How to Ensure Cost-Effectiveness in Industrial Fan Manufacturing Solutions?
In the realm of industrial fan manufacturing, precision and efficiency are paramount. ALTRON AUTO, a leading supplier in this domain, has been spearheading innovations through the utilization of spinning forming techniques. This blog explores the transformative impact of spinning forming on industrial fan production, highlighting its advantages over traditional methods and showcasing ALTRON AUTO’s groundbreaking solutions.
Understanding Spinning Forming
1.1 Overview of Spinning Forming
Spinning forming, also known as spin forming or metal spinning, is a metalworking process that entails the rotation of a metal disc or tube on a spinning lathe. As the metal rotates, it is gradually shaped into the desired form using specialized tools. This process allows for the creation of seamless, high-precision components with a smooth surface finish.
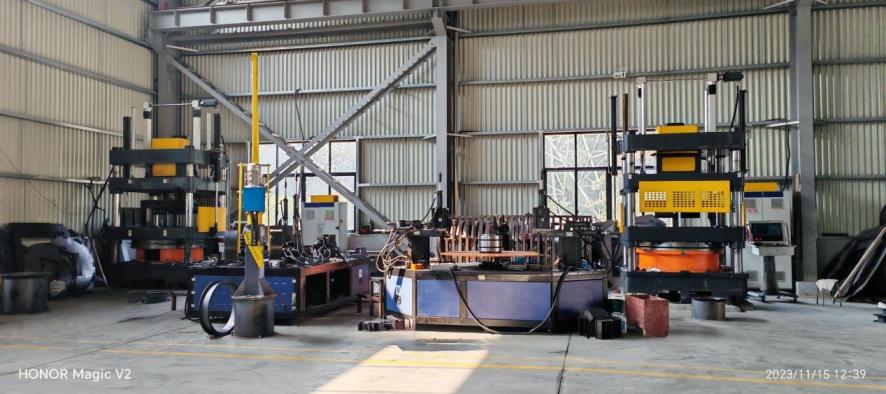
1.2 Advantages of Spinning Forming
- Smooth Surface Finish: One of the primary advantages of spinning forming is the ability to achieve a consistently smooth surface finish, free from imperfections often associated with other manufacturing methods.
- High Accuracy:Spinning forming enables the production of components with exceptional dimensional accuracy, meeting stringent quality standards and specifications.
- Material Efficiency: By minimizing material waste and optimizing the use of raw materials, spinning forming offers cost-effective solutions without compromising on quality.
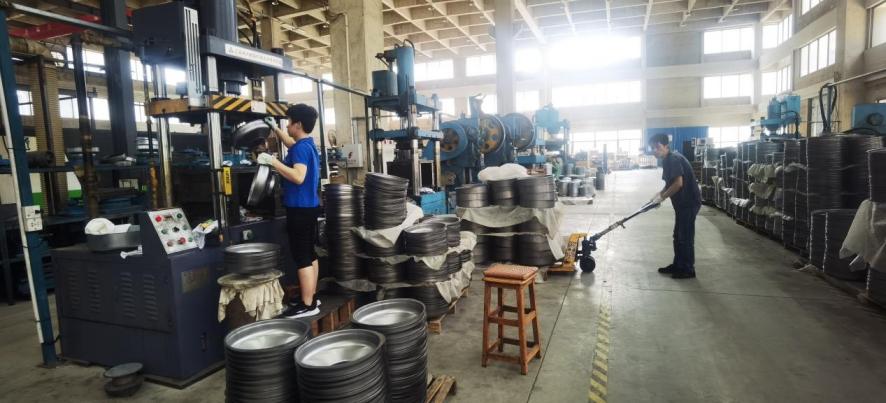
1.3 Comparison with Traditional Methods
When compared to traditional methods such as deep drawing and welding, spinning forming emerges as the superior choice for industrial fan manufacturing. Unlike deep drawing, which may result in material thinning and deformation, spinning forming maintains uniform material thickness throughout the component. Additionally, the absence of welding seams eliminates potential weak points, enhancing the durability and structural integrity of the fan components.
Steel Air Inlet: A Case Study in Spinning Forming
2.1 Detailed Process of Spinning Forming
ALTRON AUTO’s expertise in spinning forming is exemplified in the production of steel air inlets for industrial fans. The process begins with the selection of high-quality steel blanks, which are mounted onto spinning lathes. As the blanks rotate, precision tools shape the metal into seamless air inlets with smooth contours and accurate dimensions.
