2024 New Industrial Centrifugal Fans Manufacturing Solutions
Choosing ALTRON for custom industrial centrifugal fan manufacturing solutions ensures access to unparalleled expertise, quality, customization options, and customer support. With a proven track record of delivering innovative fan solutions tailored to meet the unique needs of customers across various industries, ALTRON is the trusted partner for all industrial ventilation and air movement requirements. For inquiries and consultation, interested parties can reach out to ALTRON via email at crystal@auto-altron.com or WhatsApp at +86 156 2739 7226.
Introduction to Industrial Centrifugal Fans
Industrial centrifugal fans are an important part of various industries. Plays a vital role in ventilation, air movement and air pollution control systems. These fans are designed to produce large amounts of airflow at varying pressures. Making it indispensable in environments where air circulation is critical to process efficiency, air quality and worker safety.
1.1 Components and Working Principles
Centrifugal fans consist of several key components, including an impeller, housing, inlet/outlet ducts, and motor. The impeller, often composed of blades or vanes, rotates within the housing, drawing air in axially and accelerating it radially before discharging it tangentially through the outlet duct. This radial acceleration creates the necessary airflow and pressure for industrial applications.
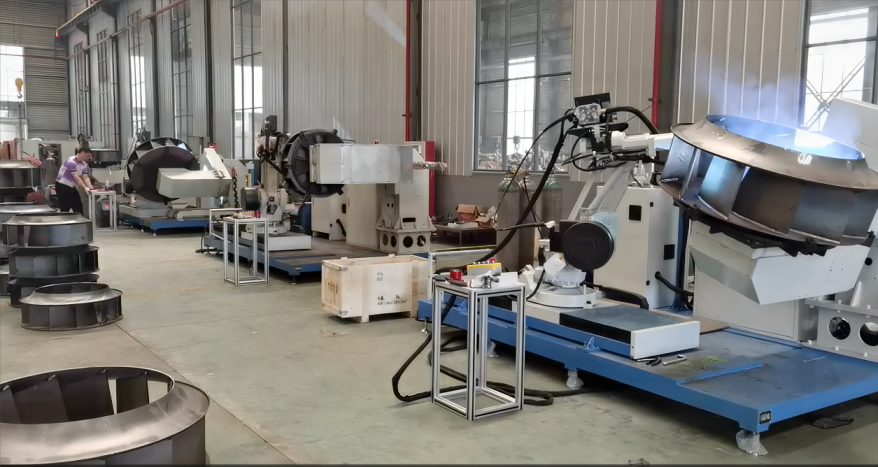
1.2 Importance of Efficient Ventilation
Efficient ventilation and air movement are paramount in industrial settings for several reasons. Proper ventilation helps regulate temperature, remove airborne contaminants, control humidity levels, and maintain air quality. In facilities such as manufacturing plants, warehouses, refineries, and power plants, effective air circulation is critical for ensuring worker comfort, equipment performance, and compliance with safety regulations.
1.3 Supplier Spotlight: ALTRON
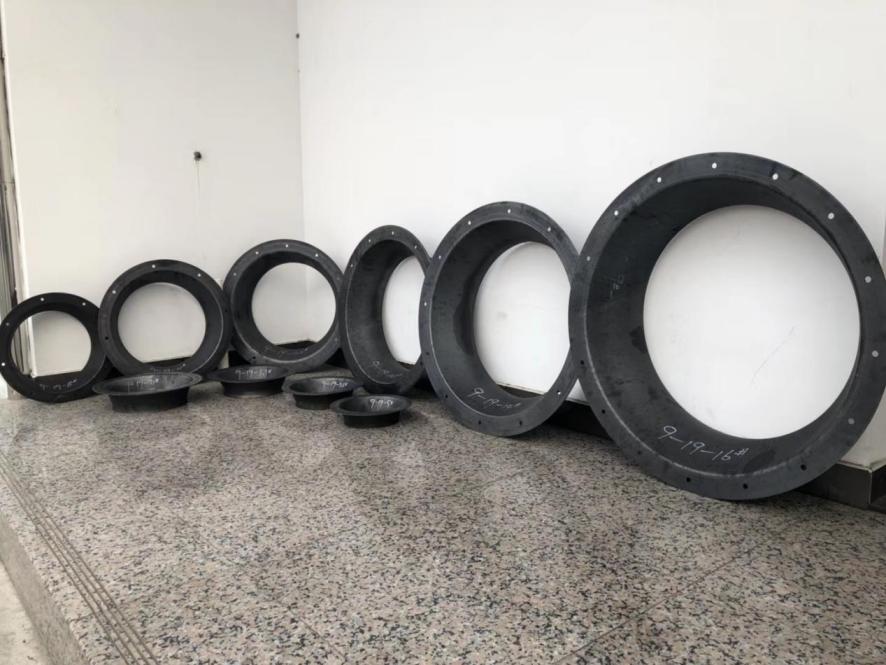
For industrial centrifugal fan manufacturing solutions, ALTRON stands out as a leading provider, offering a comprehensive range of high-performance fans tailored to meet the diverse needs of industries worldwide. With a focus on innovation, quality, and customer satisfaction, ALTRON delivers cutting-edge solutions backed by decades of engineering expertise and a commitment to excellence. Whether it’s for HVAC systems, industrial processes, or specialized applications, ALTRON’s centrifugal fans are engineered for performance, reliability, and longevity, making them the preferred choice for industrial ventilation and air movement solutions.
