Customized 5-Axis Rolling Machines For Axial Flow Fans
CNC rolling machines for fans-Machine Advantage
- √Digital control
- √Siemens PLC
- √5-axis fully hydraulic drive axial fans rolling machines
- √Self-lubricating system
- √Tip-over mechanism
- √Unloading device
- √Easy operation ;Stable performance, high efficiencys
- √Capable of supporting Axial Flow Fans duct Production Line
Main Rolling Machines For Industrial Fans:
CNC Spinning Machine, CNC Flanging Machine, Automatic Rolling Machine, Automatic Seam Welding Machine, Impeller Robot Welding Machine, Centrifugal Fan Housing Welding Machine, Air Duct Production Line …
Altron provides technical services and customized machine solutions for industrial fan manufacturers; it can provide turnkey solution services for axial flow fans, centrifugal fans, mixed flow fans metal forming, automated welding and rolling machines.
illustration of Rolling Machine
Large Custom Rolling Machine And Seam Welding Machine Video
Altron can customize drum rolling machines and wind welding machines of different heights according to the actual requirements of rolling!
Especially in the industrial fan industry! We provide different welding machines and processes for different materials such as stainless steel, carbon steel, aluminum, etc.!
Rolling Machine Overview of the subject
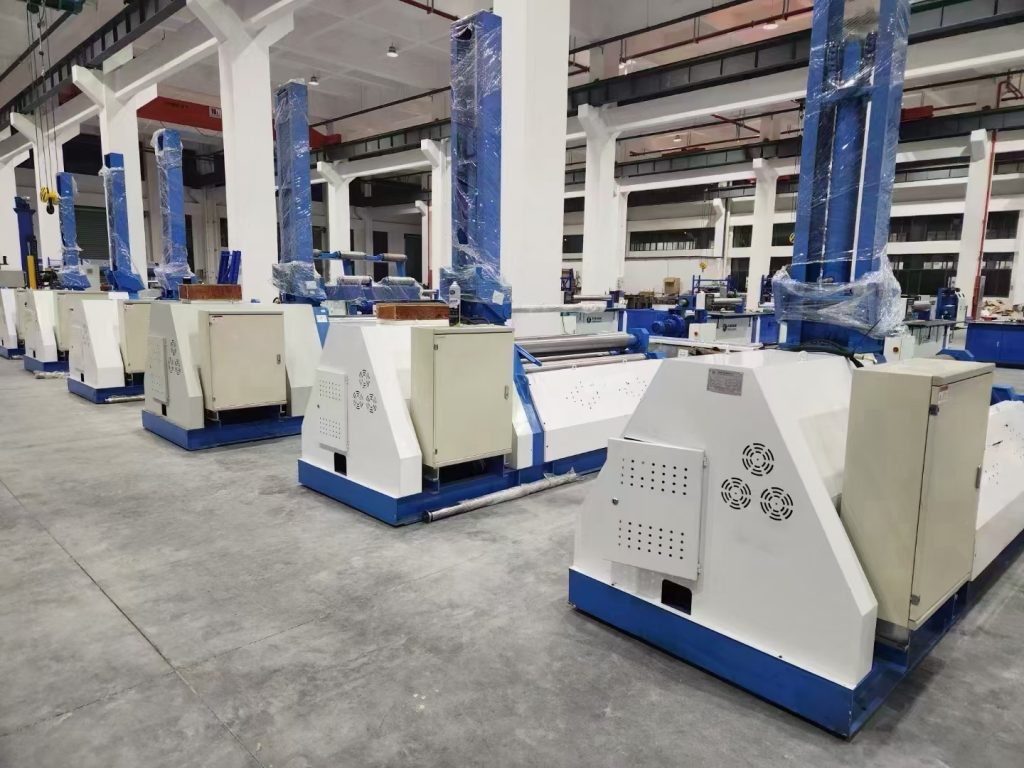
1-1. Main body overview
Rolling machine has digital control, five axes, and full hydraulic drive. The whole machine has an advanced structure, superior performance, and high efficiency. Altron’s CNC plate rolling machine
1.2 Features:
- The side roller moves linearly to increase working stability. The following users are suitable for using this CNC plate rolling machine.
- Absolute encoders are used on both sides of the pressure roller to control synchronization.
