CNC Metal Spinning Machine -Single Roller AC2000
Metal Spinning Machine For Blower & Centrifugal Fans
Machine Name |
Single Wheel CNC Metal Spinning Machine |
Model |
AC-2000:(diameter Max Ф2050;Al-1Max 12mm; Carbon Steel-Max 8mm) |
Application Industry |
(Aerospace, Aviation Weapons, Building, Musical Instruments, Automotive Parts, Pressure Vessel, Ventilation, Blower & Centrifugal Fans) |
Technical Service |
Complete the test in the early stage; provide online and offline training in the later stage, and complete the turnkey project. |
Technical Guidance |
Online 24 hours a day/ 7*24 Pre-sales technical service |
Project Progress |
30-120 days |
Relevant Files |
ALTRON_AUTO Catalog-Industrial Blower Machinery Turnkey Project |
- ADAVANTAGES
- PARAMETERS
- CUSTOMER TESTIMONIALS
Single Roller CNC Metal Spinning Machine-AC2000 Introduction:
Single-Roller CNC Metal Spinning Machine-AC2000 is a larger metal CNC spinning machine, which can process round materials with a diameter of 2050mm; it can cover industrial blowers and centrifugal fans:
Air inlet funnel: diameter: about 1750mm, height: 400mm;
Impeller shrouds: about diameter 1900mm, height: 200mm;
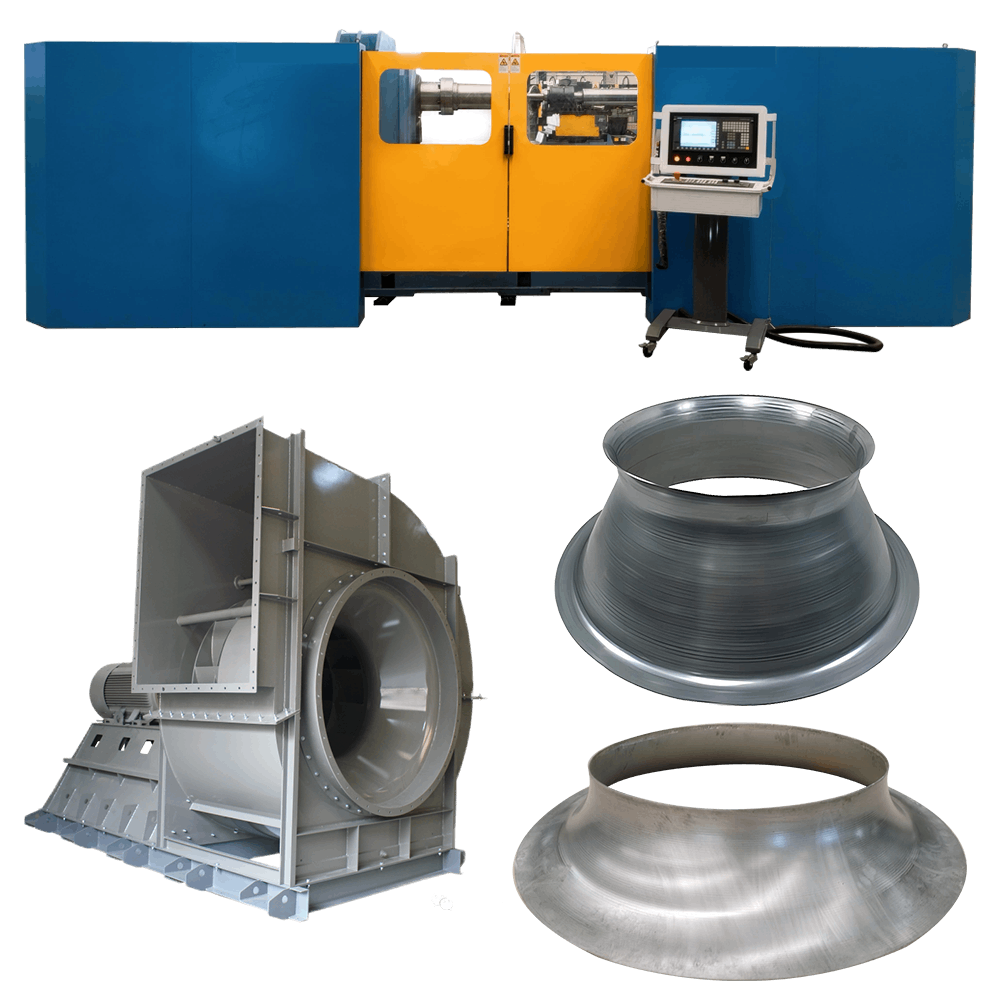
Improve The Quality Of Industrial Blowers & Centrifugal Fans
In the manufacturing of larger industrial fans, it replaces the traditional hydraulic or rolling process, greatly improving the quality and precision of accessories;
The core of a good industrial centrifugal fan:
energy efficiency, air volume, air pressure, noise and vibration, service life and environment;
Industrial Fan Calculation Technology:
- The arc profile of the impeller shrouds plays a role in the assembly of the impeller and the welding strength of the blades Key;
- The gap between the air inlet funnel and the impeller, too large a gap will affect the efficiency of the fan;
Solutions For Improving The Quality Of Industrial Fans By Spinning:
- The CNC spinning machine makes the impeller shrouds to ensure that the arc size is consistent with the design drawings;
- The CNC spinning machine makes the air inlet funnel to ensure the size and overall height of the mouth, making the assembly process of the centrifugal fan more efficient;
Advantages Of Industrial Fan Accessories Produced By Spinning:
Small mold investment, only 10% of the cost of deep drawing molds;
One-time forming, no welding welds, high strength and appearance quality;
Save materials, such as impeller shrouds, the bottom material cut off after spinning can produce the next model of accessories;
High precision, making solid molds in the main dimensions;
Working Video Of CNC Metal Spinning Machine
Spinning Technology Solutions For Blower & Centrifugal
Customized industrial fans are a market trend. Every industrial fan manufacturer hopes that the fans they produce are different from the drawings of other factories, and their performance and energy efficiency should be better than other industrial fan brands!
As a result, engineers of industrial fan manufacturers are constantly optimizing and improving core accessories; they must be tested in the fan laboratory to achieve energy efficiency before they can be produced! This happens to be the unique advantage of the spinning machine: whether it is the production of industrial fan accessories samples or mass production, the spinning machine can flexibly solve it!