Types of Industrial Centrifugal Fans
Industrial centrifugal fans come in various types, each designed to meet specific airflow, pressure, and application requirements.
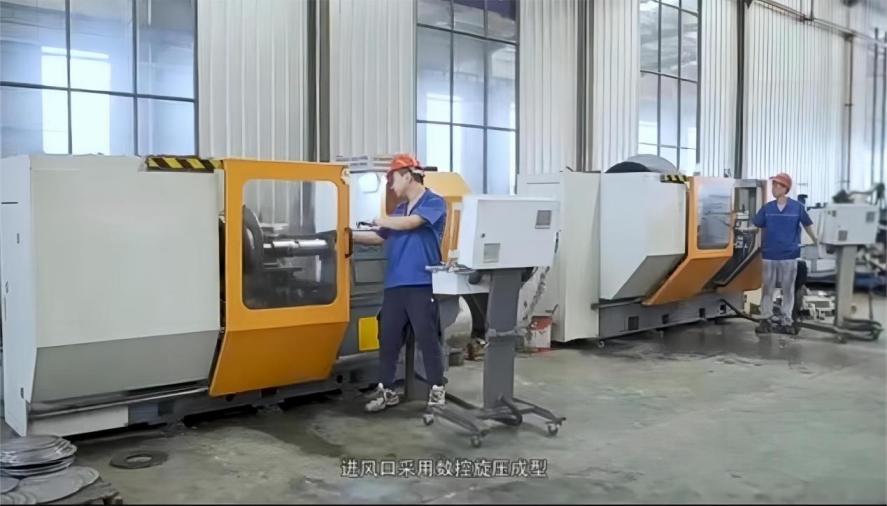
2.1 Forward-curved, Backward-Curved, and Radial-Blade Fans
Forward-curved, backward-curved, and radial-blade centrifugal fans differ in their blade orientation and airflow characteristics. Forward-curved fans are efficient for low-pressure, high-flow applications such as HVAC systems and ventilation. Backward-curved fans are ideal for high-pressure, low-flow conditions, commonly used in dust collection, combustion air supply, and industrial drying processes. Radial-blade fans offer a balance between airflow and pressure, suitable for pneumatic conveying, air handling units, and material handling systems.
2.2 Applications Across Industries
Each type of centrifugal fan finds its niche in various industries. Forward-curved fans are prevalent in HVAC systems for commercial buildings, while backward-curved fans are integral to heavy industries like mining, chemical processing, and power generation. Radial-blade fans are versatile and find applications in food processing, pharmaceutical manufacturing, and automotive production, where precise airflow control is essential.
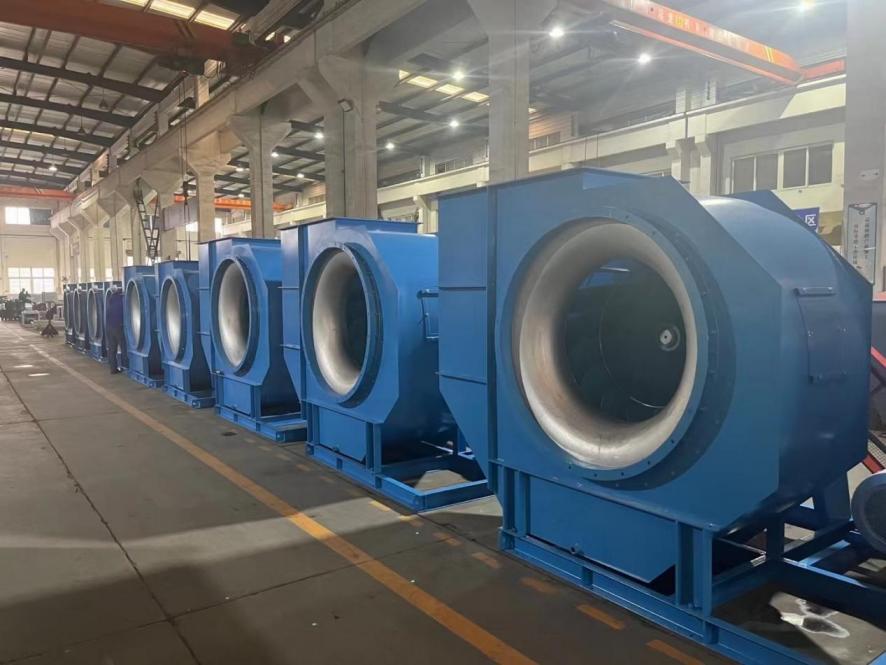
Factors Influencing Industrial Centrifugal Fan Selection
Selecting the right centrifugal fan for industrial applications requires careful consideration of several factors.
