2024 Precision Crafting: Production Solutions For Industrial Axial Flow Fan Ducts
Industrial axial flow fan ducts play a crucial role in various industries where ventilation and air movement are essential. These ducts are designed to efficiently channel airflow generated by axial flow fans, directing it to specific areas or processes. The significance of these ducts lies in their ability to ensure proper ventilation, temperature control, and air quality within industrial settings, thus enhancing productivity and maintaining a safe working environment.
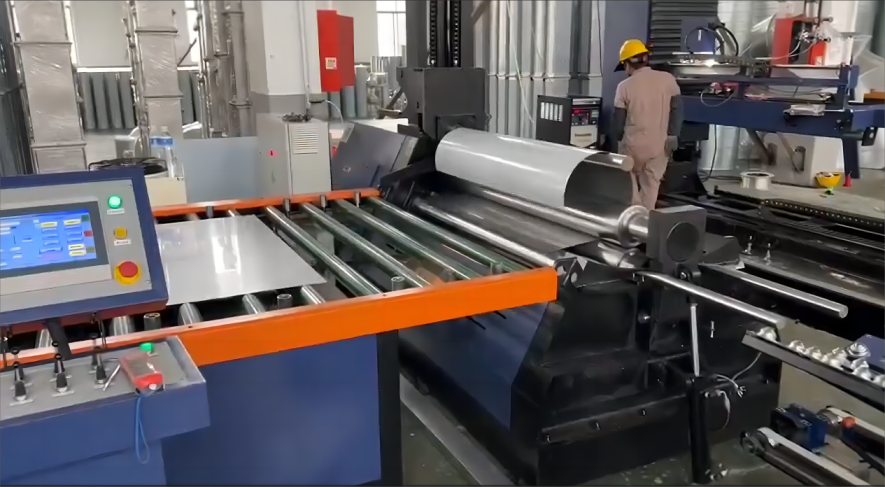
Introduction to Industrial Axial Flow Fan Ducts
1.1 Definition and Importance
Industrial axial flow fan ducts are specialized conduits that facilitate the movement of air in industrial environments. They are crucial components of ventilation and HVAC systems, serving to extract harmful fumes, regulate temperature, and maintain air circulation. Without these ducts, industrial facilities would face challenges in controlling air quality and temperature, which could adversely affect both worker health and equipment performance.
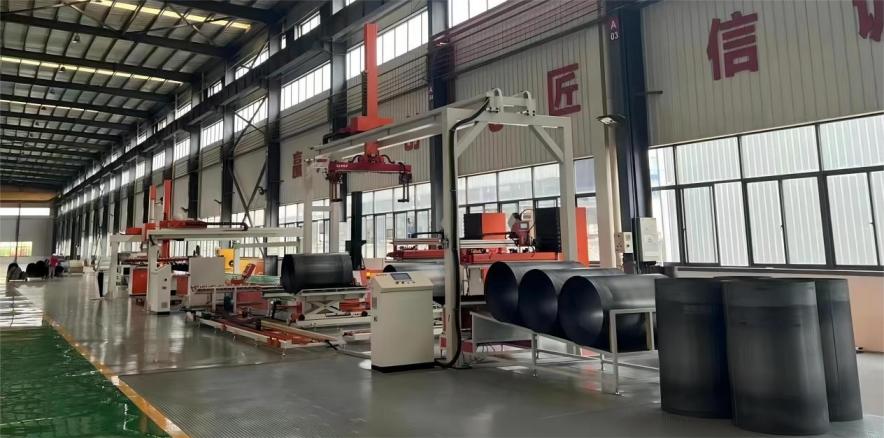
1.2 Applications Across Industries
The applications of industrial axial flow fan ducts are diverse and span across various industries such as manufacturing, chemical processing, power generation, and mining. In manufacturing plants, these ducts aid in removing heat generated by machinery and ensuring proper ventilation. In chemical processing facilities, they play a critical role in extracting toxic gases and maintaining a safe working environment. Additionally, axial flow fan ducts are integral to cooling systems in power generation plants and underground ventilation systems in mining operations.