CNC Spinning Machine For Centrifugal Fan Air Inlet:
Altron’s CNC spinning machine supports simple mold spinning process, commonly known as moldless metal M; because the shape of the air inlet funnel has sufficient strength to achieve hollow spinning:

Dieless metal spinning for industrial fan air inlet step description:
- Install an extended connecting sleeve on the main shaft to reserve enough distance for hollow core spinning;
A removable simple positioning plate is designed at the front end of the connecting sleeve to control the diameter of the air inlet end face; - The shape of the air inlet funnel is controlled by the CNC spinning trajectory program. Different metal materials have different rebound coefficients. The size requirements of the industrial fan design drawings are met by modifying the data of the last spinning program short;
- The height control of the air inlet funnel is controlled by the hydraulic reverse roller device of the Altron spinning machine. When the product is formed, the hydraulic roller pushes forward and the sensor reaches the specified position The sensor is triggered, the cylinder stops moving and maintains pressure, and the CNC spinning tool wheel is programmed to spin the flange edge of the air inlet flat;
- The indexing punching mechanism can be selected; the flange edge of the air inlet is indexed and punched (replace the servo spindle motor and add the punching mechanism);
- Finally, the turret is rotated and the cutting tool is used to cut from the end face of the air inlet;
- The installation sequence: remove the bottom waste, the hydraulic tailstock assists in separating the mold, and removes the air inlet funnel;
- Complete the single production of the air inlet funnel, when the worker puts the material and presses the start program, the machine will automatically carry out batch production!

