CNC Metal Spinning Machine -Single Roller AC800
CNC Metal Spinning For Automotive Parts and environmental equipment
Machine Name |
Single Wheel CNC Metal Spinning Machine |
Model |
AC800:(diameter max Ф800;aluminum-Max 5mm; carbon steel-Max 3.5mm) |
Application Industry |
(Aerospace, Aviation Weapons, Medical, Furniture, Lighting, Building, Fire, Musical Instruments, Crafts, Automotive Parts, Pressure Vessel,) |
Technical Service |
Complete the test in the early stage; provide online and offline training in the later stage, and complete the turnkey project. |
Technical Guidance |
Online 24 hours a day/ 7*24 Pre-sales technical service |
Project Progress |
30-120 days |
Relevant Files |
ALTRON_AUTO Catalog-Industrial Blower Machinery Turnkey Project |
- ADAVANTAGES
- PARAMETERS
- CUSTOMER TESTIMONIALS
Single Roller CNC Metal Spinning Machine-AC600 Introduction:
Altron’s Single Roller CNC Metal Spinning Machine can spin a variety of metal materials and is suitable for the Aerospace, aviation weapons, medical, furniture, lighting, construction, firefighting, musical instruments, handicrafts, auto parts, pressure vessels, etc..
Single Roller CNC Metal Spinning-AC800 CNC spinning machine is a general-purpose CNC spinning machine developed by Altron in the early stage. It can spin products with a disc diameter of less than 800mm. The equipment is equipped with a 6-station horizontal special metal spinning turret, which is designed to spin 4mm carbon steel and has an ultimate spinning batch production processing capacity of 3.5mm (tensile strength about 380Mpa, Carbon steel). Since January 2014, the company has carried out a new mechanical and electrical upgrade on this equipment. It currently uses Siemens mid-to-high-end system 808D, which has remote network diagnosis and maintenance functions, making it convenient for foreign customers to use machine tools, and is used in conjunction with CNC spinning programming software; Single Roller CNC Metal Spinning-AC800 CNC spinning machine is a standard model suitable for manufacturers in the automotive parts and environmental equipment industries.
Working Video Of Spinning Machine
- CNC metal spinning machine is precise and efficient, suitable for various metal forming;
- Intelligent control reduces labor costs;
- High repeatability ensures product consistency;
- Multi-functional and applicable to meet diverse production needs;
- Energy-saving and environmentally friendly, reducing energy consumption;
- Stable and reliable, improving production efficiency and quality.
Principle And Introduction Of CNC Spinning Machine
CNC spinning is a complex metalworking process technology that changes the production process of rotationally symmetrical parts. It works by spinning metal sheets or tubes on a CNC-controlled CNC spinning machine while applying pressure through a dedicated spinning tool to plastically deform them into an axisymmetric shape. The process is able to create complex geometries with high precision and repeatability.
CNC Metal Spinning Process Flowchart And Case Studies:
CNC metal spinning is divided into 6 key manufacturing processes that can form metal into various cylindrical shapes.

Stretch metal spinning
Shear metal spinning
Neaking metal spinning
Expanding metal spinning
Tube Thinking metal spinning
Spin Flanging metal spinning
1.Stretch Metal Spinning
Stretch metal spinning refers to the process of fixing a metal sheet disc between the machine mold and repeatedly spinning and stretching the metal spinning wheel tool; the metal sheet will be thinned to fit the mold contour.

