How are sheet metal CNC spinning machines transforming your industry?
Unlock the potential of CNC spinning technology and delve into the future of sheet metal fabrication. Gain valuable insights into materials, tooling, quality control, cost analysis, and upcoming trends. Discover how industry leaders like ALTRON AUTO are reshaping the landscape of metal manufacturing.
Introduction to CNC Spinning Machines
CNC spinning machines, a vital component in modern sheet metal fabrication, have revolutionized the manufacturing industry. These machines employ computer numerical control (CNC) technology to shape sheet metal into various forms with unparalleled precision and efficiency. Unlike traditional spinning methods that rely heavily on manual labor, CNC spinning machines automate the process, leading to higher productivity and consistency in the final products.
1.1 Significance in Sheet Metal Fabrication
The significance of CNC spinning machines lies in their ability to produce intricate shapes and complex geometries with ease. By utilizing programmed commands, these machines can execute precise movements and adjustments, resulting in finished parts that meet tight tolerances. This capability makes CNC spinning machines invaluable in industries such as aerospace, automotive, and architectural, where precision and quality are paramount.
1.2 How CNC Spinning Machines Work
CNC spinning machines operate by rotating a metal blank against a spinning mandrel while applying pressure using various tools. This process gradually shapes the metal into the desired form, whether it be a cone, cylinder, or other complex shapes. Unlike traditional spinning methods that require skilled craftsmen to manually manipulate the metal, CNC spinning machines follow pre-programmed instructions, ensuring consistency and repeatability in production.
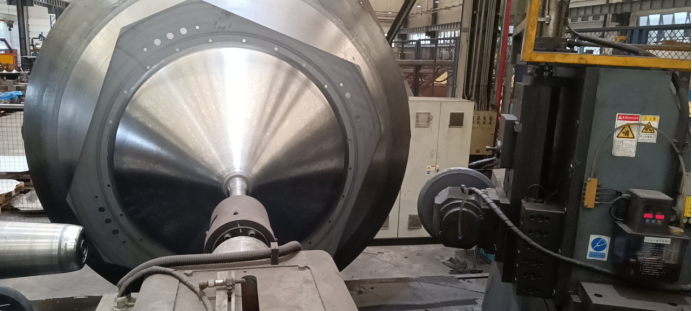
1.3 Benefits of Using CNC Spinning Machines
The benefits of utilizing CNC spinning machines are manifold. Firstly, they offer exceptional precision, allowing manufacturers to produce parts with minimal deviations from design specifications. Secondly, CNC spinning machines are incredibly fast, reducing production times compared to manual methods. Lastly, their ability to replicate shapes accurately ensures consistent quality across all produced parts, thereby minimizing waste and maximizing efficiency.
Advancements in Sheet Metal CNC Spinning Technology
Over the years, CNC spinning technology has undergone significant advancements, enhancing its efficiency and accuracy.
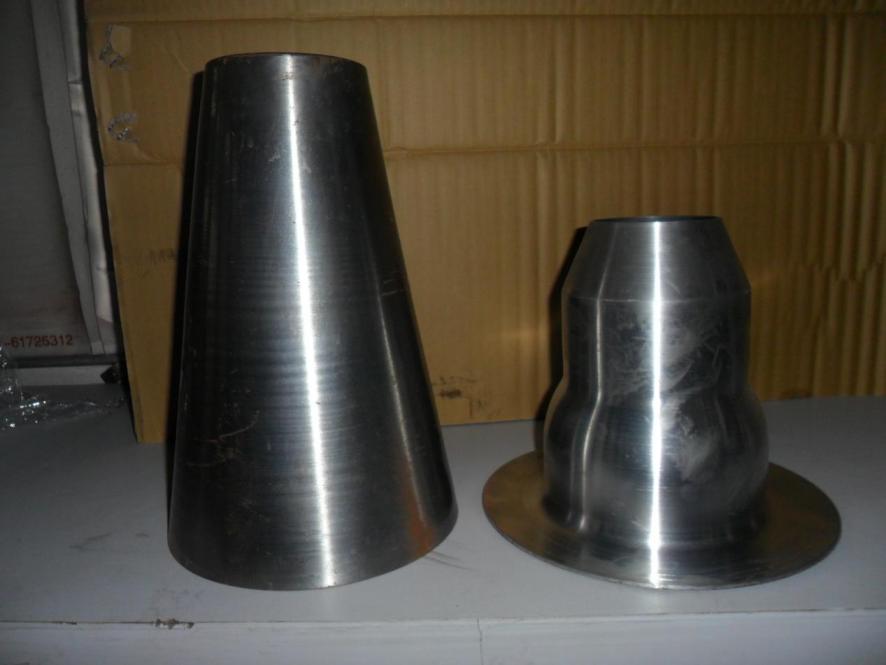
2.1 Evolution of CNC Spinning Technology
CNC spinning technology has evolved from rudimentary manual machines to highly sophisticated automated systems. Early CNC spinning machines were limited in their capabilities, but advancements in computer technology have enabled the development of more complex and versatile machines. Today, CNC spinning machines can handle a wide range of materials and geometries, making them indispensable in modern manufacturing.