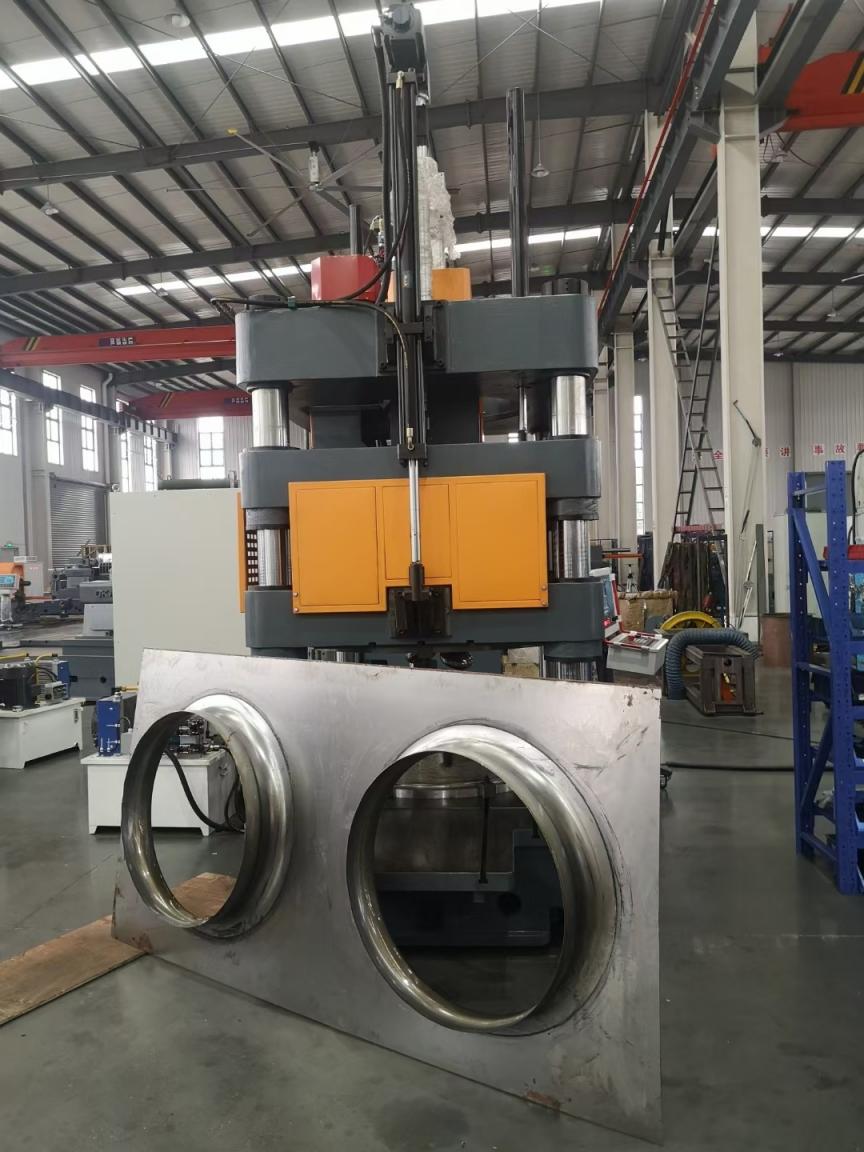
2.2 Advantages and Applications
- Smooth Surface:The spinning forming process ensures a flawless surface finish, facilitating optimal airflow and reducing turbulence within the fan system.
- Material Efficiency:By minimizing material waste and optimizing the use of resources, ALTRON AUTO delivers cost-effective solutions to its customers.
- Cost-Effectiveness:Compared to alternative manufacturing methods, spinning forming offers significant cost savings without compromising on quality.
2.3 Application in Industrial Fan Manufacturing
The steel air inlets produced through spinning forming find widespread application in industrial fan manufacturing. These critical components play a vital role in ensuring efficient airflow and ventilation within industrial facilities, contributing to enhanced productivity and worker safety.
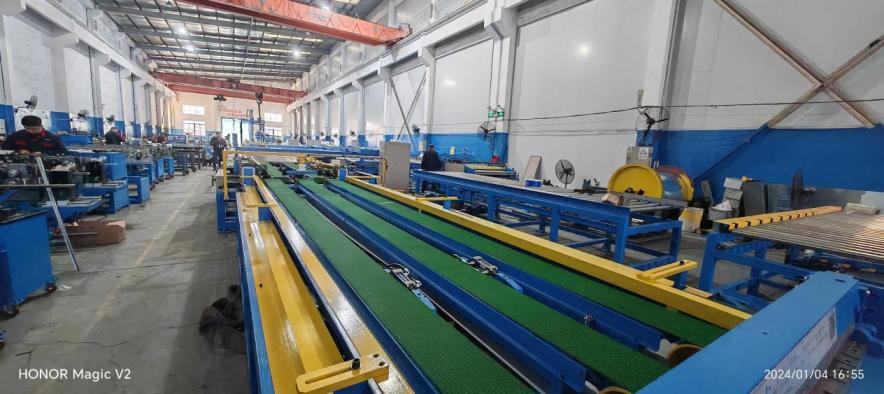
Steel Front Disk: Enhancing Efficiency with Spinning Forming
3.1 Exploring the Process
ALTRON AUTO’s commitment to innovation is evident in its approach to manufacturing steel front disks for industrial fans. Through spinning forming, the company achieves unparalleled precision and efficiency in the production of these essential components.