2.Shear Metal Spinning
Shear metal spinning refers to fixing a metal sheet disc between the machine mold. When the product contour shape is a cone or a cone, and the single-side angle must be greater than 20°, the metal spinning wheel performs a single-pass spinning on the cone workpiece. This process requires high precision and strength of the machine.
Between 20°-30°, the thickness of the sheet is greater than 4MM;
Between 30°-40°, the thickness of the sheet is greater than 1.5MM;
Greater than 45°, the thickness of the sheet is greater than 0.8MM;
Calculation formula for spinning wall thickness: T(metal sheet thickness) * (Sin* A° cone angle);
For example: the wall thickness of the round sheet material: 2.0mm, the angle between the single side of the product and the axis is 40°; 2*(Sin*40)=1.28 (data for reference, different metal materials have different hardness, and the gap between the metal spinning tool wheel and the mold needs to be adjusted relative to each other)

3.Necking metal spinning
Necking metal spinning refers to fixing the metal pipe or barreled metal blank in a special mold or fixture, and repeatedly spinning the metal on the mouth or waist of the metal with the metal spinning wheel. This process is a special process of metal spinning! It solves the problem that the water bulging machine and traditional tube shrinking machine cannot change the diameter significantly.
It is mainly used in milk cans, chemical barrels, energy storage cylinders, hydrogen cylinders, and other pressure vessels with high pressure and airtightness!

4.Expanding metal spinning
Expansion metal spinning refers to fixing the metal pipe or barreled metal blank in a special mold or fixture, and the metal spinning wheel repeatedly expands the metal from the inside of the workpiece to the outside; this process is a less used process in metal spinning, and its mold tooling design is relatively complex! This process is opposite to necking metal spinning, and the corresponding process selection is mainly based on judging the ratio of the metal spinning part to the original pipe part.

5.Tube Thinning metal spinning
Tube Thinning metal spinning refers to fixing the metal tube in a special mold or fixture, and multiple sets of symmetrical metal spinning tool wheels thin the wall thickness of the tube to increase the length of the metal tube! The main feature of this process is that the wall thickness accuracy after metal spinning is high, the length of the machine is long, and the diameter is generally not large! The assembly accuracy of the equipment is quite strict, so the price of the machine is much more expensive than that of ordinary spinning machines. Due to the installation method of the special spinning wheel of this machine, this process is mainly used in room temperature metal spinning process.
This process is widely used in aerospace, military industry, energy storage, hydrogen cylinders and other long tube processing.

6.Spin Flanging Metal Spinning
Spin Flanging Metal Spinning refers to fixing a metal reel with a larger diameter on a special tensioning fixture or hydraulic chuck, and the flanging spinning wheel with rotary power tightens the edge of the reel, driving the workpiece to rotate on the main shaft. The flanging spinning wheel is controlled by the program to perform 90° flanging or bell-mouth spinning on the reel; this type of machine generally has a graduated punching function. After the flange is formed, the main shaft realizes power access through a complex clutch, the servo motor makes the workpiece accurately indexed, and the hydraulic punching mechanism starts working after receiving the indexing signal from the encoder.
Spin Flanging Metal Spinning is most commonly used in the manufacture of wind tubes for industrial axial fans and tunnel and subway jet fans.
Summary CNC metal spinning encompasses a variety of technical applications, and different process technologies are suitable for specific applications. Stretch metal spinning, shear metal spinning, shrink metal spinning, expansion metal spinning, tubular metal spinning and rotary flanging provide a variety of solutions for accurate and efficient metal forming.
Understanding the metal spinning process helps you choose the process production options for manufacturing high-quality metal. Altron also supports you to customize the perfect metal forming solution department and automated machine for your workpiece!