CNC Spinning For Centrifugal Fan Impeller Shrouds
The metal spinning process of impeller shrouds is much simpler than that of inlet funnels. There are two main options: solid mold spinning and moldless spinning:

Solid mold spinning:
- The mold investment is relatively high, suitable for parts that can be produced stably in large quantities;
- The inner contour accuracy is high, and the welding and assembly accuracy of the impeller blades is higher;
- The spinning operation is easier for production workers;
Moldless spinning:
- The mold cost is low and can be basically ignored! Suitable for sample development and small batch production;
- Good development efficiency, you only need to make a simple positioning plate to make samples!

If you are planning or producing Blower and Centrifugal Fans, please contact me and Joby engineers will give you a detailed plan.
Altron’s Factory Video
Configuration
Standard Configuration
- SIEMENS CNC 828D
- SIEMENS Servo Motor & Drive
- Asynchronous Servo Spindle Motor
- APEX Servo Reducer
- High Strength Ductile Iron Sliding Table
- Blanks Center Assembly
- Back Roller Assembly
- CNC Tool Turret
- Hydraulic Station & Air Cooling System
- Air Unload Assembly
- Self-developed Spinning System
- Control System Remote Maintenance
Select Configuration
- Spindle Spinning Cylinder
- Trimming Tool Assembly
- Air Conditioner for Hydraulic Station
- Hot Spinning Parts Under 700℃
- Teach In & Play Back System
Model No. |
Max. Material Dia. (mm) |
Radial Stroke (mm) |
Axial Stroke (mm) |
Roller Thrust (KN) |
Tailstock Force (KN) |
Spindle Power (KN) |
Spindle Speed (RPM) |
Material Thickness AL./carbon steel/SUS (mm) |
AC-800 | 800 | 400 | 600 | 40 | 20 | 18.5 | 50-1000 | 5 / 3 / 2 |
AC-1000 | 1050 | 450 | 650 | 40 | 20 | 22 | 50-1000 | 6 / 4 / 3 |
AC-1200 | 1250 | 480 | 800 | 60 | 50 | 30 | 50-800 | 8 / 5 / 4 |
AC-1400 | 1450 | 650 | 800 | 70 | 50 | 37 | 50-500 | 10 / 6 / 4.5 |
AC-1600 | 1650 | 680 | 800 | 80 | 50 | 37 | 50-500 | 10 / 6 / 4.5 |
AC-2000 | 2000 | 750 | 1250 | 140 | 100 | 55 | 20-400 | 14 / 10 / 7 |
AC-2500 | 2500 | 800 | 1750 | 200 | 140 | 90 | 20-300 | 14 / 10 / 7 |
AC-3000 | 3000 | 900 | 2000 | 200 | 160 | 115 | 10-250 | 14 / 10 / 7 |
Machine Configuration Parameters
Technical index
Ball screw rod
-
Marcley
★★★★★Post a review on Aug 21, 2022 From Bolivia
The AC2000 Single Wheel CNC Spinning Machine has transformed our metal spinning process. Its precise control and repeatability have allowed us to achieve exceptional results with ease. Highly recommended!
-
Arthur Zonneveld
★★★★★Post a review on Fec 21, 2022 From Mauritius
The AC2000 has exceeded our expectations in terms of efficiency and versatility. Its user-friendly interface and adjustable tooling options have made component shaping a breeze. We are thrilled with the exceptional results we have achieved
-
Nicolas Vazquez
★★★★★Post a review on jul 21, 2022 From Uruguay
Thanks to the AC2000, we have been able to streamline our metal spinning operations. Its robust construction and comprehensive safety features ensure a secure working environment, while its maintenance-friendly design has reduced our downtime. An excellent investment for our manufacturing facility
-
OSCAR URBANEJA
★★★★★Post a review on Oct 10, 2022 From Venezuela
We are extremely impressed with the performance of the AC2000 machine. It offers outstanding stability and accuracy, resulting in flawless shaping of cylindrical components. Our productivity and product quality have significantly improved.