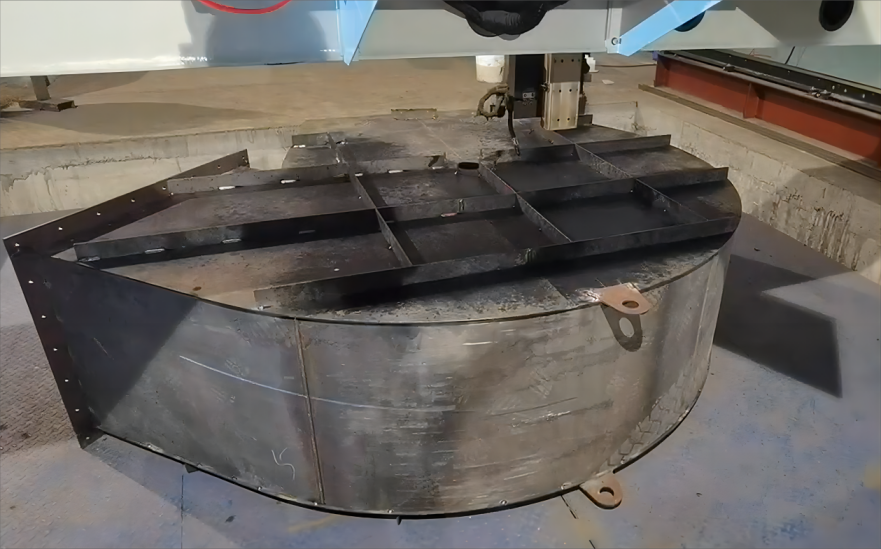
3.2 Benefits and Comparison
- High Accuracy:The spinning forming process enables ALTRON AUTO to deliver steel front disks with precise dimensions and tight tolerances, ensuring optimal performance and longevity.
- Material Savings:By minimizing material waste and maximizing resource utilization, spinning forming offers a sustainable solution for industrial fan manufacturing.
- Efficiency:Compared to traditional manufacturing methods, spinning forming allows for faster production cycles and shorter lead times, enabling ALTRON AUTO to meet the evolving needs of its customers.
3.3 Comparison with Other Methods
In contrast to conventional methods such as stamping or machining, spinning forming offers distinct advantages in terms of cost-effectiveness and design flexibility. By eliminating the need for multiple processing steps and reducing tooling costs, ALTRON AUTO streamlines the manufacturing process while maintaining the highest standards of quality and performance.
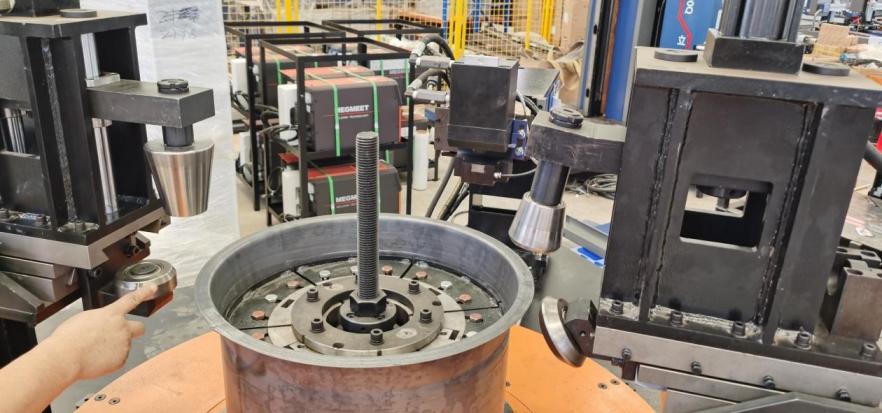
Innovative Solutions: Housing of Diagonal Fan
4.1 Utilizing Spinning and Crimping Techniques
ALTRON AUTO’s innovative approach to fan housing is exemplified in its utilization of spinning and crimping techniques for diagonal fans. By seamlessly integrating these processes, the company achieves superior structural integrity and performance in fan housing components.