Materials and Fabrication Techniques for Axial Flow Fan Ducts
2.1 Materials Used in Duct Fabrication
Industrial axial flow fan ducts are commonly fabricated using a range of materials, including metals such as stainless steel, aluminum, and galvanized steel, as well as plastics like PVC and fiberglass. Each material offers distinct properties such as corrosion resistance, durability, and cost-effectiveness, making it suitable for specific applications and environments.
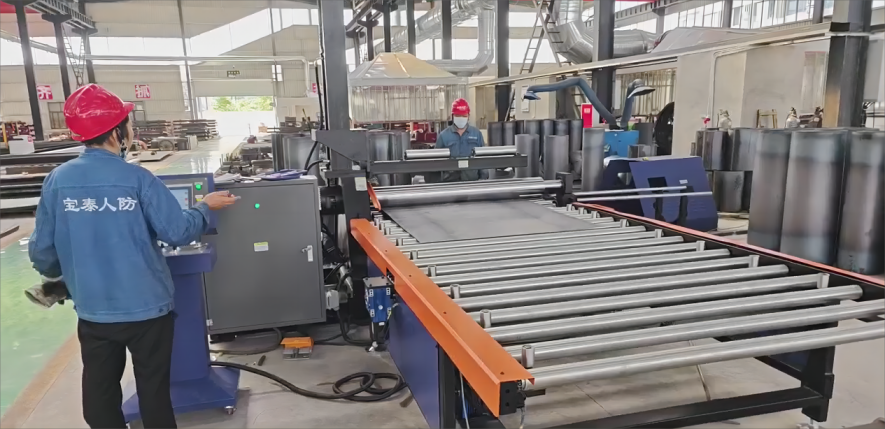
2.2 Fabrication Techniques
Several fabrication techniques are employed in the manufacturing of axial flow fan ducts, including welding, bending, and molding. Welding methods such as TIG (tungsten inert gas) and MIG (metal inert gas) are often used to join metal duct components, ensuring strength and airtight seals. Bending processes enable the shaping of ducts to conform to space constraints and airflow requirements. Additionally, molding techniques are utilized for plastic ducts, allowing for complex shapes and seamless construction.
2.3 Considerations for Selection
When selecting materials and fabrication techniques for axial flow fan ducts, various factors must be considered, including the operating environment, airflow characteristics, and budget constraints. For instance, in corrosive environments, stainless steel or fiberglass may be preferred for their resistance to chemical degradation. Similarly, the choice between welding and bending depends on factors such as duct size, shape complexity, and production volume.
Design Considerations for Optimal Performance
3.1 Factors Influencing Design
The design of axial flow fan ducts is influenced by factors such as airflow requirements, space constraints, and the specific application environment. Proper duct design is crucial for ensuring efficient airflow distribution, minimizing pressure losses, and optimizing fan performance. Factors such as duct size, shape, curvature, and the positioning of inlet and outlet openings are carefully considered to achieve optimal performance.