1-3 Rolling Machine Advantage:
- First-time users of the plate rolling machine because it is an easy-to-operate plate rolling machine
- Lack of operator inspection requires higher productivity
- Requires high precision and improved quality
- Hopes there will be only one or two operators, Reduce labor costs
- Due to the large size of the board, high production volume or safety reasons, feeding devices, material receiving devices, etc. are required.
1-4 Rolling machine features
1. Fully hydraulic drive, high efficiency and energy saving (the driving power is equivalent to about 55% of the traditional one), and the rolling work is faster than that of three-roller and other types of rolls.Triggers are relatively safe and reliable.
2. Permanent lubrication technology (no need to refuel during bearing life)
3. It can roll a cylinder with a minimum diameter of about 1.25 times the diameter of the upper roller. When the end of the rolled plate is pre-bent, the length of the straight edge is longer than that of other types.The plate bending machine should be small.
4. The clamping pressure is adjustable and is not easy to slip. The clamping force between the upper and lower rollers on the plate can be adjusted for different thicknesses through the pressure regulating valve of the hydraulic station. The corresponding required pressure when rolling plate with different thickness and width.
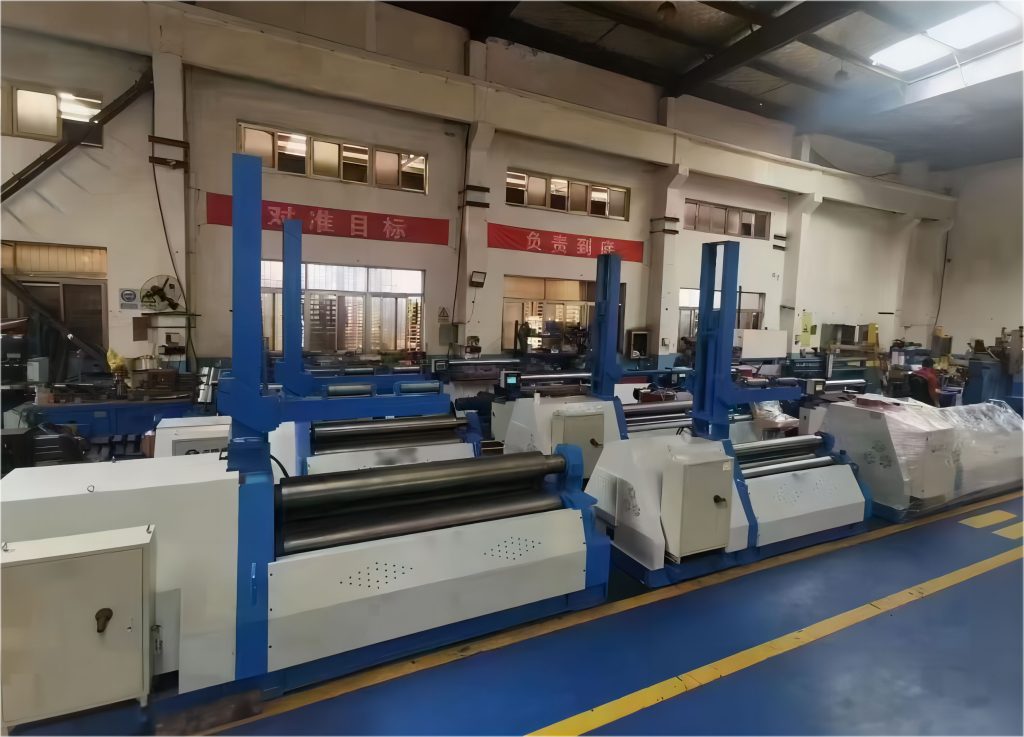
Working principle of rolling machine
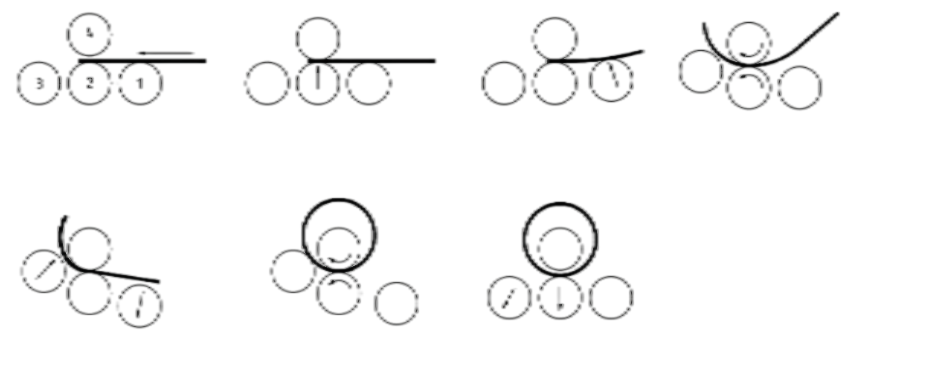
3.Main technical parameters
serial number | type | name | Specification |
1 | Specifications and models | JHJ-1508 CNC plate rolling machine | |
Roller length | Not shorter than 1500 mm | ||
Upper roller diameter | 190mm | ||
Lower roller diameter | 170mm | ||
Side roller diameter | 160 mm | ||
The minimum diameter that carbon steel can reach | 210mm | ||
The maximum diameter that can be reached | Extra large (note: extra large refers to a diameter of 4000mmabove) | ||
Roller material | Tested and tested heat-treated high-strength forged steel | ||
Roller heat treatment | HRC42-50 | ||
3 | drive | drive roller | upper roller |
Drive System | 1 independent hydraulic motor + planetary reduction directon coupling roller | ||
Maximum rolling speed | About 5m/min | ||
Circumferential compensation speed | Automatic hydraulic compensation system has almost no energy loss | ||
4 | Rolling requirements | Q235 carbon steel maximum rolled plate thickness | 8mm |
Maximum rolled plate thickness of 3 series stainless steel | 5.8mm | ||
Yield limit of plate | os≤245MPa | ||
Optimum remaining straight edge length | ≤1.5 times plate thickness | ||
Q235 maximum pre-bent plate thickness at full load | 6mm | ||
Maximum pre-bent plate thickness of 3 series stainless steel at full load | 4.8mm | ||
5 | electric | equipment power | About 4.5KW |
Factory power supply | 380 volts, 3 phase, 50 Hz | ||
6 | Roller deflectioncompensate | upper roller | Roller drum type compensates deflection |
Lower roller | none | ||
Side roller | none |
4.Introduction to the advantages of efficient rolling equipment