Advantages of CNC Spinning Machines
CNC spinning is a precision metalworking process that offers several advantages over traditional deep drawing methods.
CNC spinning machines are able to accurately form and guarantee the consistency of various metal materials during the spinning process (including special alloys such as aluminum, iron, copper, stainless steel and titanium). Secondly, CNC spinning improves productivity by reducing development time and minimizing material waste. In addition, CNC metal spinning helps to produce complex geometric rotational shapes without the need for high-powered machines and complex processes, thereby greatly reducing manufacturing costs.
Features of Altron’s CNC Spinning Machine
✔ Iemens CNC System & Siemens Drive Motor.
✔ CNC Metal Spinning Programming Software.
✔ Optional: oil-cooled air conditioner; electric cabinet air conditioner; isolation transformer
✔ Metal Spinning Thickness Capability: 0.3-25mm.
✔ Metal Spinning Diameter: 0-3800mm.
✔ Metal Spinning Trajectory Visualization.
✔ Free Guide to Metal Spinning Technology.
✔ Supports Hot Metal Spinning.
✔ Supports Water Circulation Spinning.
✔ Powerful metal spinning turret; can cut, turn, bead, flanging,
✔ Spinning tools water cooling mechanism.
✔ The spindle is equipped with punching mechanism/servo spindle.
✔ The spindle is equipped with rotary cylinder and hydraulic chuck fixture.
Cnc Spinning Programming Software:
Function:
- Synchronously create the program for two spinning wheels
- Protect the process fields for the machine
Advantages:
- Convenient and fast code automatic generation function
- Automatically generate the G code
- Automatically set the feed speed for different tracking
- Automatically set the spindle speed for different tracking
- Sampling of unknown mold surface curves
- Select the typical points for unknown surface of the molds
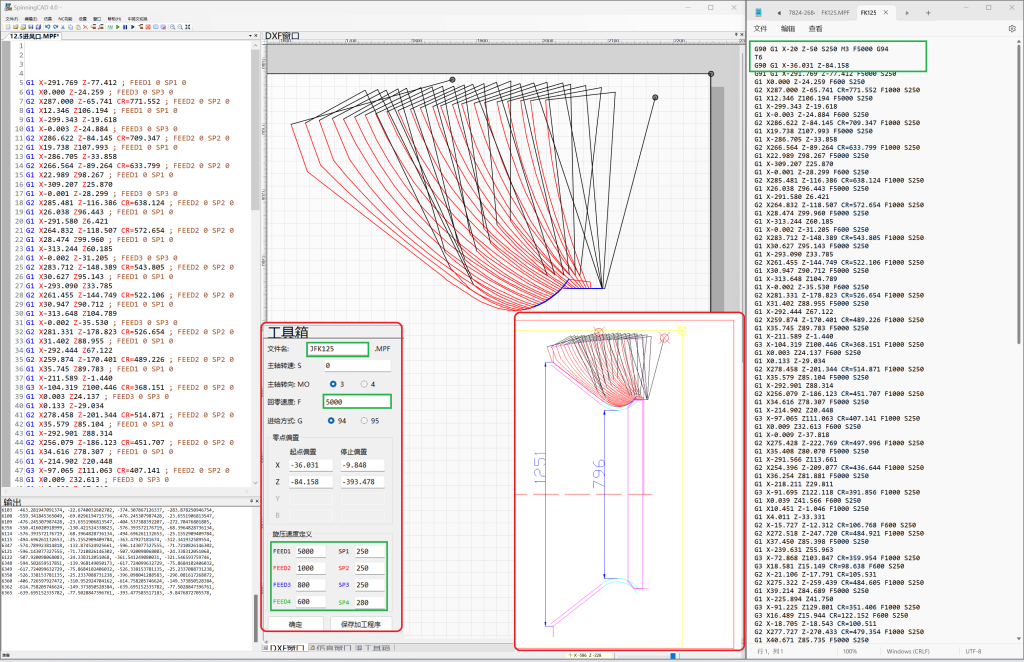
Altron provides free spinning software for CNC metal spinning machines; the CNC spinning automatic programming software can compile the CAD cross spinning path trajectory into G code, and can set the spinning feed F speed, spindle S speed, return to zero G0 F speed, starting point offset, gap compensation, and dual wheel synchronization instructions. The software has a trajectory simulation function, which can clearly find the location of the problem, allowing CNC spinning operation engineers to operate Altron’s machines more easily.
Optional Spinning Machine Recording And Re-Programming Control System
- Can be used with all types of Siemens system and other brand CNC System
- With mold protection function, it can prevent damage to the mold during spinning
- The outline of spinning moulds can be input by Gcode or DXF drawing
- The recording program can generate G code directly for part spinning processing
- The created program can be changed to G code usedfor the machine running directly
- The recording program can generate DXF files for analysis or modification
- The sentences in the programming for every productscan reach 100,000
- The system with WIFI function