2.2 Key Technological Advancements
Several key technological advancements have propelled CNC spinning technology forward. Improved spindle designs and motor controls have enhanced the precision and stability of spinning operations, resulting in higher quality finished products. Additionally, advancements in tooling materials and designs have extended tool life and reduced machining times, further increasing productivity.
2.3 Impact of Automation and Robotics
The integration of automation and robotics has had a profound impact on modern CNC spinning machines. Automated loading and unloading systems streamline production processes, reducing downtime and labor costs. Robotics also enable manufacturers to perform intricate tasks with greater speed and accuracy, expanding the capabilities of CNC spinning machines beyond traditional limits.
2.4 Software Integration
Software integration has played a crucial role in optimizing CNC spinning processes. CAD/CAM software allows designers to create complex part geometries and generate toolpath instructions with ease. Furthermore, real-time monitoring and control systems provide operators with valuable insights into machine performance, enabling them to make adjustments on the fly to optimize production efficiency.
Applications of CNC Spinning Machines in Sheet Metal Industry
CNC spinning machines find applications across various industries, owing to their versatility and efficiency.
3.1 Exploration of Various Industries
CNC spinning machines are widely used in industries such as aerospace, automotive, and architectural, where lightweight, durable components are required. In the aerospace industry, CNC spinning is used to manufacture engine components, airframe parts, and fuel tanks. In the automotive industry, it is used to produce exhaust systems, wheels, and body panels. In the architectural industry, it is used to create decorative elements, lighting fixtures, and signage.
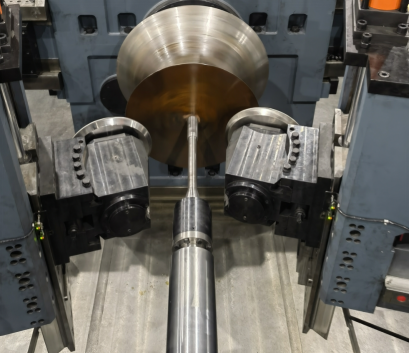
3.2 Examples of Products and Components
Examples of products and components manufactured using CNC spinning technology include cones, cylinders, hemispheres, and complex geometric shapes. These parts are used in a wide range of applications, including pressure vessels, storage tanks, lighting fixtures, and architectural elements.
3.3 Advantages in Specific Applications
The advantages of CNC spinning in specific applications are manifold. In aerospace applications, CNC spinning offers lightweight yet durable components that meet stringent performance requirements. In automotive applications, it enables the production of complex shapes with minimal material waste, leading to cost savings and improved fuel efficiency. In architectural applications, it allows designers to create custom-made components that enhance the aesthetics of buildings and structures.
Design Considerations for CNC Spun Parts
Designing parts for CNC spinning requires careful consideration of various factors to optimize the manufacturing process and ensure high-quality results.
4.1 Design Guidelines
Design guidelines for CNC spun parts include considerations such as wall thickness, material selection, and part geometry. Parts with uniform wall thickness are easier to spin and result in more consistent finished products. Additionally, selecting the appropriate material for the application is crucial to ensure the desired mechanical properties and surface finish.