3.1 Airflow Requirements and Pressure Characteristics
Understanding the required airflow rate and pressure characteristics is fundamental in fan selection. Factors such as duct size, system resistance, and air density influence the fan’s performance and efficiency.
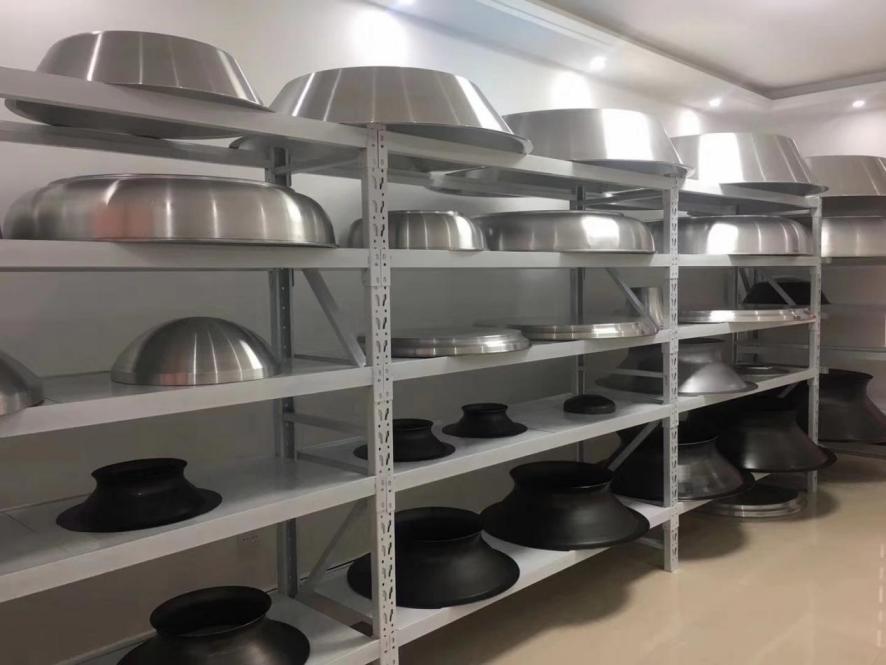
3.2 Efficiency and Environmental Conditions
Efficiency is critical for reducing energy consumption and operational costs. Additionally, environmental conditions such as temperature, humidity, corrosive gases, and explosive atmospheres dictate the choice of materials and fan construction to ensure durability and safety.
3.3 Guidelines for Selection
When selecting a centrifugal fan, engineers and facility managers should assess their specific requirements, consult with experts, and consider factors such as fan performance curves, system design, noise levels, and maintenance requirements to make informed decisions.
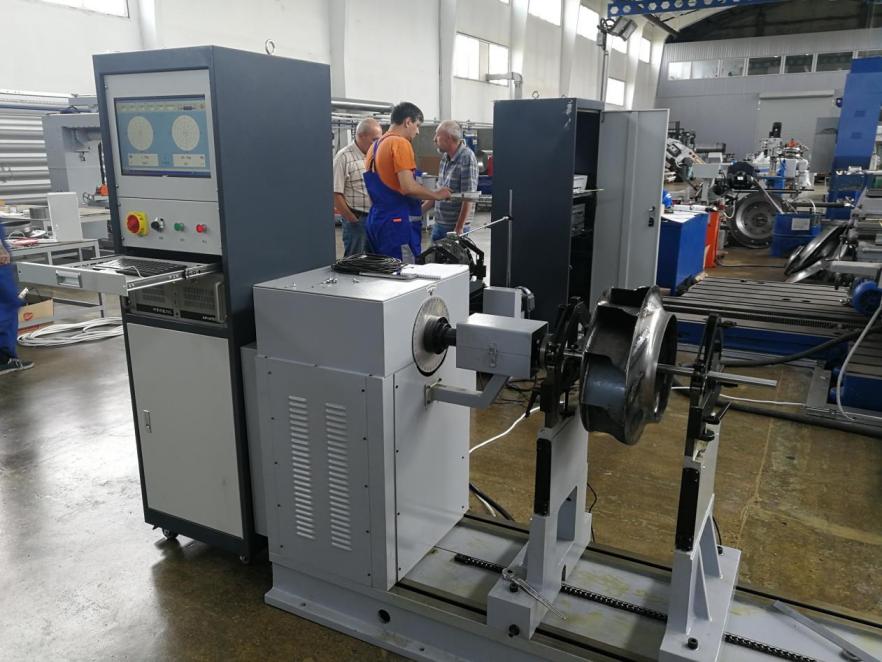
Design and Manufacturing Process of Industrial Centrifugal Fans
The design and manufacturing process of industrial centrifugal fans requires precision engineering, advanced materials, and stringent quality control measures.
4.1 Precision Engineering and Material Selection
Designing a centrifugal fan involves optimizing blade geometry, impeller diameter, and housing shape to achieve the desired airflow and pressure characteristics. Materials such as stainless steel, aluminum, and composite alloys are chosen based on their strength, corrosion resistance, and temperature tolerance.
