Welding Robot Machine For Centrifugal Fan Impeller
Welding For Centrifugal Fan Impeller ,Housing, Axial Fan Ducts
Machine Name | Welding For Centrifugal Fan Impeller |
Model | AC-YL (Camera, AI, Auto weld identification & Correction) |
Application Industry | Centrifugal , Axial Fan , aluminum, carbon , stainless steel impellers, Duct |
Technical Service | Complete the test in the early stage; provide online and offline training in the later stage, and complete the turnkey project. |
Technical Guidance | Online 24 hours a day/ Conference To Solve Pre-Sales Problems. |
Project Progress | 30-120 days |
Relevant Files | ALTRON_AUTO Catalog-Industrial Blower Machinery Turnkey Project |
Industrial Fans A-Z Project:
1 CNC Spinning Machine 2 CNC Flanging Machines, 3 Axial Flow Fans Forming Production Line, 4 CNC Rolling machine,5 Seam Welding machine 6 AI Automatic Welding,
- DETAILS
- PARAMETERS
- CUSTOMER TESTIMONIALS
Introducing Altron’s centrifugal blower impeller welding robot to simplify the welding manufacturing process of centrifugal blower impellers. The quality of the centrifugal fan impeller determines the performance and energy efficiency of the industrial fan, and is a core component!
Traditional automatic welding equipment cannot track the weld in real time and correct the welding trajectory to achieve true automatic welding, so manual welding is basically used! The assembly of the impeller and the blades cannot be consistent, and the teaching programming method cannot be applied to impeller welding!
The laser vision-guided centrifugal fan impeller automatic welding robot automates the fan impeller, fan tube and other components, reduces the number of welding workers, and improves the welding quality and welding efficiency. After welding is completed, the weld strength is guaranteed to be consistent, the appearance is beautiful, and no manual grinding is required.
Centrifugal Fan Impeller Welding Video
Industrial Fan Impeller Range:
Impeller diameter: 300-3800 MM
Impeller height: 80-2400 MM
Impeller weight: 300-3800 MM
Robot: ABB & KUKA
Impeller assembly: Blade spot welding machine or manual spot welding tooling
Altron can customize welding solutions according to the impeller
The visual welding robot completely solves the problems of labor-intensive traditional fan manufacturing, low-end fan quality, and difficulty in mass production!
Description of Centrifugal Fan Impeller Welding Machine
How does a robot identify the weld location of a centrifugal fan impeller?
The automatic welding apparatus for impellers consists of several key components, including the ABB welding robot system, a two-axis transducer, a laser vision guiding system, a welding system, a gun clearing system, and a safety protection system. The laser vision system controls the welding trajectory by accurately guiding each weld seam using 3D coordinates and welding posture information. It continuously adjusts the welding trajectory to compensate for any spot welding deviations on the blades.
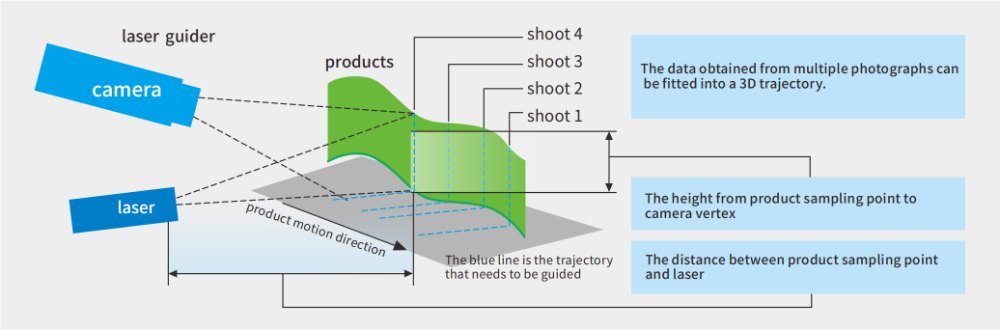
This equipment brings together the human-machine synergy, overcoming the issues associated with previous robot training methods and quickly identifying the weld seam for an optimal welding perspective. Real-time adjustments to the welding offset are made, ensuring the best welding results for subsequent weld seams.
Industrial camera & camera imaging diagram
Camera parameters of centrifugal fan impeller welding machine | |
Frame rate | 135fbs |
Pixel clock frequency | 80MHz |
Camera tap | 2 |
Grayresolution | 8bit |
Fixed analog noise | <1DN RMS@8bit |
Exposure time range | 10us-335ms |
Analog gain | n/a |
Digital gain | 0.1to 15.99(Fine Gain) |
Automatic Welding Impeller Vs Manual Welding Impeller
Industrial Fan Metal Welding Solution-Customized welding Service For Axial & Centrifugal Fans
- Altron Industrial Fan Metal Welding Solution: (Axial Fan & Centrifugal Fan)
- Axial Fan Motor Bracket Scanning Welding
- Axial Fan Cylinder External Bracket Scanning Welding
- Axial Fan Cylinder Guide, Installation Base Welding Whole Process
- Axial Fan Impeller Blade Spot Welding Assembly
- Axial Fan Impeller Scanning Welding
- Customized Dual-station Centrifugal Fan Housing Welding
- Customized Dual-station Robot Welding Trapezoidal Base and Centrifugal Fan Frame
- Industrial Fan Manufacturer Welding Factory
Impeller Welding Machine In Industry Fan Manufacturer Factory

Impeller Welding Machine Video In Korea
Impeller Welding Machine Video In Detong
Industrial Fan Impeller Blade Assembly Spot Welding Machine
The front and rear axes, upper and lower axes, and rotating axes of the spot welding machine can be flexibly adjusted, and the turntable drives the workpiece to automatically rotate, eliminating the need for manual scale marking and assisting manual insertion and spot welding.
3 Ways To Assemble Centrifugal Fan Impellers
Advantages & Disadvantages Of Assembling Centrifugal Fan Impellers:
- Laser Line Drawing: low efficiency, poor consistency, high requirements for manual welding; low cost!
- Positioning Pin: complex processing technology, high cost; good consistency!
- Impeller Spot Welding: simple operation, high angle accuracy, low tooling cost; cooperate with impeller welding production!
Impeller Manual Welding Effect & Machine Welding Effect
Impeller Spot Welding Machine Schematic Diagram
Blade Assembly Spot Welding Machine Video
Impeller Spot Welding Machine Parameter Table
Machine Size | Length | 2750 MM |
Width | 640 MM(not include cabinet) | |
Height | 2170 MM | |
Weight | 620 KG | |
Machine Travel | Front and rear axis travel | 1200 MM |
Upper and lower axis travel | 800 MM | |
Rotating axis travel | 360° | |
Processing Range | Maximum diameter of single inlet impeller | 1600 MM |
Minimum diameter of double inlet impeller | 240 MM | |
Maximum impeller weight | 1500 KG | |
Machine Accuracy | Rotating axis reverse clearance | 0.5 MM |
Rotating axis coaxiality | 0.2 MM |