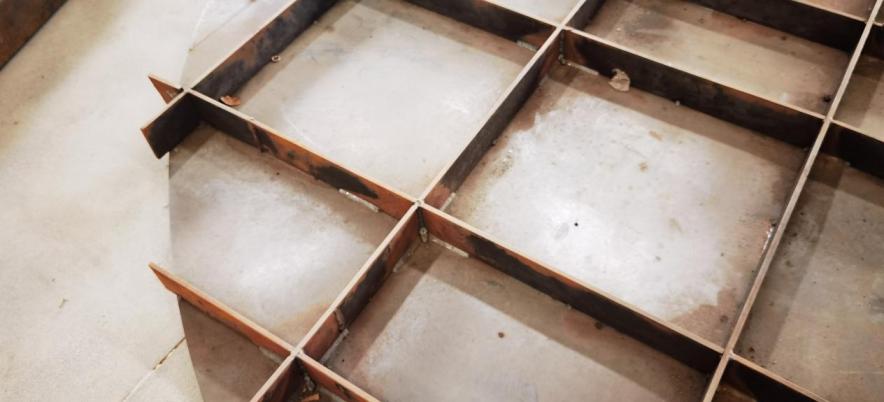
4.2 Advantages and Applications
- Seamless Construction:The combination of spinning and crimping techniques results in seamless fan housing with enhanced durability and reliability.
- Smooth Surface Finish:ALTRON AUTO’s advanced manufacturing processes ensure a smooth surface finish, minimizing airflow resistance and maximizing fan efficiency.
- Cost Savings:Through the optimization of production processes and material utilization, ALTRON AUTO delivers cost-effective solutions to its customers without compromising on quality or performance.
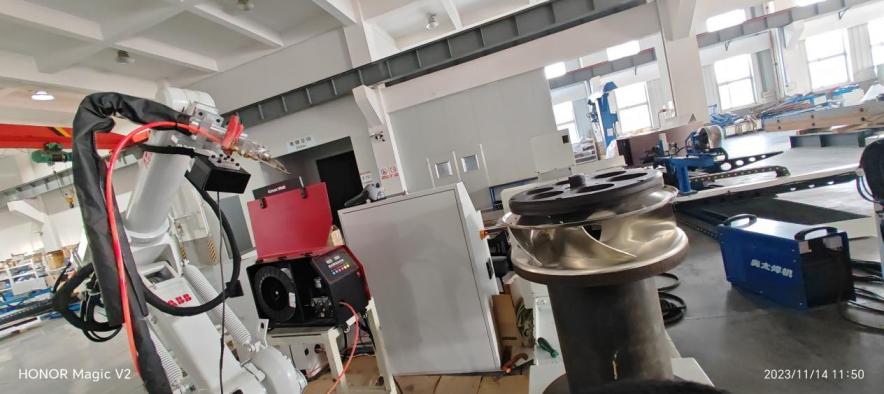
4.3 Application in Fan Performance
The housing of diagonal fans plays a crucial role in directing airflow and maximizing efficiency in industrial ventilation systems. By leveraging spinning and crimping techniques, ALTRON AUTO enhances fan performance, contributing to improved air quality and workplace comfort.
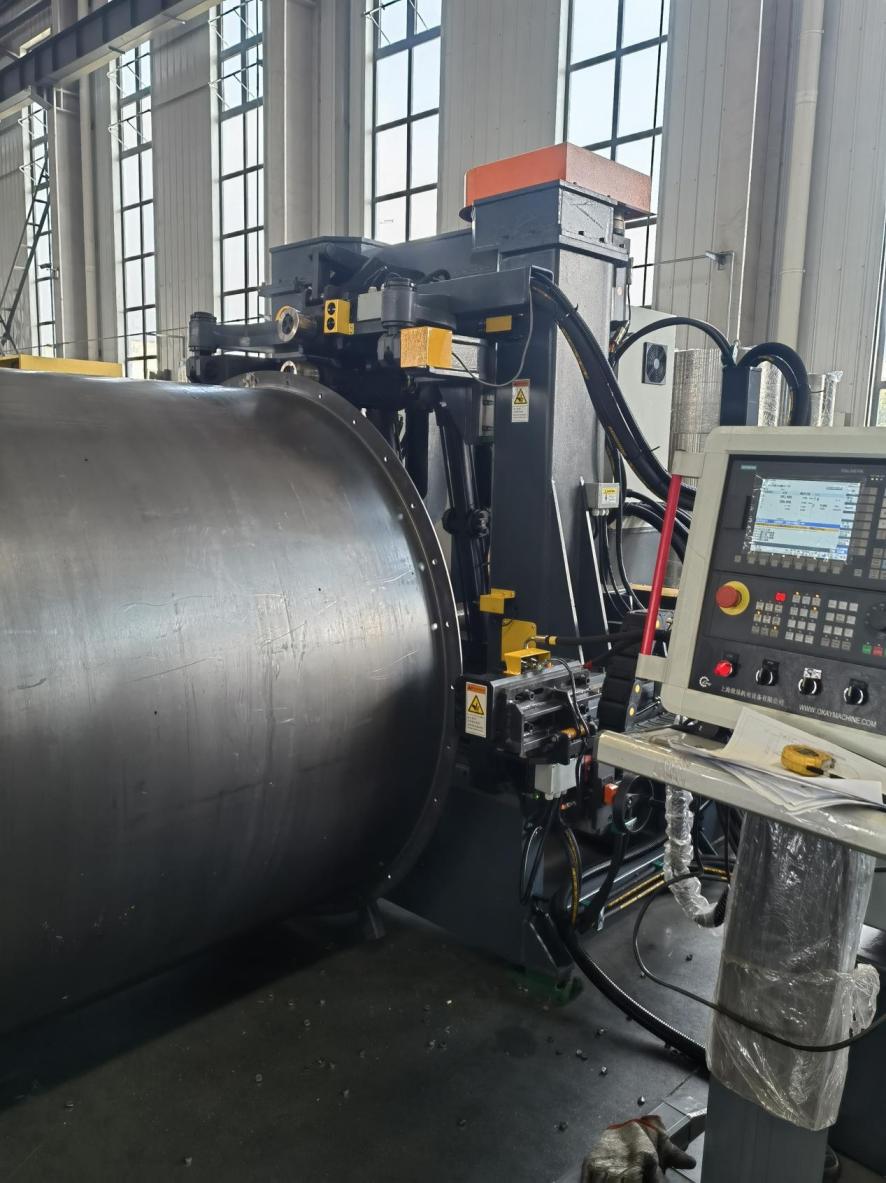
Optimizing Design with Spinning Forming: Axial Fan Duct
5.1 Application of Spinning Forming
ALTRON AUTO’s expertise in spinning forming extends to the manufacturing of axial fan ducts, where precision and design optimization are critical. By employing spinning forming techniques, the company achieves unparalleled accuracy and efficiency in duct production, ensuring seamless integration into industrial ventilation systems.