The spinning machine recording and replay programming system is a set of software and hardware CNC systems developed for manual spinning engineers.
The system hardware consists of an industrial computer with WINCE system, a PC with WIN7 system and a Hall 360-degree rocker.
The special spinning programming system has strong anti-interference ability and stable operation. The running trajectory of the spinning roller is controlled by the rocker. During the spinning process, the running trajectory of the spinning wheel can be adjusted at any time according to the deformation and rebound of the material. The system will record all the spinning data information such as trajectory and speed to automatically generate the CNC spinning program for parts, so as to achieve an auxiliary system to prevent manual spinning.
Altron’s Factory Video
Configuration
Standard Configuration
- SIEMENS CNC 808D
- SIEMENS Servo Motor & Drive
- Asynchronous Servo Spindle Motor
- APEX Servo Reducer
- High Strength Ductile Iron Sliding Table
- Blanks Center Assembly
- Back Roller Assembly
- CNC Tool Turret
- Hydraulic Station & Air Cooling System
- Air Unload Assembly
- Self-developed Spinning System
- Control System Remote Maintenance
Select Configuration
- Spindle Spinning Cylinder
- Trimming Tool Assembly
- Air Conditioner for Hydraulic Station
- Hot Spinning Parts Under 700℃
- Teach In & Play Back System
Model No. |
Max. Material Dia. (mm) |
Radial Stroke (mm) |
Axial Stroke (mm) |
Roller Thrust (KN) |
Tailstock Force (KN) |
Spindle Power (KN) |
Spindle Speed (RPM) |
Material Thickness AL./carbon steel/SUS (mm) |
AC-800 | 800 | 400 | 600 | 40 | 20 | 18.5 | 50-1000 | 5 / 3 / 2 |
AC-1000 | 1050 | 450 | 650 | 40 | 20 | 22 | 50-1000 | 6 / 4 / 3 |
AC-1200 | 1250 | 480 | 800 | 60 | 50 | 30 | 50-800 | 8 / 5 / 4 |
AC-1400 | 1450 | 650 | 800 | 70 | 50 | 37 | 50-500 | 10 / 6 / 4.5 |
AC-1600 | 1650 | 680 | 800 | 80 | 50 | 37 | 50-500 | 10 / 6 / 4.5 |
AC-2000 | 2000 | 750 | 1250 | 140 | 100 | 55 | 20-400 | 14 / 10 / 7 |
AC-2500 | 2500 | 800 | 1750 | 200 | 140 | 90 | 20-300 | 14 / 10 / 7 |
AC-3000 | 3000 | 900 | 2000 | 200 | 160 | 115 | 10-250 | 14 / 10 / 7 |
Machine Configuration Parameters
Technical index
Ball screw rod
-
Marcley
★★★★★Post a review on Aug 21, 2022 From Bolivia
The AC800 has exceeded our expectations in terms of efficiency and versatility. Its user-friendly interface and adjustable tooling options have made component shaping a breeze. We are thrilled with the exceptional results we have achieved
-
Arthur Zonneveld
★★★★★Post a review on Fec 21, 2022 From Mauritius
Thanks to the AC800, we have been able to streamline our metal spinning operations. Its robust construction and comprehensive safety features ensure a secure working environment, while its maintenance-friendly design has reduced our downtime. An excellent investment for our manufacturing facility
-
Nicolas Vazquez
★★★★★Post a review on jul 21, 2022 From Uruguay
The AC2000 Single Wheel CNC Spinning Machine has transformed our metal spinning process. Its precise control and repeatability have allowed us to achieve exceptional results with ease. Highly recommended
-
OSCAR URBANEJA
★★★★★Post a review on Oct 10, 2022 From Venezuela
We are extremely impressed with the performance of the AC800 machine. It offers outstanding stability and accuracy, resulting in flawless shaping of cylindrical components. Our productivity and product quality have significantly improved.