4.2 Factors to Consider
Factors to consider in part design include the size and shape of the part, the complexity of the geometry, and the tolerances required. Complex geometries may require multiple passes or special tooling to achieve the desired shape accurately. Tolerances should be carefully defined to ensure that the finished part meets the specified requirements.
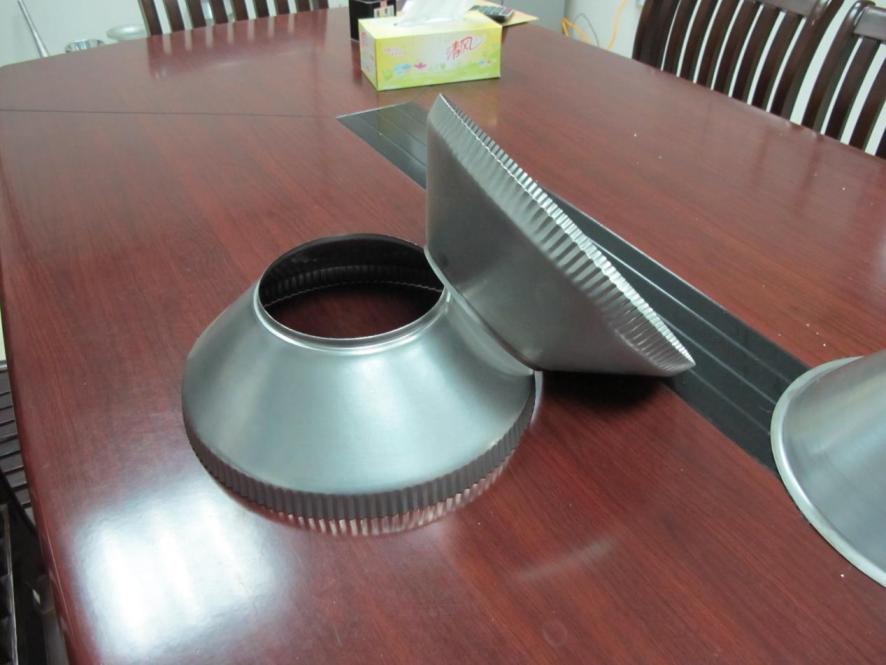
4.3 Case Studies
Case studies illustrating successful design implementations for CNC spun parts demonstrate how careful consideration of design factors can lead to optimized manufacturing processes and high-quality finished products. By examining real-world examples, designers can learn valuable lessons and apply them to their own projects.
Materials and Tooling in CNC Spinning
CNC spinning machines offer versatility in working with various materials, allowing manufacturers to produce a wide range of components with different properties.
5.1 Overview of Materials
Metals and alloys are the primary materials used in CNC spinning due to their malleability and durability. Common metals spun using CNC machines include aluminum, stainless steel, copper, and titanium. These materials offer excellent strength-to-weight ratios and corrosion resistance, making them suitable for diverse applications in industries such as aerospace, automotive, and electronics.
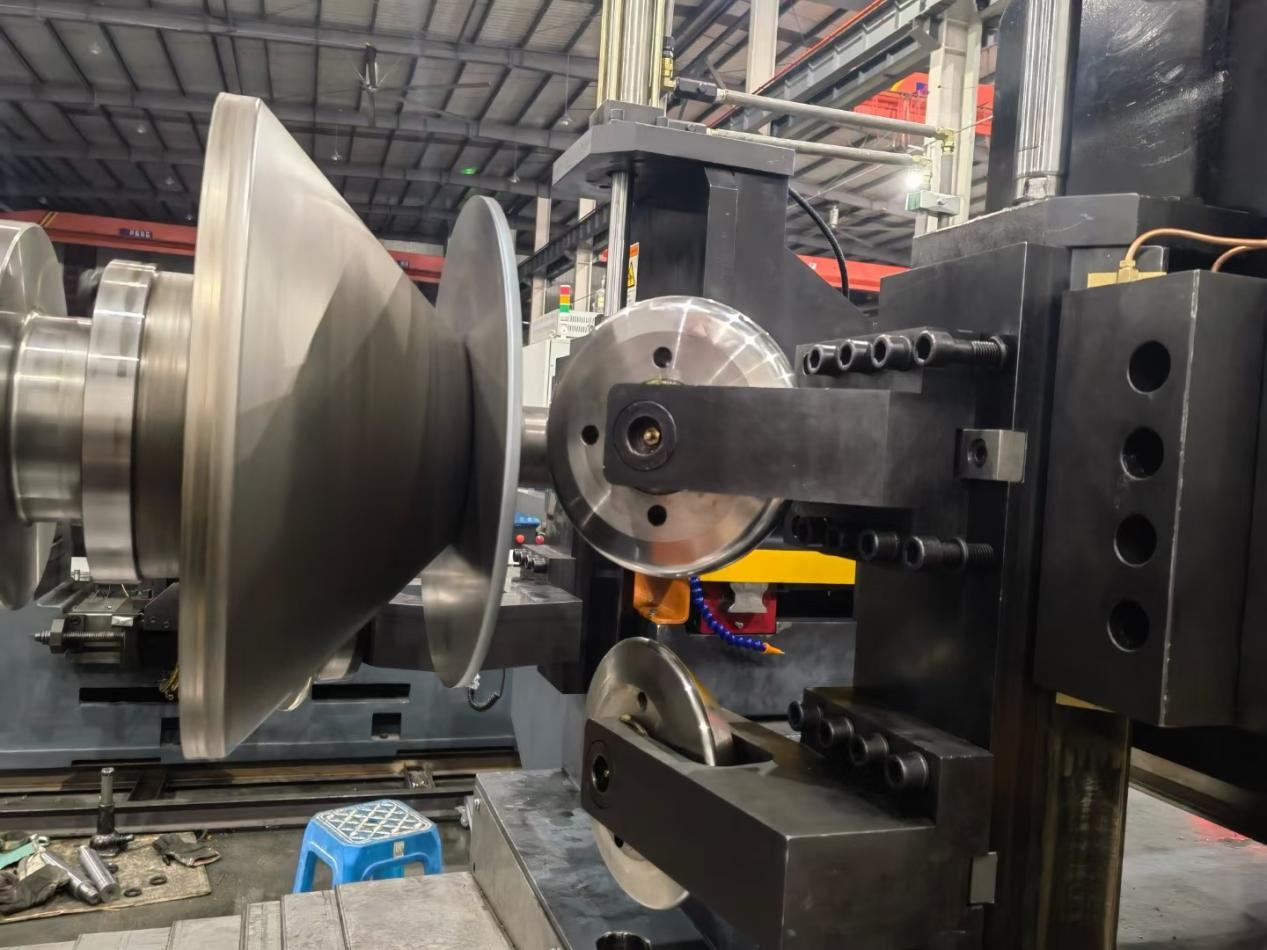
5.2 Tooling Requirements
Tooling requirements in CNC spinning include mandrels, rollers, and forming tools. Mandrels are used to support the workpiece during spinning, while rollers and forming tools shape the metal into the desired form. Tooling materials must be selected based on the properties of the workpiece material and the complexity of the part being produced. Carbide and high-speed steel are commonly used for tooling due to their durability and wear resistance.
5.3 Challenges and Solutions
One of the main challenges in CNC spinning is selecting the appropriate material for the desired part properties. Manufacturers must consider factors such as strength, ductility, and surface finish when choosing materials for CNC spinning. Additionally, tool wear and deformation can occur during spinning, affecting the quality and consistency of the finished parts. To mitigate these challenges, manufacturers employ techniques such as tool coatings, lubrication, and optimized process parameters to ensure smooth spinning operations and high-quality results.
Quality Control and Inspection in CNC Spinning
Quality control is essential in CNC spinning processes to ensure that finished parts meet the specified requirements and standards.
6.1 Importance of Quality Control
Quality control in CNC spinning helps identify and address any defects or deviations from the intended design early in the manufacturing process. By implementing rigorous quality control measures, manufacturers can minimize rework and scrap, reduce costs, and ensure customer satisfaction.