- The plate is fed horizontally – unlike three-roller and other types of plate rolling machines, which are fed at an angle.
- Use side rollers to quickly align the plate (r avoids the risk of misalignment)
- Only takes up space on the loading side
- The edge of the straight line segment is greatly reduced (due to the outstanding pre-bending ability, the clamping point falls on the edge of the plate)
- Equipment that is easy to roll. Each side roller only needs one position to roll into shape.
- The entire process is formed in one step (provided that the equipment capacity options are appropriate), including plate head pre-bending.
- Post-bending of plates is suitable for high-efficiency automatic roll manufacturing
Introduction to the advantages of efficient CNC rolling machine
5.Technical description of the basic structure of the equipment
Structure overview
The position of the upper roller of this machine is fixed, and the lower roller and side roller can move up and down. The rotation of the work roller is hydraulically driven. The lower roller and side roller are moved up and down by parallel oil cylinders at both ends. The flipping bracket at the discharge end of the upper roller can be flipped, Reset is performed by the oil cylinder. Each roller bearing body and oil cylinder are installed in the frame at the left and right ends.
Compared with the symmetrical three-roller plate rolling machine, this plate bending machine can directly pre-bend the end of the plate without the help of other equipment molds, and the remaining straight edge is smaller. Compared with the asymmetric three-roller plate bending machine, it can The plate is turned around and rolled into a work piece, which not only improves efficiency and ensures the quality of the work piece, but also has a simple process and is easy to operate.
This plate bending machine consists of work rollers (one upper roller, one lower roller, two side rollers), a frame (one high frame, one low frame, one piece of tipping support), a base, a hydraulic transmission device, a hydraulic The pumping station and main engine are composed of seven oil cylinders (four side roller moving cylinders, two lower roller lifting cylinders, and one head-turning cylinder), unloading device, solenoid valve group, and a CNC electronic control system.
Main drive (work roll rotation):
The driving roller drives the hydraulic transmission device (including planetary reducer, hydraulic motor, balance valve, etc.) through the hydraulic pump station to drive the work roller to rotate. The lower roller shaft end is equipped with a rotation encoding sensor, which can make the roller rotate accurately. Set the positioning, control the coiling arc length positioning, and fix the position of the upper roller
![]() ![]() |
![]() |
The lifting and lowering of the lower roller is driven by two oil cylinders to promote the lifting and lowering of the balance rod. The lifting and lowering of the rollers on both sides are controlled by two oil cylinders respectively. Each oil cylinder is monitored by a displacement sensor, and the two are synchronized.