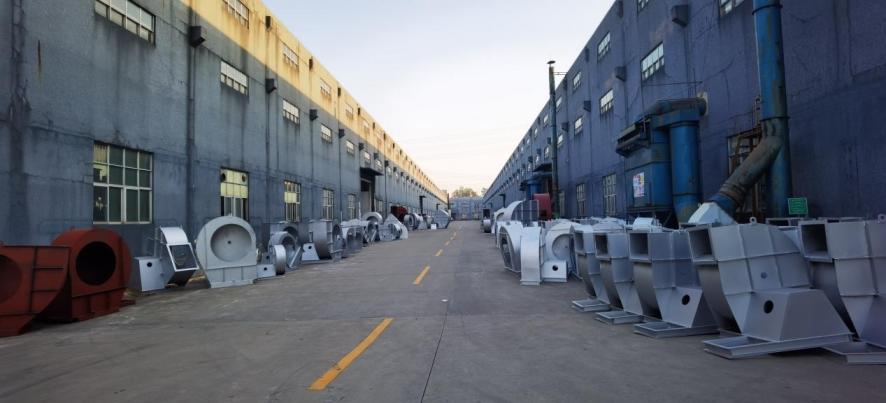
4.2 Quality Control and Advanced Manufacturing Techniques
Quality control is paramount throughout the manufacturing process to ensure consistent performance and reliability. Advanced manufacturing technologies such as computer-aided design (CAD), computational fluid dynamics (CFD), laser cutting, and robotic welding increase precision and efficiency. This results in the production of high-quality centrifugal fans that meet strict industry standards.
Applications of Industrial Centrifugal Fans
Industrial centrifugal fans find extensive applications across diverse industries, playing a pivotal role in various processes that require efficient air movement and ventilation.
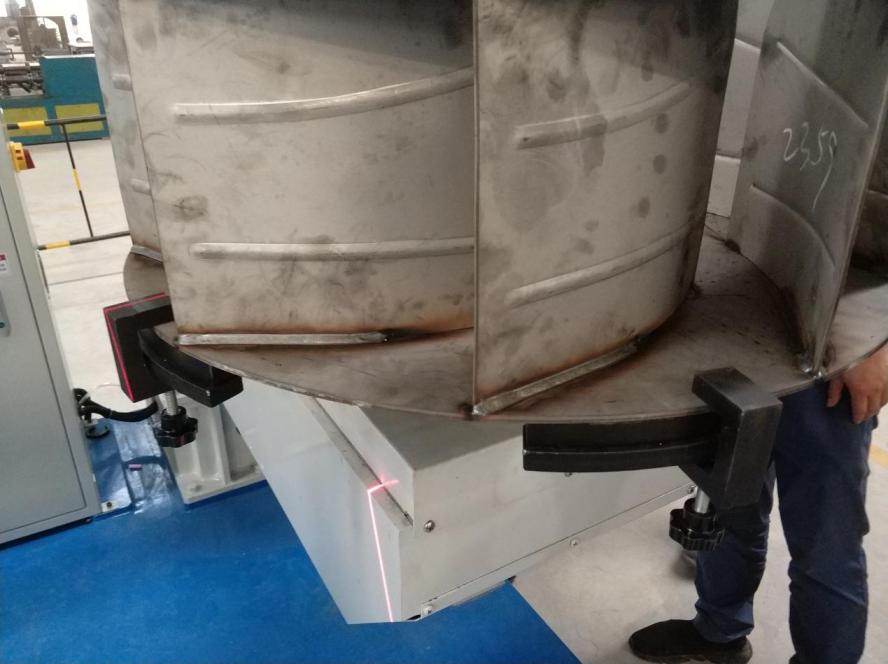
5.1 HVAC Systems and Commercial Buildings
In HVAC (Heating, Ventilation, and Air Conditioning) systems, centrifugal fans are commonly used to circulate air, regulate temperature, and maintain indoor air quality in commercial buildings, offices, and residential complexes. These fans help distribute conditioned air through ductwork, ensuring comfort and productivity for occupants while optimizing energy consumption.
5.2 Industrial Ventilation and Air Pollution Control
In industrial settings such as manufacturing plants, refineries, and chemical processing facilities. Centrifugal fans are essential for ventilation and air pollution control. They help remove pollutants, exhaust and harmful gases from the air. Ensure employees have a safe and healthy working environment while complying with environmental regulations.