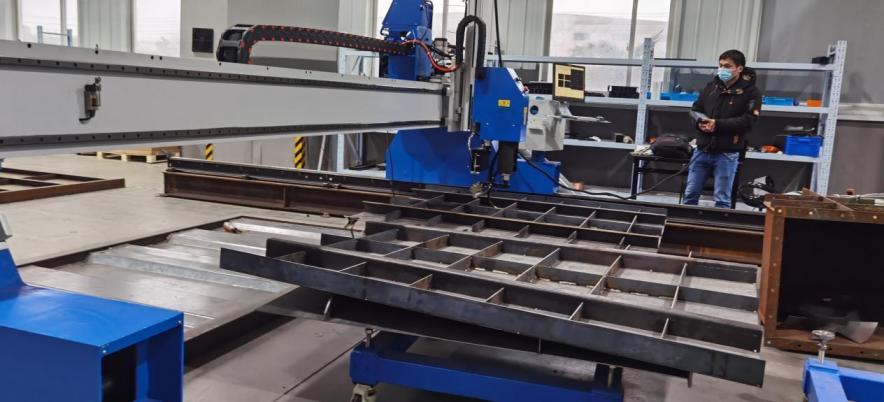
5.2 Advantages and Importance of Precision
- Smooth Surface Finish:Spinning forming yields axial fan ducts with impeccably smooth surfaces, minimizing airflow resistance and enhancing overall system efficiency.
- Material Efficiency: Through precise material utilization and minimal waste, spinning forming offers a sustainable solution for fan duct manufacturing, reducing costs and environmental impact.
- Precision and Accuracy:In duct design, precision is paramount. ALTRON AUTO’s spinning forming processes ensure dimensional accuracy and tight tolerances, guaranteeing optimal performance and airflow control.
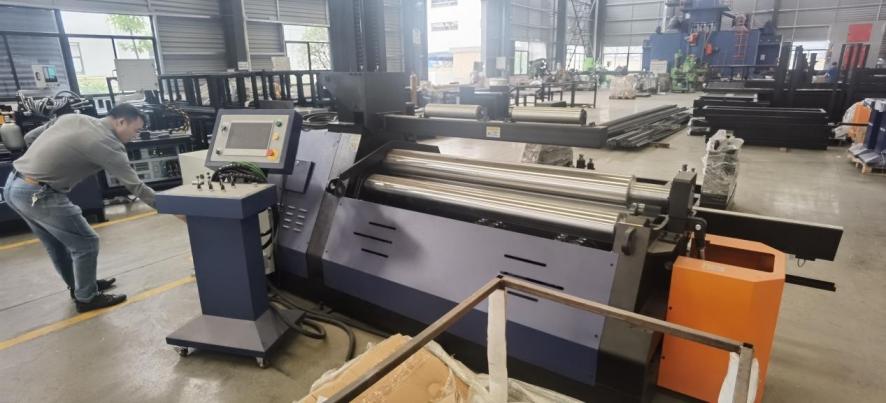
Efficiency through Spinning Forming: Steel Roof Fan Cap
6.1 Detailed Process and Advantages
ALTRON AUTO’s commitment to efficiency and quality is exemplified in the production of steel roof fan caps using spinning forming techniques. The meticulous process of shaping steel into fan caps results in components with superior surface finish, dimensional accuracy, and cost savings.