The turning and resetting of the upper roller head are performed by the oil cylinder, making unloading more convenient.
rolling machine Main components
Work roll:
![]() |
![]() |
![]() |
The work roll is the main working part of the machine. The upper work roll is made of 42CrMo, a forging. It is tempered after rough machining and has a hardness of HB270~300.
The work roll processing process is:
forging→post-forging heat treatment→rough turning→quenching and tempering→finish turning→surface quenching treatment.
Frame:
There are one high and one short frame each. It is the main body of the plate rolling machine. It is made of steel plates welded and finely machined to remove the welding stress. The lower roller bearing lifting slide is processed in the middle of the frame. The two sides of the frame are equipped with There is a side roller bearing seat, and the side roller bearing seat and the side roller oil cylinder are integrated for lifting and moving. The frame, oil cylinder, work roller, etc. are installed on the overall welded base.
It adopts an overall welded structure and undergoes post-weld thermal aging annealing treatment to reduce internal stress. The frame is the main stress-bearing component of the machine. It is designed with sufficient strength and rigidity and is further strengthened according to the process characteristics to ensure the plate rolling needs. The welded structure frame is processed by CNC machine tools to ensure its accuracy.
Frame processing process: Steel plate shot blasting → CNC cutting and blanking → Bevel processing of each plate-shaped parts → Welding → Overall annealing →
CNC boring processing.
![]() |
![]() |
Schematic diagram of left and right racks
Unloading device:
It is installed on the transmission side of the upper roller and consists of a downward pull system. It is used to balance the upper roller during unloading.
Overturning mechanism:
It is installed on the side of the inverting head and is used for overturning and recovery of the inverting head. It is executed by the inverting head cylinder.
Channel steel base:
It is made by welding channel steel and steel plate and processing after removing the welding stress. The frame, cylinder and valve group are all installed on it to form a whole.
Hydraulic system:
It consists of hydraulic pump station, channel block, throttle valve, hydraulic control check valve, electromagnetic reversing valve, oil cylinder, hydraulic transmission device and pipeline.
The hydraulic system is fully provided by a professional manufacturer. The system and cylinder are designed with a rated pressure of 20Mpa or above, but the actual pressure used is below 18Mpa. In addition to the safety factor, there is a margin, and the use of high-quality sealing rings ensures that the hydraulic system can be guaranteed Oil leakage is rare in oil cylinders.
The hydraulic system consists of high-pressure pumps, valve groups, fluid connectors, hydraulic auxiliary parts, etc.
The system consists of three circuits: overpressure protection and pressure regulation circuit, synchronization circuit, and speed circuit.
The system design is reasonable and reliable, using quality-assured hydraulic components. The main hydraulic valves and hydraulic auxiliary parts are all high-quality brand products. The pipeline layout is reasonable, simple, beautiful, and easy to maintain and debug.
The entire hydraulic system rarely leaks under normal working conditions, and the lifting and lowering of the rollers on both sides and the lower roller have high synchronization accuracy
Microcontrol system
Structural composition
The electrical system uses a Siemens color touch screen display, a Siemens intelligent PLC and corresponding input, output and storage modules. This configuration has been proven in the long-term use by various users: it has the advantages of strong anti-interference ability, long service life, earthquake resistance, and stable operation.
The sensor uses a high-precision absolute displacement sensor to ensure position accuracy and monitor the position of each roller. There will be no data deviation even in the event of a power outage. The main components of the high-voltage part are all products from famous companies, and have the characteristics of long life and long trouble-free time.
Adopting an advanced and sophisticated EPS electronic balance system (as shown below), there is an EPS electronic balance system that performs synchronous movement through 3 sets of hydraulic cylinders. The Siemens PLC central controller ensures that the work rolls are perfectly parallel under any coil load. The minimum error of EPS trimming is approximately ±0.2mm.