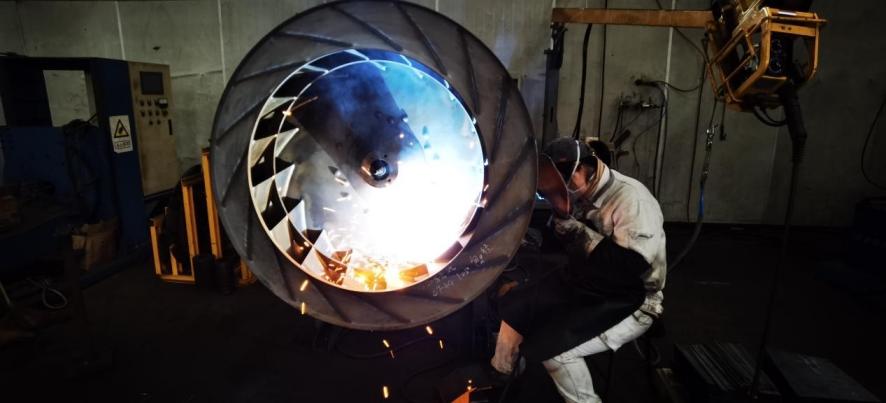
5.3 Material Handling and Pneumatic Conveying
Centrifugal fans are integral to material handling and pneumatic conveying systems used in industries like mining, agriculture, and food processing. They facilitate the movement of bulk materials, powders, and granules through pipelines, enabling efficient production processes and logistical operations.
Energy Efficiency and Performance Optimization
Energy efficiency is a crucial consideration in the design and operation of industrial centrifugal fans, as they consume significant amounts of electricity in industrial applications.
6.1 Optimizing Fan Performance
To optimize fan performance and reduce energy consumption, engineers employ various strategies. Examples include selecting the correct fan type and size for the application, optimizing the system design, and implementing speed control mechanisms such as variable frequency drives (VFDs). To match airflow requirements to demand.
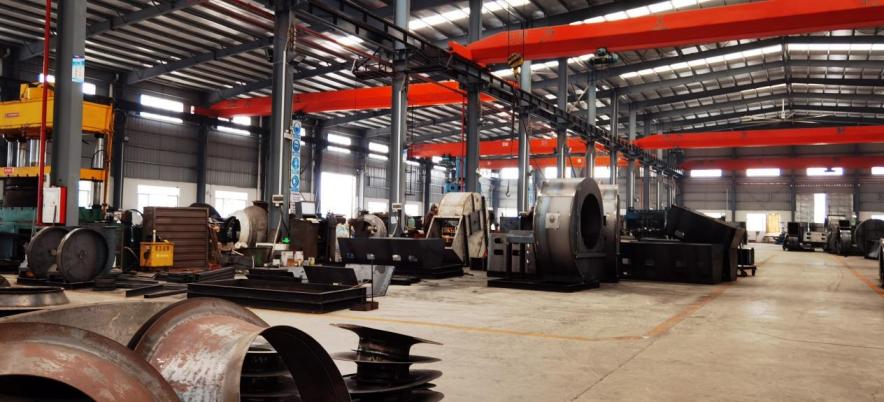
6.2 Advancements in Fan Design
Recent advancements in fan design focus on improving aerodynamic efficiency, reducing noise levels, and enhancing overall performance. Innovations such as computational fluid dynamics (CFD) simulation, blade optimization, and the use of lightweight materials contribute to energy savings and operational reliability.
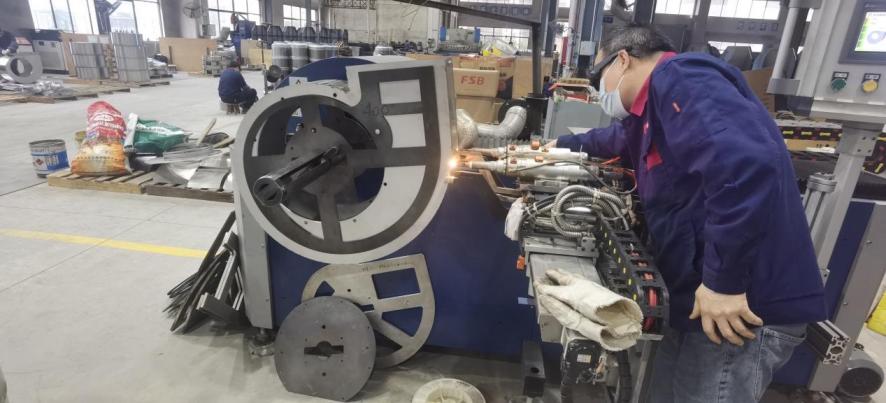
Maintenance and Troubleshooting of Industrial Centrifugal Fans
Proper maintenance and timely troubleshooting are essential for ensuring the optimal performance and longevity of industrial centrifugal fans.
7.1 Maintenance Guidelines
Regular maintenance practices include inspecting and cleaning fan blades, lubricating bearings, checking belt tension, and monitoring motor performance. Scheduled inspections and preventive maintenance help identify potential issues before they escalate, minimizing downtime and costly repairs.