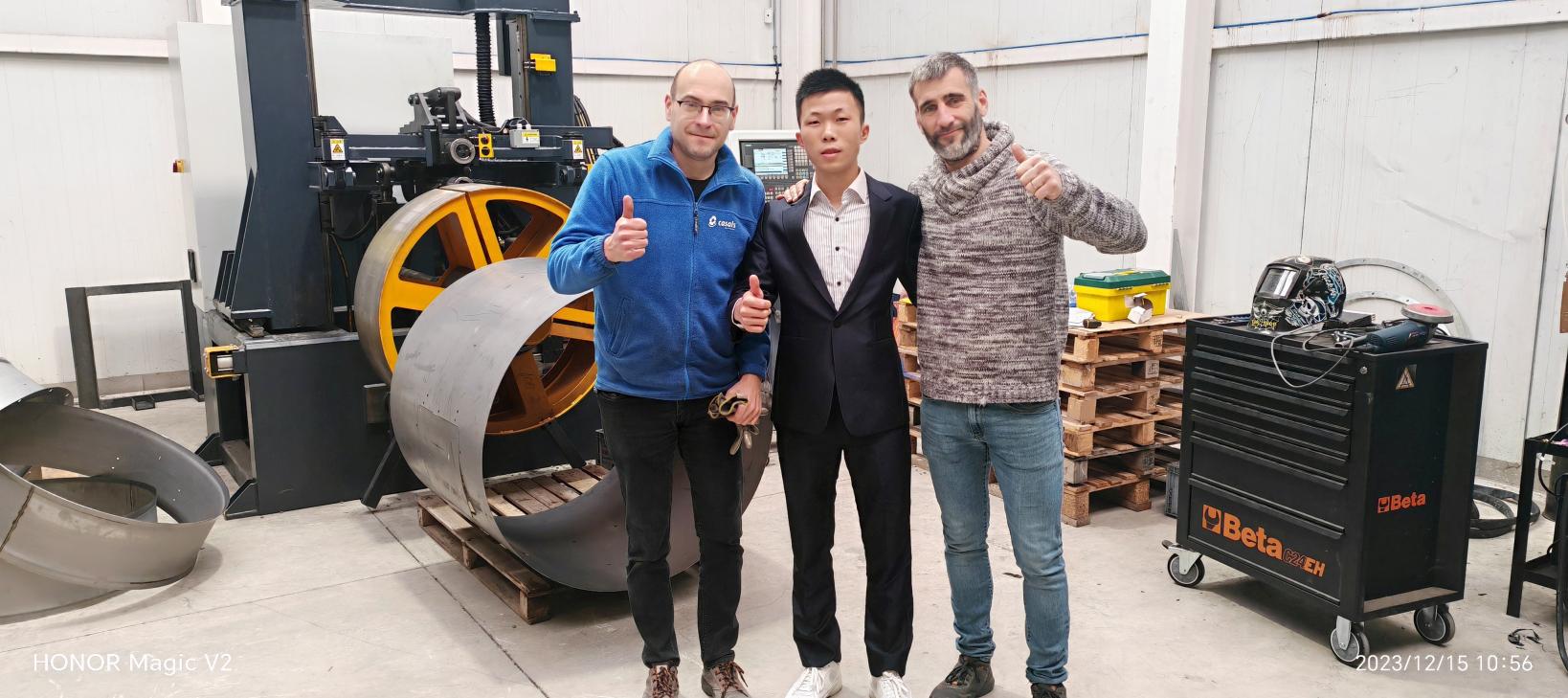
3.2 Aerodynamics and Fluid Dynamics
A thorough understanding of aerodynamics and fluid dynamics is essential in designing axial flow fan ducts for optimal performance. By applying principles such as Bernoulli’s equation and conservation of mass, engineers can predict airflow patterns, pressure gradients, and turbulence within duct systems. This knowledge enables the design of ducts with minimal resistance to airflow, reducing energy consumption and enhancing overall efficiency.
3.3 Optimization Strategies
To optimize the performance of axial flow fan ducts, various strategies can be employed, including streamlining duct geometry, reducing frictional losses, and minimizing turbulence. Computational fluid dynamics (CFD) simulations are often used to analyze airflow behavior and identify potential design improvements. Additionally, incorporating features such as smooth transitions, gradual bends, and flow straighteners can help mitigate airflow disturbances and enhance duct performance.
Automation in Duct Manufacturing
4.1 Role of Automation
Automation plays a significant role in improving efficiency and consistency in the manufacturing of axial flow fan ducts. By automating various production processes, manufacturers can achieve higher throughput, greater precision, and reduced labor costs. Automation also enables the integration of advanced technologies such as robotics, CNC machining, and laser cutting, further enhancing manufacturing capabilities.
