Gantry stiffener automatic welding equipment
ALTRON’S Gantry Stiffener Automatic Welding Equipment
Introduction to Welding-Industrial Fan Volute Reinforcement
Gantry Stiffener Automatic Welding Equipment is commonly used in large- and small-sized industrial centrifugal fans. Since large industrial centrifugal fans require high-strength fan volutes, industrial fan design requires welding of sweaty corner strips to strengthen the side panels of the industrial fan volutes. , to avoid deformation or noise in industrial fans in high wind pressure environments;
Gantry Stiffener Automatic Welding Equipment can be a good solution for fan manufacturers to reduce welding labor costs and eliminate complex grinding processes.
Gantry stiffener automatic welding equipment -machine mechanism
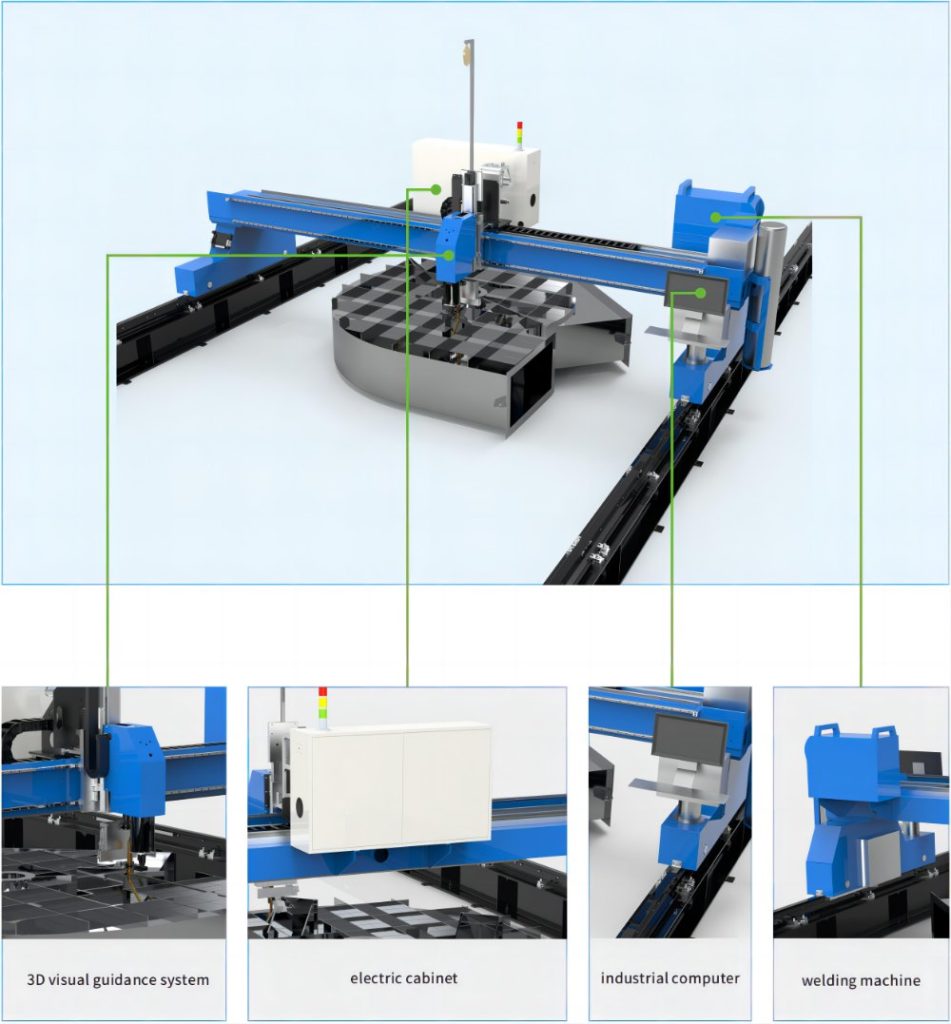
Gantry stiffener automatic welding equipment – fan manufacturer factory commissioning and installation
Gantry stiffener automatic welding equipment can solve the problem of factory mass production of side panels and pre-processing, and it does not occupy a large space, greatly improving the production cycle of industrial fans.
