CNC Inner Spinning Machine -Siemens System
Inner Spinning Machine For Air-Cooled Condenser
Machine Name |
Square Blank Inner Spinning Machine |
Model |
ACIN-1200 |
Application Industry |
wall-mounted axial fan, roof fans , kitchen fans, Box fans, HVAC Condenser Fan, Frame axial flow fan… |
Technical Service |
Complete the test in the early stage; provide online and offline training in the later stage, and complete the turnkey project. |
Technical Guidance |
Online 24 hours a day/Online Conference To Solve Pre-Sales Problems. |
Project Progress |
30-120 days |
Relevant Files |
ALTRON_AUTO Catalog-Industrial Blower Machinery Turnkey Project |
- ADAVANTAGES
- PARAMETERS
- CUSTOMER TESTIMONIALS
AC-IN-1200 Siemens Metal Inner Metal Spinning Machine is mainly used for forming, designing and manufacturing metal sheets such as condensers, refrigeration evaporators, axial flow fan guides, air conditioning cooling panels, etc.! This type of metal sheet metal shrouds has a common feature, the metal plate is square, and the position to be formed is round…
CNC Metal Inner Spinning Machine Video
Sheet Metal Panel For Air-Cooled Condenser

As shown in the picture, you can see the metal panels of the air-cooled condenser and refrigeration evaporator, with multiple fan heat dissipation outlets! Metal panels are generally made of galvanized sheet, carbon steel or aluminum! Altron improves the metal inner spinning machine for condenser manufacturers to reduce the cost of manufacturing rectangular round hole metal panels.
Inner Spinning Machine Processing Capacity
Inner Spinning Machine Processing Range
- C-Rectangular plate width: 1400mm
- A-Rectangular plate length: no limit
- Inner hole diameter: 300-1200mm
- B-Inner hole spinning depth: 200mm (determined by the ductility and thickness of the plate of different materials)
- Material thickness: 2.5mm Max
- Narrowest width of rectangular flange: 65mm (min)
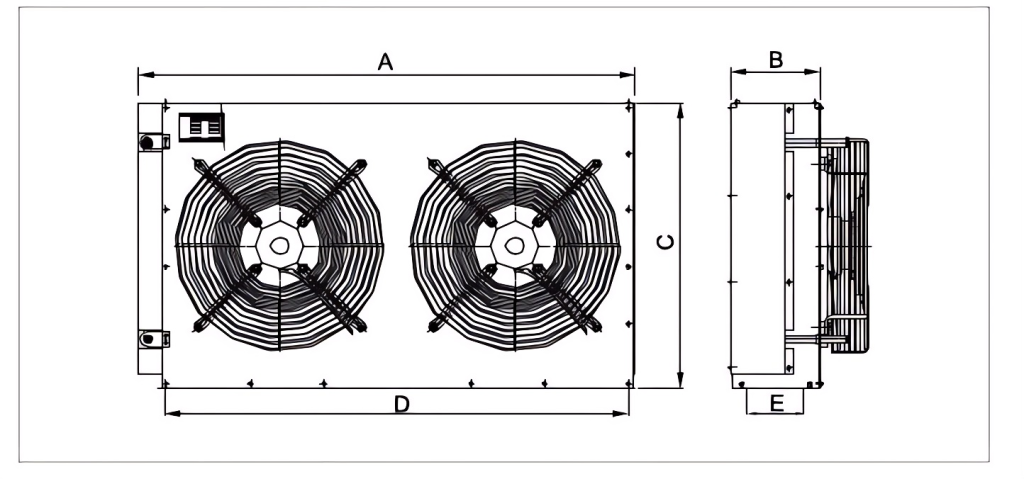
Altron’s AC-IN-1200 CNC double-wheel internal spinning machine is mainly used for precision spinning of refrigeration equipment external air outlets and air conditioning fan shields. It can easily perform flanging on square and rectangular plates, and easily realize the molding of multiple air outlets. Experience the efficiency and versatility of AC-IN-1200 in molding various components for refrigeration and air conditioning applications.
Inner Spinning VS Deep Drawing
The traditional manufacturing process uses large deep drawing molds, which are not only expensive, but also time-consuming and difficult to modify!
- Spinning molds account for 10% of deep drawing molds, and the mold investment cost is low!
- The size can be modified by modifying the CNC program!
- The product development cycle is completed in 5-14 days, which is much faster than the manufacturing cycle of deep drawing molds!
Machine Configuration Parameters
AC-IN-1200 CNC two-wheel internal spinning machine ALTRON
-
Marcley
★★★★★Post a review on Aug 21, 2022 From Bolivia
The AC-IN-1200 CNC Two-Wheel Inner Spinning Machine has revolutionized our production process. It has enabled us to effortlessly shape the tuyeres and protective covers for our refrigeration equipment and air conditioner fans with exceptional precision and efficiency.
-
Arthur Zonneveld
★★★★★Post a review on Fec 21, 2022 From Mauritius
We are extremely satisfied with the performance of the AC-IN-1200 machine. Its ability to carry out flanging forming on square and rectangular boards has streamlined our production of air outlets, saving us time and effort
-
Nicolas Vazquez
★★★★★Post a review on jul 21, 2022 From Uruguay
The AC-IN-1200 has exceeded our expectations in terms of reliability and quality. Its user-friendly interface and advanced CNC system have made the spinning process of our tuyeres and protective covers seamless and highly accurate.
-
OSCAR URBANEJA
★★★★★Post a review on Oct 10, 2022 From Venezuela
Thanks to the AC-IN-1200, we have achieved remarkable productivity and consistency in shaping various components for our refrigeration and air conditioning units. It has become an essential asset in our manufacturing process