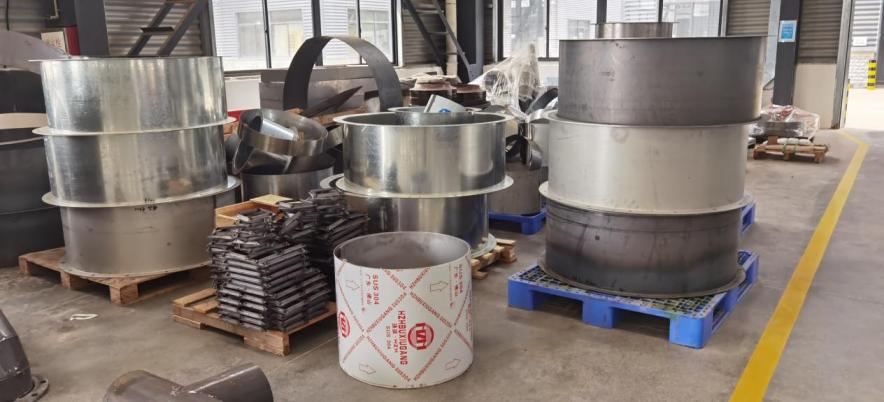
4.2 Automated Processes
In duct manufacturing, automated processes such as CNC machining, robotic welding, and laser cutting are commonly employed to streamline production workflows and ensure consistent quality. CNC machines enable precise fabrication of duct components from raw materials, while robotic welding systems ensure accurate and uniform welds, enhancing structural integrity. Laser cutting technology allows for fast and precise cutting of duct materials, minimizing material waste and production time.
4.3 Benefits of Automation
The implementation of automation in production lines for axial flow fan ducts offers numerous benefits, including increased productivity, improved product quality, and reduced lead times. Automation allows manufacturers to meet high demand while maintaining consistent quality standards, thus enhancing customer satisfaction and competitiveness in the market. Additionally, by reducing reliance on manual labor, automation helps mitigate labor shortages and minimize safety risks in manufacturing operations.
Quality Control and Testing in Duct Production
Quality control measures are paramount in ensuring the reliability and performance of industrial axial flow fan ducts. ALTRON, a leading manufacturer in duct production, prioritizes rigorous quality control procedures throughout the manufacturing process. These measures include comprehensive inspections, material testing, and adherence to strict quality standards. By maintaining stringent quality control, ALTRON ensures that each duct meets or exceeds performance requirements, providing customers with dependable solutions for their ventilation needs.
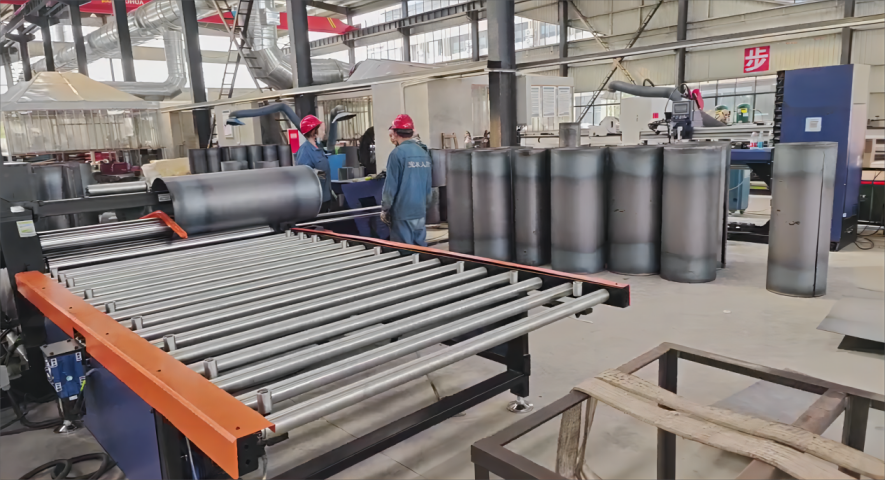
5.1 Importance of Quality Control
Quality control measures are essential for identifying and addressing any defects or inconsistencies in duct production. By implementing robust quality control protocols, manufacturers like ALTRON can minimize the risk of product failures, ensuring customer satisfaction and loyalty. Moreover, consistent quality control contributes to the longevity and reliability of ducts, reducing maintenance costs and downtime for end-users.