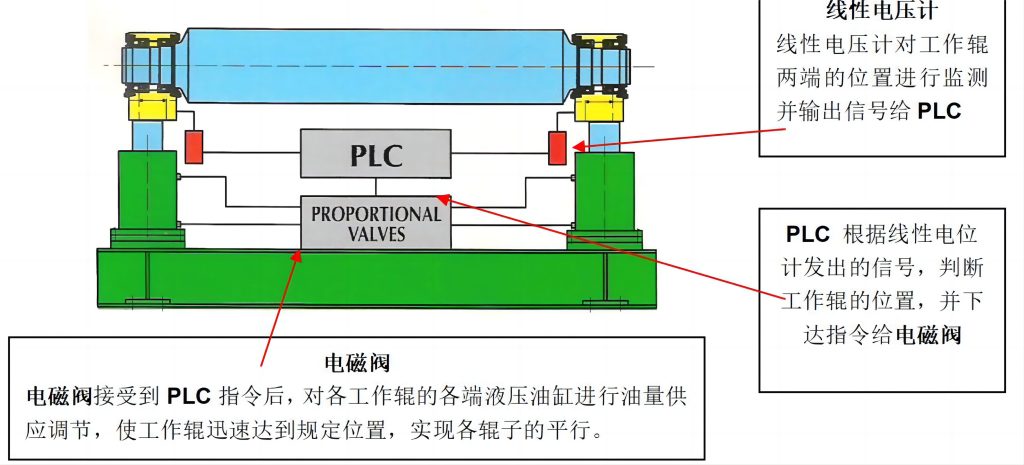
Control system functions
-
Automatically control the synchronous movement of work rolls
- Control the synchronous lifting and lowering of the lower roller, the best synchronization accuracy is ±0.2mm
- Control the synchronous lifting and lowering of the rollers on both sides, with the best synchronization accuracy of ±0.2mm
-
Display a variety of real-time data and rolling plate information
- The absolute position of both ends of the lower roller is displayed in real time
- The absolute position of both ends of the side roller is displayed in real time
- The inclination amount of both ends of the lower roller is displayed in real time
Real-time display of the tilt amount at both ends of the side roller
- The control system provides alarm information to facilitate operation and maintenance.
Rolling Machine Each action of the machine tool
Rolling Machine Automatic operation
Automatic selection
Open the right roller material setting parameters (such as the left roller material setting and open the left roller material setting parameters)
Rolling Machine Machine lubrication
Reasonable lubrication of various transmission parts and sliding surfaces of the machine is an effective measure to reduce power consumption and extend the life of the machine. Therefore, it is necessary to select reasonable lubricating grease and establish a necessary lubrication system.
Lubrication method
- According to the working conditions of the machine, box lubrication and regular refueling lubrication are adopted.
- Wafangdian self-aligning roller bearings are used at the neck positions of the upper roller, lower roller and side roller. Apply sufficient grease during assembly and large and medium repairs. No need to add grease during normal operation. Each sliding guide surface is regularly lubricated with oil cups.
Selection of lubricating oil
For the self-aligning roller bearings of each roller, it is recommended to use M0S2 lithium grease No. 1. If other types of grease are used instead, grease with a dropping point of not less than 160 degrees and a penetration in the range of 325~360 must be used.
Lubrication system and precautions
- Before each shift, oil should be added to each lubrication point, and the lubricating oil in the reduction box should be checked to see if it is at the specified oil level.
- It is recommended that the machine lubrication system be cleaned at least once a year.
- If the machine is at continuous full load for a long time, it should be cleaned once every six months.
Main standard parts configuration
name | content | ||
Bearing | type | Heavy duty roller double row self-aligning bearings | |
Manufacturer | Wafangdian Bearing Factory | ||
Work roll | Upper work roll material | Secondary flaw detection, 42CrMo | |
hardness | HB260-300/HRC42-50 | ||
Manufacturer | Jiangsu Huaxiang Special Steel, Nanjing Steel | ||
Chassis and side frames | Machined materials | Q235A | |
Processing methods | Welded structural parts, annealing treatment, CNC boring and milling machine processing | ||
Manufacturer | ALTRON | ||
hydraulic motor | Manufacturer | Zhejiang Just | |
electric motor | Type | Y type | |
Manufacturer | Jiangsu Tongde | ||
Hydraulic system | Hydraulic pump | Type | gear pump |
manufacturing plant | Hefei Hydraulic Parts Factory | ||
valve | manufacturing plant | Yuci YUKEN/Shanghai JINHAI | |
main cylinder | Cylinder and piston rod | 45 steel, quenched and tempered HB217-255. | |
Manufacturer | Jiangsu Op | ||
Main cylinder seal | UN type | ||
Manufacturer | Taiwan Dingji etc. | ||
Main electrical componentsCNC system | touchscreen | SIEMENSGermany Siemens | |
PLC programmable controller | SIEMENSGermany Siemens | ||
CNC calculation software | SIEMENSGermany Siemens |