6.2 Discussion on Flange Variations
- Flange Variations: ALTRON AUTO offers a range of flange variations for steel roof fan caps, each tailored to specific application requirements. Whether it’s straight flanges or arc flanges, the company ensures optimal airflow management and structural integrity.
- Benefits:The utilization of spinning forming for fan caps not only ensures seamless construction and smooth surfaces but also offers significant cost savings compared to traditional manufacturing methods.
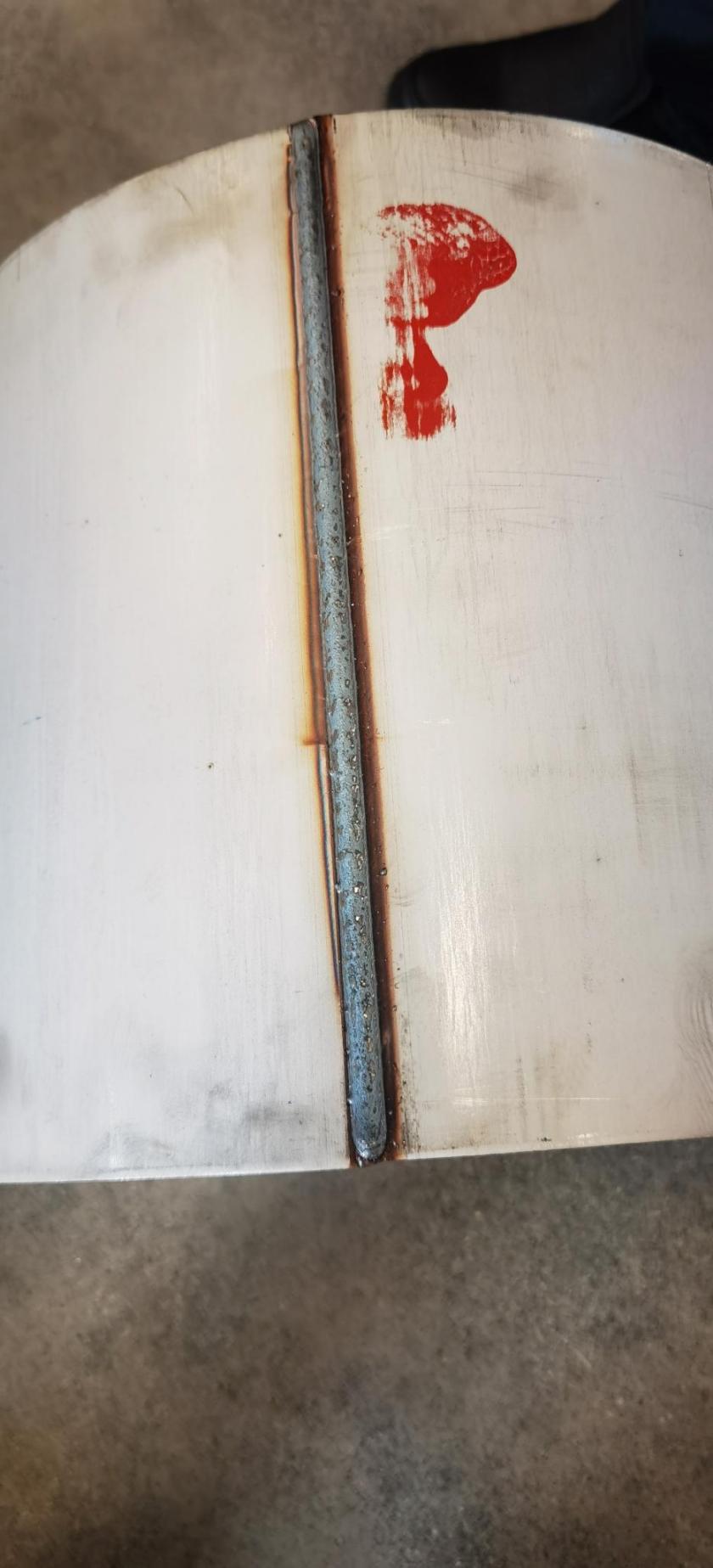
Advanced Techniques for Fan Components
7.1 Diameter and Thickness Considerations
ALTRON AUTO’s adoption of advanced techniques such as spinning, flanging, and punching revolutionizes the production of fan components. By leveraging these processes, the company achieves versatility, mold-free production, and precise shape control, particularly in large fan manufacturing.