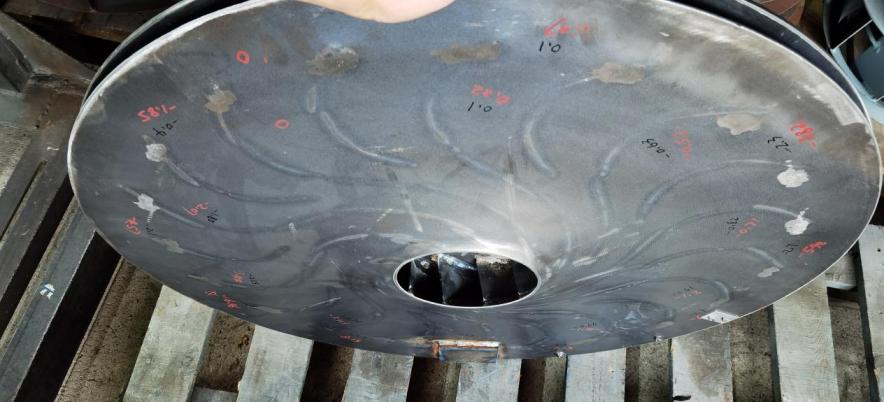
7.2 Troubleshooting Techniques
Common issues with centrifugal fans include motor overheating, bearing failures, imbalance, and excessive noise. Troubleshooting techniques involve diagnosing the root cause of the problem, which may require visual inspection, vibration analysis, or performance testing, followed by appropriate corrective measures.
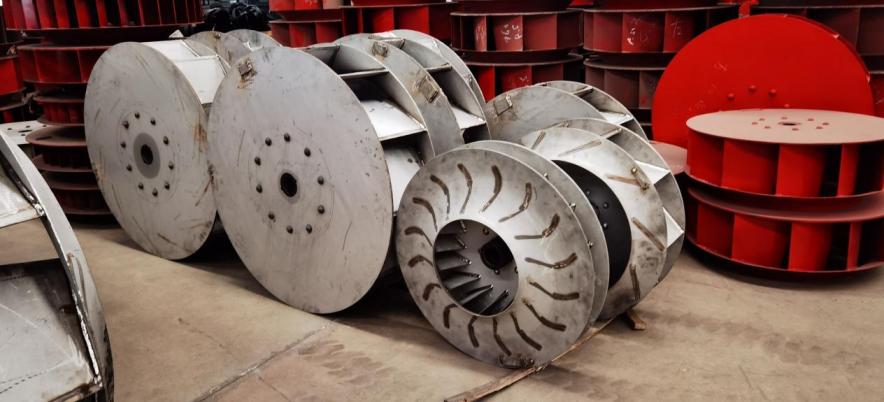
Future Trends in Industrial Centrifugal Fans
The future of industrial centrifugal fans is driven by technological advancements and industry trends that focus on sustainability, digitalization, and enhanced performance.
8.1 Innovations in Fan Technology
Future centrifugal fan designs are expected to incorporate advanced materials, aerodynamic optimization, and smart control systems to improve energy efficiency, reliability, and environmental sustainability. Integration with IoT (Internet of Things) platforms enables remote monitoring, predictive maintenance, and real-time performance optimization.
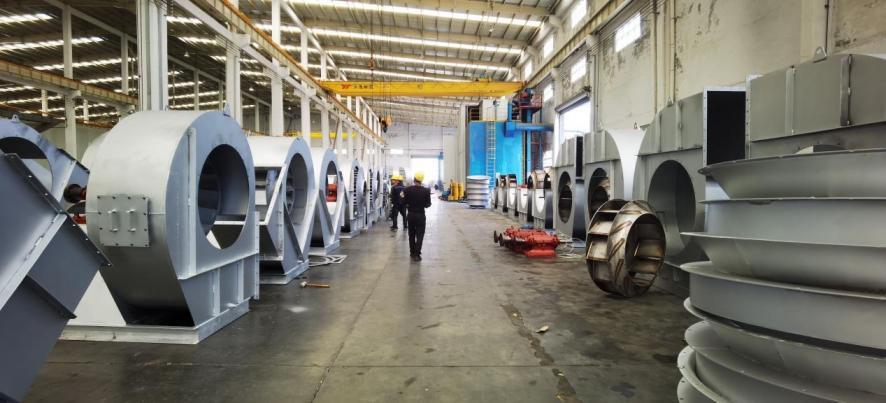
8.2 Digitalization and Data Analytics
Digitalization plays a crucial role in the development of industrial centrifugal fans. Manufacturers use data analytics, machine learning and artificial intelligence to optimize turbine operation, predict maintenance needs and improve overall system efficiency. Predictive analytics algorithms help identify patterns and anomalies in fan performance data, enabling proactive maintenance strategies and minimizing unplanned downtime.
Steps to Custom Industrial Centrifugal Fans Manufacturing Solutions
Customizing industrial centrifugal fans to meet specific requirements is a meticulous process that involves careful engineering, precise manufacturing, and rigorous quality control measures.