5.2 Testing Procedures
Testing procedures are integral to verifying the performance and durability of industrial axial flow fan ducts. ALTRON employs various testing methods, including pressure testing and airflow measurement, to assess duct integrity and functionality. Pressure testing involves subjecting ducts to controlled air pressure to detect leaks or weaknesses in the structure. Airflow measurement tests evaluate the duct’s ability to deliver the required airflow rate efficiently. These tests ensure that ALTRON’s ducts meet performance specifications and comply with industry standards.
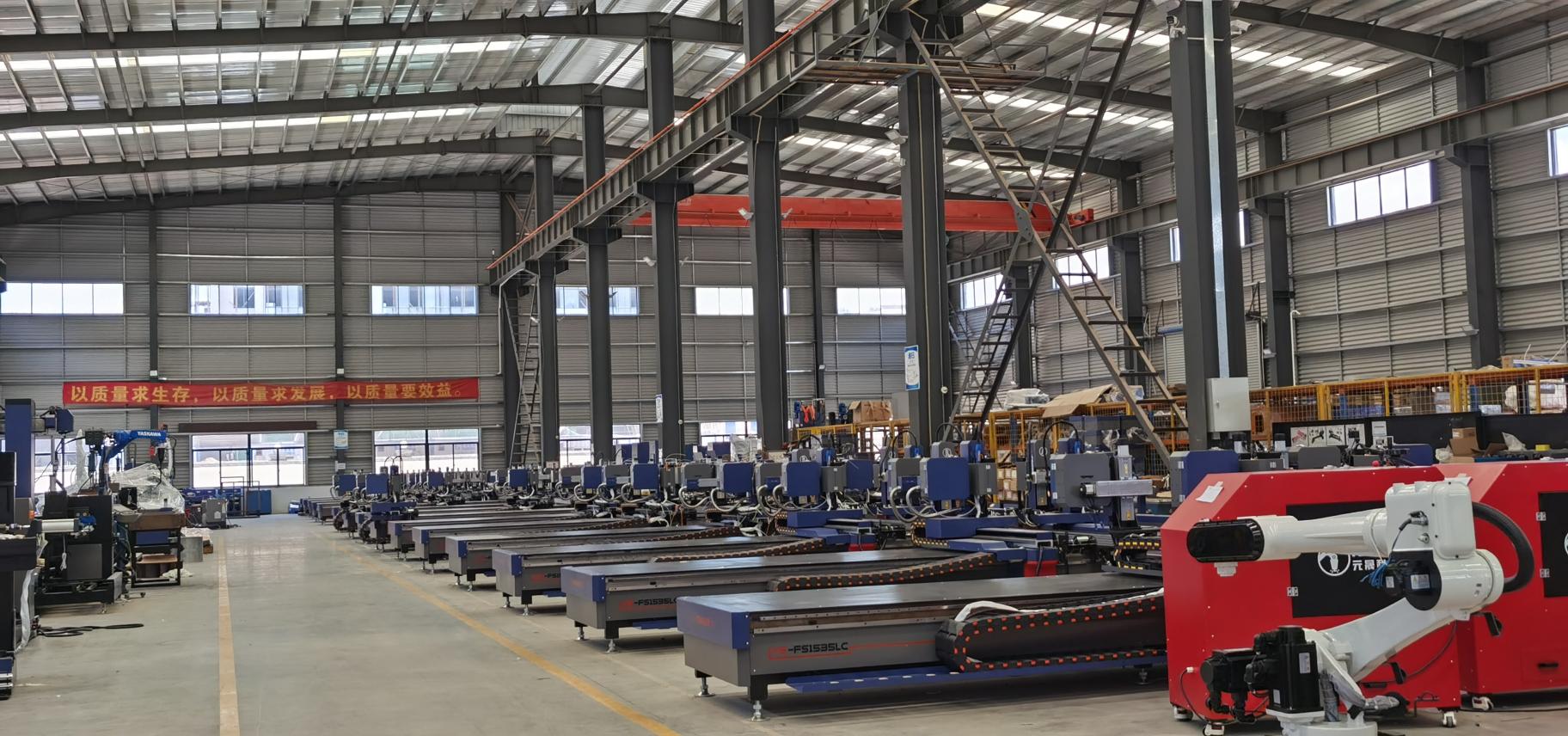
5.3 Strategies for Maintaining Quality Standards
To maintain high-quality standards throughout the production process, ALTRON utilizes advanced manufacturing technologies and employs skilled technicians with expertise in duct fabrication. Additionally, continuous training programs and regular equipment maintenance help optimize production workflows and minimize errors. By prioritizing quality at every stage of production, ALTRON delivers superior ducts that meet the most demanding requirements of its customers.