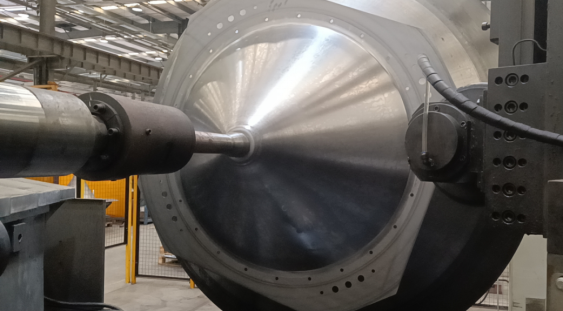
6.2 Methods and Techniques
Methods and techniques for inspecting CNC spun parts include dimensional measurement, surface roughness analysis, and visual inspection. Dimensional measurement ensures that parts meet the specified tolerances, while surface roughness analysis evaluates the quality of the surface finish. Visual inspection is also used to identify any visible defects such as cracks, scratches, or deformations.
6.3 Integration of Quality Control Measures
Integrating quality control measures into CNC spinning workflows requires careful planning and coordination. Manufacturers may implement automated inspection systems to streamline the inspection process and improve efficiency. Additionally, real-time monitoring and feedback systems allow operators to make immediate adjustments to spinning parameters to ensure consistent quality throughout the production process.
Cost Analysis and ROI of CNC Spinning Machines
Investing in CNC spinning technology requires careful consideration of the costs involved and the potential return on investment.
7.1 Evaluation of Cost-effectiveness
The cost-effectiveness of investing in CNC spinning technology depends on various factors, including initial capital investment, operating costs, and production volume. While CNC spinning machines typically have higher upfront costs compared to traditional spinning methods, they offer significant advantages in terms of productivity, quality, and versatility.
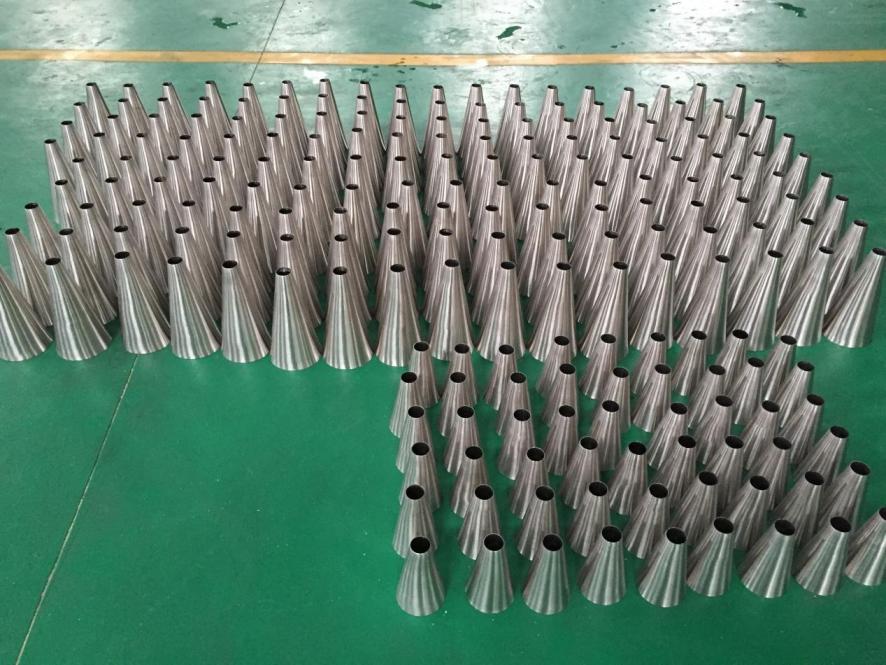
7.2 Factors Influencing Overall Cost
Factors influencing the overall cost of ownership for CNC spinning machines include machine maintenance, tooling costs, energy consumption, and labor expenses. Manufacturers must carefully evaluate these factors and develop strategies to optimize production efficiency and minimize costs.
7.3 Calculation of ROI
Calculating the return on investment (ROI) for CNC spinning equipment involves analyzing the potential cost savings and revenue generation opportunities associated with the technology. Manufacturers may consider factors such as increased production capacity, reduced scrap and rework, and improved product quality when calculating ROI. The payback period for CNC spinning equipment varies depending on the specific circumstances of each manufacturing operation.
Future Trends and Innovations in Sheet Metal CNC Spinning
The future of CNC spinning technology holds exciting possibilities, with advancements in additive manufacturing integration, materials utilization, and process optimization on the horizon.