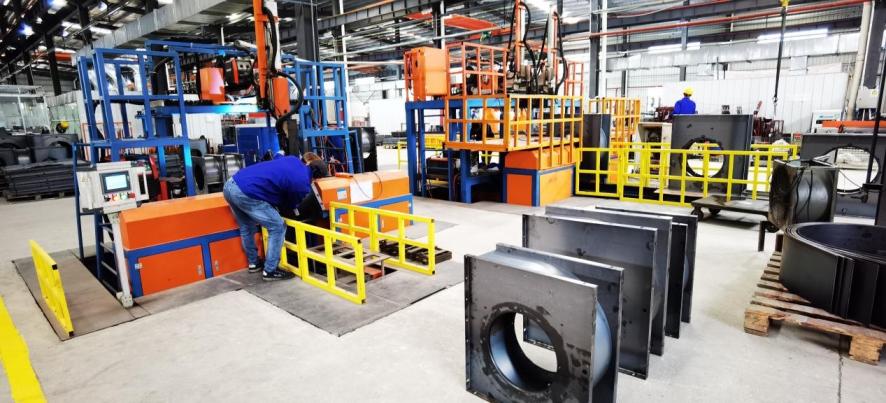
9.1 Understanding Customer Needs
The first step in customizing industrial centrifugal fans is to understand the unique needs and requirements of the customer. This involves gathering information about the application, airflow requirements, pressure characteristics, space constraints, environmental conditions, and any other relevant factors that may influence fan performance and design.
9.2 Engineering Design and Analysis
Once customer needs are identified. ALTRON engineers use advanced design software and cal
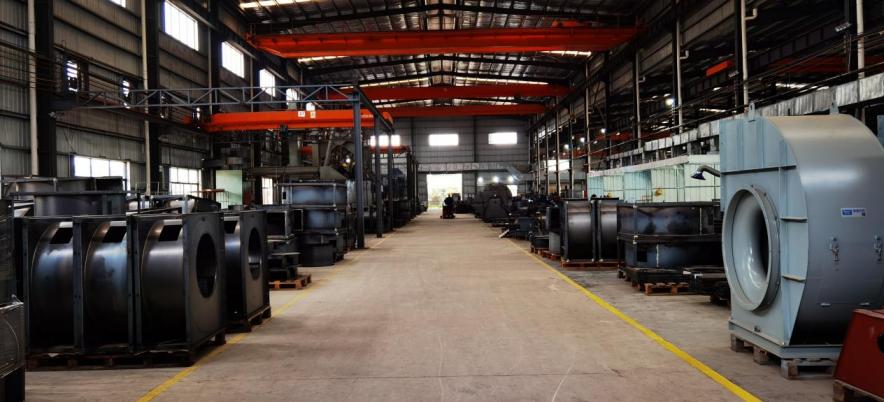
culation tools to develop custom fan solutions. This includes optimizing impeller geometry, casing design, blade angles and motor specifications. To ensure optimal airflow, pressure and efficiency for the intended application. Computational fluid dynamics (CFD) simulations are often employed to analyze airflow patterns and optimize fan performance.
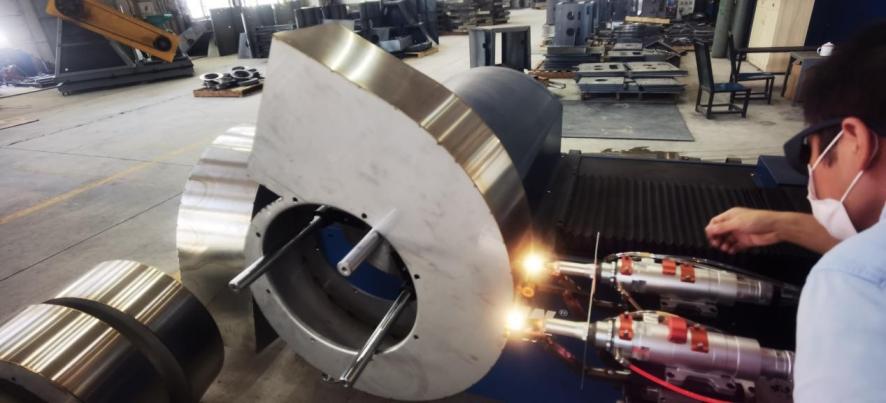
9.3 Prototype Development and Testing
After the design phase, a prototype of a customized industrial centrifugal fan was manufactured. and undergo rigorous testing in ALTRON’s state-of-the-art testing facilities. Performance testing includes measuring airflow, pressure, power consumption and noise levels. To validate designs and ensure compliance with customer specifications and industry standards. Any necessary adjustments or refinements are made based on the test results to optimize fan performance and reliability.
9.4 Manufacturing and Production
Once the prototype is approved, ALTRON’s skilled craftsmen and technicians proceed with the manufacturing of the custom industrial centrifugal fans. Advanced manufacturing techniques such as laser cutting, CNC machining, robotic welding, and precision assembly are employed to ensure consistency, accuracy, and high-quality craftsmanship. Quality control inspections are conducted at every stage of the manufacturing process to maintain the highest standards of product excellence.