Environmental Considerations and Sustainability
Duct manufacturing processes can have a significant impact on the environment, including energy consumption, emissions, and waste generation. ALTRON recognizes the importance of minimizing its environmental footprint and is committed to implementing sustainable practices across its operations. Through initiatives such as recycling materials, optimizing energy usage, and reducing waste generation, ALTRON strives to mitigate its environmental impact while maintaining operational efficiency.
6.1 Reducing Environmental Footprint
ALTRON employs various strategies to reduce its environmental footprint in duct production. This includes utilizing recycled materials whenever possible, optimizing manufacturing processes to minimize energy consumption, and implementing waste management practices to reduce landfill waste. By prioritizing sustainability, ALTRON not only minimizes its environmental impact but also demonstrates its commitment to responsible business practices.
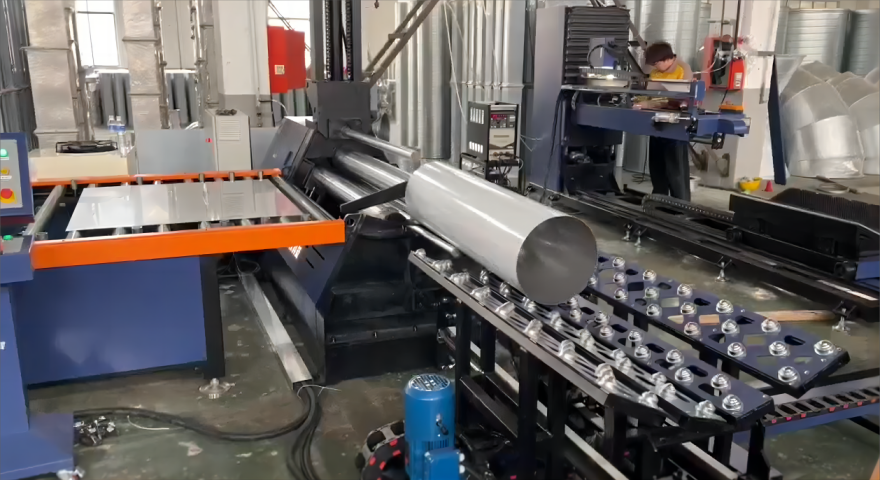
6.2 Importance of Sustainability
Sustainability is increasingly becoming a priority for both regulatory agencies and customers. By embracing sustainable practices, ALTRON not only complies with environmental regulations but also meets the expectations of environmentally conscious consumers. Furthermore, sustainability initiatives can enhance ALTRON’s reputation as a socially responsible company, attracting environmentally conscious customers and fostering long-term business relationships.
Customization and Specialized Solutions
As the demand for customized axial flow fan ducts continues to grow, ALTRON offers specialized solutions tailored to specific industries and applications. Whether it’s designing ducts for HVAC systems, aerospace applications, or specialized industrial processes, ALTRON leverages its expertise and capabilities to meet unique requirements.
