How To Make The Program For CNC Metal Spinning Machine
Introduction
CNC (Computer Numerical Control) metal spinning machines have transformed the precision metalworking industry. These sophisticated machines enable the creation of complex shapes and components with remarkable accuracy and efficiency.
However, the key to harnessing their full potential lies in mastering the art of programming.
In this comprehensive guide, we’ll delve into the intricacies of creating a program for CNC metal spinning machines, ensuring that you’re equipped with the knowledge and skills to bring your designs to life. let us discuss how to make the program for cnc metal spinning machine.
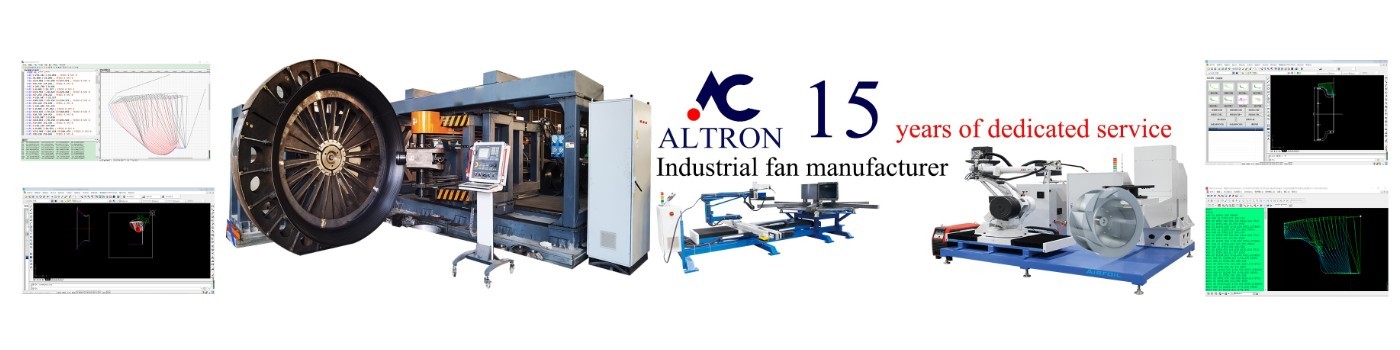
The Essentials of CNC Metal Spinning
Before we jump into the programming aspects, let’s gain a solid understanding of CNC metal spinning. At its core, CNC metal spinning involves rotating a metal blank while shaping it using controlled tools and machinery.
The precision and intricacy of this process are achieved through the computer program that guides the machine’s every move.
Step 1: Blueprint Your Design
The first step in creating a program for your CNC metal spinning machine is to design your project. This digital representation will serve as the foundation for your program. When crafting your blueprint, consider the following elements:
Material Selection: Choose the right metal for your project, considering the unique properties of different metals that can affect the spinning process.
Dimensions and Tolerances: Specify exact dimensions and tolerances that your final product must meet. Precise measurements are crucial in CNC metal spinning.
Tool Selection: Determine the tools and toolpaths required to shape the metal. The choice of tools and their sequence can significantly impact the outcome.
Step 2: Utilize CAM Software
After designing your project, it’s time to translate it into machine-readable instructions. This is where Computer-Aided Manufacturing (CAM) software plays a vital role.
CAM software facilitates the generation of toolpaths, setting cutting speeds, and configuring other machining parameters.
Several CAM software options are available, such as Mastercam, Fusion 360, and SolidCAM. Choose the one that best aligns with your project’s requirements and your team’s expertise.
Step 3: Machine Setup
Before programming, it’s crucial to ensure your CNC metal spinning machine is correctly set up and calibrated. This entails:
Secure Material Fastening: The metal blank must be securely fastened to the chuck to prevent movement during the spinning process.
Tool Installation: Ensure that all necessary tools are correctly installed and aligned.
Safety Measures: Implement safety precautions to protect operators and prevent accidents.
Step 4: Programming Your CNC Metal Spinning Machine
Here’s where the heart of the matter lies – programming your CNC metal spinning machine. Let’s break down the process:
1. G-Code Generation:
G-code serves as the language your CNC machine understands. It consists of commands that dictate the machine’s movements and actions. G-code generation typically involves:
- Defining Toolpaths:Specify the paths the tools will follow to create the desired shape.
