards and Regulations
ALTRON adheres to stringent industry standards and regulations governing forming and welding processes to ensure product quality, safety, and reliability. By maintaining compliance with standards such as ISO 9001 and ASME Boiler and Pressure Vessel Code, ALTRON demonstrates its commitment to delivering superior solutions that meet customer expectations.
Innovations in Forming and Welding for Next-Generation Industrial Fans
As the manufacturing landscape evolves, ALTRON continues to innovate, leveraging emerging technologies and trends to shape the future of forming and welding in industrial fan production.
7.1 Integration of Automation, Robotics, and Digitalization
ALTRON embraces automation, robotics, and digitalization to streamline forming and welding processes, enhance efficiency, and reduce production costs. By integrating robotics for material handling and automated inspection systems for quality control, ALTRON optimizes workflow and ensures consistent, high-quality results.
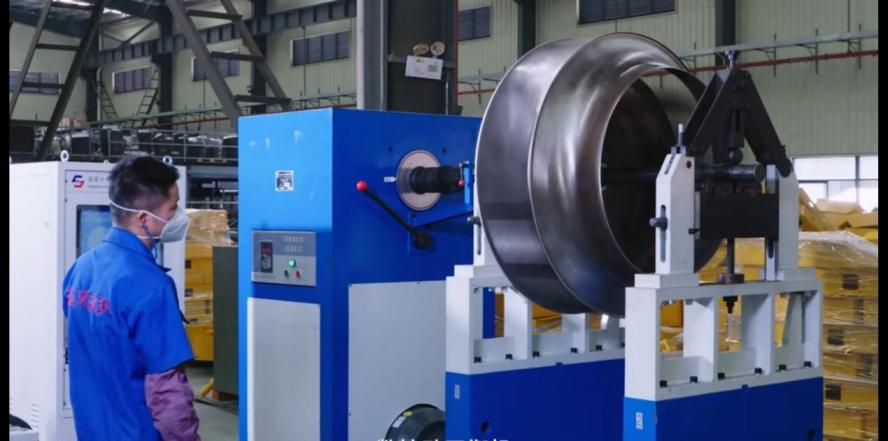
7.2 Environmental and Sustainability Implications
ALTRON recognizes the environmental and sustainability implications of manufacturing processes and strives to minimize its ecological footprint. Through initiatives such as waste reduction, energy efficiency, and recyclability, ALTRON contributes to a greener and more sustainable future for industrial fan manufacturing.
7.3 Case Studies: Successful Applications of Forming and Welding Solutions
ALTRON’s expertise in forming and welding solutions is exemplified through real-world case studies showcasing successful applications in industrial fan manufacturing. By analyzing challenges faced, solutions implemented, and outcomes achieved, these case studies provide valuable insights and best practices for incorporating ALTRON’s solutions into production processes.
Maximizing Efficiency and Reliability: Why Choose ALTRON
8.1 Enhanced Precision and Customization
One of the primary reasons to opt for forming and welding solutions from ALTRON is the enhanced precision and customization they offer. Industrial fans often require intricate designs and precise tolerances to function optimally. ALTRON’s advanced forming processes, such as stamping, rolling, and bending, allow for the creation of complex geometries with unparalleled accuracy. This level of precision ensures that industrial fans meet stringent performance requirements and operate reliably in various applications.
8.2 Superior Strength and Durability
Industrial fans are subjected to harsh operating conditions, including high temperatures, corrosive environments, and heavy loads. Therefore, it’s crucial that fan components possess superior strength and durability to withstand these challenges. ALTRON’s welding solutions, including advanced techniques like laser welding and electron beam welding, enable the creation of high-strength welds with minimal heat distortion. As a result, industrial fans manufactured using ALTRON’s solutions exhibit exceptional durability and longevity, minimizing downtime and maintenance costs for end-users.
8.3 Efficiency and Cost Savings
In today’s fast-paced manufacturing environment, efficiency is paramount. ALTRON’s forming and welding solutions are designed to streamline production processes, reduce cycle times, and minimize material waste. By optimizing forming processes and leveraging automation technologies, ALTRON helps manufacturers achieve higher throughput and lower production costs. Additionally, the superior quality and reliability of ALTRON’s solutions translate to fewer defects and rework, further contributing to cost savings over the long term.
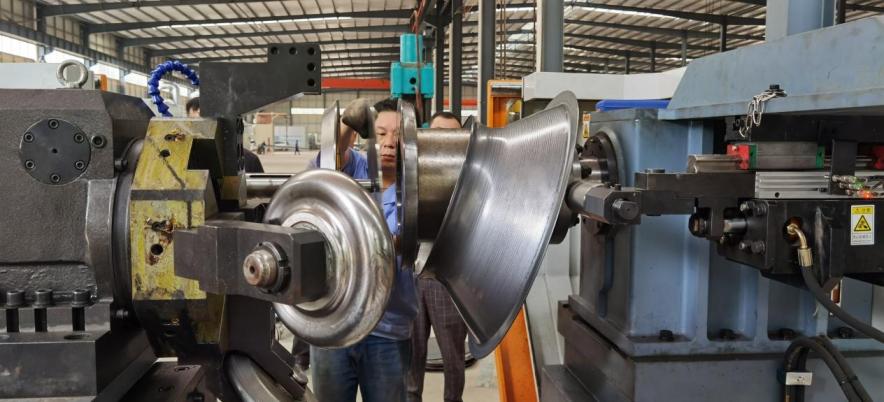
Conclusion
In conclusion, ALTRON’s comprehensive forming and welding solutions empower manufacturers to achieve optimal performance and efficiency in industrial fan manufacturing. By leveraging advanced technologies and expertise, ALTRON helps companies meet the demanding requirements of modern industrial applications while maintaining high standards of quality and reliability.