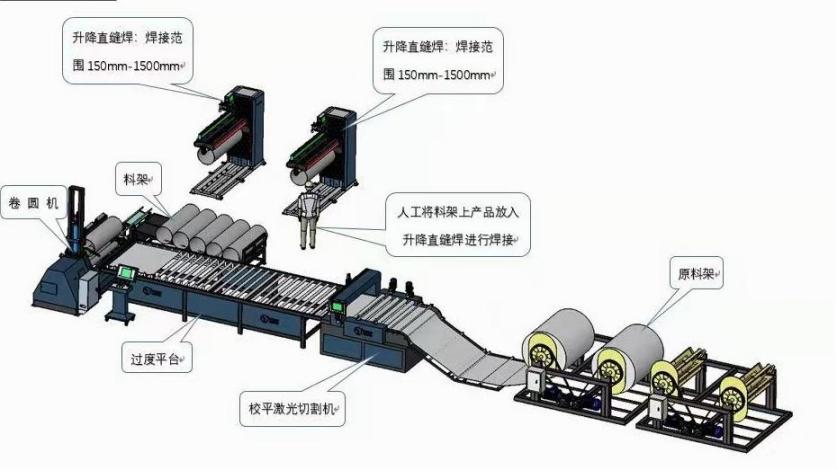
7.1 Growing Demand for Customization
The growing demand for customization reflects the diverse needs of industries requiring axial flow fan ducts. ALTRON recognizes this trend and offers a range of customization options, including size, shape, material selection, and performance specifications. By collaborating closely with customers and understanding their unique requirements, ALTRON delivers tailored solutions that address specific challenges and maximize efficiency.
7.2 Examples of Specialized Solutions
ALTRON provides specialized duct solutions for various industries, including HVAC, aerospace, automotive, and manufacturing. For HVAC applications, ALTRON offers ducts optimized for airflow distribution, noise reduction, and energy efficiency. In aerospace, ALTRON designs lightweight ducts capable of withstanding extreme temperatures and aerodynamic forces. Additionally, ALTRON develops ducts for specialized industrial processes such as chemical handling, food processing, and cleanroom environments.
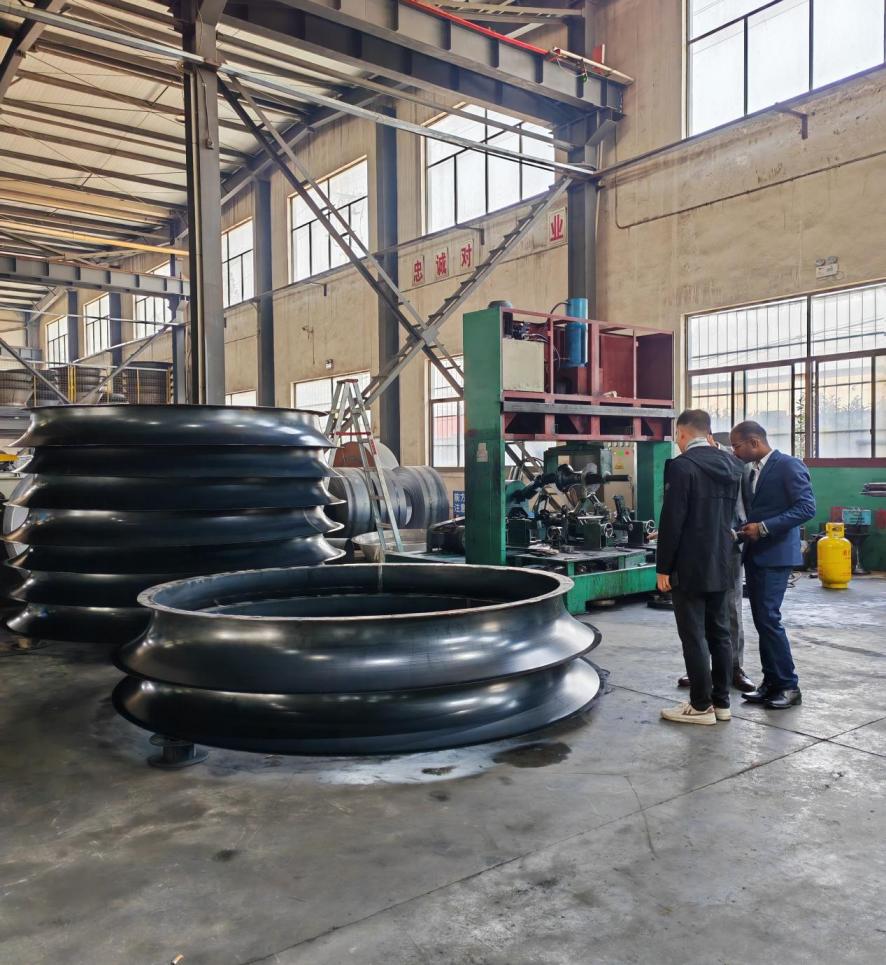
7.3 Considerations for Custom Duct Design
When designing custom ducts, ALTRON considers factors such as airflow requirements, space constraints, environmental conditions, and regulatory compliance. By leveraging advanced design software and simulation tools, ALTRON engineers can optimize duct performance and ensure seamless integration with existing systems. Moreover, ALTRON’s manufacturing expertise allows for precise fabrication and assembly of custom duct components, resulting in reliable solutions tailored to customer needs.