- Selecting Cutting Speeds and Feeds:Determine the optimal speeds and feeds to achieve precision without compromising tool life.
- Tool Changes:If your project necessitates multiple tools, program tool changes at the relevant stages of the process.
- Spindle Speed Control:Adjust the spindle speed to match the specific requirements of your material and tooling.
2. Tool Compensation:
In CNC metal spinning, tool wear and deflection can occur as the metal stretches and forms. To account for this, implement tool compensation in your program.
Tool radius compensation (G41 and G42) is commonly used to maintain the desired dimensions and tolerances throughout the process.
3. Test Runs and Debugging:
Prior to full-scale production, conduct test runs to identify any potential issues or errors in your program. Check for tool collisions, verify that toolpaths are accurate, and ensure that the final product aligns with your design specifications.
4. Optimization:
Optimize your program for efficiency and precision. This includes fine-tuning cutting speeds, feeds, and toolpath strategies to reduce cycle times while preserving quality.
Step 5: Documentation and Quality Assurance
Proper documentation is often an overlooked but vital step in CNC metal spinning. Create a comprehensive set of instructions and records for your program.
This documentation will serve as a reference for future runs and troubleshooting, ensuring consistency in your production process.
Incorporate a quality assurance process to monitor the output of your CNC metal spinning machine. Regular inspections and measurements should be conducted to confirm that the finished components meet your specified tolerances and quality standards.
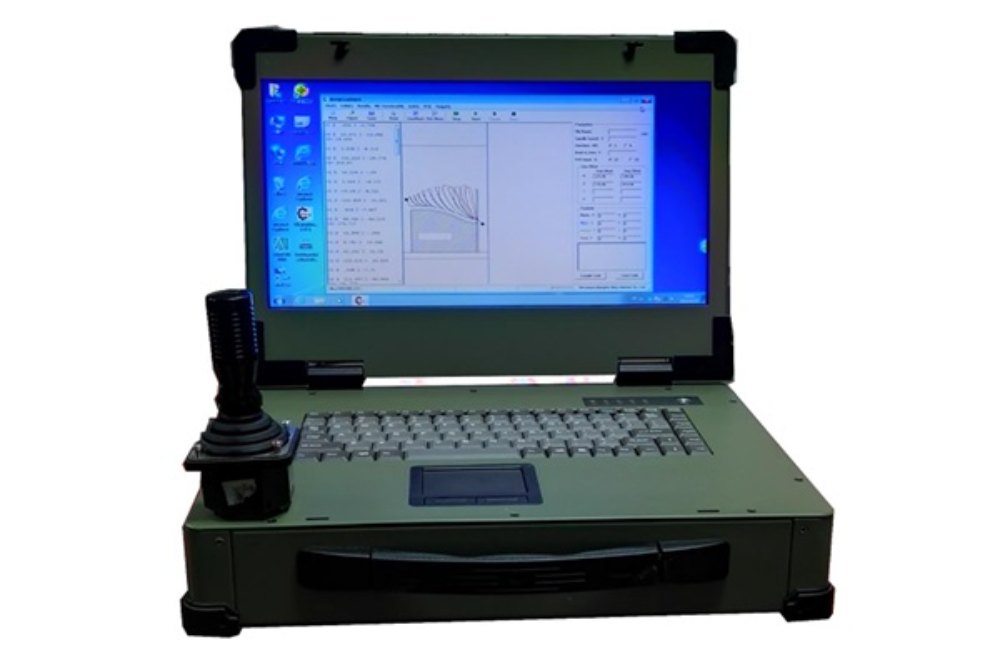
Conclusion
Crafting a program for your CNC metal spinning machine is a meticulous process that demands careful planning, programming, and quality assurance. By following these steps, you can ensure your CNC metal spinning projects are executed with precision and efficiency.
Altron provides free CNC metal spinning software to all customers who purchase CNC spinning machines! Improve the efficiency of metal spinning program writing and shorten the debugging time!