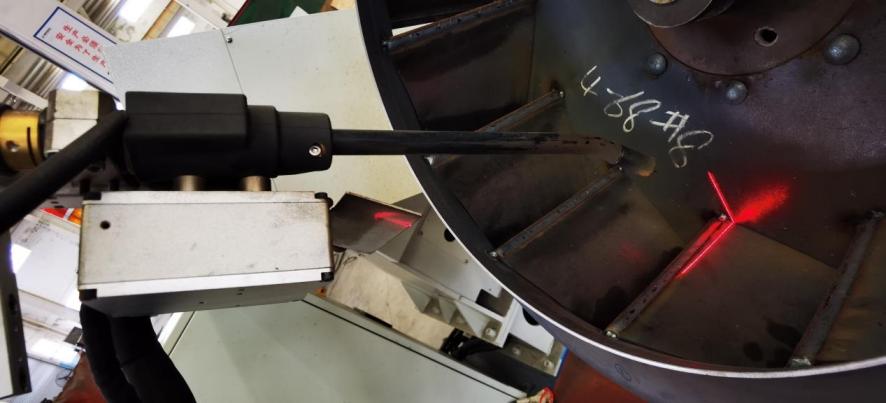
7.2 Advantages and Applications
- Versatility:The combination of spinning, flanging, and punching techniques allows for the production of a diverse range of fan components with varying diameters and thicknesses, catering to specific industrial requirements.
- Mold-Free Production:Unlike conventional methods that rely on molds, ALTRON AUTO’s advanced techniques offer flexibility and cost-effectiveness, eliminating the need for expensive tooling and reducing lead times.
- Shape Control: With precise control over shaping and forming processes, ALTRON AUTO ensures consistency and quality in every fan component, meeting the highest industry standards and customer expectations.
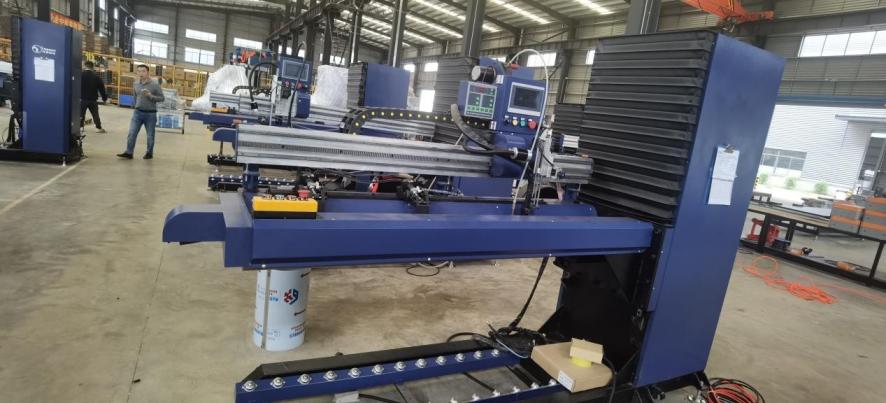
Tailored Solutions for Diverse Applications
8.1 Customization and Flexibility
ALTRON AUTO understands that every industrial ventilation system is unique, with specific requirements and challenges. That’s why the company offers tailored solutions that can be customized to meet the needs of diverse applications, from large-scale manufacturing plants to commercial facilities and beyond.
8.2 Comprehensive Product Range
From fan blades and housings to motor mounts and ductwork, ALTRON AUTO’s product range covers a wide spectrum of industrial fan components. Whether customers require standard off-the-shelf products or custom-designed solutions, ALTRON AUTO has the expertise and capabilities to deliver.
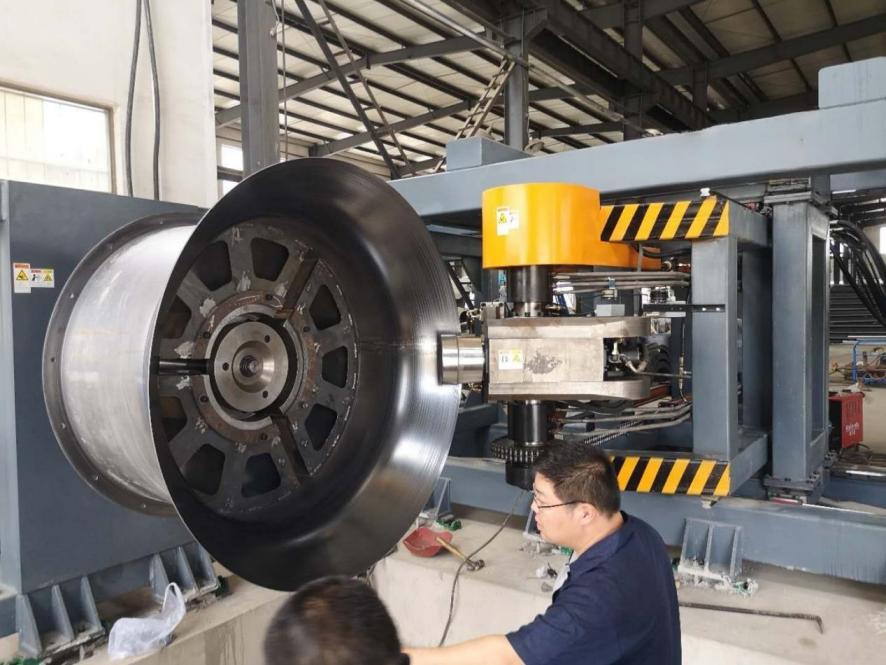
Continuous Innovation: Shaping the Future of Fan Manufacturing
9.1 Investment in Research and Development
ALTRON AUTO is committed to staying at the forefront of innovation in industrial fan manufacturing. The company invests heavily in research and development, constantly exploring new materials, processes, and technologies to push the boundaries of what’s possible.