8.1 Predictions for the Future
Future trends in CNC spinning technology are likely to focus on enhancing automation, increasing process efficiency, and expanding the capabilities of CNC spinning machines. Additive manufacturing integration, such as 3D printing of tooling and fixtures, may offer new opportunities for optimizing CNC spinning processes and reducing lead times.
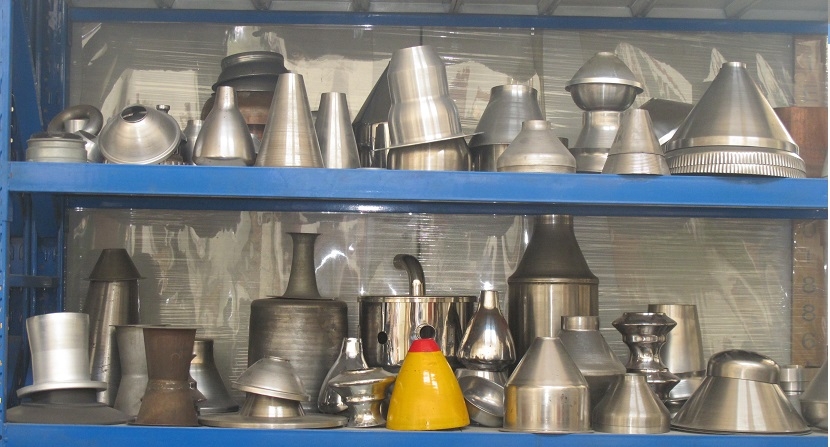
8.2 Emerging Trends
Emerging trends in CNC spinning include the use of advanced materials such as composites and lightweight alloys, which offer superior strength-to-weight ratios and enhanced performance characteristics. Additionally, advancements in machine learning and artificial intelligence may enable predictive maintenance and optimization of CNC spinning operations, further improving productivity and quality.
8.3 Potential Innovations
Potential innovations in CNC spinning include the development of smart sensors and monitoring systems for real-time process control and quality assurance. By incorporating data analytics and predictive modeling, manufacturers can identify potential defects or process deviations before they occur, minimizing downtime and optimizing production efficiency. Research areas such as nanotechnology and advanced surface treatments may also lead to new opportunities for improving the performance and functionality of CNC spun parts.
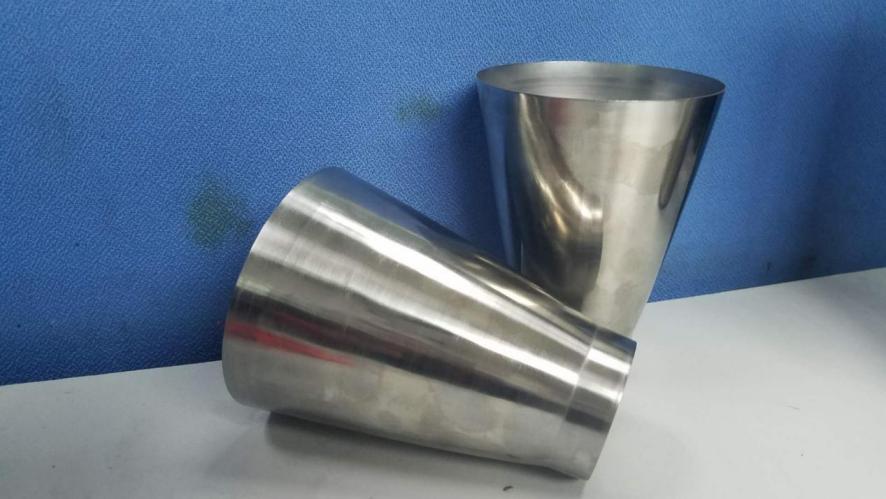
Conclusion
In conclusion, CNC spinning machines play a critical role in modern sheet metal fabrication, offering unmatched precision, speed, and repeatability. Advancements in technology have further enhanced the efficiency and accuracy of CNC spinning processes, making them indispensable in various industries. By understanding the applications, benefits, and design considerations associated with CNC spinning, manufacturers can leverage this technology to produce high-quality parts with confidence.