The entire volute can also be placed in the gantry stiffener automatic welding equipment to weld the stiffeners, which can prevent the industrial fan shell from being heated and deformed during the welding process.
Gantry Stiffener Automatic Welding Equipment
Item | HJQJ01 / HJQJ02 |
Length | Full length of track 10-20 meters, out of range support customization |
Width | Total width of equipment 4M / 5M / 6M / 7M |
Height | 3.2 Meters |
Machine Mass | 5 T (not include track) |
Applicable Product Size | Product length < total rail length – 2 meters; Product width < machine width – 1.2 meters |
Power Supply | Equipment: AC380V; Welding M/C: AC380V |
Streamlining Industrial Fan Stiffener Production with Automated Welding Equipment
In the realm of industrial manufacturing, the creation of robust and efficient equipment is paramount. Among the critical components contributing to the functionality of various machinery, industrial fan stiffeners play a pivotal role. These components are crucial for maintaining stability and durability within fans, ensuring optimal performance in diverse industrial settings.
Traditionally, the fabrication of fan stiffeners involved labor-intensive welding processes. However, the landscape of manufacturing has undergone a remarkable transformation with the advent of automated welding equipment. These advanced technologies have revolutionized production methodologies, offering a slew of benefits that augment efficiency, precision, and overall quality.
The fundamental concept behind automated welding equipment revolves around leveraging cutting-edge robotics and sophisticated machinery to execute welding tasks with unparalleled accuracy and speed. Unlike manual welding, which is prone to human error and limitations in consistency, automated systems operate with a remarkable degree of precision. This precision ensures uniformity in welds, resulting in enhanced structural integrity and longevity of the fan stiffeners.
One of the primary advantages of employing automated welding equipment in the production of industrial fan stiffeners is the significant increase in productivity. These automated systems can work tirelessly around the clock, consistently delivering high-quality welds without experiencing fatigue or errors due to human factors.
As a result, manufacturers witness a substantial boost in output while maintaining a consistent level of quality—a feat that was challenging to achieve with manual labor alone.
Furthermore, the integration of automation streamlines the overall manufacturing process. Tasks that once required multiple operators and extensive time commitments can now be accomplished seamlessly by a single automated system. This consolidation not only reduces the required manpower but also optimizes floor space, allowing for a more efficient and organized workspace within the manufacturing facility.
Another notable advantage is the reduction in material waste. Automated welding equipment, with its precise control and accuracy, minimizes the likelihood of errors that often lead to material wastage. This aspect contributes not only to cost savings but also aligns with sustainable manufacturing practices, promoting environmental responsibility within the industry.
Moreover, the implementation of automated systems in welding operations enhances workplace safety. By minimizing human intervention in hazardous welding environments, the risk of occupational hazards and injuries significantly decreases. This not only ensures a safer work environment for employees but also mitigates potential liabilities for manufacturing companies.
The versatility of automated welding equipment further amplifies its value in the production of industrial fan stiffeners. These systems can adapt to various welding techniques, accommodating different materials and designs. Whether it’s stainless steel, aluminum, or other alloys, the flexibility of automated systems allows for seamless welding across a spectrum of materials, catering to diverse manufacturing needs.
However, transitioning to automated welding systems requires careful consideration and investment. The initial setup costs and the need for specialized training for operating and maintaining these systems may pose challenges for some manufacturing entities.
Yet, the long-term benefits in terms of increased efficiency, improved product quality, and reduced operational costs far outweigh the initial investment.
In conclusion, the incorporation of automated welding equipment has revolutionized the production of industrial fan stiffeners. The precision, efficiency, and safety offered by these advanced systems have redefined manufacturing standards, setting new benchmarks for productivity and quality.
As technology continues to evolve, the utilization of automated welding equipment will likely become ubiquitous, shaping the future of industrial manufacturing across various sectors.