Future Trends and Innovations in Duct Production
ALTRON remains at the forefront of duct production by embracing emerging technologies and driving innovation in design and manufacturing processes. With a focus on continuous improvement and adaptation to market trends, ALTRON anticipates future challenges and opportunities in the duct manufacturing industry.
8.1 Emerging Technologies
Emerging technologies such as 3D printing, advanced materials, and automation are shaping the future of duct production. ALTRON explores the potential of additive manufacturing techniques to enhance design flexibility, reduce lead times, and optimize material usage. Additionally, ALTRON evaluates advanced materials such as composites and nanomaterials for their durability, lightweight properties, and resistance to corrosion.
8.2 Trends Driving Innovation
Several trends are driving innovation in duct design and production, including IoT integration, predictive maintenance, and digital twin technology. ALTRON explores the integration of IoT sensors and connectivity solutions to enable real-time monitoring of duct performance and condition. Predictive maintenance algorithms help optimize duct lifecycle management by predicting maintenance needs and preventing costly downtime. Furthermore, digital twin technology allows ALTRON to simulate and optimize duct performance in virtual environments, enabling rapid prototyping and design iterations.
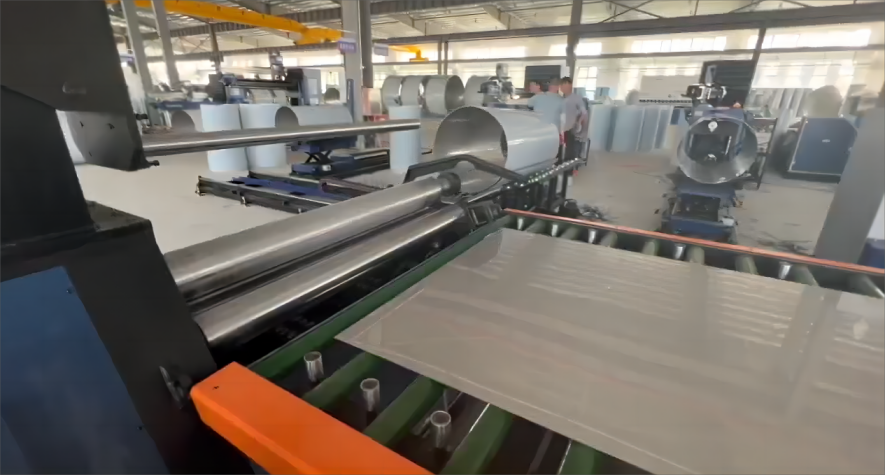
8.3 Opportunities and Challenges
As the duct manufacturing industry evolves, ALTRON faces both opportunities and challenges in adapting to changing market demands. Opportunities lie in the growing demand for customized solutions, advancements in technology, and expansion into new markets. However, challenges such as global supply chain disruptions, regulatory changes, and competitive pressures require ALTRON to remain agile and innovative in its approach. By embracing collaboration, innovation, and sustainability, ALTRON aims to maintain its position as a leader in industrial axial flow fan duct production.
Conclusion
In conclusion, the production of industrial axial flow fan ducts requires careful consideration of materials, fabrication techniques, design principles, and automation technologies. By leveraging the right combination of these factors, manufacturers can produce ducts that meet the stringent performance requirements of various industries while maximizing efficiency and reliability. ALTRON, a leading manufacturer in this field, continues to innovate and optimize production solutions for industrial axial flow fan ducts, ensuring superior performance and durability in demanding environments.