What are the main uses of CNC spinning
What Are The Main Uses Of A CNC Spinning Machine?
It can process and form different metal materials, axially symmetrical return shell parts, and has a wide range of application industries, from household cookware to aerospace and military accessories, all of which can be involved in the application of metal spinning!
Application areas of CNC metal spinning
As more and more industries use metal spinning for specific metal products, the application industries become more extensive! (Learn more about metal spinning forming cases)
Lighting, furniture, cookware, musical instruments, handicrafts, auto parts in the civil field;
Industrial fan accessories, large machinery parts, environmental protection equipment, fire fighting equipment, hardware construction, and other metal accessories for pressure vessels in the industrial field;
Missile shells, fish shells, shaped charge liners, etc. in the military field;
Aerospace fairings, guide covers, end covers, tank heads, nose cones, nozzles, etc.
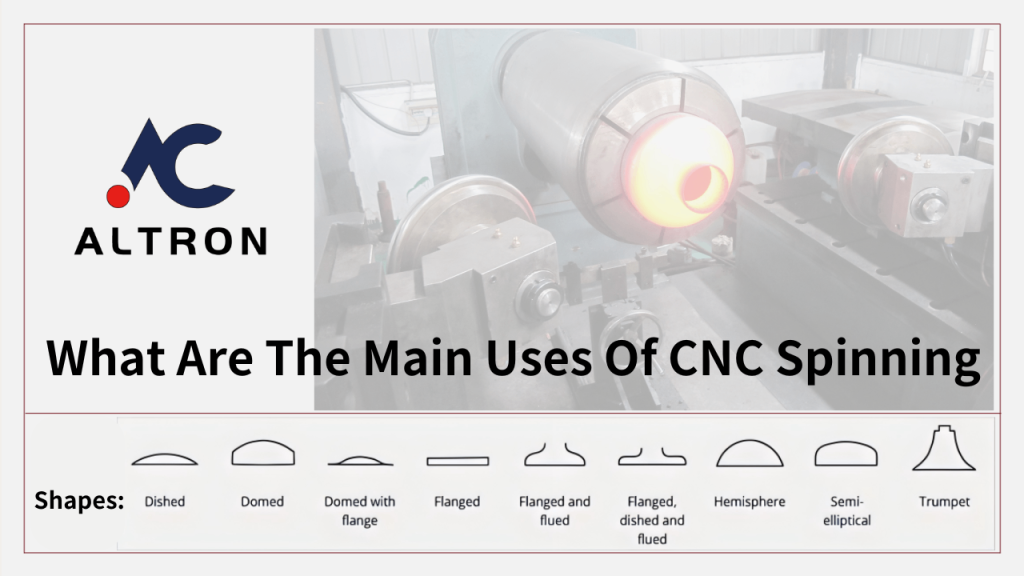
Materials suitable for metal spinning
Metal spinning of conventional metal materials
Conventional metal spinning materials are copper, iron, aluminum, galvanized sheet, and stainless steel! Different metal materials have unique properties in different industries!
In the ventilation industry, copper and aluminum are used to make air inlet cones, which can play an explosion-proof role! In the working process of industrial fans, the high-speed rotation of the impeller is very easy to produce sparks of metal collision, and the performance of aluminum and copper can perfectly solve it!
In the environmental protection, waste gas treatment and other industries, most parts are made of stainless steel! Because stainless steel is particularly stable in special and corrosive working environments, and can increase service life!
In many household lighting or decorative applications, many parts will use iron. Due to its low cost and good forming performance, it is easy to be processed into various parts, combined with painting or electroplating!
Metal spinning of special materials
In some specific application scenarios, special metal materials must be used, such as aviation 7 series aluminum alloy, platinum, titanium alloy, molybdenum, Hastelloy, inconel, nickel-based alloy, chromium alloy, and other high-temperature alloy materials composed of special elements;
Often these special materials generally require the use of hot spinning processing technology in the metal forming process! Different heating temperatures reduce the hardness of different metal materials and improve ductility! Achieve a higher forming process!
Shapes that can be processed by metal spinning
- Curved surface shape: Dished head;
- Dome shape: Lampshade with arc on the top;
- Dome with flange: The top is arc-shaped, and the flange is used for sealing or container cover;
- Flange shape: Large diameter round tabletops need to be reinforced with flange edges;
- Flanged and flued: Formed by expansion of the tube body or necking;
- Flanged dished and flued: Shapes composed of multiple arcs and straight segments, which are difficult to form;
- Hemispherical shape, half of a round sphere, usually used in craft decoration and other fields;
- Semi ellipticl shape: The bottom is elliptical with straight edges, usually used as the ends of the container;
- Trumpet: The mouth changes from small to large and has an arc, such as musical instrument trumpets, modern furniture bases, etc.
The Development of Metal Spinning
Metal spinning has a long history of development, from early manual spinning to automated metal spinning!
The ability of metal spinning has also developed from thin-walled parts to thicker parts! This involves the processing capacity of heavy-duty CNC spinning machines; ordinary CNC spinning has a simple structure similar to a CNC lathe! The design and manufacturing requirements of large metal spinning machines are much higher than those of small spinning machines!
Advantages of CNC metal spinning:
- The manufacturing cost is lower than that of deep drawing, stamping and other processes;
- Shorter production cycle, flexible application in the production tasks of small and medium batch orders;
- More flexible design and development, from design to sample within 3-7 days;
- Production of symmetrical axial rotation parts without welding;
- High material utilization rate, no large amount of scrap metal is generated;
What is Metal Spinning Machine:
Metal spinning machine is a device used for metal forming processing. Its working principle is derived from the forming principle of pottery!
The metal workpiece rotates and is subjected to axial and radial extrusion thrust, forming from point to line, curve to contour surface!
Components of metal spinning machine:
Spindle, tailstock, spinning roller, X, Z axis drive slide, the main structure is similar to that of a car factory, and the power, thrust and bearing capacity are greater than those of a lathe!
Altron metal spinning engineers solve your forming problems
When you encounter difficulties in metal forming, please contact Altron’s engineering team, Joby will solve your problems and provide a complete solution!
More Metal Spinning Video List

Altron Manufactures And Provides Forming and Welding Solutions For:
- CNC Metal Spinning Machine,
- Multi-Roller Flow Forming Machine,
- Neck Spinning Machine,
- Internal Spinning Machine,
- Hub Spinning Machine,
- CNC Flanging Machine,
- Welding Robot, Rolling Machine,
- Seam Welding,
- Axial Flow Fan Production Line,
- Centrifugal Fan Impeller Welding,
- Centrifugal Fan Housing Welding,
- Air Duct Production Line,
- Spiral Duct Production Line,
- Rectangular Duct Production Line,
- Impeller Forming Production Line,
- Customized Industrial Fan Impeller,
- Laser Cutting Production Line,
- Laser Welding Solution, ect…