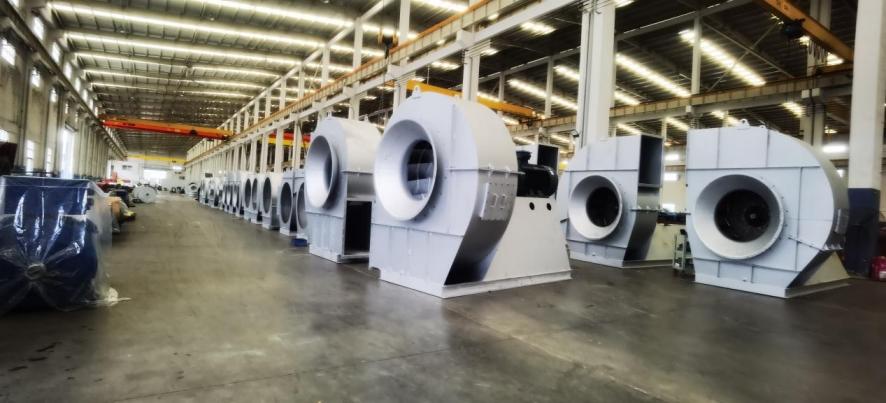
9.5 Delivery and Installation Support
ALTRON provides comprehensive support throughout the entire process, from initial consultation to final installation. Once the custom industrial centrifugal fans are manufactured, they are carefully packaged and delivered to the customer’s location. ALTRON’s technical support team is available to assist with installation, startup, and troubleshooting, ensuring a seamless integration of the fan solution into the customer’s facility.
Why Choose ALTRON
ALTRON stands out as a premier provider of industrial centrifugal fans manufacturing solutions for several compelling reasons.
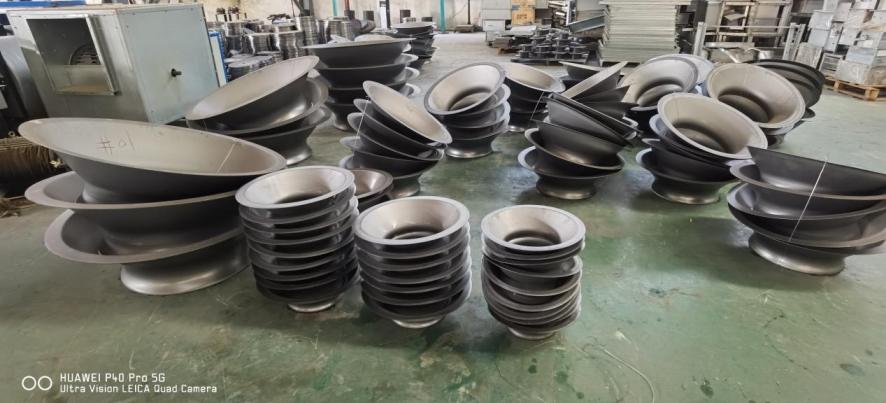
10.1 Expertise and Experience
With years of experience in the industry, ALTRON has accumulated a wealth of knowledge and expertise in designing and manufacturing custom industrial centrifugal fans for a wide range of applications. Their team of skilled engineers, technicians, and craftsmen is dedicated to delivering innovative solutions that exceed customer expectations.
11.1 Quality and Reliability
ALTRON is committed to delivering products of the highest quality and reliability. Their stringent quality control measures ensure that every fan is manufactured to the highest standards of craftsmanship and performance. From material selection to final inspection, ALTRON maintains a relentless focus on quality throughout the entire manufacturing process.
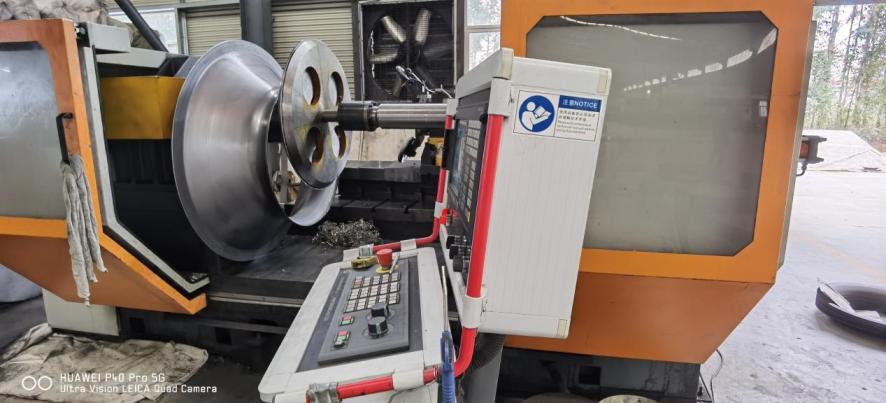
11.2 Customization and Flexibility
One of ALTRON’s main advantages is the ability to customize industrial centrifugal fans. to meet the unique needs and requirements of our customers. Whether it’s specific airflow requirements, pressure characteristics or space constraints. ALTRON has the engineering expertise and manufacturing capabilities to customize fan solutions to meet customer specific specifications.
11.3 Responsive Customer Support
ALTRON prides itself on providing exceptional customer support and service. From initial consultation to post-sales support, their dedicated team is committed to ensuring the success of every project. Customers can rely on ALTRON for prompt communication, technical assistance, and ongoing support throughout the entire lifecycle of their fan solution.
Conclusion
In conclusion, industrial centrifugal fans play a crucial role in various industrial processes, providing efficient ventilation, air movement, and environmental control solutions. Understanding the different types of fans, factors influencing fan selection, and the design and manufacturing process is essential for optimizing performance, energy efficiency, and operational reliability in industrial applications.