9.2 Focus on Sustainability
In an increasingly environmentally conscious world, sustainability is a top priority for ALTRON AUTO. The company strives to minimize its environmental footprint through responsible manufacturing practices, waste reduction initiatives, and the use of eco-friendly materials.
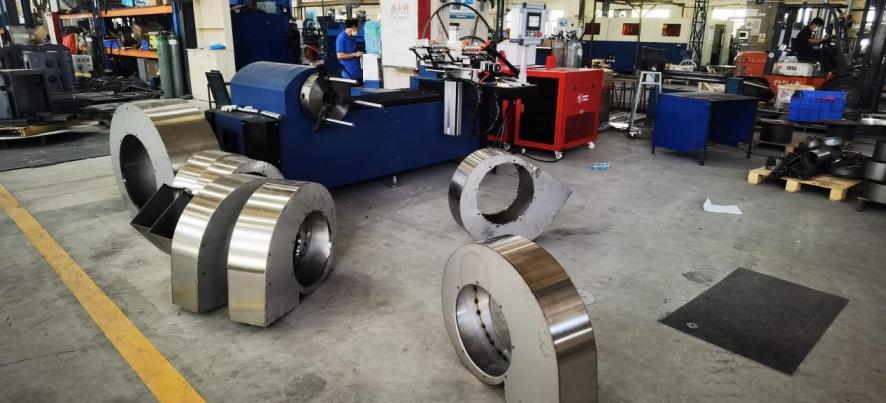
Future Directions in Industrial Fan Manufacturing
10.1 Potential Advancements and Integration
Looking ahead, ALTRON AUTO envisions significant advancements in spinning forming technology, driven by the integration of automation and software control. By embracing automation, the company aims to enhance production efficiency, reduce labor costs, and ensure consistent quality across all fan components.
10.2 Sustainability Considerations
As the industry evolves, sustainability considerations play an increasingly crucial role in fan manufacturing. ALTRON AUTO is committed to minimizing environmental impact through responsible resource management, waste reduction initiatives, and the adoption of eco-friendly manufacturing practices.
10.3 Meeting Future Challenges
While the future of industrial fan manufacturing holds immense promise, it also presents challenges such as evolving market demands, technological disruptions, and regulatory requirements. ALTRON AUTO remains poised to tackle these challenges head-on, leveraging its expertise, innovation, and commitment to excellence to drive industry growth and transformation.
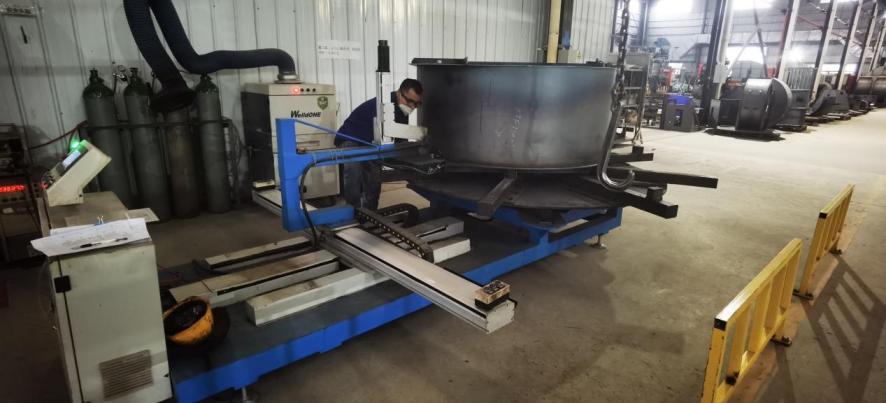
Conclusion
ALTRON AUTO’s innovative solutions in industrial fan manufacturing are revolutionizing the industry landscape. Through the utilization of spinning forming techniques, the company delivers high-quality, cost-effective components that meet the stringent demands of modern industrial applications. From steel air inlets to front disks and fan housings, ALTRON AUTO continues to drive advancements in fan technology, ensuring optimal performance, efficiency, and reliability for its customers.